The Benefits Of Custom Plastic Injection Molding For Plastic Injection Manufacturing Process
The Benefits Of Custom Plastic Injection Molding For Plastic Injection Manufacturing Process
Custom plastic injection molding involves injecting molten plastic into a mold to ensure a particular design or shape is created. This process is widely used in various industries, including automotive, medical, and consumer goods. Choosing the right manufacturing process for your business is crucial to ensure the quality and efficiency of your products.
In this article, we will explore the benefits of custom plastic injection molding and why it may be the right choice for your business. If you have been trying to find out what makes custom plastic injection crucial for your business, ensure to read the details from beginning to the end. Check them out below to help you make a smart decision. So long as you are hiring the right company to handle such process, these benefits will become a reality.
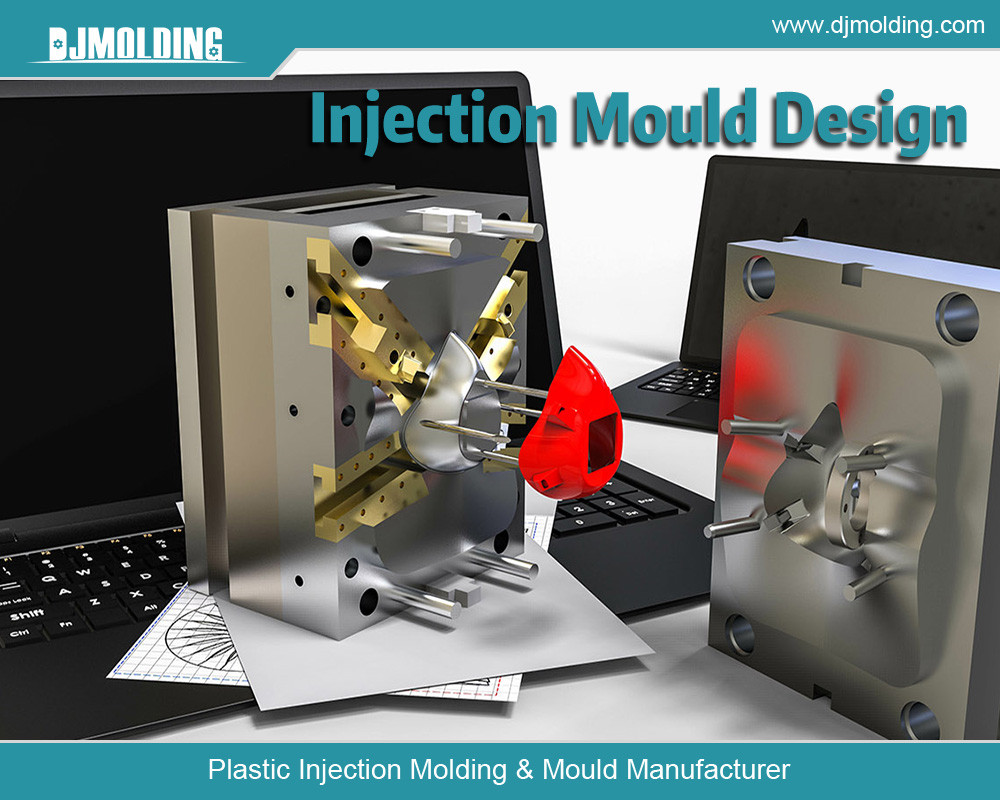
Cost-Effective Production
One of the main benefits of molding custom plastic injection is its cost-effectiveness. This process allows for high-volume production at a lower cost per unit compared to other manufacturing processes. The initial tooling cost may be higher, but the cost per unit decreases as the volume of production increases. This makes it a great option for businesses that require large quantities of products.
In comparison to other manufacturing processes such as CNC machining or 3D printing, custom plastic injection molding is more cost-effective for high-volume production. CNC machining is more suitable for low-volume production, while 3D printing is more suitable for prototyping and small-scale production.
High-Quality and Consistent Results
Molding custom plastic injection produces high-quality and consistent products. The process allows for tight tolerances and precise measurements, resulting in products that meet the required specifications. The use of computer-aided design (CAD) and computer-aided manufacturing (CAM) software ensures accuracy and consistency in the production process.
In comparison to other manufacturing processes such as blow molding or thermoforming, custom plastic injection molding produces products with higher quality and consistency. Blow molding and thermoforming may result in products with uneven thickness or inconsistent shapes.
Versatility in Design and Functionality
Custom plastic injection molding allows for versatile designs and functionality. The process can create complex shapes and designs that may not be possible with other manufacturing processes. The use of different materials and additives can also enhance the functionality of the products.
Examples of unique products that can be created with custom plastic injection molding include medical devices, automotive parts, and consumer goods such as toys and kitchenware.
Faster Turnaround Times
Custom plastic injection molding can speed up production times. The process allows for high-volume production at a faster rate compared to other manufacturing processes. The use of automation and robotics can also increase the speed and efficiency of the production process.
In comparison to other manufacturing processes such as CNC machining or 3D printing, custom plastic injection molding has a faster turnaround time for high-volume production. CNC machining and 3D printing may take longer for low-volume production or prototyping.
Reduced Waste and Environmental Impact
Custom plastic injection molding can reduce waste and environmental impact. The process allows for precise measurements and minimal material waste. The use of recycled materials and biodegradable additives can also reduce the environmental impact of the products.
In comparison to other manufacturing processes such as blow molding or thermoforming, custom plastic injection molding produces less waste and has a lower environmental impact. Blow molding and thermoforming may result in excess material waste and require more energy to produce.
Increased Product Durability and Longevity
Custom plastic injection molding can increase product durability and longevity. The process allows for the use of high-quality materials and additives that can enhance the strength and durability of the products. The precise measurements and tight tolerances also ensure that the products meet the required specifications and can withstand wear and tear.
In comparison to other manufacturing processes such as CNC machining or 3D printing, custom plastic injection molding produces products with higher durability and longevity. CNC machining and 3D printing may result in products with weaker structures or lower durability.
Enhanced Branding and Marketing Opportunities
Molding custom plastic injection can enhance branding and marketing opportunities. The process allows for unique designs and shapes that can stand out in the market. The use of different colors and finishes can also enhance the visual appeal of the products.
Examples of how unique products can stand out in the market include custom-shaped bottles or containers, branded promotional items, and unique packaging designs.
Customization for Unique Business Needs
Molding custom plastic injection can be tailored to unique business needs. The process allows for customization of the products to meet specific requirements or specifications. The use of different materials and additives can also enhance the functionality of the products.
Examples of how businesses have used custom plastic injection molding to their advantage include creating custom medical devices, automotive parts, and consumer goods that meet specific requirements or regulations.
Collaborative Design and Development Process
The design and development process of molding custom plastic injection involves collaboration between the manufacturer and the business. The manufacturer works closely with the business to ensure that the products meet the required specifications and requirements. The use of CAD and CAM software also allows for real-time adjustments and modifications to the design.
The importance of collaboration between the manufacturer and the business ensures that the products meet the required specifications and requirements. The use of CAD and CAM software also allows for real-time adjustments and modifications to the design.
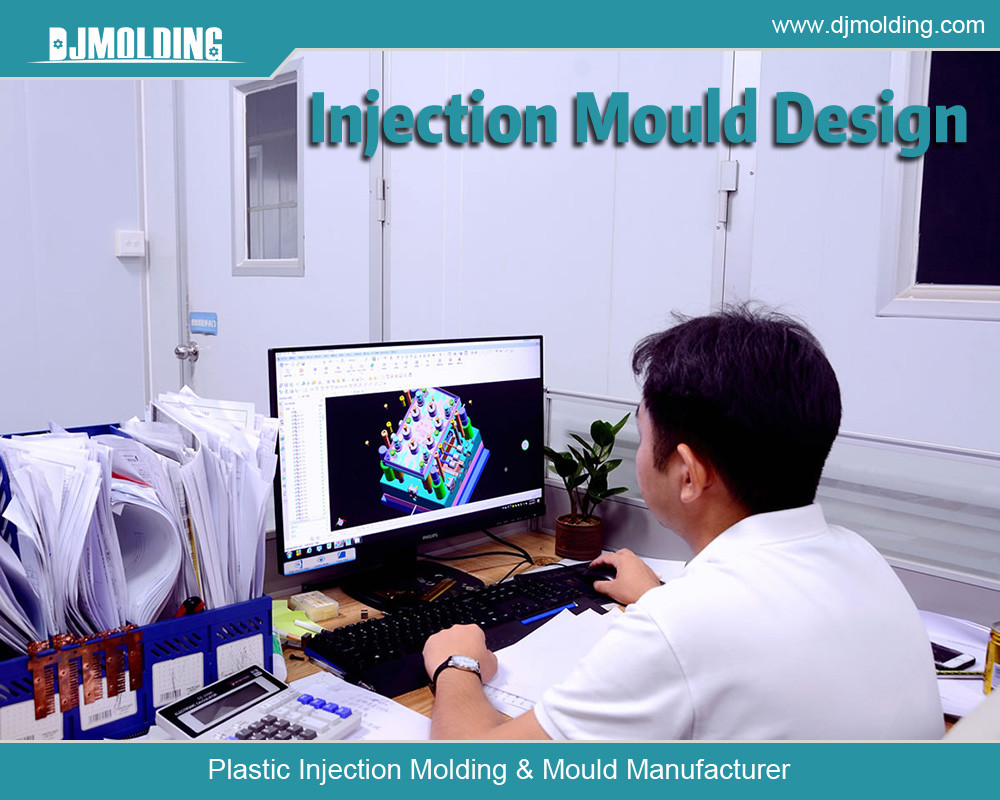
Conclusion
Molding custom plastic injection offers numerous benefits for businesses, including cost-effective production, high-quality and consistent results, versatility in design and functionality, faster turnaround times, reduced waste and environmental impact, increased product durability and longevity, enhanced branding and marketing opportunities, customization for unique business needs, and a collaborative design and development process.
If you are looking for a manufacturing process that can meet your specific requirements and specifications, custom plastic injection molding may be the right choice for your business. The benefits of this process can help you save money, increase efficiency, and enhance the quality of your products.
For more about the benefits of custom plastic injection molding for plastic injection manufacturing process,you can pay a visit to Djmolding at https://www.djmolding.com/custom-plastic-injection-molding/ for more info.