What is Rapid Injection Molding?
What is Rapid Injection Molding?
Rapid injection molding is an incredible manufacturing process that lets you quickly craft plastic parts with relative ease. Compared to the pricey molds used in traditional injection molding, this method employs cheaper aluminum or epoxy molds crafted from 3D printers or machines.
Flowing molten plastic into a mould— filled high pressure— once it cools and sets, the adornment pops out like magic! It’s all about repeatability for the speedy production of many items simultaneously.
Most manufacturers use rapid injection molding for prototyping, low-volume creation, and bridge tooling due to its swiftness and affordable cost. So, before taking an expensive plunge on steel molds for high-volume production, this molding offers ample testing time to refine designs without getting in too deep.
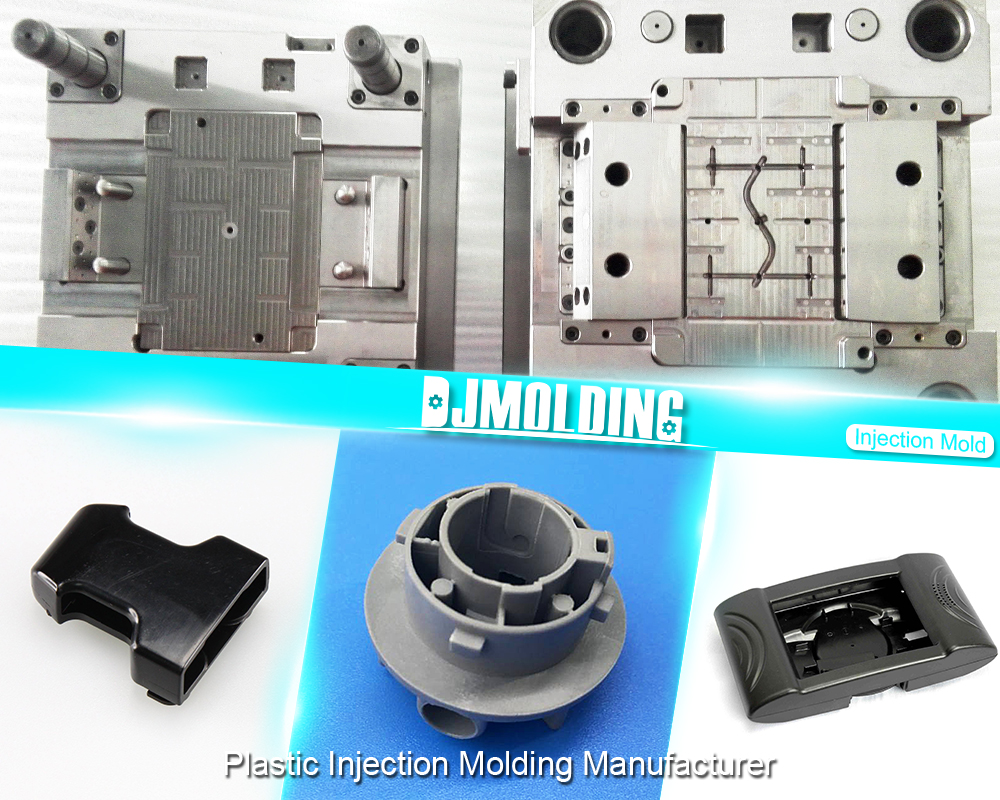
The Advantages of Rapid Injection Molding
Rapid injection molding offers several benefits — speeding up your production, cutting costs, ensuring that quality stays high, and enabling flexible design changes. You get all this immediately – no waiting weeks or months while you would with traditional methods.
The advanced machinery of rapid injection molding lets the cycle times fire off quicker. It means labor and tooling costs stay low as custom molds are out of the picture. On top of that, productivity booms thanks to small batch sizes keeping any waste to a minimum — great news for your budget and bottom line, especially when demanding quality standards must be met in industries such as medical and aerospace!
It’s easier, faster, cheaper – not just another ‘run-of-the-mill’ solution; here, speed is king, but quality still reigns supreme. Plus, rapid injection molding also gives you serious maneuverability in design alterations without needing additional molds – letting you quickly respond to market demands with ease.
How Rapid Injection Molding Works
The task of rapid injection molding is an intricate procedure that requires precision and finesse. It begins with developing a 3D CAD model for the desired finished product, which then serves as a blueprint to create molds made of aluminum or steel.
These molds are affixed to an injection molding machine composed of a hopper, injection unit, and clamping unit. Inside this machination, a plastic resin is heated until just molten enough before being injected into the metal cavity under enormous pressure.
Once completely cooled down in its unique shape, the part springs forth from its metallic formwork – ready to be used!
Materials Used in Rapid Injection Molding
Rapid injection molding can use various materials, like thermoplastics and thermosetting plastics. In most cases, they’ll use thermoplastics since these plastics can be melted and remelted countless times without degradation.
The usual suspects are ABS, polycarbonate, polypropylene, and nylon – although, for shorter production periods or reduced batch sizes, you may require different material forms to get the optimal end product. These may feature faster cooling levels or improved flow characteristics to ensure your process runs smoothly.
The Role of 3D Printing in Rapid Injection Molding
3D printing is the game-changer for rapid injection molding, providing companies with a cost-efficient and speedy way of making molds. Instead of laboriously machining them with traditional methods, digital designs can now be directly produced, reducing the need for pricey tooling and accelerating lead times.
The implications 3D printing brings to rapid injection molding are numerous. To start, complex shapes that may have been left out in the cold by more classical techniques can finally be realized. This leads to pioneering designs featuring intricate detail and exactness perfectionists could only aspire for.
It also allows design iterations aplenty; with 3D printed molds being created fast and efficiently like you please, designers get ample elbow room to test out their ideas and modify them accordingly sans possible costly setbacks when mass production commences since time-to-market rates will shrink right down as well.
Lastly, we can’t forget its strategic difference-maker status either: it shakes up low-volume batch productions no matter what niche industry they belong in or how unpredictable demand rivers sometimes become around there, causing investment-heavy waves otherwise.
Applications of Rapid Injection Molding
Rapid injection molding has its fingers in every pie – from automotive components, like interior and exterior parts of cars like dashboards and bumpers, all the way up to aerospace components made out of advanced materials such as carbon fiber-reinforced polymers. It’s even used in the consumer electronics industry to create casings for gadgets like phones and laptops.
However, it has a vital role in medical devices, with physicians relying on high-speed precision manufacturing of syringes, catheters, and other surgical instruments that can make a difference between life and death. Talk about pressure!
Cost Comparison: Rapid Injection Molding vs. Traditional Injection Molding
It’s essential to weigh all the factors when pitting the price tags of rapid injection molding against traditional injection molding. Tooling costs, material fees, labor costs, and production volume are just some of those considerations.
Creating custom molds for regular injection molding can be costly in time and money – how complex your part is and what materials you use will usually dictate the cost. In contrast, rapid injection molding obviates that almost entirely due to its ability to bypass customized molds.
Materials used in both processes are similar. However, batch sizes for rapid injections result in less running waste and inventory expenditure. As far as rates for manual labor go?
Automated processes come into play here, significantly lowering related expenses compared with traditional solutions. Consequently, if batches on a large-scale need whipping up, then classic methods may offer more cost 31558uggestive benefits. Still, when smaller runs have got to get going rapidly, there’s no competition – ask any boardroom suit or engineer alike.
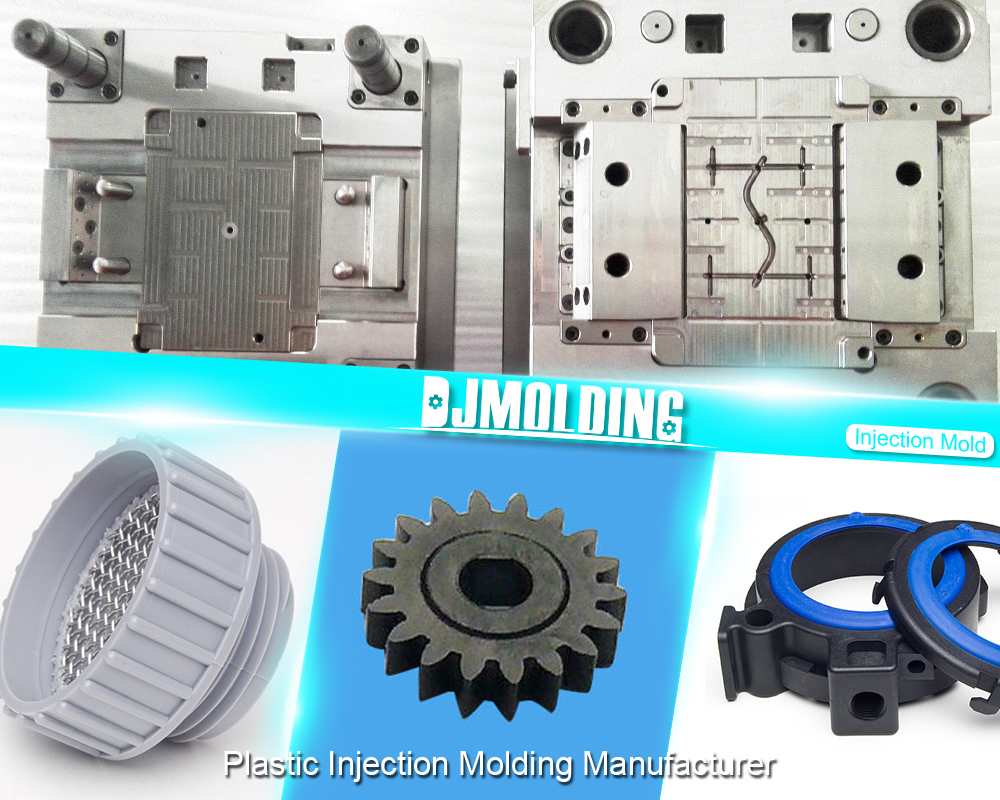
Final Thoughts
To wrap it up, rapid injection molding is a super-efficient manufacturing process, bringing plenty of perks to the table compared to the run-of-the-mill version. It offers faster production speeds and lower bills, which not only heed well for efficiency but also calm your nerves when quality counts too – something that rapid injection pulls off fantastically with its precision control over every detail imaginable! Mixing 3D printing into the system adds flexibility for design amendments as you create whatever shape your heart desires out of molten plastic.
It’s these characteristics that have made rapid injection invaluable in countless industries we encounter day to day. If going on price alone isn’t incentive enough, this should be: despite standard false alarms, high-end results like smooth surfaces and accurate dimensions come par for the course!
For more about what is rapid injection molding,you can pay a visit to Djmolding at https://www.djmolding.com/what-is-rapid-tooling-injection-molding-for-plastic-parts-manufacturing/ for more info.