TPU vs TPE Injection Molding: Understanding The Differences, Applications, And Benefits
TPU vs TPE Injection Molding: Understanding The Differences, Applications, And Benefits
Injection molding is a popular and versatile manufacturing process, widely used for producing complex shapes and durable products across various industries. Recently, two thermoplastic elastomers, TPU (Thermoplastic Polyurethane) and TPE (Thermoplastic Elastomer), have become particularly prominent due to their flexibility, resilience, and ease of processing. Choosing between TPU and TPE for injection molding can be critical, as each material has unique properties that make it more or less suitable for specific applications.
In this article, we’ll explore the characteristics, advantages, limitations, and applications of TPU and TPE in injection molding to help manufacturers make informed decisions.
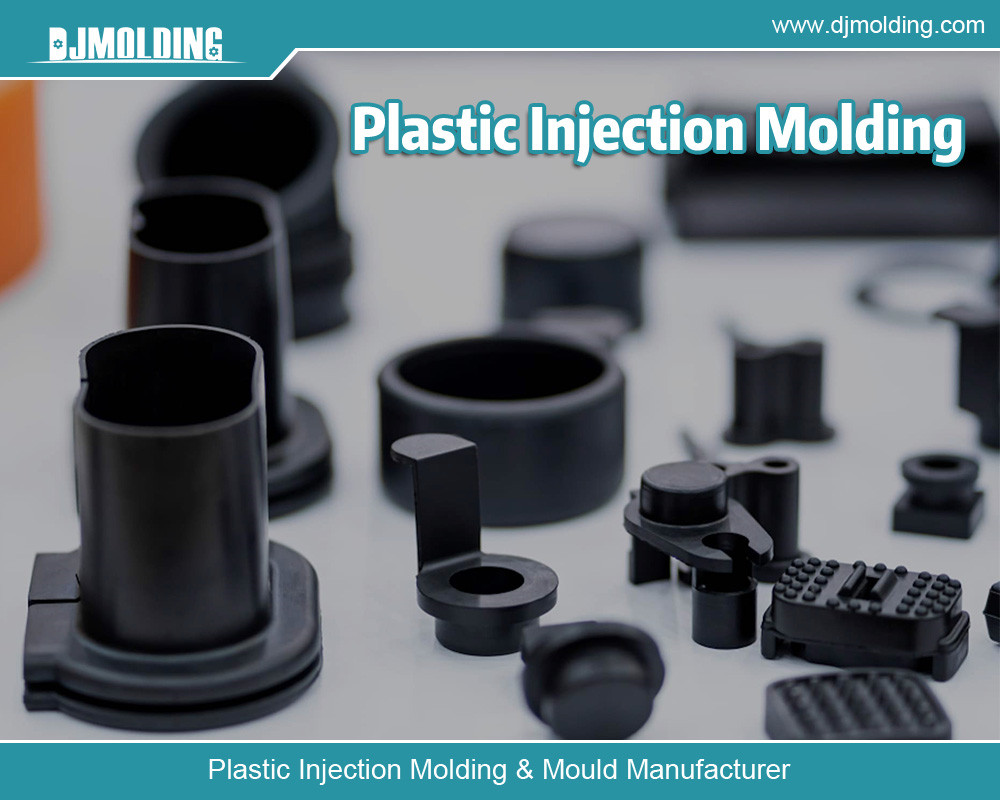
Understanding TPU and TPE: Basic Properties and Differences
Thermoplastic Polyurethane (TPU) and Thermoplastic Elastomer (TPE) are both thermoplastics with elastomeric properties, meaning they exhibit both plastic and rubber-like qualities. While both materials are often interchangeable in certain applications, they differ in their specific attributes, which can significantly impact the final product’s performance.
Thermoplastic Polyurethane (TPU)
TPU is a unique thermoplastic polymer known for its high elasticity, flexibility, and abrasion resistance. It is produced by reacting diisocyanates with polyols, creating a material that bridges the properties of rubber and plastic. The three main categories of TPU are based on the polyol used: polyester, polyether, and polycaprolactone. These types of TPU offer different levels of strength, abrasion resistance, and environmental resilience, catering to a wide range of applications.
- Hardness Range: TPU hardness can be adjusted, typically from Shore A 60 to Shore D 85, making it suitable for flexible and rigid parts.
- Flexibility and Elasticity: TPU has excellent flexibility, with high elongation at break and recovery, making it ideal for parts that require durability and impact resistance.
- Abrasion Resistance: TPU is known for its exceptional abrasion resistance, which is crucial for wear-resistant products like wheels, seals, and industrial belts.
- Temperature and Chemical Resistance: TPU exhibits good temperature stability, generally withstanding temperatures from -40°C to 80°C and moderate chemical resistance.
Thermoplastic Elastomer (TPE)
TPE is a broad category of materials that combine the characteristics of thermoplastics and elastomers, usually through a physical mixture of a rigid thermoplastic and a soft elastomer component. TPE encompasses various types, such as SBS (Styrene-Butadiene-Styrene), SEBS (Styrene-Ethylene-Butylene-Styrene), TPV (Thermoplastic Vulcanizate), and more, each with its specific properties and applications.
- Hardness Range: TPE also covers many hardness levels (Shore A 5 to Shore D 70), though softer TPEs are more commonly used for consumer products.
- Flexibility and Elasticity: TPE materials are highly flexible and provide a rubbery feel. They are often used in applications where comfort and flexibility are prioritized, such as grips, seals, and over-molding applications.
- Abrasion Resistance: TPEs have moderate abrasion resistance, generally lower than TPUs, but suitable for less demanding applications.
- Temperature and Chemical Resistance: TPEs can withstand moderate temperatures, though their chemical resistance may vary significantly depending on the specific type of TPE.
Advantages and Disadvantages of TPU and TPE in Injection Molding
TPU and TPE are highly adaptable to injection molding, though their specific characteristics lend themselves to distinct benefits and limitations.
Advantages of TPU in Injection Molding
- Durability and Longevity: TPU’s superior abrasion resistance ensures that products made with this material are long-lasting, even in demanding environments.
- Mechanical Strength: TPU’s tensile strength and tear resistance make it suitable for durable parts, such as industrial and automotive components.
- Versatility in Applications: TPU’s hardness and elasticity are tunable, allowing various uses, from soft grips to rigid automotive parts.
- Chemical Resistance: Certain TPUs (particularly polyester-based types) are highly resistant to oils, greases, and various chemicals, making them ideal for harsh environments.
Disadvantages of TPU in Injection Molding
- Cost: TPU tends to be more expensive than TPE due to its complex manufacturing process.
- Higher Processing Temperatures: TPU requires higher temperatures and longer cycle times during injection molding, increasing production costs.
- Limited Color Options: While TPU can be colored, it generally has fewer options than TPE, which can be a drawback for consumer products that rely on aesthetics.
Advantages of TPE in Injection Molding
- Ease of Processing: TPEs generally have lower melting points than TPU, allowing for faster cycle times and reduced energy consumption.
- Wide Range of Textures and Colors: TPE is available in numerous colors and textures, making it ideal for consumer products requiring aesthetic appeal and tactile variation.
- Cost-Effective: TPE is generally more affordable than TPU, making it a preferred choice for high-volume consumer goods.
- Good Adhesion in Over-Molding: TPE’s chemical structure enables strong adhesion to other materials, making it ideal for over-molding applications.
Disadvantages of TPE in Injection Molding
- Lower Abrasion Resistance: TPE does not have the same abrasion resistance as TPU, limiting its use in high-wear applications.
- Temperature Sensitivity: Some TPEs have lower heat resistance than TPUs, which can affect performance in high-temperature environments.
- Chemical Resistance Variability: While certain TPE types offer moderate chemical resistance, their performance is generally lower than that of TPUs in chemically demanding applications.
Applications of TPU and TPE in Different Industries
Understanding the specific strengths and weaknesses of TPU and TPE can help identify which material is best suited for a given application. Below are some key industries where TPU and TPE are commonly used and how each material fits into these sectors.
Automotive Industry
In the automotive sector, TPU is widely used for parts that require durability, abrasion resistance, and flexibility. Common applications include:
- Seals and Gaskets: TPU’s resilience and resistance to oils make it suitable for automotive seals and gaskets that endure harsh conditions.
- Protective Coatings: TPU is used for scratch-resistant coatings on automotive surfaces and parts, offering long-lasting protection.
- Air Ducts and Tubing: TPU’s flexibility and strength are ideal for air ducts and other tubing systems.
TPE, on the other hand, is often used in automotive interiors, where comfort and aesthetic appeal are prioritized:
- Interior Trim and Grips: TPE’s soft touch and range of colors make it suitable for interior trim, door handles, and grips.
- Wire and Cable Sheathing: Due to its flexibility, TPE is used to insulate and protect wires and cables in automotive electrical systems.
Consumer Electronics
TPU and TPE are extensively used in consumer electronics, and the choice depends on the application’s durability, feel, and aesthetic requirements.
- Phone Cases (TPU): TPU’s flexibility, shock absorption, and transparency make it popular for protective phone cases that require a snug fit.
- Earbud Cables and Connectors (TPE): TPE is used in earbud cables and connectors for its soft feel, flexibility, and ease of over-molding with rigid parts.
Medical and Healthcare
In medical applications, the biocompatibility and flexibility of both TPU and TPE make them suitable for various healthcare products.
- Catheters and Tubing (TPU): TPU is often used in medical tubing and catheters due to its flexibility, abrasion resistance, and biocompatibility.
- Wearable Devices (TPE): TPE’s soft touch and comfort make it suitable for wearable medical devices like wristbands and flexible enclosures for health monitors.
Sports and Recreation
The flexibility, impact resistance, and cushioning properties of TPU and TPE make them well-suited for sports equipment and recreational products.
- Soles of Athletic Shoes (TPU): TPU’s high abrasion resistance and cushioning properties make it an ideal material for athletic shoe soles.
- Soft Grips and Handles (TPE): TPE’s tactile softness and grip make it suitable for the handles of sports equipment, such as racquets and gym equipment.
Industrial Applications
In industrial settings, TPU is frequently preferred for parts that experience heavy wear and require high durability, while TPE finds applications in less demanding, more aesthetic roles.
- Conveyor Belts and Rollers (TPU): TPU’s abrasion resistance and load-bearing capacity make it suitable for conveyor belts and rollers in industrial environments.
- Grips and Protective Covers (TPE): TPE’s lower cost and easy processing make it a good choice for protective covers and grips on tools.
TPU vs. TPE: Key Factors for Material Selection in Injection Molding
When choosing between TPU and TPE for injection molding, several factors come into play:
- Performance Requirements: For applications requiring high wear resistance and load-bearing capabilities, TPU is generally the better choice, while TPE excels in softer, more flexible applications.
- Production Costs: TPE is typically more cost-effective due to lower processing temperatures and faster cycle times, making it ideal for high-volume production.
- Environmental Factors: If the product will be exposed to chemicals, extreme temperatures, or heavy wear, TPU’s resilience makes it a more suitable option.
- Aesthetic Requirements: TPE’s range of colors and textures makes it preferable for consumer products that require aesthetic appeal and a softer feel.
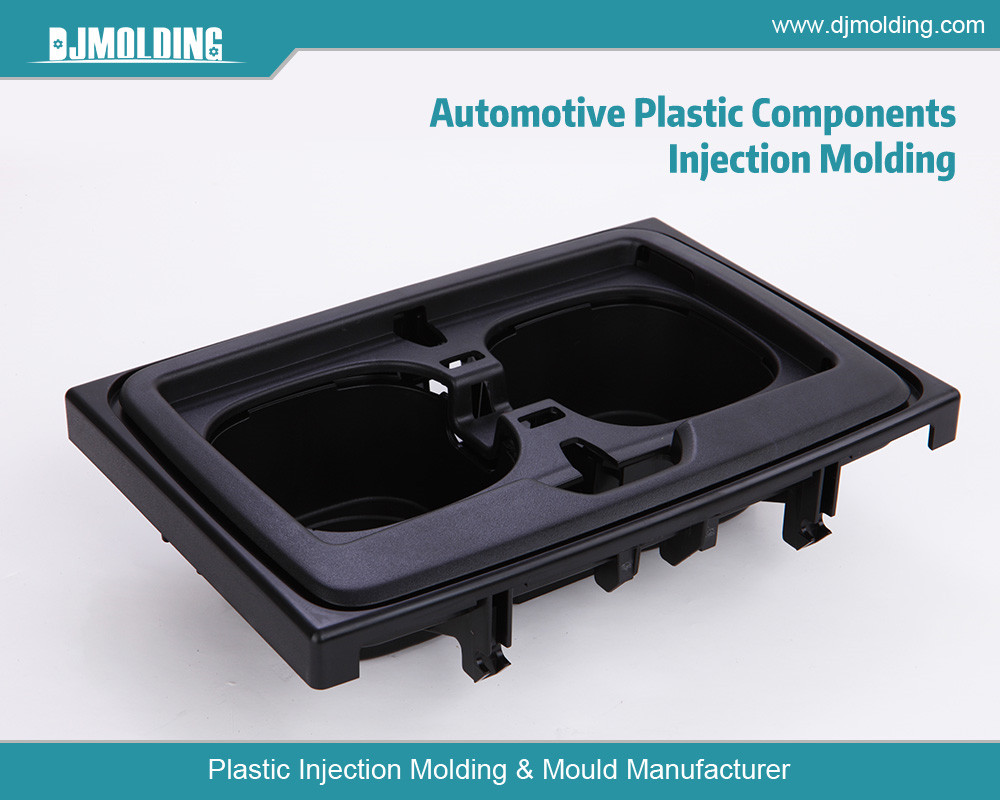
Conclusion
While both TPU and TPE offer excellent injection molding options, the choice of material ultimately depends on the specific requirements of the application. TPU’s durability, abrasion resistance, and flexibility make it ideal for demanding environments, while TPE’s ease of processing, tactile feel, and affordability make it well-suited for consumer goods.
In industries where high performance, durability, and chemical resistance are critical, TPU is often the preferred choice. Conversely, TPE is likely the better option for products that require flexibility, a soft touch, and aesthetic customization. Understanding these nuances can help manufacturers optimize product performance, longevity, and cost-effectiveness, ensuring that suitable material is used for each unique application.
For more about the tpu vs tpe injection molding: understanding the differences, applications, and benefits, you can pay a visit to Djmolding at https://www.djmolding.com/ for more info.