Types Of Gating System For Plastic Injection Mold Design
Types Of Gating System For Plastic Injection Mold Design
Plastic injection molding is a widely used manufacturing process for producing high-quality plastic parts. Central to this process’s success is the gating system’s design, which plays a crucial role in ensuring the efficient and effective flow of molten plastic into the mold cavities. The gating system impacts the final product’s quality, performance, and cost. This article delves into the various aspects of gating system design for plastic injection molds, highlighting key considerations, types of gating systems, design principles, and practical applications.
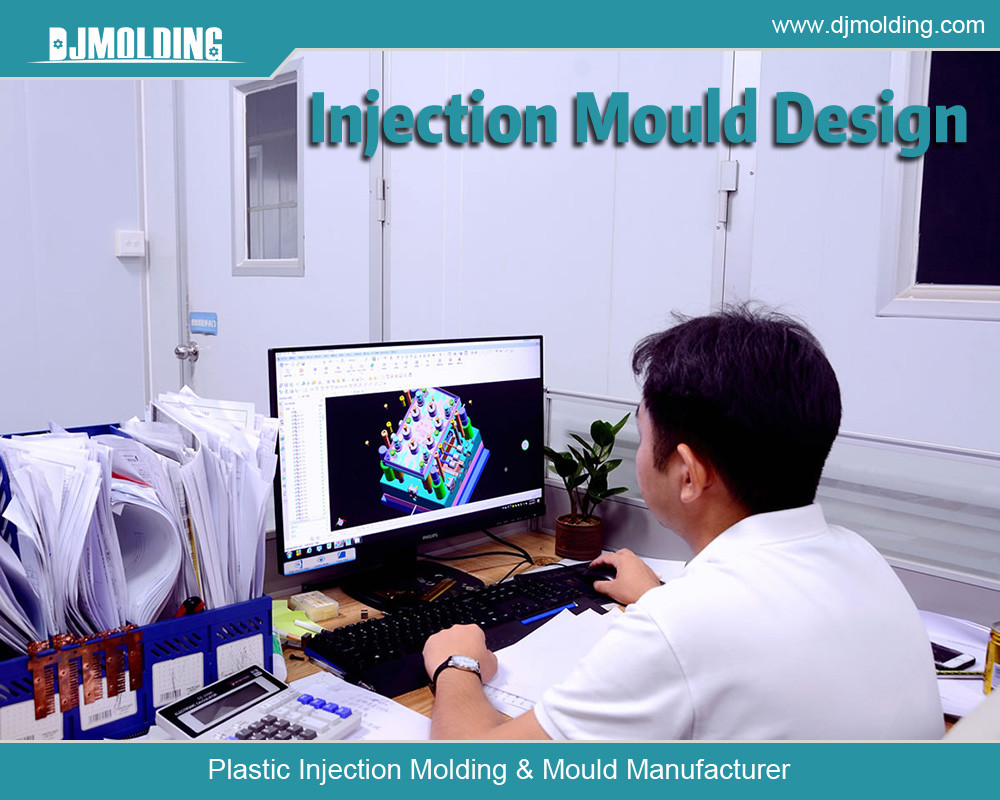
Importance of Gating System Design
The gating system is a network of channels that guides molten plastic from the injection unit into the mold cavities. Its design is critical for several reasons:
- Uniform Filling: A well-designed gating system ensures uniform filling of the mold cavities, reducing the risk of defects such as voids, sink marks, and warpages.
- Cycle Time: Optimized gating can reduce cycle time by enabling faster and more consistent filling, directly impacting productivity.
- Material Efficiency: Proper gating minimizes material wastage by reducing the volume of runners and gates, thereby enhancing material utilization.
- Quality Control: The gating system influences the final product’s mechanical properties, surface finish, and dimensional accuracy.
Critical Considerations in Gating System Design
Several factors must be considered when designing a gating system:
- Material Properties: Different plastics have varying flow characteristics, shrinkage rates, and thermal properties, influencing gate design.
- Part Geometry: Complex geometries may require multiple gates or specific gate placements to ensure complete and even filling.
- Production Volume: High-volume production might justify more complex gating systems that optimize cycle time and material usage.
- Aesthetic Requirements: Visible gate marks must be minimized or placed in non-visible areas to maintain the aesthetic quality of the part.
- Mechanical Requirements: Gates should be placed to reduce stress concentrations and preserve the mechanical integrity of the part.
Types of Gating Systems
There are several types of gating systems, each suited for different applications and materials:
- Direct Gating: This system involves a single gate directly from the sprue to the cavity, also known as sprue gating. It is simple and cost-effective but may not be suitable for large or complex parts due to the potential for uneven filling.
- Edge Gating: This type places the gate on the edge of the part. It is commonly used for flat, thin parts and provides reasonable control over filling and packing.
- Submarine (Tunnel) Gating: The gate is below the parting line, and the runner is automatically trimmed during ejection. This method is suitable for automated production and high-volume runs.
- Fan Gating: A wide, shallow gate spreads the molten plastic across a broad area, reducing the risk of flow lines and improving surface finish. It is often used for large or flat parts.
- Diaphragm Gating: Used for cylindrical or symmetrical parts, this method places a gate around the part’s circumference, ensuring even filling.
- Hot Runner Systems: These systems keep the plastic molten within the runners, reducing waste and cycle time. They are ideal for high-volume production and complex parts but involve higher initial costs.
Design Principles for Gating Systems
Designing an effective gating system involves several principles and best practices:
- Gate Location: The gate should be placed to ensure balanced filling, avoiding areas that may cause weld lines or air traps. For complex parts, simulation software can help optimize gate placement.
- Gate Size: The gate size affects the plastic’s flow rate and cooling rate. A more enormous gate reduces pressure drop and ensures faster filling but may leave a more significant gate mark. The gate size should be carefully calculated based on the material and part requirements.
- Runner Design: The runner channels should minimize pressure loss and ensure uniform flow. Runners should be as short as possible while maintaining a balanced flow to all cavities.
- Cooling Considerations: The gating system should promote uniform cooling, preventing thermal gradients leading to warpage and dimensional inaccuracies.
- Ejection System: The design should facilitate easy ejection of the part and the runner system, minimizing cycle time and potential damage to the part.
Practical Applications and Case Studies
Case Study 1: Automotive Component
An automotive manufacturer needed to produce a complex plastic component with stringent dimensional tolerances and a high-quality surface finish. After analyzing the part geometry and material properties, a hot runner system with edge gating was chosen. This design ensured even filling and reduced cycle time, meeting the high production volume requirements.
Case Study 2: Consumer Electronics Housing
A consumer electronics company required housing for a new device, prioritizing aesthetic quality and minimal visible gatemarks. A fan gating system was employed, distributing the plastic evenly across the surface and minimizing flow lines. The result was a high-quality part with a smooth finish.
Case Study 3: Medical Device
A medical device manufacturer needed a small, precise part with stringent mechanical properties. A submarine gating system was selected, allowing automated production and reducing the risk of contamination. The gate location and size were optimized to ensure mechanical integrity and dimensional accuracy.
Advanced Techniques in Gating System Design
Computer-Aided Engineering (CAE) and Simulation
Modern gating system design heavily relies on CAE tools and simulation software. These tools enable designers to visualize plastic flow within the mold, predict potential issues, and optimize gate placement and size. Simulation can reduce the number of trial-and-error iterations, saving time and cost.
Conformal Cooling
Conformal cooling involves designing cooling channels that follow the part’s contours, providing more efficient and uniform cooling. This technique can significantly reduce cycle time and improve part quality, particularly for complex geometries.
Additive Manufacturing of Mold Components
Additive manufacturing (3D printing) allows for creating complex, custom gating systems that would be difficult or impossible to produce with traditional machining methods. This technology enables greater design flexibility and can lead to more efficient and effective gating solutions.
Challenges and Solutions in Gating System Design
Balancing Flow and Pressure
Ensuring uniform flow and pressure distribution within the mold is a common challenge. Uneven flow can lead to defects such as warpages and voids. Advanced simulation tools and careful design of runner systems can help achieve a balanced flow.
Gate Vestige
The remnant of the gate on the finished part, known as the gate vestige, can affect the product’s aesthetic and functional quality. Optimizing gate size and location and post-processing techniques can minimize gate vestige.
Material-Specific Considerations
Different materials require specific gating strategies. For example, crystalline polymers may require more enormous gates due to their higher shrinkage rates, while amorphous polymers benefit from smaller gates to control the flow rate. Understanding material properties and their impact on gating design is essential.
Future Trends in Gating System Design
Bright Molds and Industry 4.0
The integration of sensors and intelligent technologies into molds is becoming increasingly common. These bright molds can monitor real-time pressure, temperature, and flow data, enabling dynamic adjustments to the gating system for optimal performance.
Sustainable Gating Solutions
With growing environmental concerns, there is a push towards more sustainable gating solutions. This includes designing gating systems that reduce material waste, using biodegradable or recyclable materials, and implementing energy-efficient production processes.
Enhanced Simulation Capabilities
Advancements in simulation technology, including AI-driven optimization and more accurate material models, are set to improve gating system design further. These tools will provide even greater precision in predicting and preventing potential issues.
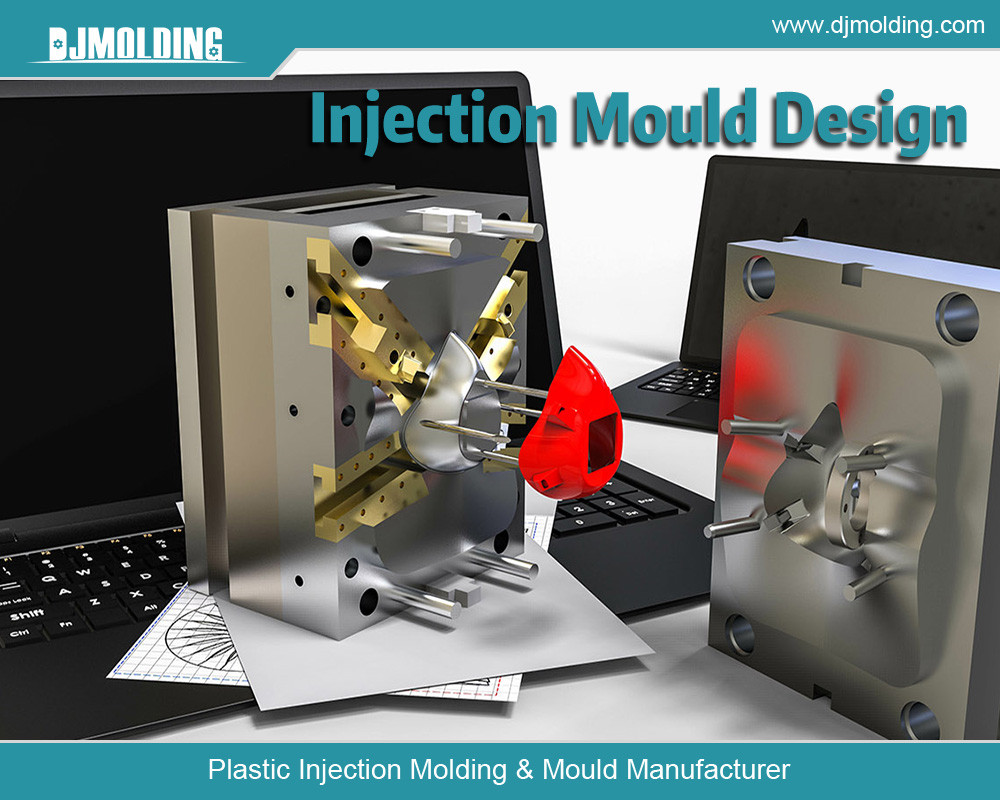
Conclusion
The gating system is a critical component in plastic injection mold design, significantly impacting the final product’s quality, efficiency, and cost. By understanding the principles of gating system design, considering material and part requirements, and leveraging advanced technologies, manufacturers can create optimized gating systems that meet the demands of modern production. As the industry evolves, continued innovation in gating system design will be vital in advancing plastic injection molding processes.
For more about types of gating system for plastic injection mold design,you can pay a visit to Djmolding at https://www.djmolding.com/a-simple-guide-to-injection-mold-gate-design/ for more info.