The Ultimate Solution For All Your Low Volume Plastic Parts Manufacturing
The Ultimate Solution For All Your Low Volume Plastic Parts Manufacturing
Low-Volume Plastic Molding: What Is It?
Low-volume molding by injection is the process of producing plastic parts in tiny batches, usually fewer than 1000 pieces. Low-volume molding of plastic is often carried out using smaller calibrated equipment that can be utilized for prototyping, much like low-volume manufacturing techniques for metal or wood. Prototypes and functioning components, such as those found in automotive or medical equipment, are the usual forms of low-volume production.
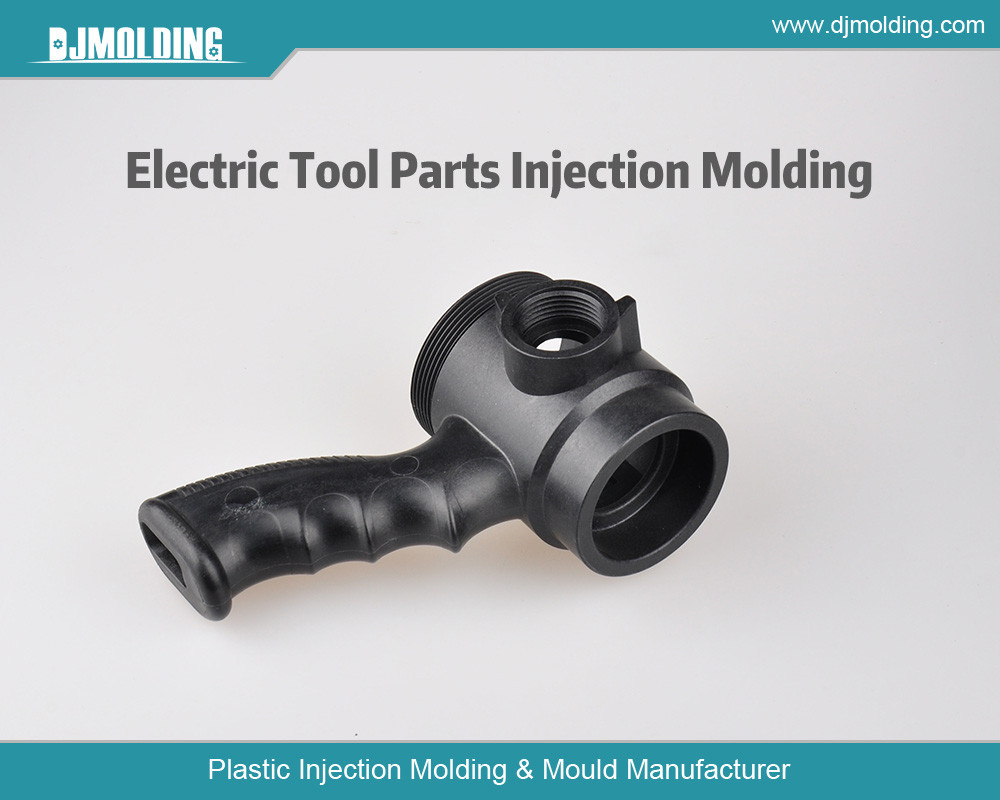
Efficiency Gains in Product Development with Low-Volume Molding by Injection
With over forty years of injection molding experience under our belt, we have established an incredibly efficient operation made possible by highly qualified personnel and cutting-edge machinery. Owing to our extensive experience and adaptability, which are fueled by a variety of equipment, we can meet a broad range of prototyping and production needs. With our Heavy Mix Low Volume (HMLV) solution, we can also meet your individual needs for custom injection molding of plastics. This includes a broad mix of instruments, even for low-volume molding.
We are aware that, depending on the situation, our clients’ manufacturing needs could fluctuate from high to low. We are dedicated to meeting all of your needs in-house, from concept to manufacturing tooling and manufacturing, regardless of the industry you are in or the quantity or mix requirements. You can take advantage of low-volume injection molding’s versatility in the following ways:
High Variety: You can choose from a wide range of products in tiny amounts thanks to our big mix and low volume.
Time Efficiencies: Production throughput is accelerated by low-volume production, which can result in substantial time savings.
Design Flexibility: Low-volume injection molding makes it quicker to construct injection molding prototypes, enabling you to make design modifications more quickly and affordably.
Prototype Injection Molding: What Is It?
One kind of low-volume manufacturing process used to swiftly make small quantities of components for product testing and assessment is prototype injection molding. An early model, sample, or distribution of a finished product is called a prototype. During the product development process, our engineering team can evaluate and confirm the structure’s layout, functionality, and manufacturing feasibility using prototype injection mold tooling. Because it warms and cools more quickly than steel molds, the injection-molded aluminum tooling made using CNC machining is perfect for small-volume injection molding. This makes quick prototyping more effective by cutting the typical delay for small-quantity molding via injection.
Why is injection molding done in low volumes?
Many applications call for the use of low-volume injection molding, including:
1.To manufacture parts in small quantities for product evaluation and testing.
2.To expedite the manufacturing process.
3, to build a final product prototype.
4.Low-volume injection molding makes it quicker to construct injection molding prototypes, enabling you to make design adjustments more quickly and affordably.
What Are Injection Molding’s Four Steps?
The four steps of low-volume injection molding are as follows:
Securing
Introducing
Thermance
Removal
To produce high-quality parts, the low-volume molding method has several crucial steps. In automotive and low-volume injection-molded products, having a trustworthy and knowledgeable partner that can guide you through every stage is essential.
What Is the Low-Capacity Injection Molding Process?
The plastic is initially inserted into a mold while being clamped. Subsequently, the plastic melts and fills every crevice inside the mold. The item is released from the mold once the material has cooled and set. Lastly, the part’s surplus material, or flash, is cut away.
Why is injection casting the ideal option for plastic parts made in low volumes?
Due to its many benefits, molding by injection is the most often used production method for low-volume plastic parts.
It can create pieces of excellent quality and is incredibly exact.
It is affordable in small amounts.
The components are strong and resistant to high pressures and temperatures.
It is simple to reduce flash from the components.
Insert molding: what is it?
Insert molding is the name given to a particular turnkey injection molding technique that makes use of a pre-placed insert. This insert, which is often made of steel or another substance, is necessary for injection molding. It is inserted into the mold before the plastic is injected. The method of insert molding enables the smooth integration of the plastic components and insert.
Then, as the plastic melts and hardens into the shape of the mold, it successfully encloses the insert. By doing this, the plastic and insert become one cohesive unit, and, as a result, a solid bond is formed between them.
Several insert kinds, including screws, pins, clips, and even more intricate parts, may be incorporated during the process. The integrated insert gives the final molded pieces increased strength, conductivity, or functionality.
Describe Overmolding.
A manufacturing process known as “overmolding” or “two-shot molding” involves injecting several different materials into one mold. A substrate—which may be machined or pre-molded—is placed into a mold during the overmolding process.
A distinct substance is subsequently introduced into the mold to create an encapsulating connection with the substrate. The main goal of overmolding was to create a single part that is made of several different materials, each with unique characteristics.
Overmolding makes it possible to create complex parts out of multiple components in one manufacturing cycle, which simplifies assembly and improves product reliability. Nevertheless, since a successful link between the two materials is essential, it is critical to properly evaluate the compatibility of the materials during the overmolding process.
Advantages of Low-Volume, High-Mix Manufacturing
High-mix, low-quantity manufacturing is the method that makes it possible to produce a wide range of goods in small amounts, as the name says. You can benefit from our high-mix, small-volume plastic part molding services if you require intricate items with specific requirements. With our HMLV services, our clients benefit from a higher level of product variety and personalization. Above all, they can lower their inventory while still being able to react to shifting customer demands more quickly.
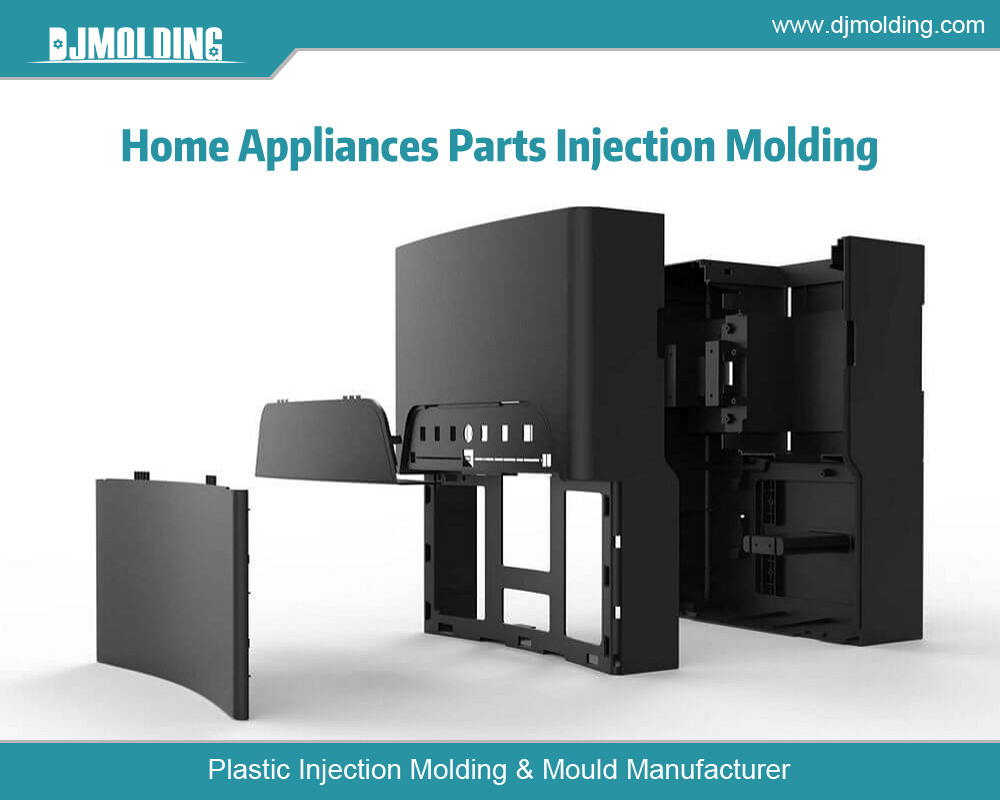
Which low-volume polymer is best for me?
Whether you are producing or prototyping will determine what kind of low-quantity plastic you need to utilize. Acrylic plastics are reasonably priced, multipurpose, and incredibly simple to deal with. Yet, they are more expensive and prone to scratches than glass. The service temperature is also too low for certain industrial uses. Although it costs more than acrylic, ABS is a type of engineering-grade polymer that is stronger and more rigid. Additionally, because of its greater service temperature ratings of up to 100°C (212°F), it is appropriate for industrial applications where frequent contact with high temperatures is necessary for regular operation. Due to its strength and inherent transparency, polycarbonate is a good choice for applications requiring exceptional dimensional stability and optical clarity. It has strong impact strength and may retain its physical characteristics at high temperatures.
For more about the ultimate solution for all your low volume plastic parts manufacturing,you can pay a visit to Djmolding at https://www.djmolding.com/the-advantages-of-low-volume-production-molds-for-plastic-parts-manufacturing-companies-in-usa/ for more info.