Plastic Injection Molding Manufacturers And Companies In Korea: Pioneering Innovation And Quality
Plastic Injection Molding Manufacturers And Companies In Korea: Pioneering Innovation And Quality
Plastic injection molding is a crucial manufacturing process that has revolutionised various industries by enabling the production of intricate plastic components with high precision and efficiency. In Korea, the landscape of plastic injection mold manufacturing has evolved significantly, driven by innovation, technological advancements, and a growing demand for quality products. This article explores the current state of plastic injection mold manufacturers in Korea, their capabilities, challenges, and contributions to the global market.
-
Custom Low Volume Plastic Parts Manufacturing The Growth of Plastic Injection Mold Industry in Korea
Korea’s plastic industry has witnessed robust growth over the years, buoyed by technological advancements and a burgeoning manufacturing sector. The injection mold segment, in particular, has expanded rapidly to meet the diverse needs of industries such as automotive, consumer goods, electronics, and healthcare.
- Emergence of Technological Hubs: Cities like Pune, Chennai, Bengaluru, and Ahmedabad have emerged as critical hubs for plastic injection mold manufacturing. These regions benefit from a robust industrial base, skilled workforce, and supportive infrastructure.
- Adoption of Advanced Machinery: Korean mold manufacturers have increasingly invested in state-of-the-art machinery and equipment to enhance production capabilities and meet international quality standards.
- Technological Advancements and Innovation
Innovation is at the heart of Korea’s plastic injection mold industry, driving competitiveness and differentiation in the global market.
- Tool Design and Simulation: Manufacturers leverage advanced CAD/CAM software for tool design and simulation, enabling precise mold development and optimization of production processes.
- Industry 4.0 Integration: Adopting Industry 4.0 technologies such as IoT, AI, and automation has streamlined operations, improved efficiency, and minimized downtime in manufacturing facilities.
- Material and Process Innovation: Continuous research and development efforts focus on exploring new materials and refining injection molding techniques to achieve superior product quality and performance.
- Quality Standards and Certification
Ensuring adherence to stringent quality standards is paramount for Korean plastic injection mold manufacturers to gain global acceptance and maintain competitiveness.
- ISO Certification: Many manufacturers in Korea are ISO 9001 certified, demonstrating their commitment to quality management systems and continuous improvement.
- Compliance with International Standards: Compliance with global standards such as ASTM, DIN, and JIS ensures that products meet the requirements of international markets, fostering trust and reliability among global customers.
- Challenges Faced by Plastic Injection Mold Manufacturers
Despite the industry’s growth trajectory, Korean mold manufacturers encounter several challenges that impact their operations and growth prospects.
- Skill Shortage: There is a persistent need for skilled technicians and engineers with specialized knowledge in mold design, maintenance, and operation.
- Cost Pressures: Fluctuations in raw material costs, energy prices, and competitive pricing pressures pose challenges to maintaining profitability.
- Infrastructure Bottlenecks: Inadequate infrastructure, particularly transportation and logistics, can hinder timely delivery and increase operational costs.
- Market Trends and Opportunities
The Korean plastic injection mold industry is poised for continued growth, driven by evolving market trends and emerging opportunities.
- Rising Demand in the Automotive Sector: With increasing vehicle production and demand for lightweight components, there is a growing need for precision molds that meet automotive industry standards.
- Electronics and Consumer Goods: The proliferation of electronic devices and consumer appliances fuels the demand for high-precision molds to manufacture intricate plastic parts.
- Medical and Healthcare Applications: Injection molds play a critical role in producing medical devices and equipment, presenting significant growth opportunities driven by advancements in healthcare technology.
- Global Competitiveness and Export Potential
Korean plastic injection mold manufacturers increasingly focus on enhancing global competitiveness and exploring export opportunities.
- Partnerships and Collaborations: International OEMs and strategic alliances with global players enable technology transfer and market expansion.
- Export Markets: Korean manufacturers are targeting markets in North America, Europe, and the Asia-Pacific region, leveraging competitive pricing and compliance with quality standards to gain market share.
- Future Outlook and Innovations
The future of plastic injection mold manufacturing in Korea appears promising, propelled by innovation, technological advancements, and strategic initiatives.
- Advanced Materials and Sustainable Practices: Emphasis on sustainable materials and environmentally friendly practices will drive innovation in mold design and production processes.
- Digital Transformation: Increased adoption of digital technologies and predictive analytics will further optimize manufacturing processes and enhance operational efficiency.
- Government Initiatives: Supportive government policies and incentives to promote manufacturing excellence and technological innovation will create a conducive environment for industry growth.
- Case Studies of Leading Plastic Injection Mold Manufacturers
To provide a deeper insight into the capabilities and contributions of Korean plastic injection mold manufacturers, let’s examine case studies of some leading companies in the industry:
- JeongWoo Precision: Based in South Korea, JeongWoo Precision specializes in designing and manufacturing high-precision injection molds for the automotive, electronics, and healthcare industries. The company is known for its advanced mold simulation capabilities and stringent quality control processes, ensuring reliable and durable molds that meet global standards.
- Shinsung Mold Co., Ltd.: Located in South Korea, Shinsung Mold Co., Ltd is renowned for its expertise in complex mold designs and rapid prototyping services. The company leverages advanced CNC machining and EDM technologies to produce molds with intricate geometries and tight tolerances, catering to diverse customer requirements across sectors.
- Daewon: Operating from South Korea, Daewon has established itself as a critical player in the injection molding industry by focusing on innovation and customer-centric solutions. The company offers comprehensive mold design, tooling, and production services, serving automotive, consumer goods, and industrial clients.
These case studies illustrate the diversity and specialization within Korea’s plastic injection mold manufacturing sector, showcasing companies that have excelled in innovation, quality assurance, and customer satisfaction.
- Sustainable Practices and Environmental Responsibility
In response to global environmental concerns, Korean plastic injection mold manufacturers are increasingly adopting sustainable practices and embracing eco-friendly initiatives.
- Recycling and Waste Reduction: Implementing recycling programs for plastic waste generated during manufacturing processes helps minimize environmental impact and supports circular economy principles.
- Energy Efficiency: Adoption of energy-efficient technologies and processes reduces operational costs and lowers carbon footprint, contributing to sustainable manufacturing practices.
- Green Materials: Exploration of bio-based and recyclable materials for mold production aligns with global trends towards sustainability, offering customers environmentally responsible solutions.
- Collaborations and Industry Partnerships
Collaborations and partnerships play a pivotal role in the growth and innovation of Korea’s plastic injection mold industry, fostering knowledge exchange, technology transfer, and market expansion.
- Academic Institutions: Collaborations with universities and research institutes facilitate R&D initiatives, enabling manufacturers to stay at the forefront of technological advancements in materials science and manufacturing processes.
- International OEMs and Suppliers: Partnerships with multinational OEMs and suppliers enable access to advanced technologies, global supply chains, and market insights, enhancing competitiveness and expanding market reach.
- Industry Associations: Active participation in industry associations and trade organizations provides networking opportunities, advocacy support, and access to industry best practices, fostering industry growth and development.
- Regulatory Landscape and Compliance
Navigating regulatory requirements and compliance standards is crucial for Korean plastic injection mold manufacturers to ensure product quality, safety, and market acceptance.
- Regulatory Standards: Adherence to national and international regulatory standards such as RoHS, REACH, and FDA regulations is essential for manufacturing molds in automotive, electronics, and medical devices.
- Quality Management Systems: Implementing robust quality management systems (QMS) and certifications such as ISO 13485 (for medical devices) and ISO/TS 16949 (for the automotive industry) underscores a commitment to quality and compliance.
- Challenges and Opportunities in Export Market Expansion
While Korean plastic injection mold manufacturers have made significant strides in the domestic market, expanding into international markets presents challenges and opportunities.
- Competitive Pricing: Price competitiveness remains crucial in global markets, necessitating efficient cost management strategies and optimization of manufacturing processes to offer competitive pricing without compromising on quality.
- Cultural and Market Adaptation: Understanding cultural nuances and market dynamics in target regions is essential for effective market penetration and long-term partnerships with international customers.
- Trade Barriers and Tariffs: Negotiating trade barriers, tariffs, and regulatory hurdles in international markets requires strategic planning and engagement with local trade authorities and industry associations.
- Future Directions and Strategic Imperatives
Looking ahead, several strategic imperatives will shape the future growth and competitiveness of Korea’s plastic injection mold manufacturing industry:
- Investment in Technology and Innovation: Continued investment in advanced technologies such as additive manufacturing, AI-driven design optimization, and automation will drive efficiency, product innovation, and competitiveness.
- Skills Development and Talent Acquisition: Addressing the skill gap through vocational training programs, apprenticeships, and collaborations with educational institutions will ensure a skilled workforce capable of meeting industry demands.
- Diversification and Market Expansion: Diversifying product portfolios and expanding into emerging sectors such as renewable energy, aerospace, and telecommunications will mitigate risks associated with sector-specific economic fluctuations.
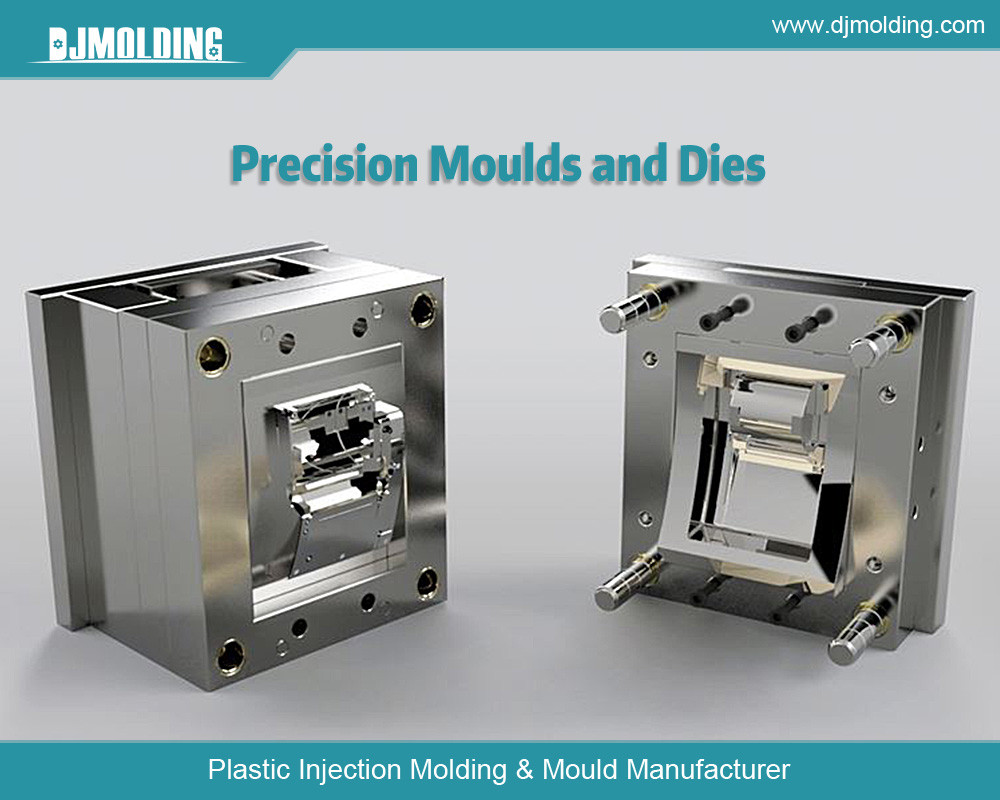
Conclusion
Korea’s plastic injection mold manufacturing sector has evolved into a dynamic and competitive industry characterised by technological innovation, adherence to quality standards, and a growing focus on global markets. Despite facing challenges, manufacturers continue to innovate and expand their capabilities, positioning Korea as a critical player in the global plastic injection mold market. As the industry embraces digital transformation and sustainable practices, the future holds immense growth potential, driven by ongoing advancements and strategic collaborations.
For more about the plastic injection molding manufacturers and companies in korea: pioneering innovation and quality,you can pay a visit to Djmolding at https://www.djmolding.com/best-top-10-plastic-injection-molding-manufacturers-and-companies-in-usa-for-plastic-parts-manufacturing/ for more info.