Thermoplastic Injection Molding
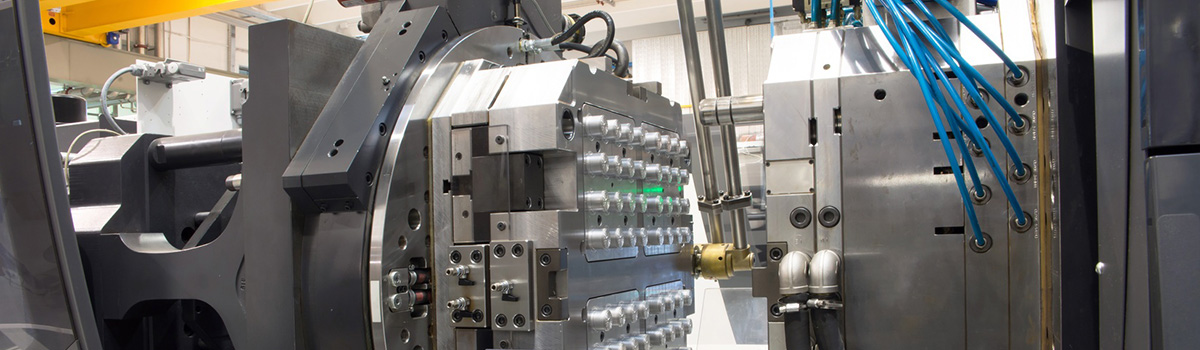
Thermoplastic injection molding is a popular manufacturing process used to create various plastic parts for multiple industries. This process involves melting plastic pellets and injecting them into a mold to produce a three-dimensional shape. Thermoplastic injection molding is highly efficient and cost-effective for producing large volumes of high-quality plastic parts with tight tolerances. This comprehensive guide will explore the various aspects of thermoplastic injection molding, including its advantages and disadvantages, the types of thermoplastics used, the injection molding process, design considerations, and much more.
History of Thermoplastic Injection Molding
The history of thermoplastic injection molding spans over a century of technological advancements, material developments, and industrial applications. From its humble beginnings as a celluloid molding process to the present-day sophisticated technology, injection molding continues to be a vital manufacturing technique, driving innovation and shaping various industries.
- Early Developments:John Wesley Hyatt and his brother Isaiah developed the first practical injection molding machine, tracing the origins of thermoplastic injection molding back to the late 19th century. In 1872, they patented a device that used a plunger to inject celluloid into a mold cavity, creating solid objects. This breakthrough laid the foundation for the modern injection molding process.
- Advancements in Materials:In the early 20th century, introducing new synthetic polymers opened up new possibilities for injection molding. Bakelite, a phenolic resin, became a popular material for molding due to its excellent electrical insulating properties. Throughout the 1930s and 1940s, advancements in polymer chemistry led to the development of other thermoplastics, such as polystyrene and polyethylene, which further expanded the range of materials suitable for injection molding.
- Industrial Adoption: The widespread adoption of thermoplastic injection molding began in the 1950s as manufacturers recognized its cost-effectiveness and versatility. Introducing high-pressure machines allowed for faster cycle times and increased production volumes. As a result, a diverse selection of products for both personal and industrial use came into existence. These included car components, home appliances, and playthings.
- Technological Innovations:Over the decades, injection molding technology continued to evolve. In the 1960s, computer-controlled machines emerged, enabling precise control over the molding process. The introduction of hot runner systems in the 1980s reduced waste and improved efficiency by eliminating the need for runners and sprues. In recent years, automation, robotics, and 3D printing advancements have further revolutionized the injection molding industry, enabling complex designs and reducing production time.
- Sustainability and Recycling:With growing environmental concerns, the injection molding industry has embraced sustainability measures. Manufacturers have developed bio-based and recycled thermoplastics, reducing the reliance on fossil fuel-based materials. Additionally, improved recycling technologies have enabled reprocessing of post-consumer and post-industrial waste, minimizing the environmental impact of thermoplastic injection molding.
- Future Prospects:The future of thermoplastic injection molding looks promising. The industry is exploring innovations such as micro-injection molding for miniature components, multi-material and overmolding techniques for complex parts, and integrating intelligent technologies for process monitoring and optimization. Furthermore, researchers expect advancements in biodegradable materials and additive manufacturing to revolutionize the field, making injection molding even more sustainable and versatile.
Advantages of Thermoplastic Injection Molding
Thermoplastic injection molding offers numerous advantages for manufacturers. It provides design flexibility, allowing for complex and intricate designs with various features. The process is cost-efficient, reducing material waste and lowering unit costs. Thermoplastic injection molding supports multiple materials, providing versatility for different applications.
- Design Flexibility:Thermoplastic injection molding allows for intricate and complex designs with features like undercuts, thin walls, and varying thicknesses, providing designers with immense freedom.
- Cost Efficiency: The process is highly efficient, reducing material waste and lowering unit costs. Simultaneous molding of multiple parts and fast production cycles contribute to cost savings.
- Material Versatility: Thermoplastic injection molding supports a wide range of materials, enabling manufacturers to choose the most suitable option for each application, including rigid or flexible, transparent or opaque, and chemically resistant materials.
- Strength and Durability:Injection-molded thermoplastics can exhibit excellent mechanical properties, such as high strength, toughness, and impact resistance. Reinforcement options, like glass or carbon fibers, further enhance these properties.
- Consistency and Quality:Injection molding ensures consistent part-to-part quality and dimensional accuracy, delivering tight tolerances and reliable products. The process also provides a smooth and uniform surface finish, eliminating the need for additional finishing operations.
- Scalability and Mass Production:Injection molding is scalable from low to high volumes, making it suitable for mass production. Once manufacturers create the mold, they can produce large quantities of identical parts with minimal variations.
- Integration and Assembly:Injection-molded parts can incorporate multiple components into one piece, reducing the need for additional assembly processes. This integration enhances product performance, reduces assembly time, and lowers costs.
- Sustainability:The injection molding industry is showing an increasing focus on sustainability. The availability of bio-based and recycled materials allows for producing environmentally friendly products. The efficient material usage and recyclability of thermoplastics contribute to a greener manufacturing process.
These benefits have made it a widely adopted manufacturing method across various industries, providing high-quality, cost-effective, and environmentally friendly solutions for complex product requirements.
Disadvantages of Thermoplastic Injection Molding
While thermoplastic injection molding offers numerous advantages, there are also several disadvantages. Manufacturers need to carefully assess these factors and weigh them against the benefits to determine the suitability of thermoplastic injection molding for their specific applications.
- High Initial Investment: Setting up a thermoplastic injection molding operation requires a significant initial investment in mold design and fabrication and purchasing specialized machinery. The costs associated with creating molds and tooling can be substantial, especially for complex and intricate designs.
- Design Limitations: While thermoplastic injection molding offers design flexibility, certain limitations exist. For example, achieving uniform wall thickness throughout the part can be challenging, leading to variations in material distribution and potential structural weaknesses. Additionally, the presence of undercuts or complex geometries may require the use of additional mold features or secondary operations, increasing costs and production time.
- Long Lead Times:The process of designing and fabricating molds for injection molding can be time-consuming, leading to longer lead times for product development. The design iteration process, mold production, and testing can add significant time to the overall production timeline, which may not be suitable for projects with tight deadlines.
- Material Selection Constraints:Although thermoplastic injection molding supports a wide range of materials, there are certain limitations and constraints. Some materials may have specific processing requirements or limited availability, impacting design choices and material selection for a particular application.
- Part Size Limitations:Injection molding machines have size limitations, both in terms of the physical size of the device and the size of the molds they can accommodate. Producing huge parts may require specialized equipment or alternative manufacturing methods.
- Environmental Impact:While the industry is working towards sustainability, the thermoplastic injection molding process still generates waste material, including scrap and sprues. Proper disposal and recycling of these materials are necessary to minimize the environmental impact.
- The complexity of Process Optimization:Achieving optimal process parameters for thermoplastic injection molding can be complex and time-consuming. Manufacturers must carefully control and optimize temperature, pressure, cooling rates, and cycle times to ensure consistent part quality and minimize defects.
Types of Thermoplastics Used in Injection Molding
These are just a few examples of the thermoplastics commonly used in injection molding. Each material has unique properties, making it suitable for specific applications based on strength, flexibility, chemical resistance, transparency, and cost. Manufacturers should consider these properties and requirements when selecting the appropriate thermoplastic for their injection molding projects.
- Polypropylene (PP):Polypropylene is a versatile thermoplastic commonly used in injection molding. It offers excellent chemical resistance, low density, and good impact strength. PP (polypropylene) has wide-ranging applications in packaging, automotive components, household appliances, and medical devices.
- Polyethylene (PE):Polyethylene is another widely used thermoplastic in injection molding. It is available in various forms, such as high-density polyethylene (HDPE) and low-density polyethylene (LDPE). PE offers good chemical resistance, toughness, and flexibility, making it suitable for bottles, containers, and pipes.
- Polystyrene (PS):Polystyrene is a versatile thermoplastic known for its clarity, rigidity, and affordability. It finds common usage in packaging, consumer goods, and disposable products. PS (polystyrene) allows for quick processing and provides good dimensional stability, but it can be brittle and susceptible to environmental stress cracking.
- Acrylonitrile Butadiene Styrene (ABS): ABS is a popular thermoplastic known for its excellent impact resistance and durability. It combines the properties of acrylonitrile, butadiene, and styrene to create a versatile material suitable for automotive parts, electronic housings, and toys.
- Polyvinyl Chloride (PVC): PVC is a widely used thermoplastic known for its excellent chemical resistance, durability, and low cost. It can be rigid or flexible depending on the formulation and additives used. PVC (polyvinyl chloride) finds common usage in construction, electrical insulation, healthcare products, and packaging.
- Polycarbonate (PC): Polycarbonate is a transparent thermoplastic with extraordinary impact and high heat resistance. It finds common usage in applications that require optical clarity, such as automotive components, safety helmets, and electronic displays.
- Nylon (Polyamide):Nylon is a strong and durable thermoplastic known for its excellent mechanical properties and chemical resistance. It finds common usage in applications that demand high strength, such as automotive parts, industrial components, and consumer goods.
- Polyethylene Terephthalate (PET):PET is a popular thermoplastic for producing bottles, containers, and packaging materials. It offers good clarity, chemical resistance, and barrier properties, making it suitable for food and beverage applications.
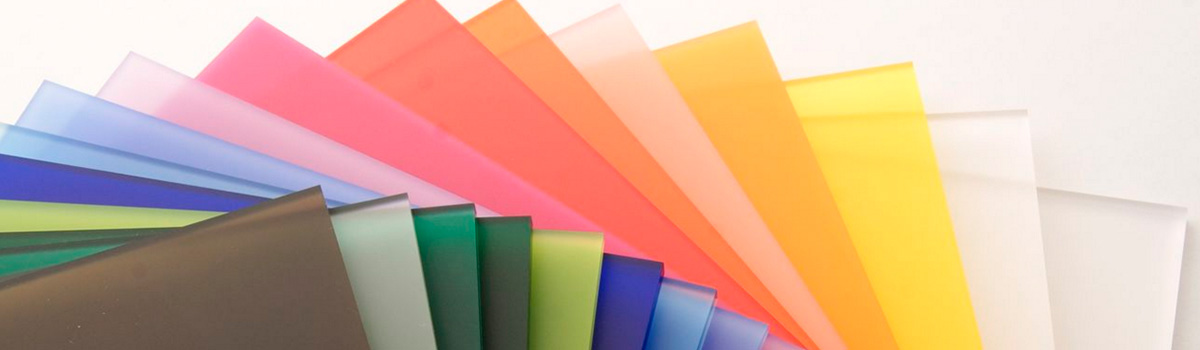
Properties of Thermoplastics Used in Injection Molding
These properties of thermoplastics play a crucial role in determining their suitability for specific injection molding applications. Manufacturers must carefully consider these properties and select the appropriate thermoplastic based on the desired performance, environmental conditions, and cost requirements.
- Mechanical Properties:Thermoplastics used in injection molding can exhibit various mechanical properties, including tensile strength, impact resistance, and flexural strength. These properties determine the material’s ability to withstand applied forces and its overall durability in various applications.
- Chemical Resistance:Many thermoplastics utilized in injection molding possess remarkable resistance to chemicals, solvents, and oils. This property is crucial for applications that involve exposure to harsh environments or corrosive substances.
- Thermal Stability:The thermal stability of thermoplastics refers to their ability to withstand elevated temperatures without significant degradation. Some thermoplastics exhibit excellent heat resistance, allowing them to maintain their mechanical properties even at high temperatures.
- Electrical Properties:Thermoplastics used in injection molding can have specific electrical properties, including electrical insulation, conductivity, or dielectric strength. These properties are essential for applications in electrical and electronic industries, where materials must provide reliable electrical performance.
- Transparency and Clarity:Certain thermoplastics, such as polycarbonate and PET, offer excellent transparency and clarity, making them suitable for applications that require optical properties. Manufacturers commonly use these materials in products such as transparent windows, lenses, and displays.
- Flexibility and Toughness: Flexibility and toughness are essential properties of thermoplastics used in applications that require impact resistance and durability. Some thermoplastics, such as ABS and nylon, offer excellent toughness, allowing them to withstand repeated impacts without breaking.
- Dimensional Stability:Dimensional stability refers to a thermoplastic’s ability to maintain its shape and size under varying conditions, including temperature changes. Materials with good dimensional stability ensure consistent part dimensions, minimizing the risk of warping or distortion.
- Chemical Compatibility:The chemical compatibility of thermoplastics refers to their ability to resist degradation or interaction with various chemicals, including acids, bases, and solvents. To ensure optimal performance, selecting a thermoplastic that can withstand the specific chemical environment it will encounter in the intended application is essential.
- Density: Thermoplastics have varying thicknesses, which can impact their weight and overall part properties. Low-density materials, such as polyethylene, offer lightweight solutions, while high-density materials, such as polypropylene, provide added strength and rigidity.
Injection Molding Process: Step-by-Step
The injection molding process follows these steps, allowing for the efficient and precise production of high-quality thermoplastic parts. Each step requires careful control and monitoring to ensure consistent part dimensions, material properties, and overall quality.
- Mold Design and Fabrication: The first step in the injection molding process is the design and fabrication of the mold. Manufacturers must create a precise and detailed mold design to achieve the desired part specifications. Manufacturers then fabricate the mold using various techniques, such as CNC or electrical discharge machining (EDM).
- Material Preparation: The next step is preparation once the mold is ready. Thermoplastic pellets or granules are selected based on the desired material properties and melted in a hopper. Operators then feed the material into the barrel of the injection molding machine, where it undergoes melting and homogenization.
- Injection:During the injection phase, operators inject the molten thermoplastic into the mold cavity under high pressure. The machine’s injection unit pushes the melted material through a nozzle and into the mold. The material fills the mold cavity, taking the shape of the desired part.
- Cooling and Solidification:After filling the mold, operators allow the molten plastic to cool and solidify. Cooling is crucial for achieving dimensional stability and proper part formation. Operators can control the cooling process by circulating coolant through channels within the mold or by using cooling plates.
- Mold Opening and Ejection:Operators open the mold and eject the part from the mold cavity once the plastic solidifies. The ejection system within the machine uses pins, ejector plates, or air blasts to remove the region from the mold. The mold is then ready for the next injection cycle.
- Post-Processing: After ejection, the part may undergo post-processing operations, such as trimming, deburring, or surface finishing. These steps help remove excess material, smooth rough edges, and improve the part’s final appearance.
- Quality Inspection: The final step involves inspecting the injected parts for quality and ensuring they meet the specified requirements. Various quality control techniques, including dimensional measurement, visual inspection, and functional testing, can be employed to verify the part’s quality and integrity.
- Recycling and Material Reuse:Any excess or scrap material generated during the injection molding can be recycled and reused. Reducing the use of new thermoplastic material helps minimize waste and improve sustainability.
Equipment Used in Injection Molding
These equipment components facilitate the injection molding process, from melting and injecting the thermoplastic material to shaping, cooling, and ejecting the final part. Proper operation and maintenance of these equipment components are crucial for achieving efficient, high-quality injection molding production.
- Injection Molding Machine:The primary equipment in injection molding is responsible for melting the thermoplastic material, injecting it into the mold, and controlling the process.
- Mold: The mold, custom-designed to create the desired shape and features of the plastic part, comprises two halves, the cavity and the core. Operators mount it onto the clamping unit of the injection molding machine.
- Hopper:Container that holds the thermoplastic material in pellet or granular form and feeds it into the injection molding machine’s barrel for melting and injection.
- Barrel and Screw: The barrel, a cylindrical chamber, melts and homogenizes the thermoplastic material as the screw rotates within it to melt, mix, and standardize the material.
- Heating and Cooling Systems:Injection molding machines have heating elements, such as electric heaters or heaters using hot oil, to raise the temperature of the barrel, and cooling systems, such as water or oil circulation, to cool the mold and solidify the plastic part.
- Ejector System:Removes the molded part from the mold cavity after solidification, typically utilizing ejector pins, plates, or air blasts during the mold opening.
- Control System:Monitors and controls various parameters of the injection molding process, allowing operators to set and adjust parameters such as injection speed, temperature, pressure, and cooling time.
Injection Molding Machines: Types and Characteristics
Each type of injection molding machine has its characteristics and advantages, allowing manufacturers to choose the most suitable device for their specific production requirements.
- Hydraulic Injection Molding Machines: These machines use hydraulic systems to generate the necessary pressure to inject molten plastic into the mold. They are known for their high clamping force, precise control, and versatility in handling various thermoplastics. Hydraulic machines are suitable for large-scale production and can accommodate complex molds.
- Electric Injection Molding Machines:Electric machines utilize electric servo motors for the machine’s operation, including the injection, clamping, and ejector systems. They offer precise control, energy efficiency, and faster response times than hydraulic machines. Electric machines are ideal for precision molding applications that require high repeatability and accuracy.
- Hybrid Injection Molding Machines:Hybrid machines combine the benefits of both hydraulic and electric devices. They utilize a combination of hydraulic and electric servo systems to achieve high precision, energy efficiency, and cost-effectiveness. Hybrid machines are suitable for a wide range of applications, providing a balance between performance and operational costs.
- Two-Platen Injection Molding Machines: Two-platen machines have a unique design with two separate plates for clamping the mold. This design provides enhanced stability, improved mold synchronization and allows for larger mold sizes and higher clamping forces. Two-platen machines are suitable for large and complex parts that require precise molding.
- Multi-Component Injection Molding Machines:Manufacturers design these machines to produce parts with multiple materials or colors in a single molding cycle. They have various injection units and molds, enabling simultaneous injection of different materials. Multi-component machines offer flexibility and efficiency in manufacturing complex parts with varying characteristics.
- Micro-Injection Molding Machines:Specifically designed for producing small and precise parts, micro-injection molding machines offer incredibly high precision and accuracy. They can produce intricate details with tight tolerances and minimal material waste. Electronics, medical devices, and micro-optics commonly use micro-injection molding machines.
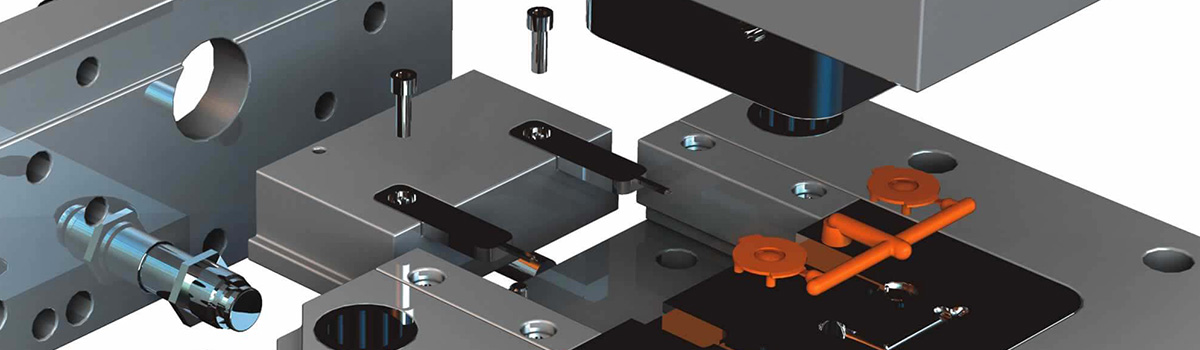
Mold Design Considerations for Injection Molding
Careful mold design considerations are essential for successful injection molding production.
- Part Design:The mold design should accommodate the specific requirements of the part, including its shape, dimensions, and functional features. Manufacturers should properly consider draft angles, wall thickness, undercuts, and any necessary elements to ensure ease of ejection and part quality.
- Mold Material: The mold material selection is crucial for achieving durability, dimensional stability, and heat resistance. Common mold materials include steel alloys, aluminum alloys, and tool steels. The choice of material depends on factors such as production volume, part complexity, and expected tool life.
- Cooling System:Efficient cooling is essential for proper part solidification and minimizing cycle time. The mold design should incorporate cooling channels or strategically positioned inserts to ensure uniform mold cooling. Proper cooling reduces the risk of warpage, shrinkage, and part defects.
- Venting:Adequate venting is necessary to allow the escape of air and gases during the injection process. Insufficient venting can lead to gas traps, burn marks, or incomplete part filling. Manufacturers can achieve venting by incorporating venting grooves, pins, or other mechanisms into the mold design.
- Ejection System:The mold design should include an effective ejection system to safely and efficiently remove the molded part from the mold cavity. The ejection system can consist of ejector pins, sleeves, or other mechanisms, strategically positioned to avoid interference with the function or critical features.
- Gate Design:The gate is where molten plastic enters the mold cavity. The gate design should ensure proper part filling, minimize flow lines, and prevent premature material freezing. Standard gate designs include edge gates, tunnel gates, and hot runner systems, depending on the part requirements and material properties.
- Parting Line:The mold design should define a suitable parting line, which is the line where the two halves of the mold come together. Proper parting line placement ensures minimal flash and parting line mismatch and facilitates efficient mold assembly.
- Mold Maintenance and Serviceability: Manufacturers should consider the ease of maintenance, repair, and mold servicing. Mold components should be easily accessible for cleaning, inspection, and replacement. Incorporating features like quick-change inserts or modular mold designs can improve mold serviceability.
Mold Materials Used in Injection Molding
Collaborating with mold material specialists and considering the specific needs of the molding application can help determine the most suitable material for achieving optimal mold performance and part quality.
- Steel Alloys: Steel alloys, such as tool steels (e.g., P20, H13) and stainless steels, are commonly used for injection molding molds due to their excellent durability, heat resistance, and wear resistance. These materials can withstand the high temperatures and pressures in the injection molding process and offer good dimensional stability for producing high-quality parts.
- Aluminum Alloys:Aluminum alloys, such as 7075 and 6061, are lightweight and offer good thermal conductivity, making them suitable for molds that require efficient cooling. Manufacturers often use aluminum molds for prototyping, low-volume production, or applications where weight reduction is critical. However, aluminum molds may have lower durability compared to steel alloys.
- Copper Alloys:Copper alloys, such as beryllium copper, exhibit high thermal conductivity and good machinability. They find usage in molds that require excellent heat transfer for effective cooling. Copper alloys can help reduce cycle times by quickly dissipating heat from the molded part, resulting in faster solidification.
- Tool Steels:Tool steels, including H13, S7, and D2, are designed for high-performance tooling applications. These steels offer a combination of high strength, hardness, and wear resistance. Tool steels suit molds with high production volumes, abrasive materials, or demanding molding conditions.
- Nickel Alloys:Nickel alloys, such as Inconel and Hastelloy, are known for their exceptional corrosion resistance, high-temperature strength, and thermal stability. Manufacturers use these alloys in molds that handle corrosive materials or require resistance to extreme temperatures and aggressive molding environments.
- Composite Materials:Composite materials, such as reinforced plastics or composites with metal inserts, are occasionally used for specific molding applications. These materials offer a balance of properties, such as high strength, thermal stability, and reduced weight. Composite molds can be cost-effective alternatives for specific production requirements.
Types of Injection Molds
Injection molding is a versatile and widely used manufacturing process for plastic parts.
- Two-Plate Mold:The two-plate mold is the most common type of injection mold. It consists of two plates, the cavity plate, and the core plate, which separate to allow the ejection of the molded part. The cavity plate contains the cavity side of the mold, while the core plate houses the core side. Manufacturers use two-plate molds for producing a wide range of parts due to their relatively simple design.
- Three-Plate Mold:The three-plate mold is an advanced version of the two-plate mold. It includes an additional plate, the runner, or the sprue plate. The runner plate creates a separate channel for the sprue, runners, and gates, allowing easier removal of the molded part. Manufacturers commonly use three-plate molds for details with complex gating systems or when avoiding a gate vestige on the piece is desirable.
- Hot Runner Mold:The runner and gate system is heated in hot runner molds, eliminating the need for solidification and re-melting of the material during each cycle. The hot runner system consists of heated manifolds and nozzles that maintain the molten state of the plastic. Hot runner molds offer advantages such as reduced cycle time, lower material waste, and improved part quality by minimizing gate vestiges.
- Cold Runner Mold: Cold runner molds have a traditional runner and gate system where the molten plastic flows through cold runners that solidify with each cycle. Operators subsequently remove the solidified runners, resulting in material waste. Manufacturers typically use complex runner molds for lower volume production or when material costs are less critical due to their more straightforward design.
- Insert Mold:Insert molds incorporate metal or plastic inserts into the mold cavity during the injection molding. Inserts can be pre-placed into the mold or inserted by automated processes. This mold allows for integrating additional components or reinforcing elements into the molded part, enhancing its functionality or strength.
- Overmold: Overmolding involves molding one material over another, typically bonding a rigid plastic substrate with a softer elastomer or thermoplastic. This process allows for creation of parts with multiple materials or textures in a single mold, providing improved grip, cushioning, or aesthetic features.
Factors Affecting Injection Molding Costs
Considering these factors can help manufacturers estimate and optimize the cost of injection molding, ensuring a balance between quality, efficiency, and cost-effectiveness for their specific production requirements.
- Part Complexity:The complexity of the part design plays a significant role in determining the cost of injection molding. Intricate geometries, undercuts, thin walls, or complex features may require additional tooling, specialized molds, or longer cycles, increasing the overall manufacturing cost.
- Material Selection:The choice of thermoplastic material affects the injection molding cost. Different materials have varying prices per kilogram, and factors such as material availability, properties, and processing requirements can influence the overall material cost.
- Tooling and Mold Design: The initial tooling and mold design costs are significant in injection molding costs. Factors such as mold complexity, number of cavities, mold size, and mold material contribute to the tooling and mold manufacturing expenses. More complex molds or molds requiring advanced features can increase the upfront investment.
- Production Volume: The production volume directly impacts the cost per part in injection molding. Higher books often result in economies of scale, reducing the cost per part. Conversely, low-volume production runs may incur higher charges due to setup, tooling, and material waste.
- Cycle Time: The cycle time, which includes the cooling and ejection phases, affects the production capacity and overall cost. Longer cycle times result in reduced production output and potentially higher prices. Optimizing the mold design, cooling system, and process parameters can minimize cycle times and improve efficiency.
- Quality Requirements:Stringent quality requirements or specific certifications can impact the injection molding cost. Meeting exact tolerances, surface finish requirements, or additional testing may require other resources, processes, or inspections, adding to the overall cost.
- Secondary Operations:If the molded parts require post-processing operations such as assembly, painting, or additional finishing steps, these operations can add to the overall injection molding cost.
- Supplier and Location:The choice of injection molding supplier and their location can affect costs. Labor costs, overheads, logistics, and transportation expenses vary based on the supplier’s location, impacting the overall manufacturing cost.
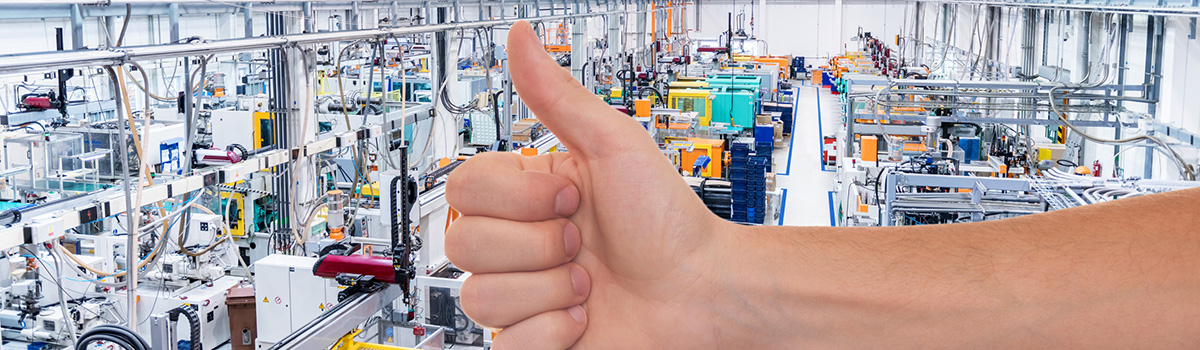
Quality Control in Injection Molding
Implementing robust quality control measures throughout the injection molding process helps identify and address potential defects, deviations, or inconsistencies, ensuring the production of high-quality parts that meet customer specifications and requirements.
- Process Monitoring: Continuous monitoring of key process parameters, such as melt temperature, injection pressure, cooling time, and cycle time, ensures consistency and repeatability in part production. Real-time monitoring and automated systems can detect variations or deviations from set parameters, allowing for timely adjustments and maintaining process stability.
- Inspection and Measurement:Regular review and measurement of molded parts are essential to verify dimensional accuracy, part quality, and adherence to specifications. Our services cover a range of quality control methods, such as measuring dimensions, analyzing surface quality, conducting visual inspections, and performing functional tests. Various inspection techniques, such as coordinate measuring machines (CMM) and optical and visual inspection systems, are employed for accurate evaluation.
- Statistical Process Control (SPC): SPC involves collecting and analyzing process data to monitor and control injection molding quality. Statistical methods, such as control charts and process capability analysis, help identify trends, detect process variations, and ensure the process remains within defined control limits. SPC enables the proactive identification of issues and facilitates process optimization.
- Material Testing: Testing the raw materials, such as thermoplastics, additives, and colorants, ensures their quality and suitability for injection molding. Material testing may include melt flow index (MFI) analysis, mechanical properties, thermal characteristics, and material composition. Verifying the material quality helps prevent defects and inconsistencies in the molded parts.
- Tooling Maintenance and Inspection:Proper maintenance and regular inspection of the injection molds are crucial for ensuring quality in injection molding. Regular cleaning, lubrication, and assessment of mold components help prevent wear, damage, or degradation that could affect part quality. Timely repair or replacement of worn-out or damaged mold components is essential to maintain consistent molding performance.
- Documentation and Traceability:Maintaining comprehensive documentation and traceability records is essential for quality control in injection molding. It is vital to record process parameters, inspection results, material information, and any changes or adjustments made during production. Proper documentation enables traceability of parts, facilitates root cause analysis, and ensures consistency in quality.
- Training and Skill Development: Providing adequate training and skill development programs for operators, technicians, and quality control personnel enhances their understanding of injection molding processes, quality requirements, and inspection techniques. Well-trained personnel can detect defects, troubleshoot issues, and implement corrective measures effectively, ensuring high-quality production.
Common Injection Molding Defects and How to Avoid Them
Regular inspection, monitoring, and analysis of injection molding processes and proper maintenance and adjustment of equipment and molds can help identify and address these common defects.
- Sink Marks:Sink marks are depressions or indentations on the surface of the molded part caused by uneven cooling or shrinkage. One should consider proper gate location and design, optimal cooling system design, and uniform wall thickness distribution to avoid sink marks. Increasing the injection pressure or adjusting the cooling time can also help minimize sink marks.
- Warpage:Warpage refers to the deformation or bending of a molded part after ejection due to uneven cooling or residual stresses. Maintaining uniform wall thickness, using proper cooling channels, and ensuring balanced filling and packing of the mold are crucial to prevent warpage. Optimizing mold temperature, using appropriate draft angles, and controlling material temperature and injection speed can help minimize warpage.
- Flash:Flash occurs when excess material flows into the mold parting line, resulting in thin, unwanted projections or extra material on the final part. One can effectively prevent flash by ensuring proper mold design, including applying adequate clamping force, precise alignment, and using appropriate venting techniques. Optimizing process parameters such as injection pressure, temperature, and cycle time reduces flash.
- Short Shot:A quick shot happens when the injected material does not fill the mold cavity, resulting in an incomplete part. Proper material selection, ensuring adequate melt temperature and viscosity, and maintaining appropriate injection pressure and time are essential to avoid short photos. Additionally, verifying the mold design for sufficient runner and gate size and proper venting can help prevent quick shots.
- Weld Lines:Weld lines occur when two or more molten material flow fronts meet and solidify, resulting in a visible line or mark on the part surface. Good gate and runner design, optimal melt temperature, injection speed, and adjusting material flow and part geometry can minimize weld lines. Mold flow analysis and gate placement optimization can also help prevent or mitigate weld lines.
- Burn Marks:Burn marks are discolorations or black spots on the surface of the molded part caused by excessive heat or overheating of the material. Avoiding extreme melt temperature, using appropriate cooling channels, and optimizing cycle time can help prevent burn marks. Adequate venting, proper gate design, and controlling mold temperature also contribute to minimizing burn marks.
Post-Molding Operations: Finishing and Assembly
After the injection molding, many molded parts may require additional finishing and assembly operations to achieve the desired final product. These post-molding operations may include:
- Trimming:Remove any excess material or flash around the molded part using trimming or cutting tools.
- Surface Treatment:Enhancing the appearance or functionality of the part surface using various techniques such as painting, coating, or texturing.
- Assembly:Joining multiple molded parts or adding components such as fasteners, inserts, or labels to complete the final product.
- Testing:Verification of part quality and functionality through various testing methods such as dimensional analysis, material properties testing, or performance testing.
- Packaging and Shipping:Proper packaging and labeling of the finished product for shipment to customers or end-users.
The selection of post-molding operations depends on the specific application and desired final product characteristics. Close collaboration between injection molding experts, finishing and assembly specialists, and the customer is crucial to achieving the desired absolute product quality and functionality. Proper planning and integrating post-molding operations into the manufacturing process can help ensure efficient production and timely delivery of high-quality products.
Injection Molding vs. Other Plastic Manufacturing Processes
Each plastic manufacturing process has advantages and limitations, making them suitable for different applications.
- Injection Molding: Injection molding is a highly versatile and widely used manufacturing process for producing plastic parts. It offers advantages such as high production efficiency, precise part replication, and the ability to create complex geometries. Injection molding is suitable for high-volume production runs and allows for using a wide range of thermoplastic materials. It offers excellent dimensional accuracy and surface finish, making it ideal for various industries such as automotive, consumer goods, and medical devices.
- Blow Molding: Blow molding is a process used primarily for producing hollow plastic parts, such as bottles, containers, and automotive components. It involves melting plastic and inflating it into a mold cavity, creating the desired shape. Blow molding is suitable for high-volume production and can produce large, lightweight parts with uniform wall thickness. However, it is limited in terms of part complexity and material selection compared to injection molding.
- Thermoforming:Thermoforming is a process used to produce plastic parts by heating a thermoplastic sheet and shaping it using molds or vacuum forming. It finds common usage in packaging, disposable products, and large-scale products such as trays and covers. Thermoforming offers cost-effective production for large parts and allows for quick prototyping. However, it has limitations regarding part complexity, material selection, and dimensional accuracy compared to injection molding.
- Extrusion:Extrusion is a continuous process to produce plastic profiles, sheets, tubes, and films. It involves melting plastic resin and forcing it through a die to create the desired shape. Extrusion is suitable for producing long, continuous lengths of plastic products with a consistent cross-section. While extrusion offers high production rates and cost-effectiveness, it is limited in terms of complex part geometries and precise dimensional control compared to injection molding.
- Compression Molding:Compression molding involves placing a pre-measured amount of thermosetting material in a heated mold cavity and compressing it under high pressure until it cures. It finds common usage in producing parts with high strength and dimensional stability, such as automotive components and electrical insulation. Compression molding offers good part consistency, high production efficiency, and the ability to use a wide range of materials. However, it is limited in terms of part complexity and cycle time compared to injection molding.
Applications of Thermoplastic Injection Molding
Various industries widely use thermoplastic injection molding due to its versatility, efficiency, and cost-effectiveness. Some of the applications of thermoplastic injection molding include:
- Automotive Industry: The automotive industry widely uses thermoplastic injection molding to manufacture various components, including interior and exterior trim, dashboards, door panels, bumpers, and electrical connectors. The process allows for precise part replication, complex geometries, and lightweight materials, improving fuel efficiency and design flexibility.
- Consumer Goods:Injection molding finds extensive applications in producing consumer goods such as household appliances, electronic devices, packaging containers, and toys. The process enables the mass production of durable, high-quality products with consistent dimensions and surface finish. It also allows for customization options and quick product iterations.
- Medical Devices:Injection molding plays a crucial role in the medical industry for producing a wide range of devices, including syringes, surgical instruments, implantable components, and drug delivery systems. The process ensures the production of sterile, precise, and biocompatible parts that meet the stringent regulatory requirements of the healthcare sector.
- Electronics and Electrical Industry:The electronics industry utilizes injection molding to manufacture electrical connectors, enclosures, switches, and other components. The process offers high dimensional accuracy, excellent surface finish, and the ability to incorporate features such as insert molding and overmolding, allowing for efficient production of complex electronic assemblies.
- Packaging Industry:Various industries, including food and beverage, pharmaceuticals, and personal care, commonly use injection molding for producing plastic packaging containers, caps, closures, and bottles. The process enables the creation of lightweight, durable, and aesthetically appealing packaging solutions with efficient manufacturing cycles.
- Aerospace Industry:The aerospace sector employs injection molding for manufacturing lightweight and high-performance components such as air ducts, brackets, interior panels, and structural parts. The process allows for using advanced materials and intricate part geometries, contributing to weight reduction and improved fuel efficiency.
Environmental Impact of Thermoplastic Injection Molding
Thermoplastic injection molding is a popular manufacturing process due to its many benefits, but it is also essential to consider its environmental impact. Here are some points to consider:
- Material Efficiency:Thermoplastic injection molding promotes material efficiency by minimizing waste. The process utilizes precise control over the amount of material injected into the mold, reducing the need for excess material. Manufacturers can also employ regrinding and recycling techniques to reuse scrap or rejected parts, further reducing material waste.
- Energy Consumption:Manufacturers design injection molding machines to be energy-efficient, with modern models incorporating advanced technologies such as servo motors and variable speed drives. These features optimize energy usage by reducing power consumption during molding, resulting in lower energy requirements and reduced environmental impact.
- Waste Management:While minimizing material waste, manufacturers should implement proper waste management practices to handle leftover materials, sprues, or runners. Manufacturers can establish recycling programs to collect and reuse plastic waste generated during injection molding, thereby reducing waste sent to landfills.
- Emission Reduction: Thermoplastic injection molding generally generates lower emissions than other manufacturing processes. Manufacturers can reduce emissions by using eco-friendly materials, implementing energy-efficient equipment, and employing advanced exhaust and filtration systems to capture any emissions released.
- Sustainable Material Choices:The selection of thermoplastic materials can significantly impact the environmental sustainability of injection molding. Opting for biodegradable or bio-based plastics, as well as recycled or recyclable materials, can help reduce the overall ecological footprint of the process.
Life Cycle Considerations: Considering the entire life cycle of the molded product is essential for assessing its environmental impact. During the design and material selection stages, manufacturers should consider factors such as the durability of the part, its recyclability, and the potential for end-of-life disposal or reuse.
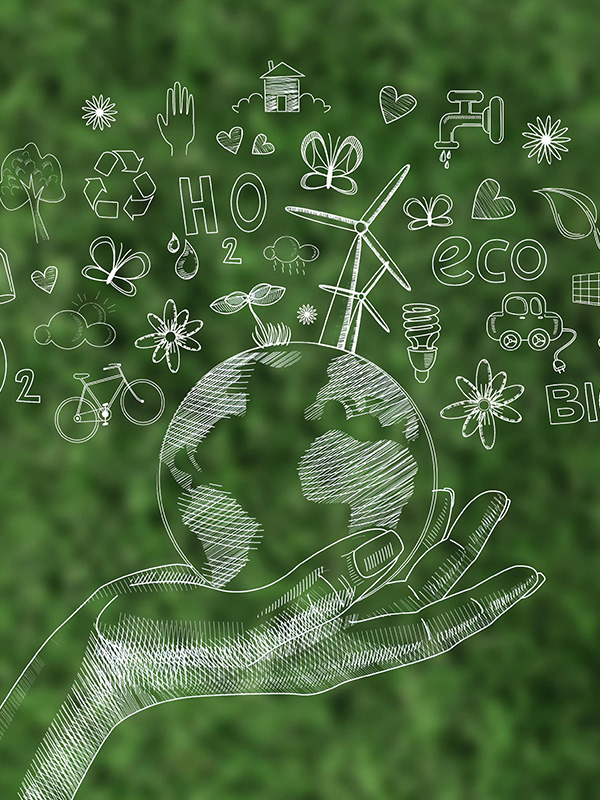
Future of Thermoplastic Injection Molding
The future of thermoplastic injection molding looks promising, with continued advancements in technology and increased demand for high-quality, precision parts across various industries. Some of the key developments expected in the coming years include:
- Increased use of automation and robotics to improve efficiency and reduce costs.
- Efforts are focused on developing new materials and processes to improve part performance and enable new applications.
- It is a growing adoption of sustainable practices, such as using recycled materials and optimizing energy consumption, to reduce the environmental impact of injection molding.
- Greater integration of digital technologies, such as 3D printing and simulation software, to improve design and production processes.
The global injection molding market is expanding, particularly in emerging economies, driven by the increasing demand for plastic products in various industries.
Choosing the Right Injection Molding Partner
Choosing the right injection molding partner is crucial for the success of your project. Take the time to evaluate multiple options, conduct site visits, and engage in thorough discussions to ensure a compatible and long-lasting partnership.
- Expertise and Experience:Look for an injection molding partner with extensive knowledge and experience in the industry. They should have a proven track record of delivering high-quality products and solutions to clients in various sectors. Consider their understanding of different materials, mold designs, and manufacturing processes.
- Manufacturing Capabilities: Assess the manufacturing capabilities of the injection molding partner. Ensure they have a well-equipped facility with modern machinery and technologies to handle your project requirements. Consider their production capacity, ability to handle different part sizes and complexities, and ability to meet your desired production volumes and timelines.
- Quality Assurance:Quality is paramount in injection molding. Evaluate the quality control systems and certifications of the potential partner. Look for partners that follow strict quality standards, have robust inspection processes, and perform comprehensive testing to ensure part quality and consistency.
- Design and Engineering Support:A reliable injection molding partner should offer design and engineering support to optimize your part design for manufacturability. They should have skilled engineers who can provide valuable input on material selection, mold design, and process optimization to enhance part quality and efficiency.
- Cost Competitiveness:While cost should not be the sole determining factor, it is essential to evaluate the pricing and cost competitiveness of the injection molding partner. Request detailed quotes and consider tooling costs, material costs, labor costs, and any additional services they provide.
- Communication and Collaboration:Effective communication and collaboration are essential for a successful partnership. Ensure that the injection molding partner has good communication channels, is responsive to your inquiries, and can provide regular project updates. A collaborative approach will help ensure we meet your requirements and promptly address any challenges.
- Customer References and Reviews:Seek customer references or read reviews/testimonials to gain insights into the experiences of other clients with the injection molding partner. Obtaining this information can help determine their dependability, promptness, and overall level of customer contentment.
Conclusion
Thermoplastic injection molding is a versatile and cost-effective method for manufacturing plastic parts in large quantities. Its ability to produce complex shapes with high precision and consistency has become a popular choice for various industries, including automotive, medical, electronics, and consumer goods. By understanding the different aspects of thermoplastic injection molding, including its advantages, disadvantages, and design considerations, you can make informed decisions about choosing the right injection molding partner for your business needs.