Small Batch Plastic Injection Molding Services Suppliers For Custom Plastic Parts Manufacturing
Small Batch Plastic Injection Molding Services Suppliers For Custom Plastic Parts Manufacturing
Small batch injection molding refers to the process of producing custom parts in small quantities using injection molding technology. This method is particularly important for industries that require specialized parts or components that are not readily available in the market. Custom part production plays a crucial role in various industries, including automotive, aerospace, medical, and consumer goods. These industries often require unique parts that are tailored to their specific needs and requirements.
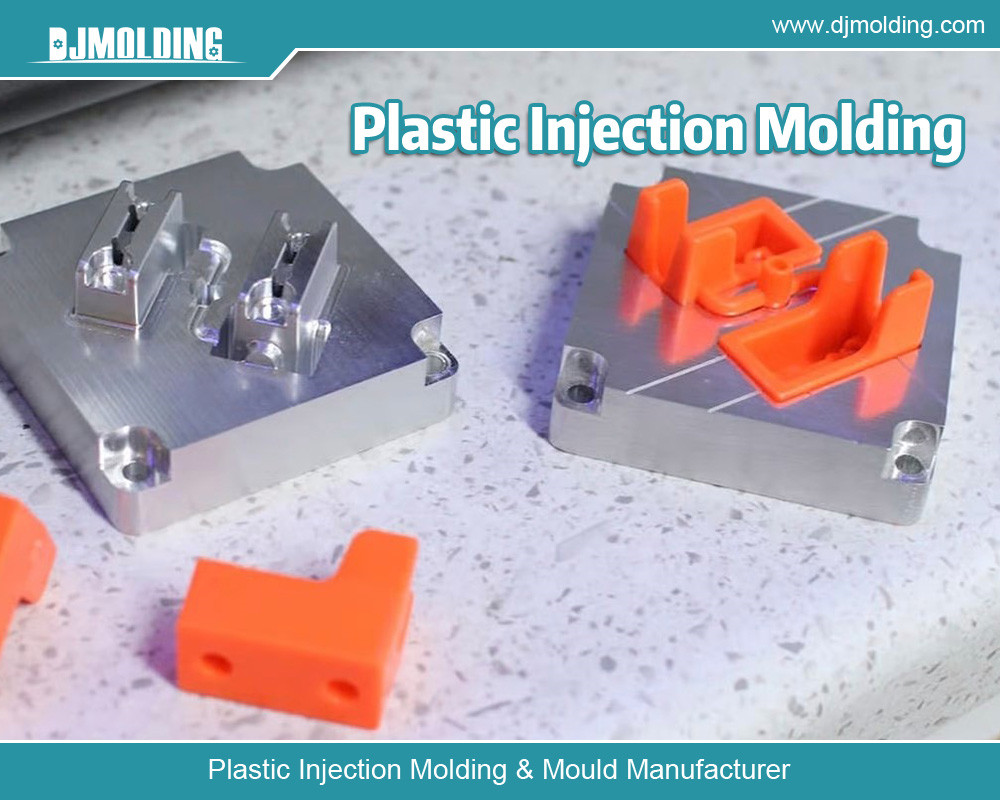
Benefits of Small Batch Injection Molding
One of the key benefits of small batch injection molding is its cost-effectiveness for small production runs. Unlike large-scale production, small batch manufacturing allows for lower upfront costs, making it an ideal solution for businesses with limited budgets. Additionally, small batch injection molding offers faster turnaround times compared to other manufacturing methods. This means that businesses can quickly bring their products to market and respond to changing customer demands.
Another advantage of small batch injection molding is the reduced waste and material costs. With this method, manufacturers can precisely control the amount of material used for each part, minimizing waste and optimizing material usage. This not only helps reduce costs but also contributes to a more sustainable manufacturing process. Furthermore, small batch injection molding provides flexibility in design changes. Manufacturers can easily modify the design of the molds without incurring significant additional costs, allowing for greater adaptability and customization.
Cost-Effective Solution for Custom Part Production
When comparing small batch injection molding with other manufacturing methods, it becomes evident that it offers a cost-effective solution for custom part production. Traditional manufacturing methods often require expensive tooling, which can be a significant barrier for businesses with limited budgets. In contrast, small batch injection molding requires lower tooling costs, making it more accessible for small and medium-sized enterprises.
Moreover, small batch injection molding reduces labor costs compared to manual or semi-automated production methods. The automated nature of the injection molding process allows for higher production efficiency and lower labor requirements. This not only saves costs but also ensures consistent quality and precision in the production of custom parts.
How Small Batch Injection Molding Works
Small batch injection molding involves several steps to produce custom parts. The process begins with the design of the mold, which is typically created using computer-aided design (CAD) software. Once the mold design is finalized, it is manufactured using high-quality materials such as steel or aluminum.
The next step is the preparation of the injection molding machine and the selection of the appropriate materials. The machine is equipped with a hopper that holds the raw material, which is usually in the form of pellets or granules. The material is then heated and melted inside the machine, forming a molten plastic that can be injected into the mold.
Once the mold is filled with molten plastic, it is cooled and solidified to form the desired shape. Afterward, the mold is opened, and the finished part is ejected. This process can be repeated multiple times to produce a batch of custom parts.
Materials Used in Small Batch Injection Molding
Small batch injection molding can accommodate a wide range of materials, including thermoplastics, thermosetting plastics, and elastomers. Each material has its own unique properties and characteristics that make it suitable for specific applications.
Thermoplastics are the most commonly used materials in small batch injection molding due to their versatility and ease of processing. They can be melted and solidified multiple times without undergoing significant changes in their properties. Examples of thermoplastics include polypropylene (PP), polyethylene (PE), polystyrene (PS), and acrylonitrile butadiene styrene (ABS).
Thermosetting plastics, on the other hand, undergo a chemical reaction during the molding process that irreversibly hardens them. This makes them more rigid and durable compared to thermoplastics. Examples of thermosetting plastics include epoxy, phenolic, and melamine.
Elastomers are a type of polymer that exhibits rubber-like properties, such as flexibility and elasticity. They are commonly used in applications that require sealing, cushioning, or vibration dampening. Examples of elastomers include silicone, natural rubber, and polyurethane.
When choosing materials for small batch injection molding, several factors need to be considered, including the mechanical properties required for the part, the operating environment, and any regulatory or safety requirements.
Advantages of Using Small Batch Injection Molding for Prototyping
Small batch injection molding offers several advantages when it comes to prototyping. One of the key advantages is the faster turnaround time compared to traditional prototyping methods such as CNC machining or 3D printing. Injection molding allows for the production of multiple prototypes simultaneously, significantly reducing the time required to test and validate designs.
Moreover, small batch injection molding is a cost-effective solution for testing designs. Unlike other prototyping methods that may require expensive materials or equipment, injection molding allows for the use of production-grade materials at a fraction of the cost. This enables businesses to evaluate the performance and functionality of their prototypes more accurately.
Additionally, small batch injection molding provides the flexibility to make design changes quickly. Since the molds can be easily modified without significant additional costs, designers can iterate and refine their prototypes based on feedback and testing results. This iterative process helps optimize the design and ensures that the final product meets all requirements and specifications.
Applications of Small Batch Injection Molding
Small batch injection molding finds applications in various industries that require custom parts or components. The automotive industry, for example, utilizes small batch injection molding to produce specialized parts such as interior trim, dashboard components, and engine components. The aerospace industry also benefits from small batch injection molding for the production of lightweight and high-strength parts used in aircraft interiors and structural components.
The medical industry relies on small batch injection molding to produce custom medical devices, surgical instruments, and disposable components. The consumer goods industry utilizes this method for the production of custom packaging, household appliances, and electronic devices.
Other industries that benefit from small batch injection molding include electronics, telecommunications, and industrial equipment manufacturing. The versatility and cost-effectiveness of this method make it a viable solution for a wide range of applications.
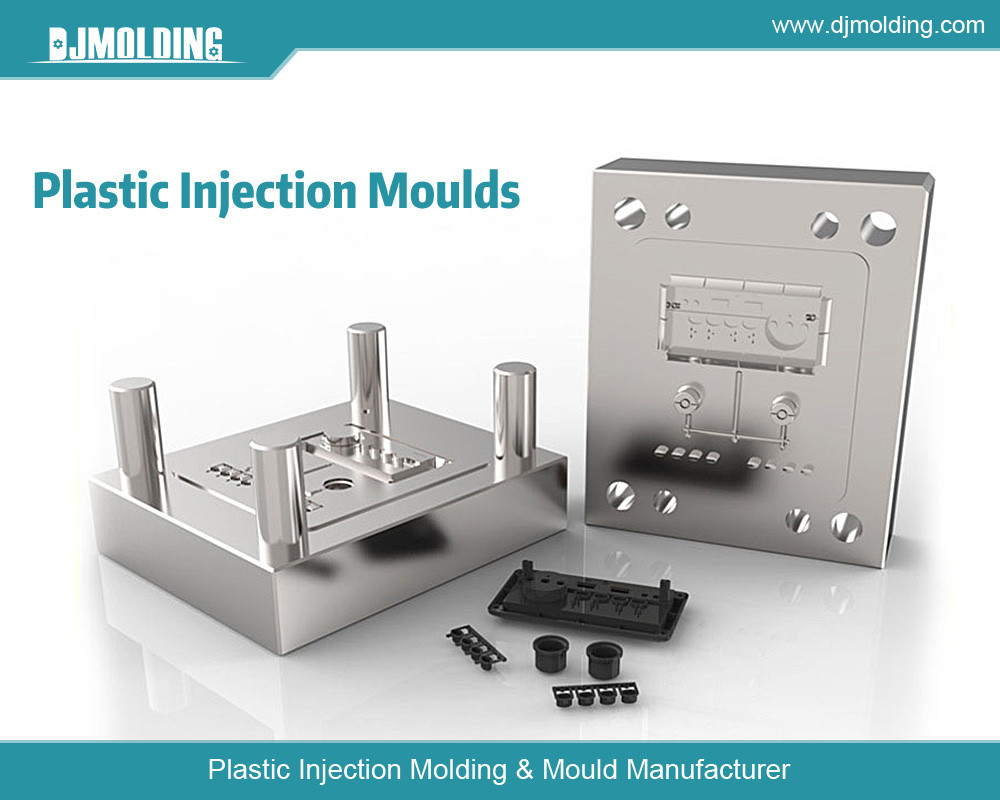
Final Words
In conclusion, small batch injection molding offers a cost-effective and efficient solution for custom part production. Its benefits include cost-effectiveness for small production runs, faster turnaround times, reduced waste and material costs, and flexibility in design changes. Small batch injection molding is particularly advantageous for prototyping, allowing for faster iterations and cost-effective testing of designs.
For more about the small batch plastic injection molding services suppliers for custom plastic parts manufacturing,you can pay a visit to Djmolding at https://www.djmolding.com/injection-mould-manufacturing/ for more info.