What is Quick Turn Injection Molding?
What is Quick Turn Injection Molding?
Quick Turn Injection Molding is a manufacturing process that allows for rapid production of plastic parts. It is a highly efficient and cost-effective method that has revolutionized the manufacturing industry. With Quick Turn Injection Molding, companies can quickly produce high-quality parts in large quantities, reducing production time and costs.
This article will provide an in-depth understanding of Quick Turn Injection Molding, its benefits, applications, materials used, factors to consider for successful implementation, a comparison with traditional injection molding, choosing the right manufacturer, cost analysis, and the future of this technology in the manufacturing industry.
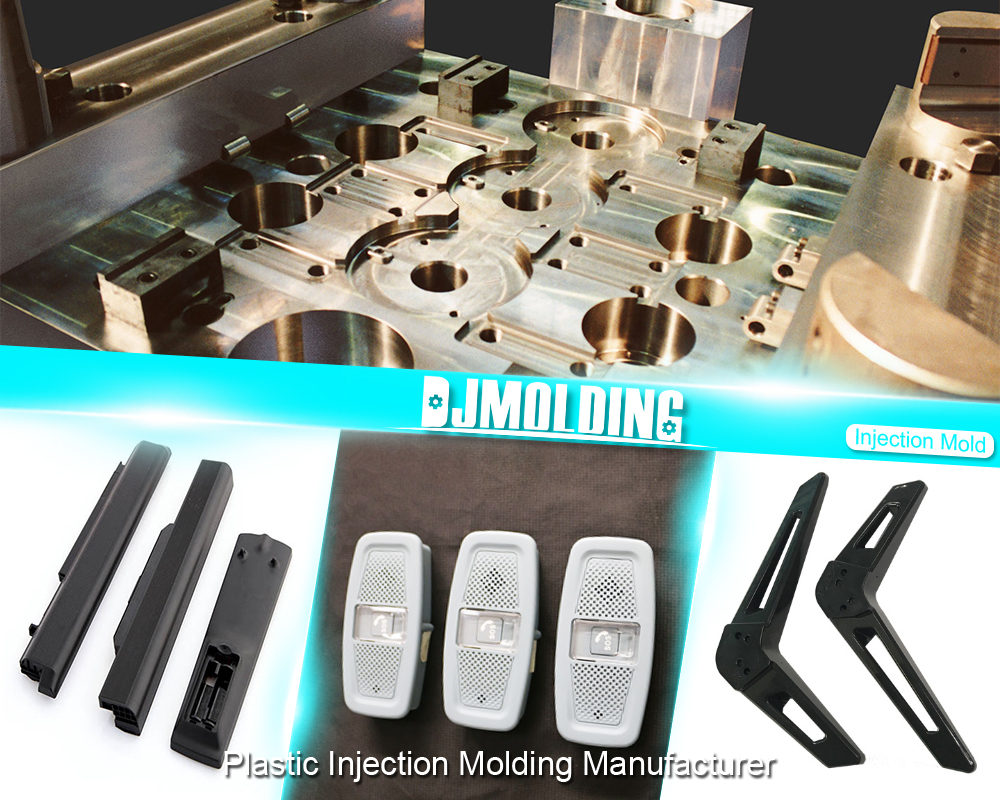
The Process of Quick Turn Injection Molding Explained
Quick Turn Injection Molding is a process that produces plastic parts like a pro. The part’s design – from shapes to features – must be programmed using CAD software. Then, CAM takes over and creates an exact mold of said design – all set to fit the precise size and capacity it needs for production.
The injection molding machine then ushers in its entrance by heating pellets of plastic, which are injected into the carefully constructed cavity under tremendous pressure before cooling them down to transform them into ready-to-go pieces.
Different tools play vital roles in this grand scheme of things, such as injection molders, molds (usually made with steel or aluminum), temperature controllers, and material dryers whose life mission is to control the heat level for good quality results, plus proper drying before injecting materials.
Yes indeed! This same method can scale itself depending on how large or complex you wish your part/s should turn out.
Benefits of Quick Turn Injection Molding
You already know that Quick Turn Injection Molding is the way to go for any manufacturing project. But why? First and foremost, it crams years of production into a fraction of the time – you can get high-grade parts in days or weeks instead of months – so you’re one step closer to market entry than anybody else.
Then there’s this little cost nugget, too – advanced automation means no labor costs, plus no need for expensive tooling or machining processes. It gets even juicier when we talk about quality! The exact control over molding parameters makes every part consistent and accurate with no deviation from blisteringly tight standard requirements.
Plus, it is cheap on materials because of the ability to produce large quantities at once feels like winning a double jackpot! And last but not least — design flexibility! Any changes are easily implemented without costly (and annoying) alterations in the tooling setup, meaning companies can swiftly adjust their products’ features according to rapidly changing demands from the market.
Applications of Quick Turn Injection Molding
Quick Turn Injection Molding is a go-to in various industries, one of the biggest being the automotive industry. It’s perfect for producing parts like dashboards, bumpers, and door panels in no time, helping automotive manufacturers save on time and cost.
It then comes as no surprise that this process also sees excellent demand from the medical sector – it tempts them with syringes, IV components, and surgical instruments made of top-notch quality paired off with flexible design tweaks.
Plus, getting convenient access to large quantities of affordable consumer goods or even intricate electronics components like connectors and housings.
Through precision molding capabilities plus fast turnaround abilities unmatched by its competitors – this process has earned itself quite a name in all corners of all markets.
Materials Used in Quick Turn Injection Molding
Quick Turn Injection Molding can be performed using various materials, depending on the requirements of the part being produced. Some of the commonly used materials include:
Polypropylene (PP)
This material is something special! Its chemical resistance and impact strength put it head and shoulders above its rivals. That’s why you see it in automotive part manufacturing and consumer goods production – it truly lives up to its reputation for versatility.
Acrylonitrile Butadiene Styrene (ABS)
ABS is a rock-solid material not fazed by smacks and scorching temperatures. Its use is ubiquitous in cars, electronics, and our daily products, demonstrating its versatility and strength.
Polycarbonate (PC)
PC is a crystal-clear material providing superior shock and heat protection, thus becoming popular with electronic and car companies. It’s the perfect option for those who maintain quality.
Polyethylene (PE)
PE is a lightweight material with good chemical resistance and low friction properties. It is commonly used in the packaging industry.
Polyvinyl Chloride (PVC)
PVC is no ordinary material; it’s the show’s real star! With its phenomenal chemical resistance and unbeatable flame retardancy, this stuff has earned itself a great rep in construction and consumer goods.
Factors to Consider for Successful Quick Turn Injection Molding
Design, material, tooling & equipment, and quality control are the mainstays of ensuring Quick Turn Injection Molding runs smoothly. Regarding design considerations, consider draft angles, wall thicknesses, and parting lines.
If you want injection molding that’ll flow, you must ensure your parts have easy transitions and uniform wall thickness for filling those molds. Next is picking the material best suited for your process: Strength, flexibility, heat resistance, and chemical stability should be considered when selecting what works.
For successful implementation, you need proper tooling and equipment, so ensure your mold is righteously designed and manufactured, plus adjust calibrations as needed for optimal machine performance!
Last but not least, solid quality control will help guarantee specs are met with regular inspections & testing to catch any warping/sink marks/voids misshaping your projects before they hit production mode. If you want to stay on the right side of regulations, document everything properly.
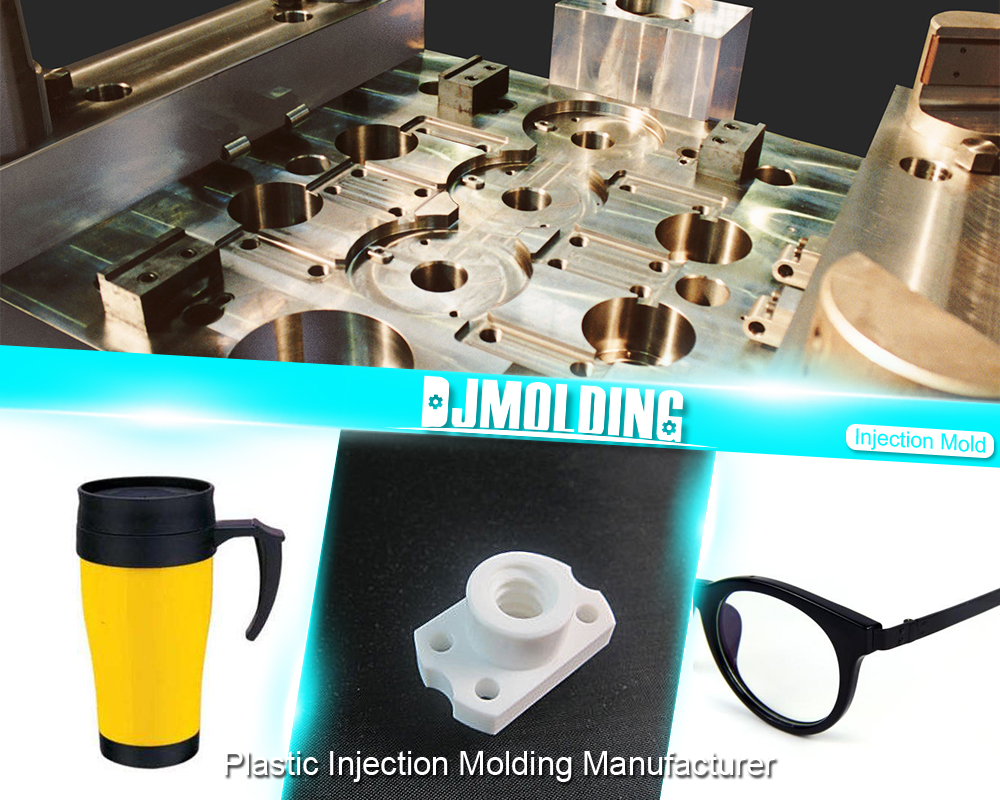
Last Words
Quick turn injection molding shook up the manufacturing industry. It’s remarkably efficient and affordable, quickly producing large batches of high-quality plastic parts – minus the hefty price tag! Talk about bang for your buck: you get a short turnaround time, lowered production costs, and added flexibility to make any tweaks or design changes along the way. The sky’s the limit, with potential applications spanning automotive, medical tech, consumer products & electronics; it truly is an invaluable resource.
For more about what is quick turn injection molding,you can pay a visit to Djmolding at https://www.djmolding.com/quick-turn-plastic-injection-molding-the-ultimate-guide-for-beginners/ for more info.