The Future Of Liquid Silicone Rubber Injection Molding In the Aerospace Industry
The Future of Liquid Silicone Rubber Injection Molding in the Aerospace Industry
The aerospace industry is constantly evolving, with new technologies and innovations shaping the future of flight. One such technology is liquid silicone rubber injection molding, which has become increasingly popular in recent years. LSR molding offers numerous benefits, such as high precision and durability, making it an ideal choice for aerospace applications. In this article, we’ll discuss the future of LSR injection molding in the aerospace industry and how it’s helping to shape the future of aviation.
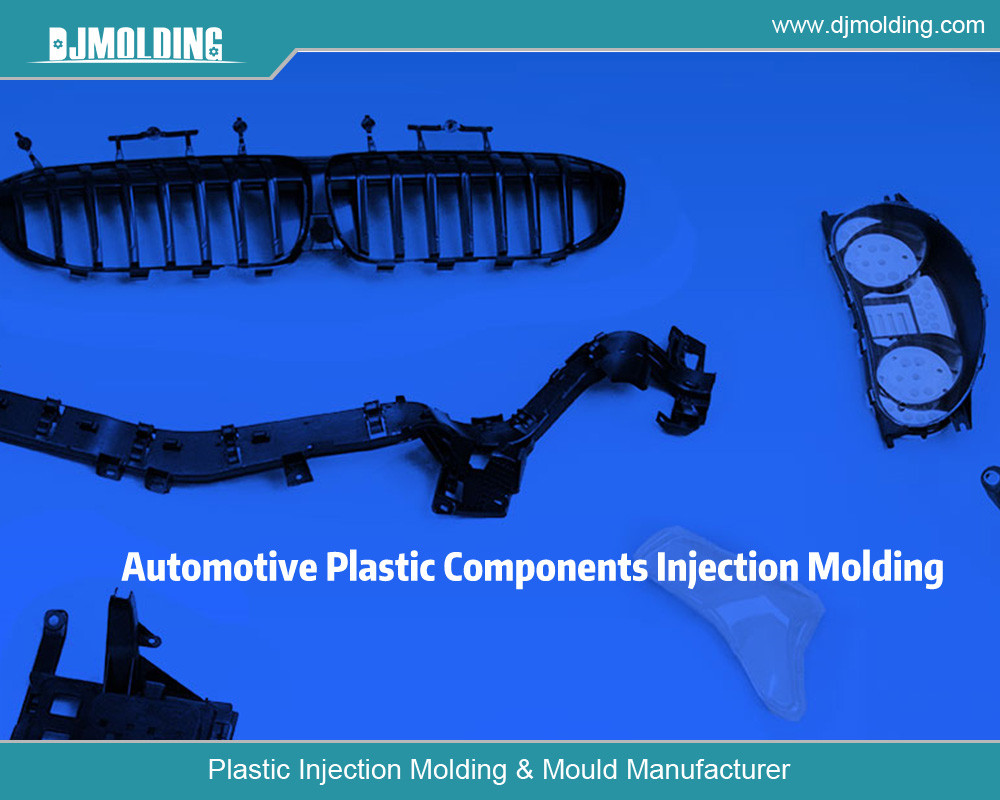
Advantages of LSR Injection Molding in Aerospace Industry
LSR molding offers several advantages over traditional molding methods, making it an ideal choice for aerospace applications. One of the most significant advantages is its high precision and accuracy. LSR injection molding can produce parts with tight tolerances and complex geometries, ensuring that the finished product meets the exact specifications required for aerospace applications.
Another advantage of LSR molding is its resistance to extreme temperatures and chemicals. LSR can withstand temperatures ranging from -50°C to 200°C, making it suitable for use in harsh environments. It is also resistant to chemicals such as jet fuel, hydraulic fluid, and lubricants, which are commonly used in the aerospace industry.
LSR molding also offers low compression set and high tear strength, making it ideal for use in seals and gaskets. Additionally, LSR is biocompatible and can be sterilized, making it suitable for use in medical applications.
Current Applications of LSR Injection Molding in Aerospace Industry
LSR molding is currently used in a variety of aerospace applications, including seals and gaskets, electrical connectors and insulators, O-rings and vibration dampeners, and aerospace lighting and optics. Seals and gaskets made from LSR are used in engines, fuel systems, and hydraulic systems to prevent leaks and ensure proper functioning. Electrical connectors and insulators made from LSR are used in avionics and communication systems to ensure reliable performance.
O-rings and vibration dampeners made from LSR are used in landing gear and other critical systems to absorb shock and reduce noise. Aerospace lighting and optics made from LSR are used in cockpit displays, navigation systems, and exterior lighting.
Challenges Faced by LSR Injection Molding in Aerospace Industry
Despite its many advantages, LSR molding also faces several challenges in the aerospace industry. One of the biggest challenges is the high tooling and equipment costs associated with the process. LSR injection molding requires specialized equipment and tooling, which can be expensive to purchase and maintain.
Another challenge is the limited material availability and processing options. LSR is a relatively new material, and there are only a few suppliers that offer it. Additionally, the processing options for LSR are limited compared to other materials, which can make it difficult to achieve certain part geometries and design requirements.
LSR molding also faces challenges related to the complex part geometries and design requirements of aerospace applications. Aerospace parts often have intricate shapes and features that require precise molding techniques and tooling. This can make it difficult to achieve the desired part quality and consistency.
Finally, LSR molding must comply with stringent regulatory and safety standards in the aerospace industry. This requires careful material selection, process validation, and risk assessment to ensure that the finished product meets all necessary requirements.
Innovations in LSR Injection Molding Technology for Aerospace Industry
Despite these challenges, there have been several innovations in LSR molding technology that have helped to overcome these obstacles. One of the most significant innovations is advanced mold design and simulation software, which allows for more precise and efficient molding techniques. This software can simulate the molding process and predict the behavior of the material, allowing for more accurate tooling and process optimization.
Another innovation is multi-component molding and overmolding capabilities, which allow for the production of complex parts with multiple materials and colors. This technology can be used to create parts with different durometers, textures, and colors, which can be useful in aerospace applications.
Automated production and quality control systems have also been developed to improve the efficiency and consistency of LSR injection molding. These systems can monitor the molding process in real-time, detect defects, and make adjustments to ensure that the finished product meets all necessary requirements.
Finally, novel material formulations and processing techniques have been developed to expand the range of applications for LSR injection molding. These new materials and techniques can improve the properties of LSR, such as its strength, flexibility, and durability, making it suitable for use in more demanding aerospace applications.
Future Trends in LSR Injection Molding for Aerospace Industry
Looking to the future, there are several trends that are likely to shape the use of LSR injection molding in the aerospace industry. One trend is the increased use of LSR in structural and functional applications. As the properties of LSR continue to improve, it is likely that it will be used in more critical aerospace applications, such as engine components and structural parts.
Another trend is the integration of LSR injection molding with additive manufacturing and 3D printing. This technology can be used to create complex parts with intricate geometries and features that would be difficult to achieve with traditional molding methods.
There is also a growing interest in the development of sustainable and eco-friendly LSR materials. As the aerospace industry seeks to reduce its environmental impact, there is a need for materials that are recyclable, biodegradable, and non-toxic.
Finally, there is an opportunity for LSR molding to expand into emerging aerospace markets, such as space exploration and unmanned aerial vehicles. These markets have unique requirements and challenges that may be well-suited for LSR injection molding.
Impact of LSR Injection Molding on Aerospace Industry Supply Chain
The use of LSR molding in the aerospace industry can have a significant impact on the supply chain. By streamlining production and reducing lead times, LSR injection molding can help to improve the efficiency and reliability of the supply chain. Additionally, the use of LSR injection molding can improve part quality and consistency, reducing the need for rework and improving overall product performance.
LSR injection molding can also enhance collaboration and communication between suppliers and OEMs. By using a common manufacturing process and material, suppliers and OEMs can work more closely together to ensure that the finished product meets all necessary requirements.
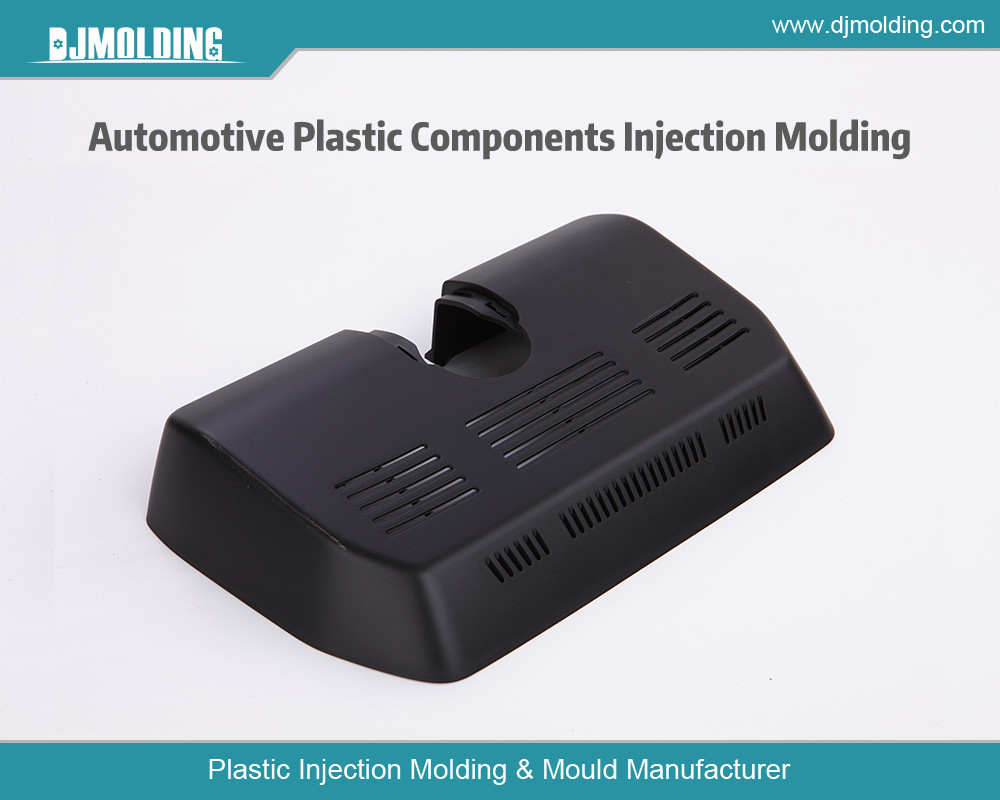
Conclusion: The Future of LSR Injection Molding in Aerospace Industry
In conclusion, LSR molding is a critical technology for the aerospace industry, offering several advantages over traditional molding methods. Despite the challenges faced by LSR injection molding, there have been several innovations in technology that have helped to overcome these obstacles. Looking to the future, there are several trends that are likely to shape the use of LSR molding in the aerospace industry, including increased use in structural and functional applications, integration with additive manufacturing and 3D printing, and the development of sustainable and eco-friendly materials.
For more about the future of liquid silicone rubber injection molding in the aerospace industry,you can pay a visit to Djmolding at https://www.djmolding.com/liquid-silicone-rubberlsr-injection-molding/ for more info.