What Is Undercut In Injection Molding?
What Is Undercut In Injection Molding?
Injection molding is a highly versatile and widely used manufacturing process, especially in producing plastic components. It allows for the creation of complex geometries with precision and efficiency. One of the critical concepts in injection molding is the term undercut. Understanding undercuts, their implications, and how to design them can significantly affect manufacturing parts’ quality, cost, and feasibility. This article will delve into what undercuts are, their types, implications for the injection molding process, strategies to handle them, and best practices for design.
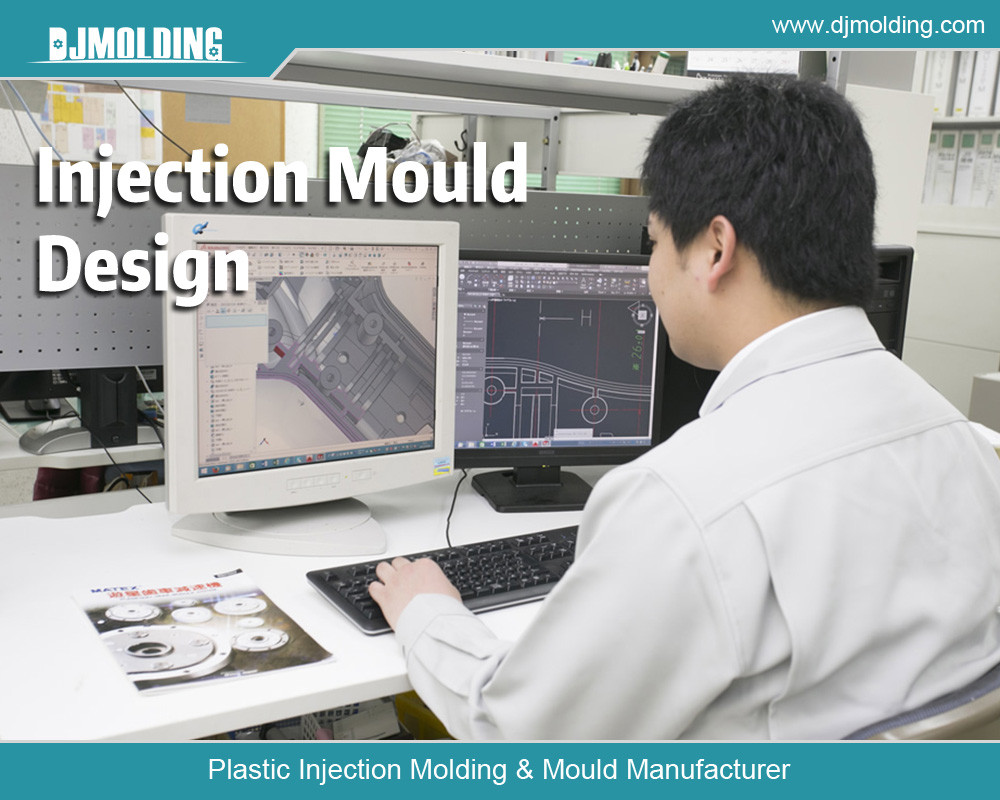
1. Understanding Undercuts
1.1 Definition of Undercut
In injection molding, an undercut refers to a portion of a molded part that is constrained or blocked by the mold, preventing the part from being removed easily once the injection process is complete. An undercut creates a geometry where the molded piece has features that recess into the mold cavity, complicating the ejection process. This characteristic is crucial in determining the part’s mold design and overall manufacturing feasibility.
1.2 Types of Undercuts
There are several types of undercuts commonly encountered in injection molding:
- A simple Undercut occurs when a part has a simple projection or recess that extends into the mold. Examples include snap fits or clips.
- Complex Undercut: This involves more intricate shapes that may require additional actions or features in the mold, such as sliders or lifters, to eject the part successfully.
- Internal Undercut: These are features inside the part, such as holes or internal grooves, that prevent straightforward ejection.
- External Undercut: These undercuts occur on the outer surface of the part, making it challenging to release the part from the mold without additional mechanisms.
Understanding the types of undercuts is vital for designers and engineers to ensure that the injection molding process runs smoothly.
2. Implications of Undercuts in Injection Molding
2.1 Design Considerations
Undercuts can significantly affect the design of injection molds. Designers must consider whether undercuts are necessary for the part’s functionality and how they impact the overall design. The presence of undercuts often means that the mold must be more complex, involving additional components that can increase manufacturing costs and lead times.
2.2 Manufacturing Complexity
The presence of undercuts increases the complexity of the mold design. Simple molds can typically be manufactured more quickly and at a lower cost, while molds with undercuts may require additional mechanisms such as:
- Lifters: These are mechanical components that move vertically to allow the molded part to be released from undercuts.
- Slides: These create moving components that can retract to release the part from the mold.
Incorporating these mechanisms adds complexity to the mold, which can also lead to higher maintenance requirements.
2.3 Cost Implications
Undercuts can lead to higher production costs for several reasons:
- Increased Mold Complexity: As mentioned earlier, molds with undercuts often require more intricate designs and additional components, leading to higher initial manufacturing costs.
- Longer Production Times: More complex molds can slow production, leading to longer cycles.
- Maintenance Costs: More components can mean more potential points of failure, leading to increased maintenance costs.
2.4 Quality Control Issues
Undercuts can also impact the quality of the finished product. When a part has undercuts, there may be increased stress on the mold during the ejection process, leading to potential defects such as:
- Surface Marks: The mold and undercut interaction can create surface imperfections on the finished part.
- Warpage: Improper ejection of parts with undercuts can lead to warping, especially if the part is made from materials sensitive to temperature changes.
Quality control is paramount when dealing with undercuts in injection molding.
3. Strategies to Handle Undercuts
Designers and engineers have several strategies to manage undercuts in injection molding effectively:
3.1 Design Modification
- Avoiding Undercuts: If feasible, the best way to mitigate the issues associated with undercuts is to prevent them altogether. This could involve rethinking the design to eliminate features that would create undercuts.
- Using Tapered Features: Incorporating tapered features can help reduce the likelihood of undercuts. Tapered sides can make it easier for the part to be ejected without requiring additional mechanisms.
3.2 Utilizing Mold Technologies
- Rotating Cores: These can be employed in specific designs to create undercuts without compromising the mold’s ability to eject the part.
- Multistage Molding: In some cases, producing parts in multiple stages may be more efficient, allowing undercuts to be added after the initial molding process.
3.3 Adjusting Material Selection
Material choice can significantly affect how a part with undercuts behaves during the injection molding. For example:
- Choosing Flexible Materials: In some cases, selecting materials with more flexibility can help mitigate the risks associated with undercuts.
- Considerations for Cooling and Shrinkage: Understanding how different materials behave during cooling and shrinkage can help design parts that can withstand undercut features.
4. Best Practices for Designing Parts with Undercuts
Designing parts with undercuts requires careful consideration to ensure feasibility in the injection molding process. Here are some best practices to keep in mind:
4.1 Collaborate with Mold Makers
Engaging mold makers early in the design process can lead to better insights into the feasibility. Mold makers can provide valuable input on minimizing the impacts of undercuts, ensuring that the design is functional and manufacturable.
4.2 Conduct Mold Flow Analysis
Using mold flow simulation software can help designers visualize how the material will flow within the mold and identify potential issues with undercuts before physical prototyping. This analysis can reveal problems such as potential air traps or uneven material distribution.
4.3 Prototype and Test
Creating prototypes of parts with undercuts can help identify challenges early in the design phase. Testing these prototypes can provide insights into the final product’s behavior and whether any design adjustments are needed.
4.4 Plan for Ejection
When designing parts with undercuts, always consider the ejection mechanism. Ensure there is enough clearance for the ejection system to operate effectively. This could mean incorporating additional features into the mold or adjusting the part design to facilitate easier ejection.
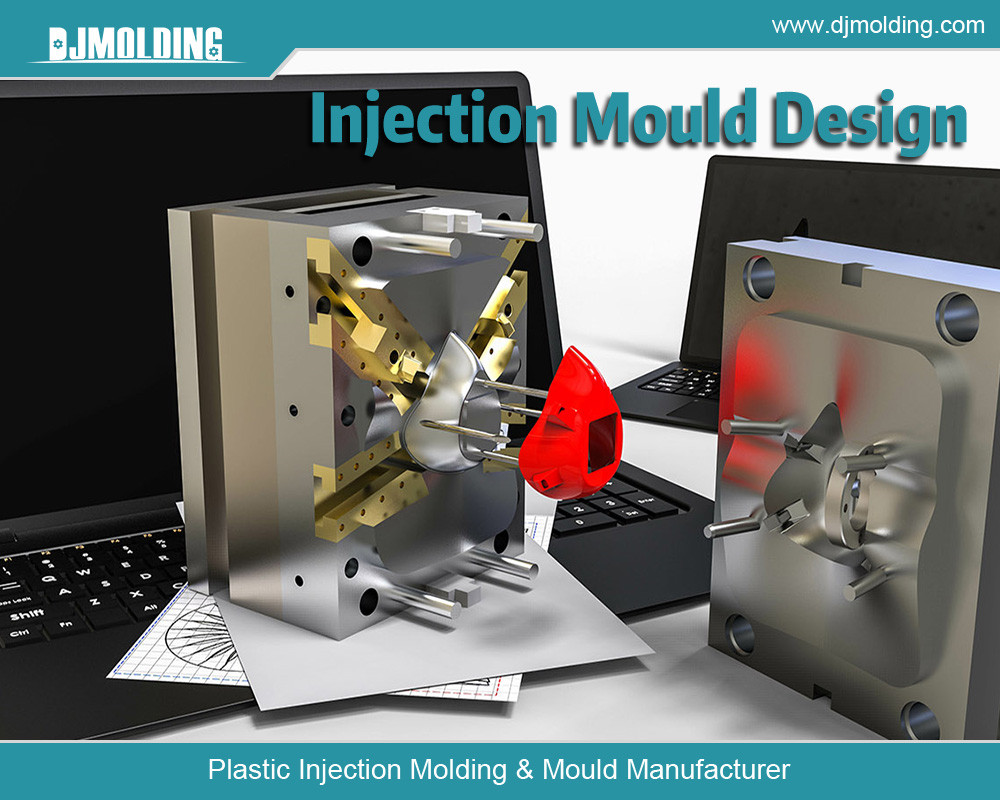
Conclusion
Undercuts in injection molding can present challenges, but with careful consideration and design strategies, these challenges can be effectively managed. Understanding what undercuts are and their implications on design and manufacturing and employing strategies to handle them can lead to successful injection molding processes. By following best practices and collaborating closely with mold makers and engineers, designers can create functional parts that meet performance and manufacturability criteria. In the world of injection molding, recognizing and addressing the complexities of undercuts can significantly enhance the overall success of a project.
For more about what is undercut in injection molding, you can pay a visit to Djmolding at https://www.djmolding.com/ for more info.