Sink Marks In Injection Molding: Causes, Solutions, And Prevention Strategies
Sink Marks In Injection Molding: Causes, Solutions, And Prevention Strategies
Injection molding is a widely used manufacturing process known for its versatility and ability to create complex, high-quality plastic parts. However, it also brings challenges, one of which is the occurrence of sink marks. Sink marks are depressions on the surface of a molded part, typically appearing in thicker sections, corners, or around bosses and ribs. While often cosmetic, sink marks can also weaken the part or hinder its intended function, making their management a priority for engineers and manufacturers. In this article, we’ll explore the causes of sink marks in injection molding, how to prevent them, and effective troubleshooting strategies.
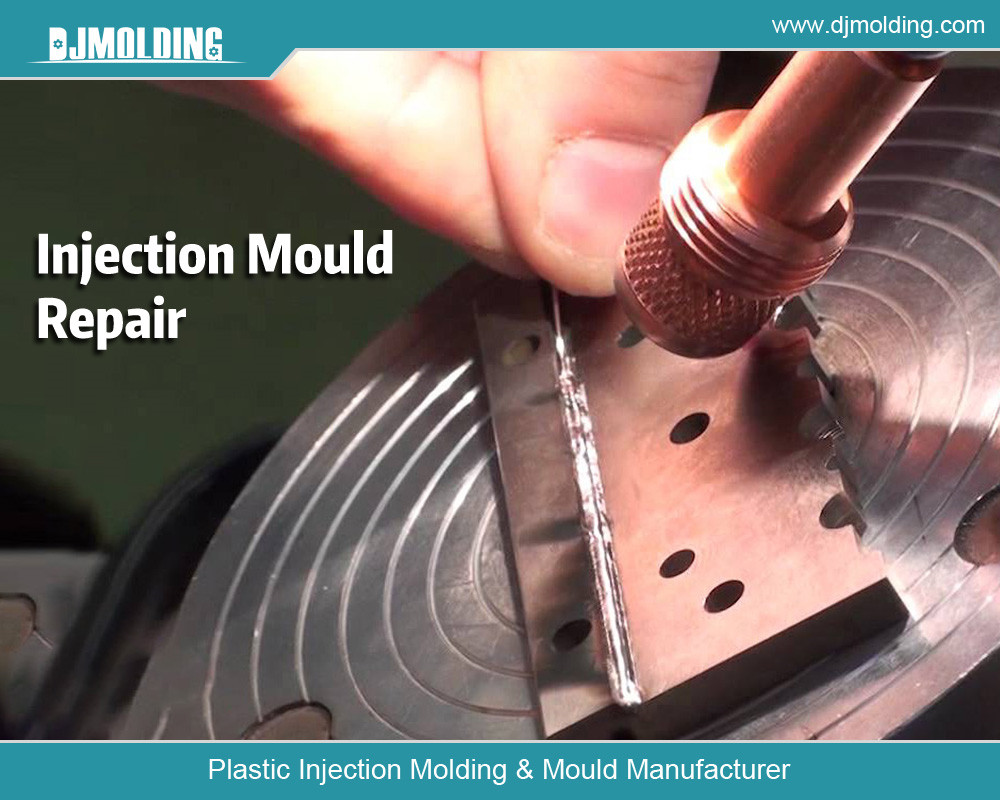
What Are Sink Marks in Injection Molding?
A sink mark is a localized depression or dimple on the surface of an injection-molded part, often resulting from uneven shrinkage of the material as it cools. Sink marks are expected in parts with varying wall thicknesses, especially when thicker sections meet thinner sections. When the plastic cools and solidifies in the mold, the material can shrink at different rates, causing these depressions or “sinks.”
Sink marks can negatively affect a part’s appearance and structural integrity. They are particularly problematic in consumer products, where surface appearance and aesthetics are essential. When designing for injection molding, understanding the causes and mitigation techniques for sink marks is crucial to ensuring a high-quality final product.
Identifying Characteristics of Sink Marks
- Appearance: Sink marks typically appear as small, shallow depressions or dimples on the part’s surface.
- Location: They often occur around thick sections, bosses, ribs, or corner transitions.
- Material: They are more common in thermoplastic parts with a higher shrinkage rate, such as polypropylene, polyethylene, or ABS.
- Impact on Part: Sink marks can affect the appearance, functionality, and strength of a part, depending on their severity and location.
Primary Causes of Sink Marks in Injection Molding
Understanding the root causes of sink marks in injection molding is crucial in developing strategies to mitigate or eliminate them. The most common causes include:
Uneven Cooling Rates
When thicker sections cool more slowly than thinner sections, the outer surface may solidify while the inner material remains molten. As the inner material cools and shrinks, it pulls the surface inward, causing a sink mark. This uneven cooling is a primary reason for sink marks in injection-molded parts.
Inadequate Packing Pressure and Time
Packing pressure refers to the additional pressure applied during the cooling phase of injection molding to compensate for shrinkage. If the packing pressure or time is insufficient, the material may not fill the cavity, especially in thicker sections, resulting in sink marks as the material cools and contracts.
Poor Mold Design
Mold design, including wall thickness, corner transitions, and rib structures, plays a significant role in forming sink marks. Parts with inconsistent wall thicknesses, thick bosses, or ribs without sufficient draft angles are likelier to experience sink marks. The material flows more easily into thicker sections, leading to localized shrinkage and deformation upon cooling.
Material Selection
Certain plastic materials, particularly those with high shrinkage rates (e.g., polypropylene or polyethylene), are more susceptible to sink marks. Other factors, such as the material’s viscosity and cooling characteristics, also influence how prone a material is to developing sink marks.
Processing Conditions
Processing conditions, such as injection speed, melt temperature, mold temperature, and cooling time, can also contribute to sink marks. Higher melt or mold temperatures may allow the material to stay fluid longer, increasing the likelihood of shrinkage during the cooling phase.
Strategies to Prevent Sink Marks in Injection Molding
Addressing mold design, processing parameters, and material selection can manage sink marks. Below are effective strategies to help prevent sink marks.
Optimize Part Design for Consistent Wall Thickness
Inconsistent wall thickness is one of the main reasons for sink marks. To avoid these defects:
- Uniform Wall Thickness: Design parts with consistent wall thicknesses where possible. Reducing the thickness of thicker areas or adding a taper to allow gradual thickness transitions can help prevent shrinkage issues.
- Bosses and Ribs: Avoid placing bosses or ribs directly on the wall; connect them through a “dome” or use cross-ribbing designs. This helps balance the material flow and reduces the risk of sink marks.
Use Proper Gate Location and Design
The gate is the entry point where molten plastic enters the mold cavity, and its location can impact material flow and cooling rates.
- Gate Placement: Place the gate near thicker sections to ensure they are packed more effectively. This minimizes localized shrinkage and reduces the risk of sink marks.
- Gate Type: To help maintain consistent packing pressure in the cavity, use gate types that provide more controlled flow, such as pin or tunnel gates.
Increase Packing Pressure and Time
To counteract shrinkage, adjust the packing phase to ensure that enough material is injected into the cavity, especially in areas prone to sink marks:
- Higher Packing Pressure: Increasing the packing pressure fills thicker sections more effectively, which reduces the chances of sink marks as the material cools.
- Extended Packing Time: Increasing the packing time allows more material to flow into the cavity as the part cools, helping to counteract the formation of sink marks.
Adjust the Cooling Rate and Mold Temperature
The cooling phase should be optimized to minimize differential cooling rates between thick and thin sections.
- Reduce Mold Temperature: Lowering the mold temperature allows quicker solidification of the outer layer, reducing the likelihood of sink marks forming in thicker sections.
- Control Cooling Rate: Use conformal cooling channels in the mold to improve heat dissipation, especially in thicker areas. This approach can help equalize cooling rates and reduce shrinkage in specific regions.
Choose Appropriate Materials
Material selection plays a crucial role in preventing sink marks. Selecting a material with a lower shrinkage rate or better flow characteristics can minimize these defects:
- Low-Shrinkage Materials: Some materials, such as polycarbonate and nylon, exhibit lower shrinkage rates and may be more suitable for parts with varying thicknesses.
- Filled Polymers: Materials reinforced with fillers (e.g., glass or mineral-filled resins) have reduced shrinkage, which can help reduce the formation of sink marks.
Advanced Troubleshooting Tips for Sink Marks
Sink marks can still occur despite implementing preventative strategies. Here are some additional troubleshooting techniques for persistent sink marks in injection molding.
Modify Injection Speed and Pressure Profile
Adjusting the injection speed and pressure profile can help manage the material flow and cooling process:
- Controlled Injection Speed: Reducing the injection speed can reduce the risk of overheating the material, which can cause inconsistent cooling.
- Pressure Profiling: Using a variable pressure profile during injection can allow for more controlled packing and prevent sink marks in thicker sections.
Redesign Mold with Better Cooling Channels
Cooling channel design directly impacts the uniformity of cooling rates in the mold. Consider the following:
- Conformal Cooling: Adding conformal cooling channels close to thicker sections improves heat transfer, reducing the likelihood of differential cooling and shrinkage.
- Selective Cooling: In cases where conformal cooling is not feasible, strategically placed cooling inserts in thicker sections of the mold can improve the cooling balance.
Increase Cycle Time for Better Cooling
Extending the cycle time allows for more thorough cooling and solidification of thicker sections, minimizing the shrinkage differential:
- Cooling Time Extension: Slightly increase the cooling phase of the cycle to ensure the part has time to solidify evenly.
- Ejection Time: Allow the part to remain in the mold for a few extra seconds to reduce warping or sink marks caused by premature ejection.
Use Secondary Processing Techniques
If sink marks are minimal and cannot be corrected through processing adjustments, secondary processing techniques can improve surface finish:
- Surface Coatings: Applying paint or other surface coatings can mask sink marks, especially for parts where appearance is a priority.
- Mechanical Buffing: In some cases, buffing the surface can reduce the visibility of sink marks, especially on larger, flat surfaces.
Common Challenges in Addressing Sink Marks
Addressing sink marks can be challenging, mainly when manufacturing complex parts with intricate geometries or stringent quality requirements. Here are some of the common challenges encountered:
- Balancing Quality and Cycle Time: Adjusting cycle time and cooling rates can increase production costs and reduce efficiency. Balancing these factors with quality requirements can be challenging.
- Material Limitations: Certain materials inherently have higher shrinkage rates, making it difficult to eliminate sink marks without switching to alternative materials.
- Design Constraints: Parts with specific functional or aesthetic requirements may not allow for design modifications, limiting the effectiveness of preventative measures.
- Cost of Mold Modification: Adding cooling channels, modifying gates, or redesigning molds to eliminate sink marks can be costly, particularly for small-scale or limited-run productions.
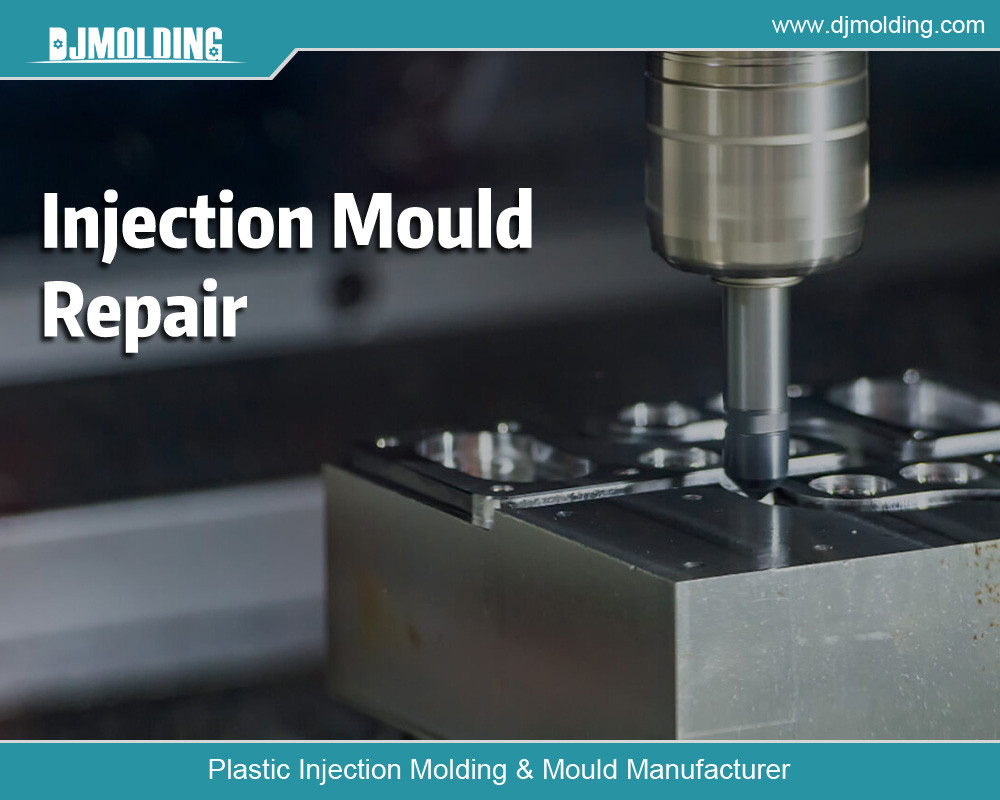
Conclusion
Sink marks in injection molding are a common issue that affects the quality and appearance of molded parts. Addressing this defect requires a thorough understanding of its causes, ranging from uneven cooling and inadequate packing pressure to mold design and material selection. Manufacturers can effectively reduce or eliminate sink marks by employing the right combination of part design, processing conditions, and mold optimization, resulting in higher-quality, defect-free parts.
Understanding and controlling sink marks in injection molding is essential for engineers and manufacturers to deliver a high-quality product. By using the preventative strategies and troubleshooting techniques outlined in this article, manufacturers can meet quality standards, reduce costs associated with rejects or rework, and maintain a competitive edge in the marketplace.
For more about sink marks in injection molding: causes, solutions, and prevention strategies, you can pay a visit to Djmolding at https://www.djmolding.com/ for more info.