Soft Tooling vs Hard Tooling: What’s The Difference For Injection Molding?
Soft Tooling vs Hard Tooling: What’s The Difference For Injection Molding?
Injection molding is an exemplary manufacturing process that involves injecting material into a mold to create complex parts. Injection Molding plays a crucial role in different parts. There are two types of tooling: tooling and hard tooling. Understanding the differences between these two parts can help manufacturers make informed decisions based on their production needs, budget, and timeliness. Hard and soft tooling highlight their respective advantages, disadvantages, applications, and how they impact the injection molding process. Tooling is acquiring, obtaining, and manufacturing the components and machines needed for production. So, the tooling process has two types: soft tooling and hard tooling.
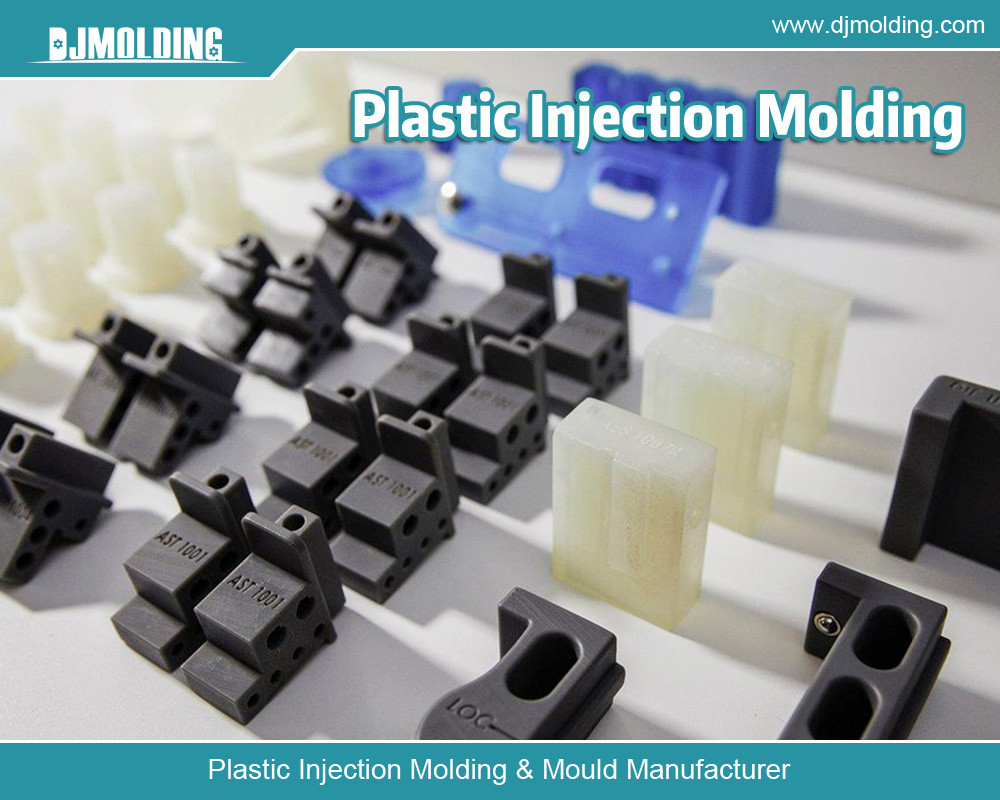
Understanding of soft tooling:
Soft tooling is a good option for companies manufacturing. It is used for prototyping, rapid tooling, bridge tooling, and low-volume production. Soft Tooling is also used for short production. These tools are made from materials that are easier to work with and modify.
The benefits and advantages of soft tooling including:
Lower upfront cost:
- Soft tooling materials like aluminum and copper are less expensive than the high-quality steel used in hard tooling, resulting in lower upfront costs.
Easier modification:
- Soft tooling is more accessible to modify than hard tooling, allowing for design changes and irritation without incurring significant costs.
Reduced weight:
- Soft tooling materials are often lighter than hard tools, making them easier to handle and store.
Cost-effective:
- Soft tooling offers cost-effective solutions for injection molding projects and reduces cost, sacrificing quality or performance.
Environmental friendly:
- Soft tooling materials like aluminum are more recyclable than high-quality materials, making them a more sustainable option.
Bridge tooling:
- Soft tooling can bridge prototyping and high-volume productions, allowing designers to test and refine their designs before investing in hard tooling.
Improved product development:
- Soft tooling enables businesses to test their products before investing in high-volume productions.
Reduced upfront risk:
- Soft tooling reduces upfront risk with high-volume production and enables businesses to test the market and refine their products before making significant investments.
Cost Savings:
- Soft tooling reduces upfront costs by utilizing lower-cost materials like aluminum and copper, making them attractive options for business and product developers.
Design flexibility:
- Soft tooling facilitates design changes without significant costs, enabling businesses to refine and test their products.
Overall, soft tooling offers numerous benefits, making it an attractive option for manufacturers seeking low-quality and efficient production processes.
The characteristics of soft tooling include:
- Upfront Costly: Soft tooling is less expensive than hard tooling, making it an attractive option for small—to medium-size production.
- Design Flexibilities: Soft tooling allows for easy modifications and changes to the tools used for designing, prototyping, and product development.
- Environmental Friendly: Soft tooling materials can be recycled and reused, reducing waste and environmental impact.
- Faster Times: Soft tooling can be produced quickly, in days or weeks, compared to hard tooling, which can take a few months.
- Lightweight: Soft tooling materials are lighter than metal or hard tooling, making them easier to handle and store.
Soft tooling offers a range of benefits and characteristics that make it an attractive option for manufacturing applications.
What is Hard tooling:
Hard tooling is a type of tooling made from high-quality steel. It is more durable and long-lasting, making it suitable for high-volume production.
Hard tooling refers to the use of metals and tools in the manufacturing process. The advantages and benefits of including:
Advantages of hard tooling
Cost-effective :
- Hard tooling costs may be high, hard tooling reduces production costs in the long run due to its durability and efficiency.
Fast production rates:
- Hard tooling enables fast production rates, increasing efficiency and reducing lead times.
Design Flexibility:
- Hard tooling allows for complex designs, enabling the production of intricate parts.
Reduced Maintenance:
- Metal molds and tools require less maintenance compared to soft tooling options.
Benefits of hard tooling:
Longer tool life:
- Metal molds and tools can have high production volumes and harsh environments, reducing the need for frequent replacements.
Improved part quality:
- Hard tooling produces parts with an excellent surface finish and material properties.
Material Versatility:
- Hard tooling can be used with various materials, including plastics, composites, and metals.
Industry standard:
- Hard tooling meets stringent industry standards and regulations, ensuring compliance and quality.
Increased Precision:
- Hard tooling allows for precise control over the manufacturing process, resulting in accurate and consistent parts.
Reduced maintenance:
- Metal molds and tools require less maintenance compared to the soft tooling options.
Scalability:
- Hard tooling is suitable for high-volume production, making it an ideal choice for large-scale manufacturing.
Cost-effectiveness:
- Although initial tooling costs may be high, hard tooling reduces production costs in the long run due to its durability and efficiency.
Faster production rates:
- Hard tooling enables fast production cycles, increasing efficiency and reducing lead times.
The characteristics of hard tooling include:
- Long Tool Life: Hard tooling materials can last many times and reduce the need for frequent replacements.
- High-Volume Production: Hard tooling is suitable for high-volume production and ideal for large-scale manufacturing processes.
- High-Strength: Hard tooling materials have high strength, making them suitable for demanding applications of hard tooling.
- Industry Standards Compliance: Hard tooling meets industry standards and regulations, ensuring compliance and best quality.
- High-Temperature Resistance: Hard toolings can have a high resistance temperature and are suitable for applying hard tooling.
Hard tooling offers many characteristics, such as long tool life, high volume production, and high strength, in application manufacturing.
Critical differences between hard tooling and soft tooling:
Precision:
- Hard tooling offers high precision and accuracy. Soft tooling may be a low compromise on precision, but it is suitable for prototyping and development.
Modifiability:
- Hard tooling is difficult and expensive to modify once produced.
- Soft toolings are Easier and less expensive to modify or change.
Cost:
- Hard tooling has a high initial cost but is cost-effective in the long run. But
- soft tooling lowers initial costs but may require frequent replacements.
Lead Time:
- Hard tooling has longer lead times, often taking months to produce. But
- Soft tooling has faster lead times and can be produced in many days.
Production volume:
- Soft tooling is suitable for low to medium-volume production. And hard tooling for high-volume suitable output.
Time limit:
- Soft tooling allows for quick prototyping and market entry.
- Hard tooling is needed many times to create a project.
Designs Flexibilities:
- Soft toolings have greater flexibility. However, the flexibility of hard tooling is less than that of soft tooling.
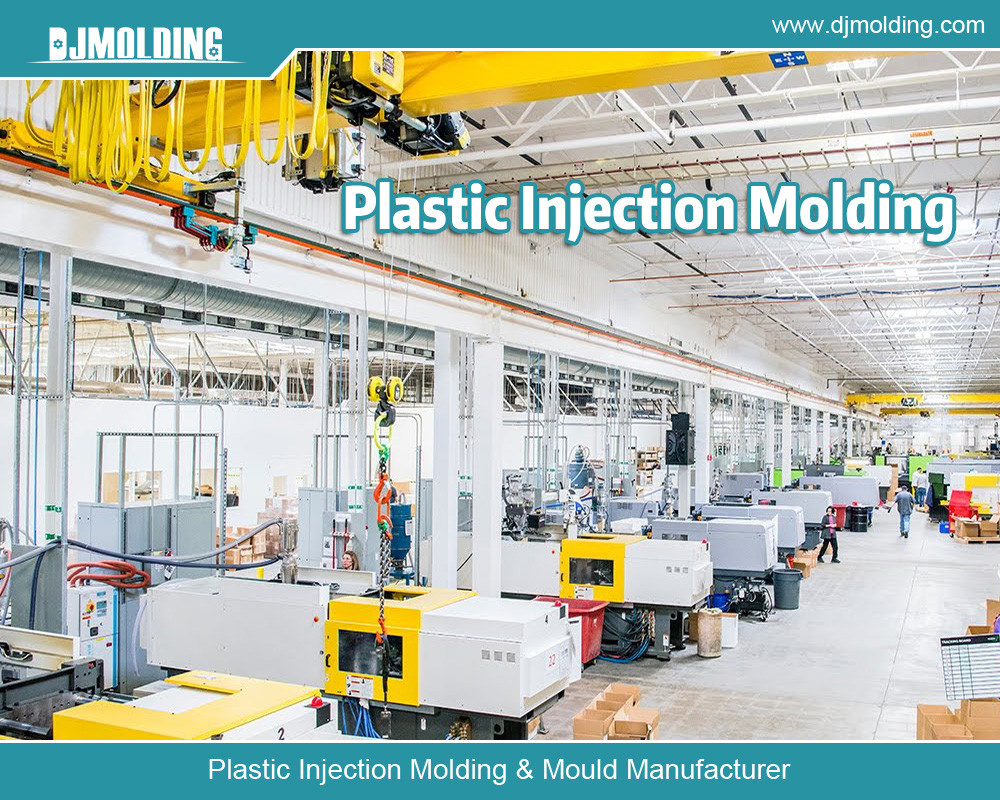
Conclusion
In conclusion, soft and hard toolings have many benefits, advantages, and characteristics of injection molding. Soft tooling allows quick prototyping and market entry, and it produces low volumes of products. On the other hand, hard tooling is suitable for high-volume production, complex designs, and long-term use. Considering the benefits and advantages, characteristics, and differences between hard and soft tooling can help make an informed decision to ensure the success of your injection molding projects.
For more about soft tooling vs hard tooling: what’s the difference for injection molding, you can pay a visit to Djmolding at https://www.djmolding.com/molding-service/ for more info.