Understanding PET Injection Molding: A Comprehensive Guide
Understanding PET Injection Molding: A Comprehensive Guide
Injection molding is a highly efficient manufacturing process that has transformed the production of various plastic products. Polyethylene Terephthalate (PET) has gained immense popularity among the materials used in injection molding due to its exceptional properties and versatility. PET injection molding is crucial in producing high-quality components for various industries, including packaging, automotive, and consumer goods. This article aims to provide a detailed overview of PET injection molding, exploring its advantages, applications, processes, and future trends.
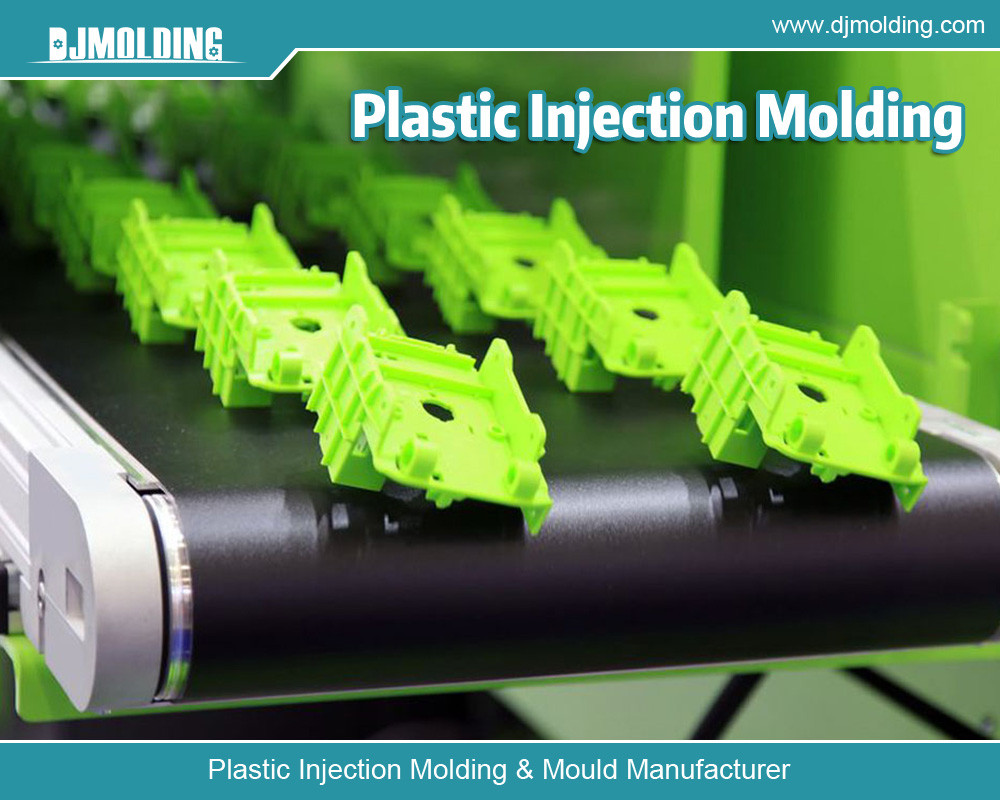
What is PET?
Polyethylene Terephthalate (PET) is a thermoplastic polymer belonging to the polyester family. It is widely used for its strength, durability, and resistance to moisture and chemicals. PET can be easily molded into various shapes and forms, making it an ideal choice for injection molding processes.
Key Characteristics of PET
- High Strength-to-Weight Ratio: PET is lightweight yet robust, essential for many applications.
- Chemical Resistance: It resists degradation from acids and bases, making it suitable for packaging food and beverages.
- Thermal Stability: PET can withstand high temperatures, maintaining structural integrity during processing and usage.
- Recyclability: PET is highly recyclable, making it an environmentally friendly choice for manufacturers and consumers.
The Injection Molding Process
The injection molding process involves several stages, from material preparation to the final product. Understanding each stage is crucial for maximizing efficiency and product quality.
Material Preparation
- Drying: PET pellets are dried to remove moisture content, which can affect the molding process and the final product’s quality.
- Feeding: The dried pellets are fed into the injection molding machine’s hopper.
Injection Phase
- Melting: The pellets are heated and melted in the barrel of the injection molding machine.
- Injection: The molten PET is injected into a pre-designed mold under high pressure, ensuring the material fills the cavity completely.
Cooling and Solidification
- After the injection, the mold is cooled, allowing the PET to solidify and take the mold’s shape.
- Cooling time varies based on the part’s thickness and the mold design’s complexity.
Ejection
- Once the part is cooled and solidified, it is ejected from the mold using ejector pins.
- The cycle then repeats for the production of subsequent parts.
Advantages of PET Injection Molding
PET injection molding offers numerous benefits, making it a preferred choice for various applications.
High Production Efficiency
- Rapid Cycle Times: The injection molding process allows quick production cycles, increasing output and efficiency.
- Automation: Many injection molding processes reduce labor costs and human error.
Cost-Effectiveness
- Material Savings: The precision of injection molding minimizes material waste, leading to cost savings.
- Mass Production: Ideal for high-volume production, reducing the cost per unit.
Design Flexibility
- Complex Shapes: Injection molding allows for creating intricate designs and complex geometries.
- Customizability: Different mold designs can accommodate various product shapes and sizes.
Improved Quality
- Consistency: Injection molding produces parts with uniform dimensions and properties, enhancing product quality.
- Reduced Defects: The controlled injection molding environment minimizes defects and improves overall reliability.
Applications of PET Injection Molding
PET injection molding is utilized in numerous industries, highlighting its versatility and adaptability.
Packaging Industry
- Containers and Bottles: PET is widely used to manufacture bottles for beverages, cosmetics, and household products.
- Food Packaging: Its chemical resistance makes it ideal for food containers, ensuring product safety and longevity.
Automotive Industry
- Interior Components: PET is used in manufacturing dashboards, door panels, and other interior parts due to its lightweight and strength.
- Exterior Parts: Its durability makes it suitable for exterior automotive components requiring weather and impact resistance.
Consumer Goods
- Household Items: PET injection molding is used for household products, including storage containers, kitchenware, and toys.
- Electronics: The electronics industry utilizes PET for various components due to its insulating properties and heat resistance.
Challenges in PET Injection Molding
Despite its advantages, PET injection molding has specific challenges that manufacturers must address.
Material Limitations
- Brittleness: While PET is strong, it can become brittle at low temperatures, affecting its application in colder environments.
- Moisture Sensitivity: PET is sensitive to moisture, which can impact molding if not adequately dried.
Processing Challenges
- High Processing Temperatures: PET requires higher processing temperatures compared to other thermoplastics, which can lead to increased energy costs.
- Cycle Time Optimization: Achieving optimal cycle times while maintaining product quality can be challenging, especially for complex molds.
Innovations in PET Injection Molding
Advancements in technology and materials science continue to enhance the capabilities of PET injection molding.
Additive Manufacturing
- 3D Printing Integration: Combining additive manufacturing with injection molding allows rapid prototyping and design validation, streamlining product development.
Bio-Based PET
- Sustainable Alternatives: The development of bio-based PET from renewable resources reduces dependency on fossil fuels, making the manufacturing process more sustainable.
Improved Mold Designs
- Hot Runner Systems: Hot runner technology reduces material waste and improves cycle times by keeping the plastic molten throughout the injection process.
Environmental Considerations
The plastic industry is pressured to adopt more sustainable practices as environmental concerns grow. PET injection molding offers several environmentally friendly benefits.
Recyclability
- Closed-Loop Recycling: PET can be recycled multiple times without significantly degrading its properties, promoting a circular economy.
Reduced Waste
- Precision Manufacturing: The accuracy of injection molding minimizes scrap, reducing the overall environmental impact.
Future Trends in PET Injection Molding
The future of PET injection molding is bright, driven by technological advancements and a growing focus on sustainability.
Automation and Smart Manufacturing
- Industry 4.0: Integrating IoT and intelligent manufacturing technologies will enhance efficiency, allowing for real-time monitoring and predictive maintenance.
Increased Demand for Sustainable Products
- Eco-Friendly Alternatives: The growing consumer preference for sustainable products will drive innovation in PET materials and manufacturing processes.
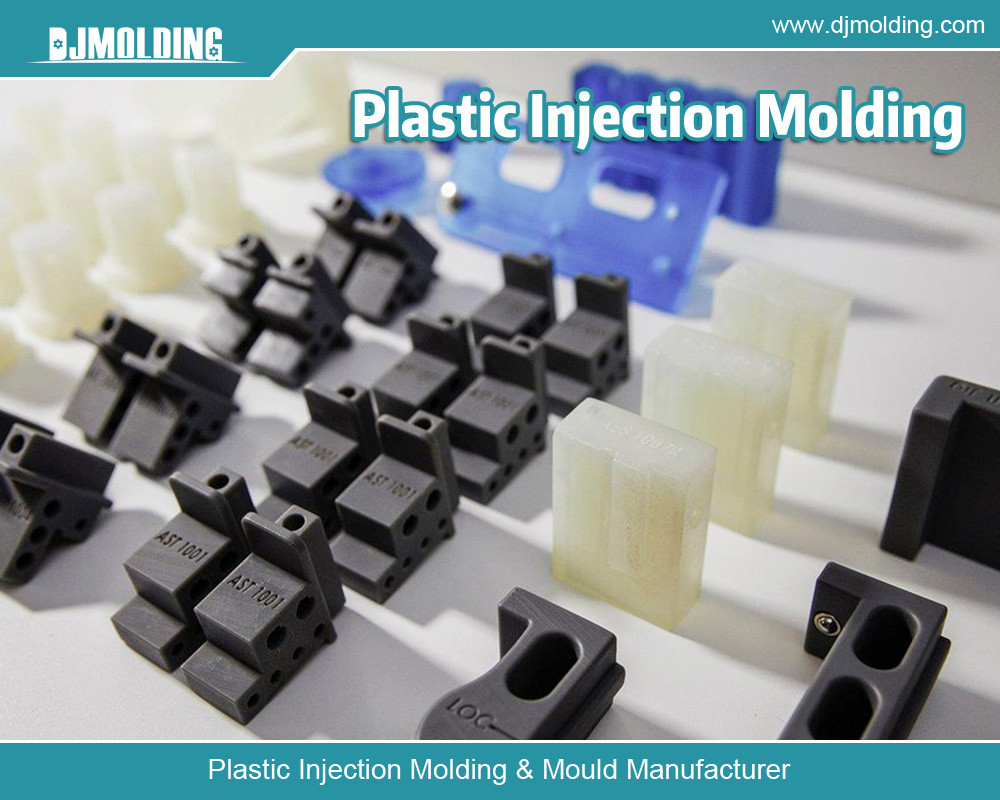
Conclusion
PET injection molding is a vital manufacturing process that combines efficiency, versatility, and quality, making it an integral part of various industries. As the demand for high-quality plastic products continues to grow, advancements in technology and a focus on sustainability will shape the future of PET injection molding. By addressing current challenges and leveraging innovations, manufacturers can ensure this essential process’s continued success and environmental responsibility.
By understanding the intricacies of PET injection molding, stakeholders can make informed decisions that enhance product quality, optimize processes, and contribute to a sustainable future.
For more about understanding pet injection molding: a comprehensive guide, you can pay a visit to Djmolding at https://www.djmolding.com/ for more info.