What are the types of injection molding?
What are the types of injection molding?
Injection molding is a widely used manufacturing process for producing parts by injecting molten material into a mold. It creates many products, from plastic components in everyday consumer goods to intricate parts used in various industries. This article will delve into the different types of injection molding, their applications, their advantages, and how they contribute to modern manufacturing.
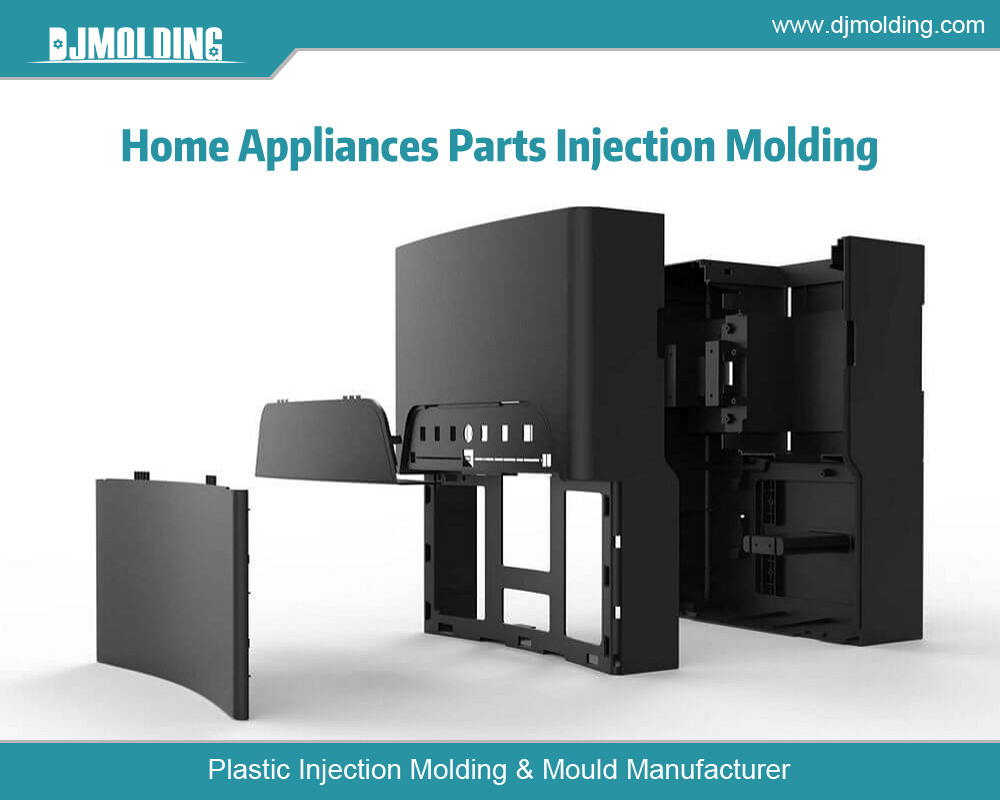
Standard Injection Molding
Overview
Standard injection molding is the most common type. It involves melting plastic resin and injecting it into a mold cavity, which cools and solidifies into the desired shape. The process is highly versatile and can produce large volumes of parts with high precision.
Applications
Standard injection molding is used across numerous industries, including automotive, consumer goods, electronics, and medical devices. Standard products include plastic bottles, toys, and automotive components.
Advantages
- High Efficiency: Once the molds are created, production is rapid, allowing for high output rates.
- Cost-Effective for Large Volumes: The initial investment in molds is high, but the cost per part decreases significantly with large production runs.
- Design Flexibility: Complex shapes and detailed designs can be achieved.
- Consistency and Precision: The process offers high repeatability and accuracy.
Overmolding
Overview
Overmolding is a process that involves molding one material over another. It usually consists of a base material (substrate) and an overmold material that can be the same or different. This process enhances the functional and aesthetic properties of the final product.
Applications
Overmolding is commonly used to manufacture toothbrushes (with a rubberized grip), electronic device housings, and automotive parts requiring different strength and flexibility materials.
Advantages
- Improved Grip and Feel: Overmolding can add soft-touch grips and ergonomic features.
- Enhanced Durability: Provides additional protection against wear, impact, and environmental factors.
- Aesthetic Appeal: Allows for multi-material and multi-color designs.
Insert Molding
Overview
Insert molding involves placing a pre-formed insert (usually metal) into the mold before injecting the plastic. The plastic then flows around the insert, creating a single solid piece.
Applications
Insert molding creates components that require metal inserts, such as threaded parts, electrical connectors, and fasteners.
Advantages
- Enhanced Strength: Combines the strength of metal with the versatility of plastic.
- Cost Savings: Reduces the need for secondary assembly processes.
- Design Versatility: Allows for integrating different materials into a single component.
Gas-Assisted Injection Molding
Overview
Gas-assisted injection molding involves injecting an inert gas (usually nitrogen) into the mold cavity after the plastic has been injected. The gas creates hollow sections within the part, reducing weight and material usage while maintaining strength.
Applications
This method is commonly used for large, complex parts with thick walls, such as automotive components, furniture, and appliances.
Advantages
- Material Savings: Reduces the amount of plastic needed.
- Lightweight Parts: Creates lighter parts without compromising strength.
- Reduced Warping and Sink Marks: Improves the cosmetic appearance of the parts.
Co-Injection Molding
Overview
Co-injection or sandwich molding involves injecting two different materials into the mold. Typically, a core material is injected first, followed by a skin material. This creates a part with other properties in the core and outer layers.
Applications
Co-injection molding is used to produce parts that require a combination of properties, such as strength in the core and aesthetic appeal on the surface. Examples include automotive interiors and packaging materials.
Advantages
- Material Efficiency: Allows recycled or less expensive materials in the core.
- Enhanced Properties: Combines the strengths of different materials.
- Improved Aesthetics: High-quality finish on the outer layer.
- Thin-Wall Injection Molding
Overview
Thin-wall injection molding focuses on producing parts with fragile walls, usually less than 1 mm. This requires specialized equipment and precise control over the molding process.
Applications
Thin-wall molding is essential for producing lightweight, high-strength parts in the electronics, telecommunications, and medical device industries. Standard products include smartphone casings and medical device housings.
Advantages
- Reduced Material Usage: Produces lighter parts with less plastic.
- High Strength-to-Weight Ratio: Maintains strength despite reduced material.
- Fast Cycle Times: Shorter cooling times due to thin walls.
Micro Injection Molding
Overview
Micro injection molding produces tiny and precise parts, often with features measured in micrometers. This process requires specialized machines capable of handling minute amounts of material and maintaining tight tolerances.
Applications
Microinjection molding is critical in medical devices, electronics, and micromechanical parts. Examples include microgears, tiny medical implants, and microfluidic devices.
Advantages
- High Precision: Capable of producing intricate, detailed parts.
- Small Part Production: Ideal for miniature components.
- Tight Tolerances: Maintains strict dimensional accuracy.
- Liquid Silicone Rubber (LSR) Injection Molding
Overview
LSR injection molding uses liquid silicone rubber, a material known for its flexibility, heat resistance, and biocompatibility. The process is similar to standard injection molding but requires specialized equipment to handle LSR’s unique properties.
Applications
LSR injection molding is widely used in medical devices, baby products, kitchenware, and automotive seals and gaskets.
Advantages
- Heat and Chemical Resistance: Ideal for applications requiring durability in harsh environments.
- Flexibility and Elasticity: Suitable for parts needing flexibility.
- Biocompatibility: Safe for medical and food contact applications.
- Reaction Injection Molding (RIM)
Overview
Reaction injection molding involves mixing two liquid components that chemically react and expand to fill the mold. The process is used to produce lightweight, durable parts with complex geometries.
Applications
RIM is commonly used in bumpers, dashboards, and other large parts in the automotive industry. It is also used to produce furniture and industrial equipment.
Advantages
- Lightweight Parts: Produces parts with low density and high strength.
- Complex Geometries: Capable of molding intricate shapes.
- Material Versatility: Allows the use of various polymers and composites.
Powder Injection Molding (PIM)
Overview
Powder injection molding combines traditional plastic injection molding with powder metallurgy. The process involves mixing metal or ceramic powders with a binder, injecting the mixture into a mold, removing the binder, and sintering the part.
Applications
PIM produces metal or ceramic parts that require high precision, such as components for medical devices, firearms, and aerospace applications.
Advantages
- High Precision: Capable of producing detailed parts with tight tolerances.
- Material Diversity: Allows for the use of various metals and ceramics.
- Complex Shapes: Suitable for intricate and detailed designs.
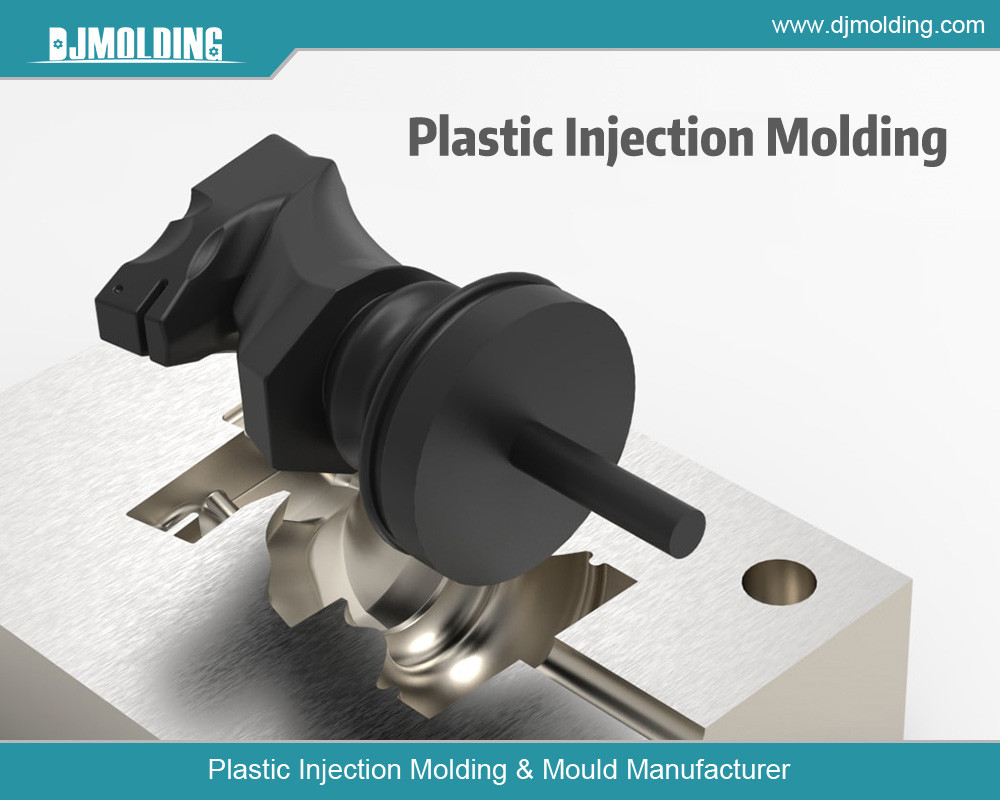
Conclusion
Injection molding is a versatile manufacturing process that can be adapted to produce various products across various industries. The different types of injection molding, from standard and over-molding to specialized processes like microinjection and powder injection molding, each offer unique benefits tailored to specific applications. Understanding these processes allows manufacturers to choose the most suitable method for their production needs, optimizing efficiency, cost, and product quality.
For more about what are the types of injection molding,you can pay a visit to Djmolding at https://www.djmolding.com/different-types-of-injection-molding-technology-for-plastic-parts-manufacturing-companies/ for more info.