The Ultimate Guide Of Acrylic Injection Molding
The Ultimate Guide Of Acrylic Injection Molding
Acrylic injection molding is a transformative process in manufacturing, offering precision and versatility for creating high-quality plastic products. This technique is especially valued for its ability to produce precise, durable, and aesthetically pleasing components. Whether you’re a seasoned professional or new to the field, understanding the intricacies of acrylic injection molding can significantly enhance your production capabilities. In this comprehensive guide, we’ll explore the fundamentals of acrylic injection molding, its advantages, challenges, and best practices to help you optimize your manufacturing processes.
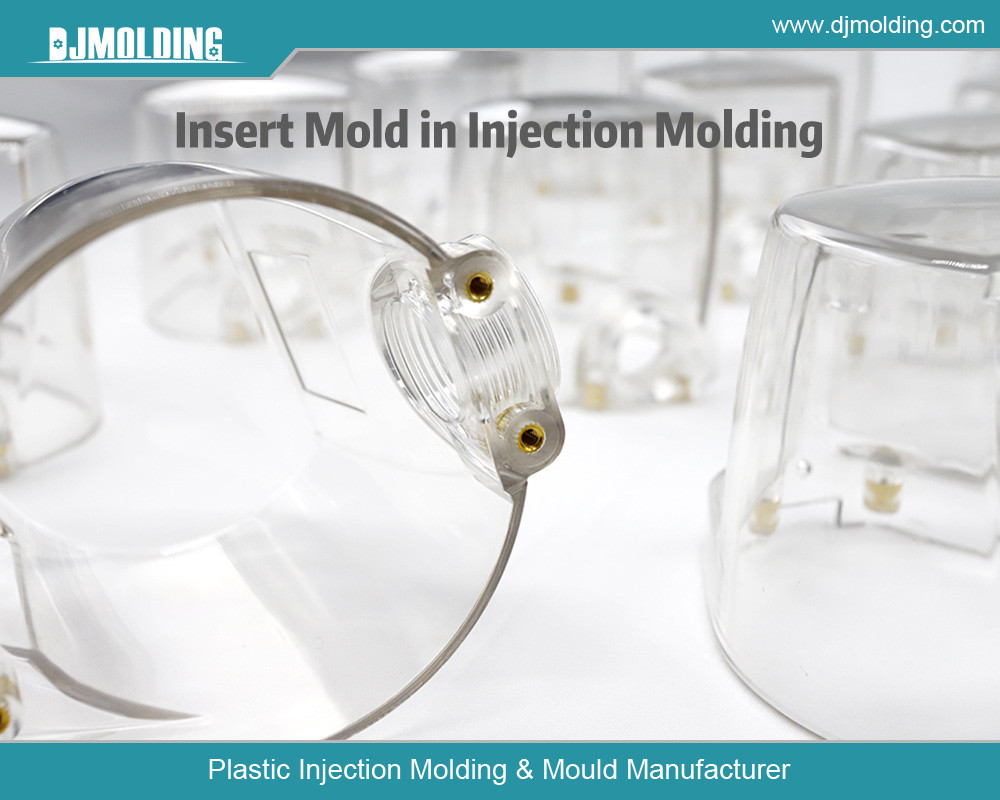
What is Acrylic Injection Molding?
Acrylic injection molding involves injecting molten acrylic material into a mold cavity to produce various components. Acrylic, known for its clarity and resistance to impact, is a popular choice for products requiring transparency and durability. The process begins with heating acrylic pellets until they melt, then injecting the molten material into a precisely designed mold. Once cooled and solidified, the molded part is ejected from the mold and ready for further processing or assembly.
Advantages of Acrylic Injection Molding
Acrylic injection molding is a favored manufacturing technique for many applications due to its numerous advantages.
Clarity and Transparency: One of the acrylic’s standout benefits is its exceptional optical clarity. It is the material of choice for applications requiring high transparency, such as lenses, light covers, and display cases. Acrylic’s ability to maintain clarity over time ensures that these components perform effectively and look pristine.
- Durability: Acrylic is known for its robustness. It is highly resistant to impact and weathering, which means products made from acrylic are more durable and can withstand harsh environmental conditions. This property is precious in outdoor signage, automotive parts, and protective covers.
- Versatility: The acrylic injection molding process is incredibly versatile. It can produce complex shapes with high precision, accommodating a broad spectrum of design requirements. Whether the need is for intricate decorative items or functional components, acrylic molding can achieve detailed and accurate results.
- Cost-Effectiveness: Although the initial costs for developing molds can be substantial, acrylic injection molding is cost-effective in the long run. The process’s efficiency allows for high-speed production, which reduces per-unit costs when manufacturing in large quantities. This cost efficiency is a significant advantage for businesses balancing quality and affordability.
- Fast Production Times: One of the most compelling reasons to choose acrylic injection molding is its speed. The process facilitates rapid production, making it ideal for high-volume manufacturing. This capability ensures that businesses meet large-scale demands while maintaining quality and increasing lead times.
The Acrylic Injection Molding Process
Understanding the steps involved in acrylic injection molding is crucial for ensuring successful outcomes:
Material Preparation:
- Acrylic pellets are fed into a hopper.
- The pellets are then heated in a barrel until they reach a molten state.
Injection:
- The molten acrylic is injected into a mold cavity under high pressure.
- The mold is designed to the exact specifications of the desired part.
Cooling:
- The molten acrylic cools and solidifies within the mold.
- Cooling time varies depending on the part’s size and complexity.
Ejection:
- Once cooled, the mold opens, and the finished part is ejected.
- The part may require additional post-processing, such as trimming or polishing.
Inspection and Quality Control:
- Each part is inspected for defects or deviations from specifications.
- Quality control ensures that all parts meet the required standards.
Challenges in Acrylic Injection Molding
While acrylic injection molding offers numerous benefits, it also comes with its share of challenges that can impact the manufacturing process:
- Mold Design: Designing molds with high precision and intricate details is complex and costly. Ensuring that molds meet exact specifications requires advanced engineering and meticulous planning.
- Material Sensitivity: Acrylic’s sensitivity to variations in temperature and pressure can influence the final product’s quality. Managing these factors is essential to avoid defects and ensure consistent results.
- Warpage and Distortion: Incorrect cooling rates or suboptimal mold design can cause warping or distortion in the finished parts. Proper cooling techniques and mold adjustments are crucial to maintain the integrity of the product.
- High Initial Costs: The upfront investment for developing molds and acquiring the necessary machinery can be substantial. This is particularly true for custom or large-scale projects, where financial commitment can be a barrier to entry.
Best Practices for Successful Acrylic Injection Molding
To achieve the best results in acrylic injection molding, consider the following best practices:
- Optimize Mold Design: Ensure the mold design accommodates proper flow and cooling. Use advanced simulation tools to predict and mitigate potential issues.
- Control Temperature and Pressure: Maintain consistent temperature and pressure settings to avoid defects and ensure uniform part quality.
- Regular Maintenance: Perform routine maintenance on injection molding machines and molds to prevent issues and extend equipment lifespan.
- Quality Control: Implement thorough quality control procedures to detect and address defects early in production.
- Material Selection: Choose the correct grade of acrylic for your specific application, considering factors like impact resistance, clarity, and color.
Applications of Acrylic Injection Molding
Acrylic injection molding has become a versatile and indispensable manufacturing process across numerous industries. This method involves injecting molten acrylic into molds to create precise and durable parts, making it ideal for a variety of applications:
- Optics: Acrylic injection molding is crucial for producing high-quality lenses, optical filters, and light covers due to its clarity and optical properties.
- Signage: It is commonly used for crafting display panels, illuminated signs, and advertising materials. Its ability to be easily molded into complex shapes and excellent light transmission are advantageous.
- Consumer Goods: This process helps create household items, toys, and decorative objects, leveraging acrylic’s durability and aesthetic appeal.
- Automotive: In the automotive sector, acrylic injection molding is employed to manufacture interior components, lighting elements, and trim pieces, contributing to functionality and design.
- Medical: This process benefits the medical field by producing clear enclosures, diagnostic equipment components, and protective covers, where the material’s clarity and strength are critical.
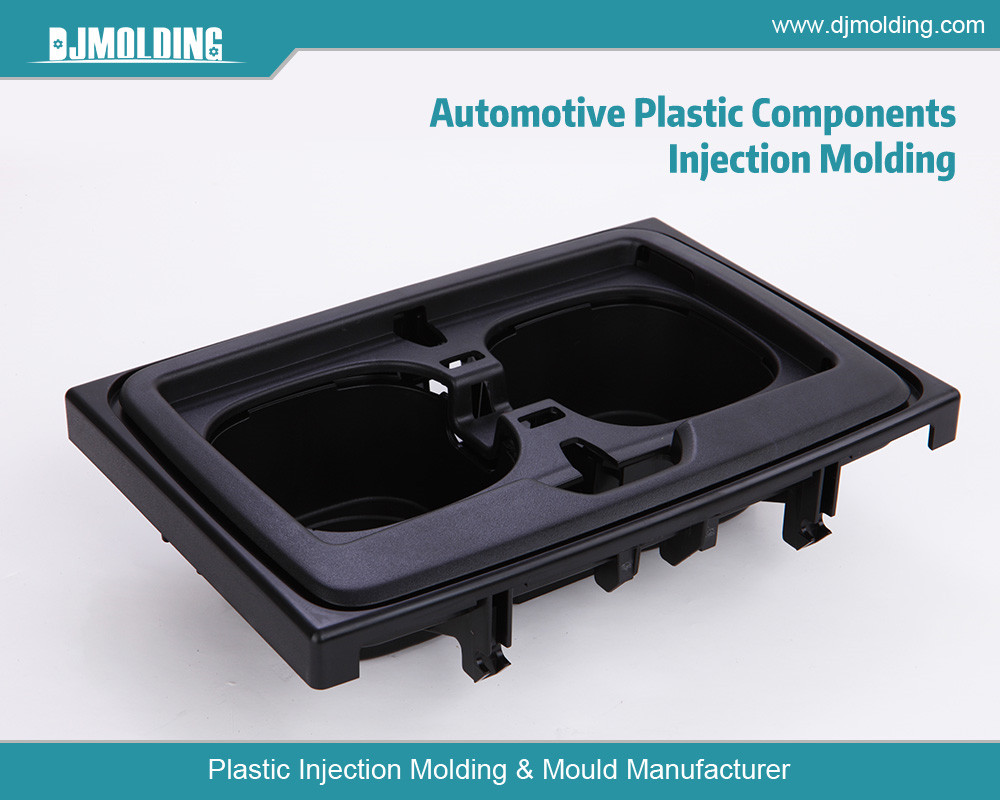
Conclusion
Acrylic injection molding is a versatile and effective method for producing high-quality plastic components. By understanding the fundamentals of the process, recognizing its advantages and challenges, and adhering to best practices, manufacturers can optimize their production and achieve exceptional results. Whether working on a new product design or refining existing processes, mastering acrylic injection molding will enhance your ability to deliver straightforward, durable, and aesthetically pleasing products to the market. Embrace the potential of acrylic injection molding to elevate your manufacturing capabilities and meet the diverse needs of your industry.
For more about the ultimate guide of acrylic injection molding, you can pay a visit to Djmolding at https://www.djmolding.com/5-common-plastic-resins-used-in-injection-molding/ for more info.