What Is Injection Molding Splay And How To Avoid It
What Is Injection Molding Splay And How To Avoid It
Injection molding is a popular manufacturing process for producing large-volume parts, especially with plastics. Despite its advantages, the process can present defects that compromise the quality and appearance of the final product. One such defect is “splay.” This article delves into splay in injection molding, its causes, and practical prevention strategies.
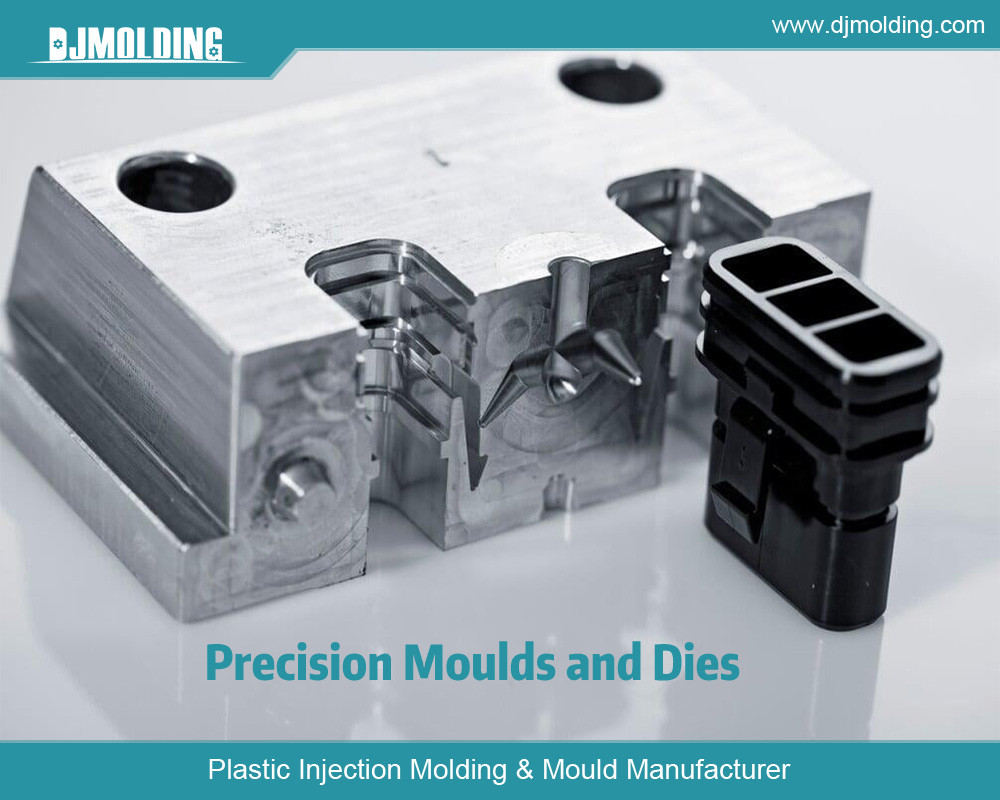
Understanding Injection Molding Splay
Splay, also known as “silver streaks,” is a surface defect in injection-molded parts that appears as streaks, lines, or clouds. It typically manifests as a silvery, hazy, or uneven finish on the part’s surface. Splay affects the product’s appearance and may indicate underlying issues in the manufacturing process, potentially impacting the part’s structural integrity.
Splay often results from improper moisture control, incorrect temperatures, or air entrapment during molding. Understanding splay and its causes is essential for improving product quality, optimizing injection molding, and reducing waste.
Types of Splay
Splay in injection molding can arise from different sources, often leading to distinct appearances. The two main types of splay are:
- Moisture-Induced Splay: This type of play occurs when excess moisture is present in the material, usually due to inadequate drying or improper storage. When exposed to high temperatures during molding, this moisture turns to steam and forms streaks or marks on the part’s surface.
- Gas-Induced Splay: Gas-induced splay arises from trapped air, volatiles, or residual gases in the material. When these gases cannot escape, they create streaks or silver lines on the part’s surface.
Although these types of splay may look similar, each requires different preventive measures. Identifying the root cause is crucial for selecting the most appropriate solution.
Causes of Splay in Injection Molding
Various factors contribute to splay formation in injection molding. Below are some common causes:
- Moisture Content: Moisture is one of the leading causes of splay, especially with hygroscopic materials like nylon, ABS, and polycarbonate. Improper drying can turn moisture into steam during injection, creating streaks on the part’s surface.
- Excessive Temperature: If the material is heated beyond its optimal range, it can lead to thermal degradation, releasing gases. These gases can form streaks and splay on the surface.
- Inadequate Venting: Proper venting is essential in the injection molding to allow trapped air and gases to escape. When venting is insufficient, these gases become trapped within the mold cavity, leading to splay.
- Injection Speed and Pressure: High injection speeds and pressures can create turbulence in the melt flow, leading to gas entrapment. This turbulence causes trapped air or gas bubbles, which result in splay when they reach the part’s surface.
- Material Quality: Low-quality or contaminated materials can also contribute to splay. When exposed to high temperatures, contaminants may release gases, leading to streaks or cloudy appearances on the part.
- Improper Melt Flow: Poor melt flow characteristics due to the wrong material choice or setup can create turbulence, leading to splay. Using materials with poor flow properties can make it harder for gases to escape, causing defects on the part’s surface.
Strategies to Avoid Splay in Injection Molding
Preventing splay involves a combination of material preparation, machine adjustments, and process optimization. Here are some best practices for avoiding splay:
Material Preparation and Handling
- Proper Drying: Ensure the material is thoroughly dried before molding, especially for hygroscopic plastics like nylon or ABS. Most materials have recommended drying times and temperatures that should be followed.
- Use of Dehumidifying Dryers: Consider using dehumidifying dryers that control the moisture content precisely. Dehumidifiers remove more moisture than hot-air dryers, which helps prevent moisture-induced splay.
- Storage Conditions: Store materials in a controlled environment to minimize moisture absorption. If possible, use airtight containers and dehumidified storage rooms.
Optimize Temperature Settings
- Control Melt Temperature: Set and monitor the melt temperature carefully to avoid overheating. Excessive temperatures can cause thermal degradation, leading to gas formation and splay.
- Proper Heater Band Calibration: Regularly check and calibrate heater bands to ensure accurate temperature settings. Faulty bands can lead to uneven heating and increase the risk of splay.
- Gradual Temperature Adjustments: Make gradual changes to temperature settings rather than large jumps to prevent unintended effects on the melt’s flow characteristics.
Improve Venting in the Mold
- Add or Enhance Vents: Ensure the mold is adequately vented to allow trapped gases to escape. Adding vents at critical points can alleviate gas build-up and reduce splay.
- Check and Maintain Vent Cleanliness: Clean the vents regularly to remove blockages. Dirt and debris can block vents, leading to trapped gases and increased splay.
- Use Vacuum Venting: In cases where conventional venting is insufficient, consider using vacuum venting systems to help remove trapped air effectively.
Optimize Injection Speed and Pressure
- Reduce Injection Speed: Lowering the injection speed reduces turbulence in the melt flow, minimizing the chance of gas entrapment that leads to splay.
- Adjust Pressure Carefully: High injection pressure may cause gases to become trapped within the part. Adjust the Pressure to ensure proper filling without causing excessive turbulence.
- Use Sequential Filling Techniques: In cases where high injection speed or Pressure is necessary, consider using sequential filling techniques that control the flow rate in multiple stages, reducing the potential for splay.
Ensure High-Quality Materials
- Inspect Material Quality: Use high-quality, contamination-free materials to prevent splay due to impurities. Regrind materials should be checked for contaminants before reuse.
- Test for Volatile Compounds: Some materials may contain additives that release volatile compounds during heating. Use grades with lower volatiles or process them at recommended temperatures.
- Use Antioxidants if Needed: For materials susceptible to thermal degradation, consider using antioxidants to prevent gas formation and degradation.
Additional Process Control Tips to Prevent Splay
Consistent process control is crucial in injection molding to prevent defects, including splay. Implementing the following practices can enhance process stability and reduce splay risk:
Regular Mold Maintenance
Mold maintenance helps prevent issues that can contribute to splay. Over time, molds can accumulate dust, plastic residues, and wear, which may compromise venting efficiency and lead to splay. Clean molds thoroughly between production runs and inspect for signs of wear or damage.
Temperature and Humidity Control
Keep the molding environment controlled in terms of temperature and humidity. Excess humidity in the production area can lead to moisture absorption by the material, increasing the risk of splay.
Conducting Trial Runs and Testing
When introducing new materials or making significant process changes, conduct trial runs to monitor for any changes in part quality, especially splay. Testing enables early detection of issues and allows adjustments before full-scale production begins.
Training and Skill Development
Equip operators and technicians with knowledge and skills to recognize splay and its causes. A well-trained team can proactively address issues by adjusting settings or spotting anomalies in the injection molding process before they result in defective parts.
Diagnosing Splay in Injection Molding
When splay appears on molded parts, diagnosing the specific cause is essential to select the most effective solution. Here is a step-by-step approach to diagnosing splay:
- Visual Inspection: Examine the surface defect to determine whether it resembles moisture-induced or gas-induced splay. Moisture splay often appears cloudier, while gas splay has a more streaky, silver look.
- Analyze Processing Parameters: Review the injection speed, Pressure, melt temperature, and mold temperature to determine if any settings deviate from recommended levels.
- Material Moisture Test: Conduct a moisture test for hygroscopic materials to ensure the material is dry. Use a moisture analyzer, if available, to check the material’s moisture content.
- Check for Contaminants: Examine the material and mold for foreign substances or residues. Contaminants are a common but overlooked cause of splay, especially when reusing materials.
- Evaluate Mold Venting: Inspect the mold’s venting system and check for blockages or wear signs. Use airflow tests if necessary to ensure proper venting.
Conclusion
Splay is a common but preventable defect in injection molding that affects the quality and appearance of parts. By understanding the different causes of splay—such as moisture content, gas entrapment, excessive temperature, and inadequate venting—manufacturers can implement targeted solutions to mitigate this issue. Proper material handling, optimized processing parameters, and regular mold maintenance are pivotal in preventing splay and ensuring high-quality, defect-free molded parts.
Investing time in diagnosing and addressing splay early in the production process helps minimize costly reworks, reduce waste, and improve customer satisfaction. Manufacturers can significantly enhance product quality and maintain a stable, efficient injection molding operation by following best practices in material preparation, process optimization, and mold design.
For more about what is injection molding splay and how to avoid it, you can pay a visit to Djmolding at https://www.djmolding.com/ for more info.