Top 10 Best Materials For Injection Molding: Ultimate Guide
Top 10 Best Materials For Injection Molding: Ultimate Guide
Injection molding is essential to making various parts and products, including industrial solid elements and complex components. The success of injection molding depends mainly on the material selection, which significantly impacts the end product’s performance, quality, and durability. This comprehensive guide will introduce you to the top 10 materials for injection molding, presenting their special qualities, uses, and advantages. It will help you make opinions that will meet your industrial needs.
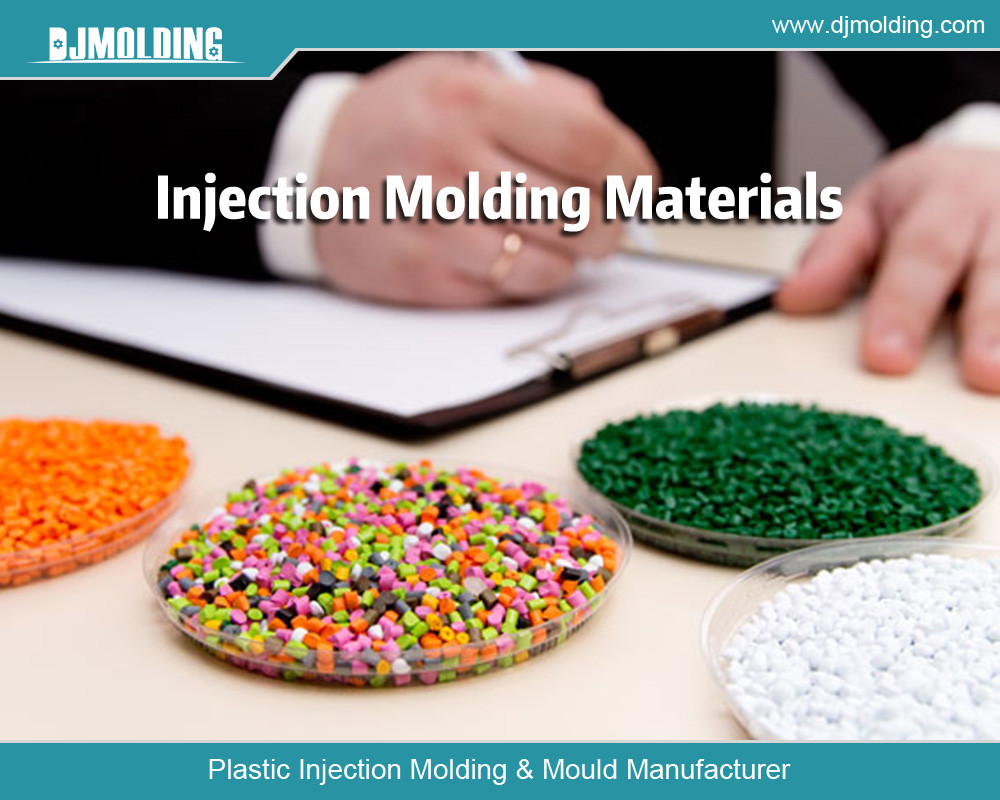
1. Acrylonitrile Butadiene Styrene (ABS)
Acrylonitrile Butadiene Styrene (ABS) is a flexible thermoplastic. It is frequently used in injection molding because of its strength and ease of processing. ABS is well-known for its superior strength, flexibility, and durability. It is perfect for manufacturing solid and long-lasting parts and components for various industries, including consumer goods, electronics, and the automotive sector. Because it can be perfectly molded into beautiful patterns, it is a material of choice for manufacturing applications that must be strong and stylish.
Properties
Acrylonitrile Butadiene Styrene (ABS) is a thermoplastic polymer known for its strength, rigidity, and impact resistance. It combines the advantages of multiple plastics, offering:
- Strength and heaviness: It is solid for use.
- Impact Resistance: It ignores the impact correctly without cracking.
- Machinability: Easily molded into complex designs.
- Finishability: Can be painted or finished to a high standard.
Applications
ABS is used in various industries due to its reliability:
- Automotive: Dashboards, bumpers, and interior components.
- Consumer Goods: Toys, kitchen appliances, and luggage.
- Electronics: Housings for devices like computers and televisions.
Benefits
ABS is a versatile and cost-effective choice due to:
- Balance of Toughness and Impact Resistance: Offers durability without sacrificing flexibility.
- Cost-Effective: Provides excellent performance at a reasonable price.
- Versatility: Suitable for a wide range of applications.
2. Polyethylene (PE)
Polyethylene (PE) is a popular thermoplastic used in injection molding for its outstanding affordability and adaptability. It is well known for its durability, chemical resistance, and ease of processing. It is the best component for producing many simple and complex products. It helps to make various-shaped mechanical parts, and it is excellent for packaging, automotive, and consumer goods.
Properties
Polyethylene (PE) is one of the most widely used plastics, recognized for its adaptability and ease of processing. It includes various grades:
- Low-Density Polyethylene (LDPE): Flexible with low tensile strength.
- High-Density Polyethylene (HDPE): High strength-to-density ratio.
- Linear Low-Density Polyethylene (LLDPE): Balances strength and flexibility.
- Ultra-High-Molecular-Weight Polyethylene (UHMWPE): Exceptional impact resistance.
Applications
PE’s diverse grades are used in:
- Packaging: Plastic bags, containers, and films.
- Pipes: For water and sewage systems.
- Consumer Goods: Toys, bottles, and household items.
Benefits
PE’s advantages include:
- Adaptability: Suitable for various applications based on grade.
- Ease of Processing: Low cost and simple to mold.
- Durability: Good resistance to impact and chemicals.
3. Polypropylene (PP)
Polypropylene (PP) is a widely used thermoplastic in injection molding, valued for its strength, flexibility, and resistance to chemical corrosion. Its lightweight and durable nature makes it ideal for producing diverse products, from automotive parts to household goods. PP’s excellent dimensional stability and low density allow for efficient and cost-effective manufacturing, making it a preferred choice for creating high-quality, functional components with precise details in various industries.
Properties
Polypropylene (PP) is known for its versatility, low density, and chemical resistance. Its properties include:
- Mechanical Strength: Strong and durable.
- Thermal Stability: Maintains properties under high temperatures.
- Chemical Resistance: Resists many chemicals and solvents.
Applications
PP is widely used in:
- Packaging: Food containers, bottles, and films.
- Automotive: Bumpers, dashboards, and interior parts.
- Medical Devices: Syringes, medical vials, and surgical instruments.
Benefits
Polypropylene offers:
- Versatility: Suitable for many industries.
- Recyclability: Environmentally friendly compared to other plastics.
- Cost-Effectiveness: Provides excellent performance at a low cost.
4. Polystyrene (PS)
Polystyrene (PS) is a versatile thermoplastic widely used in injection molding due to its excellent processing characteristics and cost-effectiveness. Renowned for its rigidity, clarity, and ease of fabrication, PS finds applications in diverse industries ranging from consumer goods to packaging. Its adaptability to various molding techniques and the ability to achieve intricate designs make it a popular choice for manufacturers seeking efficiency and precision in their production processes. Understanding PS’s properties and performance in injection molding is essential for optimizing product quality and production efficiency.
Properties
Polystyrene (PS) is valued for its transparency, rigidity, and ease of processing. Key properties include:
- Transparency: Clear for applications requiring visual clarity.
- Rigidity: Maintains shape and structural integrity.
- Chemical Resistance: Resists many chemicals.
Applications
PS is utilized in:
- Packaging: Food containers and disposable cutlery.
- Consumer Goods: Toys, CD cases, and household items.
- Medical Devices: Disposable syringes and petri dishes.
Benefits
The benefits of PS are:
- Cost-Effective: Affordable and accessible to process.
- Versatility: Suitable for a wide range of applications.
- Ease of Processing: Simple to mold and shape.
5. Polycarbonate (PC)
Polycarbonate (PC) is a high-performance thermoplastic favored in injection molding for its exceptional strength, impact resistance, and optical clarity. Its ability to withstand significant stress and temperature fluctuations makes the PC ideal for applications demanding durability and precision. Its versatility and ease of processing allow for creating complex, high-quality components used in industries such as automotive, electronics, and consumer products. Leveraging PC in injection molding enables manufacturers to produce robust and reliable parts while achieving superior performance and aesthetic appeal.
Properties
Polycarbonate (PC) is known for its toughness, clarity, and thermal stability. Its properties include:
- High Impact Resistance: Withstands significant force without breaking.
- Transparency: Excellent optical clarity.
- Thermal Stability: Maintains properties across a wide temperature range.
Applications
PC is used in:
- Automotive: Headlights and interior panels.
- Medical Devices: Surgical instruments and protective equipment.
- Electronics: Housings, connectors, and lenses.
Benefits
Polycarbonate offers:
- Durability: High impact and heat resistance.
- Clarity: Ideal for applications requiring transparency.
- Versatility: Suitable for various demanding applications.
6. Poly (Methyl Methacrylate) (PMMA)
Poly (Methyl Methacrylate) (PMMA), commonly known as acrylic, is a popular thermoplastic in injection molding due to its excellent clarity, rigidity, and weather resistance. Often used as a glass substitute, PMMA provides outstanding optical properties and durability, making it ideal for applications where transparency and impact resistance are crucial. Its ease of molding and ability to achieve fine details make PMMA a preferred choice for producing high-quality, aesthetically pleasing components in various industries, including automotive, electronics, and medical devices.
Properties
Poly (Methyl Methacrylate) (PMMA), known as acrylic, is valued for its clarity and impact resistance. Key properties include:
- Transparency: Provides clear and bright optical clarity.
- Weather Resistance: Resists UV radiation and weathering.
- Impact Resistance: Tougher than glass.
Applications
PMMA is used in:
- Signage: Outdoor and indoor signs.
- Automotive: Headlight lenses and interior components.
- Medical Devices: Optical lenses and casings.
Benefits
The benefits of PMMA are:
- Optical Clarity: Offers high-quality visual applications.
- Weather Resistance: Suitable for outdoor use.
- Impact Resistance: More durable than glass.
7. Polyvinyl Chloride (PVC)
Polyvinyl Chloride (PVC) is a widely used thermoplastic in injection molding and is known for its versatility, durability, and cost-effectiveness. With excellent chemical, moisture, and impact resistance, PVC is ideal for producing products from pipes and fittings to consumer goods. Its adaptability to various molding techniques allows for efficient and precise manufacturing, making it a popular choice across multiple industries.
Properties
Polyvinyl Chloride (PVC) is known for its durability and chemical resistance. Key properties include:
- Chemical Resistance: Resists many acids, bases, and salts.
- Durability: Long-lasting and robust.
- Flexibility: It can be rigid or flexible, depending on the formulation.
Applications
PVC is used in:
- Construction: Pipes, fittings, and flooring.
- Medical Devices: Blood bags and IV tubing.
- Consumer Goods: Credit cards and inflatable products.
Benefits
PVC offers:
- Durability: Long service life in various conditions.
- Cost-Effectiveness: Affordable and widely available.
- Versatility: Can be tailored for rigid or flexible uses.
8. Nylon (Polyamide, PA)
Nylon (Polyamide, PA) is a high-performance thermoplastic used in injection molding for its superior strength, durability, and wear resistance. Its excellent mechanical properties and dimensional stability make it ideal for producing robust, precision-engineered components across automotive, aerospace, and industrial applications.
Properties
Nylon, or Polyamide (PA), is renowned for its strength and wear resistance. Key properties include:
- Strength and Durability: High tensile strength and impact resistance.
- Wear Resistance: Low friction properties ideal for moving parts.
- Thermal Stability: Maintains properties at elevated temperatures.
Applications
Nylon is utilized in:
- Automotive: Engine covers and air intake manifolds.
- Industrial Machinery: Gears and bearings.
- Consumer Goods: Textiles, carpets, and sports equipment.
Benefits
The benefits of Nylon include:
- High Performance: Excellent for high-stress applications.
- Durability: Long-lasting and resistant to wear.
- Versatility: Suitable for various industries.
9. Polyoxymethylene (POM)
Polyoxymethylene (POM), known as acetal, is a high-performance thermoplastic valued in injection molding for its exceptional rigidity, low friction, and dimensional stability. Its superior mechanical properties and resistance to wear and chemicals make POM ideal for precision components in automotive, industrial, and consumer applications.
Properties
Polyoxymethylene (POM), known as acetal, is valued for its mechanical strength and low friction. Key properties include:
- Mechanical Strength: High strength and stiffness.
- Low Friction: Reduces wear and maintenance needs.
- Dimensional Stability: Maintains accuracy under different conditions.
Applications
POM is used in:
- Engineering Parts: Precision components in machinery.
- Automotive: Durable parts for vehicles.
- Electronics: Electrical connectors and components.
Benefits
The benefits of POM are:
- High Performance: Reliable for demanding applications.
- Durability: Long-lasting with minimal wear.
- Precision: Maintains dimensional accuracy.
10. Bulk Molding Compound (BMC)
Bulk molding compound (BMC) is a high-performance material used in injection molding and is known for its excellent mechanical properties, electrical insulation, and resistance to heat and chemicals. BMC’s ease of processing and ability to produce complex, high-strength components make it ideal for demanding automotive, electrical, and industrial applications.
Properties
Bulk Molding Compound (BMC) is a thermosetting resin known for its exceptional properties. Key characteristics include:
- Electrical Insulation: Superior insulating properties.
- Heat and Flame Resistance: Resists high temperatures and flames.
- Mechanical Strength: Robust and durable.
Applications
BMC is used in:
- Electrical Products: Insulation coatings for tools and components.
- Automotive: Components for enhanced performance.
- Food Utensils: Durable and safe for food-grade applications.
Benefits
The benefits of BMC are:
- High Performance: Excellent for electrical and mechanical applications.
- Durability: Long-lasting and resistant to extreme conditions.
- Versatility: Suitable for a range of industries.
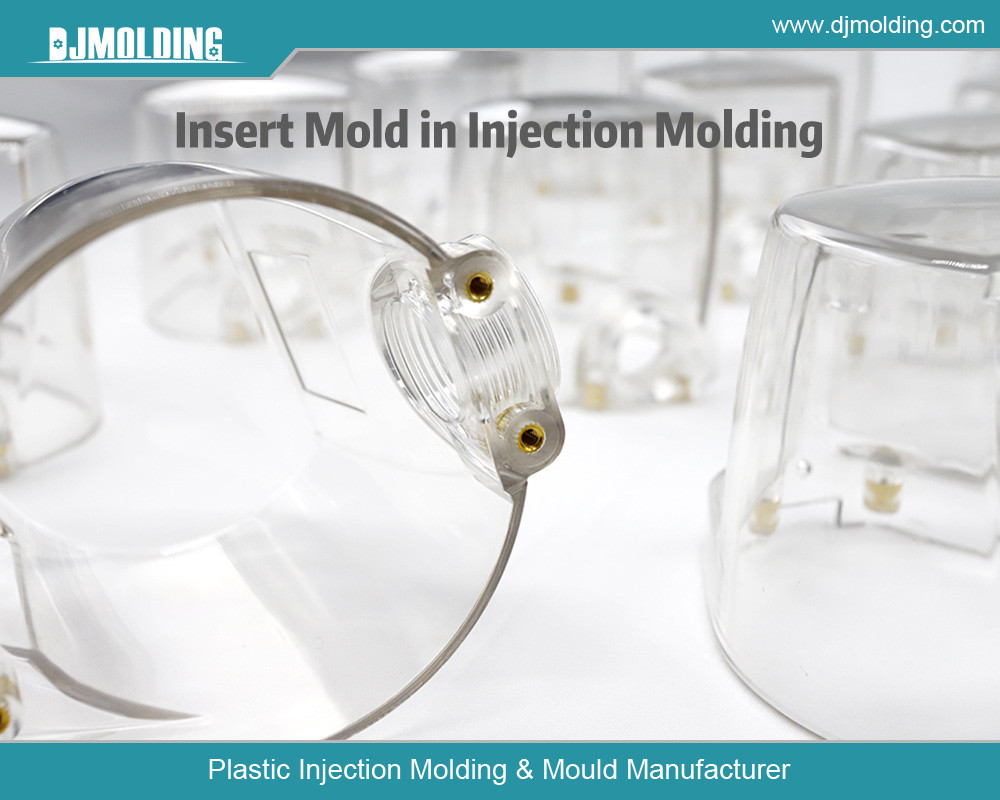
Conclusion
Choosing a suitable material for injection molding is crucial to ensure that the final product meets the desired performance and durability standards. Each material discussed in this guide—ABS, PE, PP, PS, PC, PMMA, PVC, Nylon, POM, and BMC—offers unique properties and benefits suited to different applications. By understanding these materials’ strengths and applications, manufacturers can make informed decisions, optimize production processes, and achieve high-quality results across various industries.
For more about the top 10 best materials for injection molding: ultimate guide, you can pay a visit to Djmolding at https://www.djmolding.com/how-to-choose-the-best-plastic-materials-for-plastic-injection-molding/ for more info.