POM Injection Molding: An In-depth Guide
POM Injection Molding: An In-depth Guide
Injection molding is a widely used manufacturing process for creating parts with complex geometries from various materials. One of the common materials used in injection molding is Polyoxymethylene, often known by its abbreviation POM or brand names like Delrin. This thermoplastic material is popular in various industries due to its excellent mechanical properties, low friction, and high dimensional stability. This article delves into POM injection molding, exploring its properties, benefits, applications, process parameters, and design considerations to help you understand its role and capabilities in modern manufacturing.
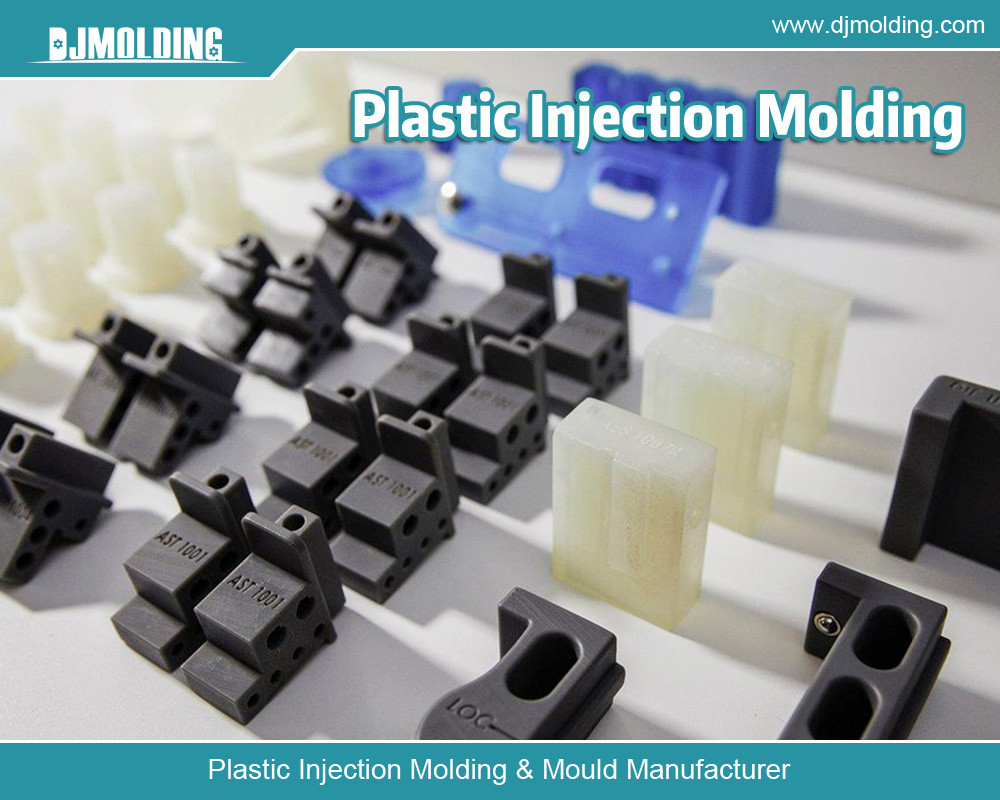
What is POM (Polyoxymethylene)?
Polyoxymethylene (POM) is a high-performance engineering thermoplastic known for its toughness, high strength, and low friction. Structurally, POM is a homopolymer (usually branded as Delrin) or a copolymer, each with unique properties. Its rigid molecular structure gives POM its remarkable durability and hardness. The material comes in two main types:
- Homopolymer POM: Known for higher stiffness and strength.
- Copolymer POM: More chemically resistant and thermally stable, ideal for applications exposed to solvents and moisture.
Key Properties of POM
POM is sought after in injection molding due to its range of desirable mechanical and thermal properties, which include:
- High Strength and Stiffness: POM offers a combination of high tensile strength and flexural modulus, making it suitable for parts that bear heavy loads or undergo stress.
- Dimensional Stability: Its low water absorption rate contributes to its stability, ensuring minimal changes in dimensions, even in humid conditions.
- Low Friction and Wear Resistance: POM’s self-lubricating nature results in low friction, making it ideal for moving parts and reducing wear.
- High Melting Point and Thermal Stability: With a melting temperature range between 162°C and 175°C, POM retains its strength under moderate heat, useful in applications that may expose parts to warmth or heat intermittently.
- Chemical Resistance: POM resists organic solvents, fuels, and weak acids, although it is vulnerable to strong acids and bases.
The Injection Molding Process for POM
The injection molding process for POM follows a sequence of precise steps to ensure consistent quality and performance. Let’s explore each of these stages:
- Material Preparation: POM pellets must be dried before injection molding to prevent moisture-related issues during melting. Typically, drying POM at 80°C for 2-4 hours is sufficient to reduce moisture content.
- Melting and Injection: POM melts at around 175°C and flows readily, essential for forming detailed parts. The material is then injected into a mold at a high pressure, typically between 800 and 1,200 bar, to ensure thorough mold cavity filling.
- Cooling and Solidification: After injection, the mold is cooled, which allows the POM to solidify. Cooling is critical since POM’s shrinkage rate is approximately 2%, meaning that design considerations are necessary for dimensional accuracy.
- Ejection: Once solidified, the molded part is ejected. POM’s rigidity can make ejection challenging, so mold designers incorporate draft angles to facilitate smooth removal.
- Post-Processing: In some cases, post-processing, such as trimming or finishing, may be required. However, POM’s surface quality and detail precision often reduce the need for extensive post-processing.
Parameters for Optimal POM Injection Molding
Successfully molding POM parts requires controlling several parameters:
- Temperature Control: Mold temperature is typically set between 80°C and 120°C, while the barrel temperature should be between 170°C and 200°C. Managing these temperatures helps prevent degradation or deformation.
- Injection Speed and Pressure: Fast injection speeds are recommended to prevent premature cooling and achieve even distribution, while high pressure helps fill intricate details.
- Holding Time: The holding time must be optimized to allow the material to pack and reduce shrinkage, improving the part’s dimensional accuracy.
- Cooling Time: Cooling time can vary based on part thickness but typically ranges from 15 to 60 seconds. Adequate cooling time prevents warping or distortion.
Design Considerations for POM Injection Molding
Proper design is essential to get the most out of POM in injection-molded parts. Here are some critical considerations for designing parts with POM:
- Wall Thickness: Keeping uniform wall thickness across the part reduces the risk of warping and uneven shrinkage.
- Draft Angles: Draft angles should be added to facilitate easy ejection and prevent part sticking.
- Ribs and Reinforcements: Ribs can add strength without increasing thickness, but they should be proportionate to the wall thickness to avoid sink marks.
- Shrinkage Compensation: Account for shrinkage (around 2%) during the design phase to ensure that dimensions are accurate post-molding.
- Flow Length: Limit flow length to avoid short shots, particularly for thicker parts, as POM may cool quickly in long, thin sections.
Benefits of Using POM in Injection Molding
Using POM in injection molding offers several advantages, especially for parts that require precision, resilience, and durability:
- Enhanced Mechanical Properties: POM’s strength and rigidity make it a suitable alternative to metal in specific applications.
- Low Maintenance Needs: POM parts are highly durable and self-lubricating, reducing the need for frequent replacements and maintenance.
- Consistency and Precision: Injection molding with POM enables the creation of intricate, high-tolerance parts that maintain their shape and size under various conditions.
- Cost-Effectiveness: Although POM may have a higher material cost, its durability and low maintenance needs contribute to overall cost savings over the product’s life.
Applications of POM Injection Molded Parts
POM’s desirable characteristics make it a preferred material in numerous industries, including automotive, consumer electronics, and healthcare. Below are some typical applications:
- Automotive Components: POM is commonly used in fuel systems, interior components, and under-the-hood parts, such as gears, clips, and housings, due to its fuel resistance and stability.
- Consumer Electronics: Switches, connectors, and housings benefit from POM’s excellent electrical insulation and durability.
- Industrial Machinery: POM’s self-lubricating properties make it ideal for gears, bearings, and fasteners that must withstand wear.
- Healthcare Equipment: POM is used in medical devices like insulin pumps and drug dispensers due to its chemical resistance.
- Household Products: Its dimensional stability and aesthetic finish make it suitable for high-quality handles, zippers, and fasteners.
Challenges and Limitations of POM in Injection Molding
Despite its advantages, POM does present particular challenges:
- Limited UV Resistance: POM is susceptible to degradation when exposed to prolonged UV light, requiring protective coatings or UV stabilizers for outdoor applications.
- Susceptibility to Strong Acids and Bases: While it is resistant to many chemicals, strong acids and bases can deteriorate POM, making it unsuitable for specific industrial applications.
- Thermal Sensitivity: POM’s melting and decomposition temperatures are close, requiring careful process control to prevent thermal degradation.
- Shrinkage and Warping: POM’s high shrinkage rate and rigidity can make it prone to warping during cooling, which requires careful mold design.
Sustainability and Recycling of POM
Sustainability is a growing concern in injection molding, and while POM can be recycled, the recycling process has limitations:
- Mechanical Recycling: POM can be mechanically recycled, where waste is ground and reprocessed. However, mechanical properties tend to degrade after several recycling cycles.
- Chemical Recycling: Newer methods aim to break down POM into its monomer for reuse, though these processes are still being optimized for efficiency.
- Environmental Impact: POM is relatively stable and has a low degradation rate, making it suitable for long-lasting applications, though it may pose challenges for waste disposal.
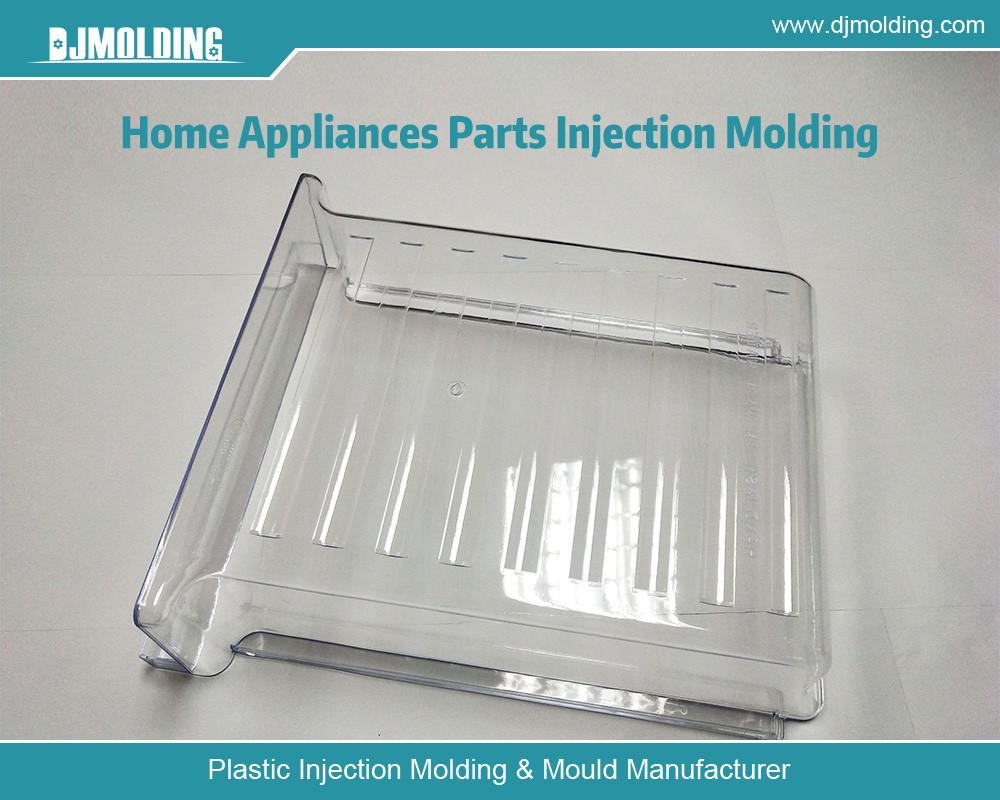
Conclusion
POM injection molding is a crucial technique in modern manufacturing, delivering high-precision, resilient parts for various industries. POM’s strength, durability, and low friction make it a preferred material for components requiring mechanical precision and low maintenance. With optimal processing conditions and mindful design considerations, POM can produce parts that rival metal in durability while offering the advantages of thermoplastic molding, such as versatility and cost-effectiveness.
Manufacturers can harness their full potential by understanding POM’s properties, molding requirements, and design principles, ensuring high-quality, reliable parts that serve critical functions across industries. As new advancements emerge in recycling and material enhancement, POM is valuable in injection molding, contributing to durable, efficient, and cost-effective solutions.
For more about pom injection molding: an in-depth guide, you can pay a visit to Djmolding at https://www.djmolding.com/ for more info.