Plastic Injection Molding
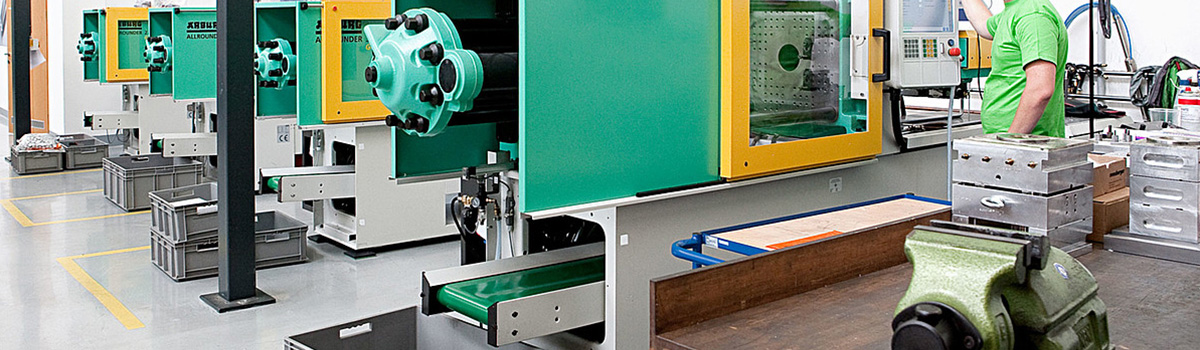
Plastic injection molding is a manufacturing process that involves melting plastic pellets and injecting them into a mold cavity to create a three-dimensional object. This process begins with many products, from small precision parts to significant automotive components. Plastic injection molding offers many advantages over other manufacturing processes, including high production rates, design flexibility, and cost-effectiveness. This guide will look in-depth at plastic injection molding and explore its various applications, benefits, and limitations.
The History of Plastic Injection Molding
Plastic injection molding is a manufacturing process that involves injecting molten plastic into a mold cavity to create a specific shape. The history of plastic injection molding can be traced back to the late 1800s when celluloid, a type of plastic, was first invented. However, it was in the 1940s that plastic injection molding became widely used as a manufacturing technique.
During World War II, the demand for mass-produced plastic products increased, and manufacturers began to search for new and more efficient ways to produce them. In 1946, James Watson Hendry, an American inventor, developed the first screw injection molding machine, which revolutionized the plastic injection molding industry. This machine allowed for more precise and consistent injection process control, making producing large quantities of plastic parts more accessible and efficient.
Throughout the 1950s and 1960s, advancements in plastics technology continued to improve the plastic injection molding process. The introduction of new materials, such as polystyrene and polyethylene, created more complex and durable plastic parts. Additionally, improvements in molding machine technology, including using hydraulic systems, made the injection molding process even more efficient and cost-effective.
Today, plastic injection molding is a highly automated process used to produce a wide range of plastic products, from toys and consumer goods to automotive parts and medical devices. With the development of new materials and technologies, the plastic injection molding process continues to evolve and improve, ensuring that it will remain a vital manufacturing technique for many years.
The Basics of Plastic Injection Molding
Plastic injection molding is a manufacturing process to create parts and products made from plastic materials. The process involves injecting molten plastic into a mold, which cools and solidifies to form the desired shape.
The basic steps involved in the plastic injection molding process are as follows:
- Mold design: The first step in the process is to design the mold that will be used to create the desired part. The mold is typically made from metal and must be prepared to account for the shrinkage as the plastic cools and solidifies.
- Material preparation: The plastic material used in the injection molding process comes in the form of pellets or granules, which must be melted down and prepared for injection into the mold. This is typically done in a hopper, where the plastic is heated to a specific temperature and melted into a liquid state.
- Injection: Once the plastic is melted, it is injected into the mold using a specialized injection molding machine. The machine applies pressure to the molten plastic, forcing it into the mold cavity, where it takes on the shape of the mold.
- Cooling and solidification: After the plastic is injected into the mold, it can cool and solidify. This can take anywhere from a few seconds to several minutes, depending on the size and complexity of the part.
- Ejection: Once the plastic has cooled and solidified, the mold is opened, and the part is ejected. The position may require additional finishing work, such as trimming or sanding, to remove excess plastic or rough edges.
Plastic injection molding is an exact and repeatable process, making it ideal for mass-producing parts and products with consistent quality. It is also highly versatile, as it can create pieces and products in various sizes, shapes, and complexities. Some of the most common applications of plastic injection molding include the production of toys, consumer goods, automotive parts, and medical devices.
Plastic Injection Molding Process: Step-by-Step
Plastic injection molding is a complex process that involves several steps. Here is a step-by-step guide to the plastic injection molding process:
- Designing the Mold: The first step is to design the mold used to create the part. The mold is typically made from steel or aluminum and must be prepared to accommodate the plastic material’s shrinkage as it cools.
- Creating the Mold: Once the mold design is complete, it is manufactured using computer-aided design (CAD) software and computer-aided manufacturing (CAM) machinery. The mold must be carefully machined and polished to ensure the final product’s accuracy and finish.
- Material Selection: The plastic resin material used for the injection molding process must be chosen based on the part’s requirements, such as its strength, flexibility, color, and texture.
- Material Preparation: The chosen plastic material is then heated to a specific temperature and melted into a liquid. The material is then injected into the molding machine’s hopper.
- Injection Molding: The molten plastic material is injected into the mold cavity using a specialized injection molding machine. The machine applies pressure to the plastic material, forcing it into the mold cavity, where it takes on the shape of the mold.
- Cooling: Once the mold cavity is filled with plastic, it can cool and solidify. The cooling time is determined by the plastic material’s characteristics, the size and thickness of the part, and the mold temperature.
- Ejection: After the plastic has solidified, the mold is opened, and the part is ejected from the mold using ejector pins.
- Finishing: The ejected part may require additional finishing work, such as trimming, sanding, or painting, to remove any excess plastic or rough edges.
- Quality Control: The finished part undergoes a thorough inspection to meet the required specifications and quality standards.
Plastic injection molding can produce various parts and products in multiple sizes, shapes, and complexities. The process is widely used in several industries, including automotive, medical, consumer goods, and electronics.
Types of Plastic Used in Injection Molding
Many types of plastic can be used in injection molding. The choice of plastic material will depend on the specific requirements of the product or part being produced, such as strength, flexibility, durability, and appearance. Here are some of the most common types of plastic used in injection molding:
- Polyethylene (PE): PE is a widely used plastic material known for its strength and flexibility. It is used to produce various products, including packaging materials, toys, and medical devices.
- Polypropylene (PP): PP is a lightweight and durable plastic material commonly used in the automotive industry for interior parts, such as dashboards and door panels. It also produces packaging materials, such as containers and bottles.
- Polycarbonate (PC): PC is a solid and transparent plastic material commonly used to produce electronic components, such as computer and phone cases. It is also used for headlamp lenses and dashboard components in the automotive industry.
- Acrylonitrile Butadiene Styrene (ABS): ABS is a versatile plastic material known for its strength, durability, and heat resistance. It is commonly used to produce automotive parts, such as dashboards, fender flares, toys, and consumer goods.
- Polyamide (PA): PA, also known as nylon, is a strong and lightweight plastic material that is commonly used in the production of automotive parts, such as engine covers and air intake systems. It also produces sports equipment, such as ski boots and tennis rackets.
- Polystyrene (PS): PS is a lightweight and rigid plastic material that is commonly used in the production of packaging materials, such as cups, trays, and food containers. It also produces consumer goods, such as toys and electronic components.
- Polyethylene Terephthalate (PET): PET is a robust and transparent plastic material commonly used to produce packaging materials, such as bottles and containers. It is also used in the textile industry to produce fibers and fabrics.
These are just a few of the most common types of plastic used in injection molding. Many other types of plastic materials are available, each with unique properties and characteristics. The choice of plastic material will depend on the specific requirements of the part or product being produced.
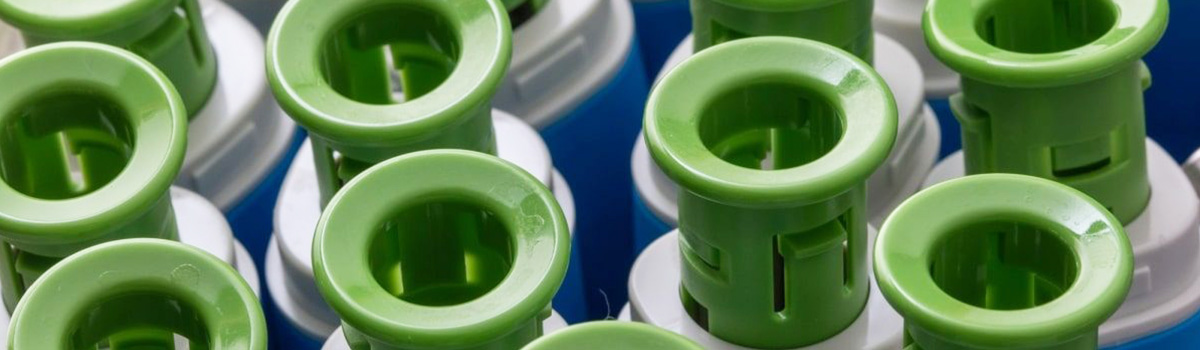
Types of Injection Molding Machines
Injection molding machines come in various types and sizes, each designed to meet specific manufacturing requirements. Here are some of the most common types of injection molding machines:
- Hydraulic Injection Molding Machine: This machine uses hydraulic power to generate pressure to inject plastic into the mold. Hydraulic machines are typically used for more significant parts that require high clamping force.
- Electric Injection Molding Machine: Electric machines use electric motors to power the injection unit and the clamp mechanism. They are known for their high precision and energy efficiency, making them famous for producing small, intricate parts.
- Hybrid Injection Molding Machine: Hybrid machines combine the benefits of hydraulic and electric devices, using both hydraulic and electric power to generate the necessary pressure and power. Hybrid machines offer a good balance of speed, precision, and energy efficiency.
- Vertical Injection Molding Machine: Vertical machines produce parts that require insert molding or over-molding. They have a vertical clamping unit that allows easy access to the mold, making them ideal for creating small or complex parts.
- Two-Shot Injection Molding Machine: Two-shot machines produce parts with different materials or colors. The device has two injection units, each capable of injecting foreign material into the mold. This type of machine is commonly used to produce automotive parts, such as handles and knobs.
- Multi-Shot Injection Molding Machine: Multi-shot machines produce parts with more than two materials or colors. The device has multiple injection units, each capable of injecting a different material into the mold. This type of machine is commonly used to produce consumer goods, such as toothbrushes and razors.
- All-Electric Injection Molding Machine: All-electric machines use electric motors to power the injection unit, the clamp mechanism, and the mold. They are known for their high precision, speed, and energy efficiency, making them famous for producing small, high-precision parts.
These are just a few of the most common types of injection molding machines. Each machine has unique features and advantages, making it essential to choose the suitable device for the specific manufacturing requirements.
Parts of an Injection Molding Machine
Injection molding machines have several parts that create plastic parts from raw materials. Here are the critical components of an injection molding machine:
Hopper: The reservoir holds the raw plastic material before it is fed into the injection molding machine. The material is typically in the form of pellets or powder.
Barrel: The barrel is the long, cylindrical part of the injection molding machine that houses the screw, which melts and mixes the plastic material.
Screw: The screw is a rotating device inside the barrel that pushes the plastic material forward and melts it by friction and heat.
Injection unit: The injection unit includes the hopper, barrel, and screw and is responsible for melting and injecting plastic into the mold.
Clamping unit: The clamping unit is responsible for securely holding the mold and applying the necessary pressure during the injection molding process.
Mold: The mold is the tool that creates the shape and size of the plastic part. The mold is typically made of steel and consists of two halves that fit together.
Nozzle: The nozzle is the part of the injection unit that connects the injection molding machine to the mold. The melted plastic material is injected through the nozzle and into the mold.
Cooling system: The cooling system is responsible for cooling the plastic part once injected into the mold. This ensures the piece is solidified and can be removed from the mold without damage.
Control panel: The control panel is the interface that allows the operator to monitor and adjust the settings of the injection molding machine, such as temperature, pressure, and cycle time.
Each of these parts plays a critical role in the injection molding process, and it is essential to maintain and optimize each piece to ensure high-quality parts are produced efficiently.
Injection Molding Tooling: Design and Manufacturing
Injection molding tooling refers to designing and manufacturing the molds used in injection molding machines to produce plastic parts. The quality and efficiency of the molds directly affect the quality and productivity of the injection molding process. Here are the critical steps in the design and manufacturing of injection molding tooling:
Product design: The first step in injection molding tooling is designing the product to be produced. The product design includes determining the part’s size, shape, and material, as well as any specific features or requirements.
Mold design: The mold design process begins once the product design is finalized. The mold designer will determine the best type of mold, the number of cavities needed, and the size and shape of the mold.
Mold construction: The mold is constructed based on the mold design, using high-quality materials such as steel or aluminum. The mold is typically made in two halves, each containing one or more cavities.
Mold assembly: Once the mold is constructed, it is assembled and tested for accuracy and functionality. The mold must withstand the pressure and heat of the injection molding process.
Mold testing and validation: After the mold is assembled, it is tested and validated to ensure that it produces high-quality parts that meet the product specifications. The mold may need to be adjusted or modified to improve its performance.
Mold maintenance: Regular maintenance and repair of the mold are critical to ensure its longevity and performance. This includes cleaning, lubricating, and replacing any worn or damaged parts.
Injection molding tooling requires precision and expertise to produce high-quality parts consistently and efficiently. By following a complete design and manufacturing process, manufacturers can make molds that meet the unique requirements of their products and optimize their injection molding processes.
Types of Injection Molding Tooling
Injection molding is a widely used manufacturing process for producing parts in large quantities. It involves injecting molten plastic into a mold cavity and allowing it to cool and solidify into the desired shape. Injection molding tooling is the process of creating the molds used in injection molding. There are several types of injection molding tooling, each with its own advantages and disadvantages.
- Two-Plate Molds Two-plate molds are the simplest type of injection molding tooling. They consist of two plates clamped together to form a mold cavity. The molten plastic is injected into the hole through a gate and allowed to cool and solidify. Once the part is created, the two plates are separated, and the amount is ejected. Two-plate molds are commonly used for small to medium-sized components with simple geometries.
- Three-Plate Molds Three-plate molds are similar to two-plate molds, but they have an additional plate, known as the stripper plate, which separates the molded part from the runner system. The runner system is the channel network that delivers the molten plastic to the mold cavity. Three-plate molds are used for more significant parts and more complex geometries.
- Hot Runner Molds In hot runner molds, the molten plastic is injected directly into the mold cavity through a series of heated channels rather than through a gate. This reduces the material wasted in the runner system, resulting in a more efficient process. Hot runner molds are used for the high-volume production of complex parts.
- Family Molds Family molds produce multiple parts in a single mold. They have various cavities arranged in a way that allows for the production of numerous domains simultaneously. Family molds are commonly used for parts with small to medium-sized volumes.
- Insert Molds Insert molds produce parts that require metal or plastic inserts. The inserts are placed into the mold cavity before injecting the molten plastic. Once the plastic has cooled and solidified, the part and the insert are permanently bonded. Insert molds are used for positions that require strength, durability, or aesthetic appeal.
- Overmolding Overmolding is a process in which a part is molded over another. It is often used for positions that require a soft touch or improved grip. Overmolding involves setting a substrate or base part first and then molding a second material over it. The second material can be a different type of plastic, a rubber-like material, or a thermoplastic elastomer.
In conclusion, the choice of injection molding tooling depends on the type of part being produced, the required production volume, and the level of complexity involved in the part design. Choosing the proper tooling is essential to ensure the process is efficient and cost-effective.
Injection Molding Design Guidelines
Injection molding is a widely used manufacturing process for producing plastic parts. Designing parts for injection molding requires a good understanding of the process, the materials, and the design guidelines that must be followed to ensure that the details can be successfully manufactured. Here are some injection molding design guidelines to keep in mind:
Wall Thickness, The wall thickness of the part should be uniform and as thin as possible while maintaining the required strength and functionality. This helps reduce the cooling and cycle time and minimizes the risk of warping and sink marks.
Ribs and Bosses Ribs and bosses can be used to increase the strength and rigidity of the part. Ribs should be no more than 60% of the nominal wall thickness, and bosses should be 1.5 times the nominal wall thickness.
Draft Angle, A draft angle of at least 1-2 degrees should be used on all vertical surfaces to facilitate part ejection and prevent damage to the mold.
Fillets and Radii Sharp corners and edges should be avoided to prevent stress concentration, which can lead to cracking and failure. Instead, fillets and radii should distribute stress and improve the part’s strength.
Gates and Runners The location and design of the gates and runners are critical for achieving good part quality. Entrances should be as small as possible in the thickest section of the part. Runners should be designed to minimize pressure drop and maximize flow.
Surface Finish The part’s surface finish should be specified based on the application requirements. A higher surface finish may be required for visible pieces, while a lower surface finish may be acceptable for hidden parts.
Material Selection The material selected for the part should be suitable for injection molding and meet the required mechanical, thermal, and chemical properties.
Secondary Operations in Injection Molding
Injection molding is a versatile manufacturing process used to produce various plastic parts. In addition to the primary molding process, many positions require secondary operations to achieve the desired shape, finish, or functionality. Here are some everyday secondary operations in injection molding:
- Trimming is removing excess material from the molded part after it has been ejected from the mold. This is typically done using a trim press or a CNC machine. Trimming is often required to achieve the final shape and size of the part.
- Welding combines two or more plastic parts using heat, pressure, or a combination of both. This is often used to create larger or more complex features that cannot be produced in a single mold.
- Decorating is the process of adding visual or functional features to the surface of the molded part. This can include painting, printing, labeling, or applying a texture or pattern.
- Assembly is the process of joining multiple parts to create a complete product. This can be done using fasteners, adhesives, or other joining techniques.
- Insert Molding Insert molding is molding plastic around a pre-formed metal or plastic insert. This is often used to create parts with a high level of strength or durability.
- Overmolding Overmolding is the process of molding a second material over a pre-formed part. This can add a soft-touch surface, improve grip, or create a two-tone or multi-material piece.
- The coating applies a thin material layer to the part’s surface to improve its appearance, durability, or other properties. This can include coatings such as chrome, nickel, or powder coatings.
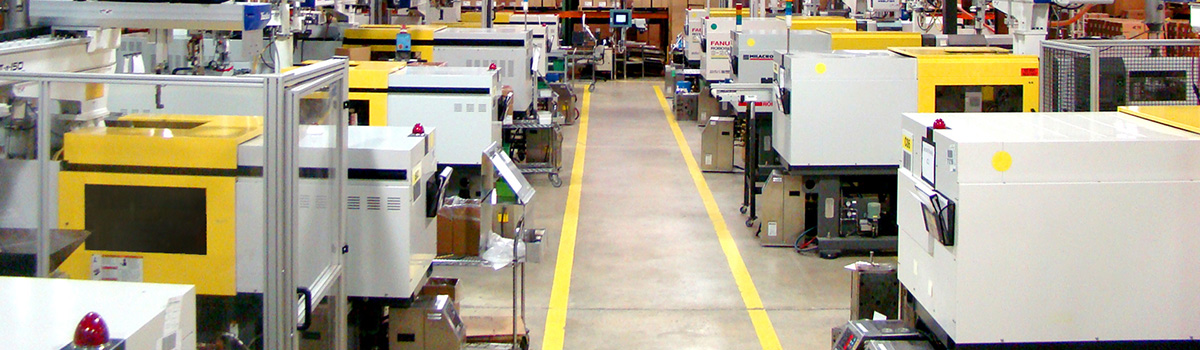
Advantages of Plastic Injection Molding
Plastic injection molding is a widely used manufacturing process for producing plastic parts with high accuracy, consistency, and quality. It involves injecting molten plastic into a mold cavity and allowing it to cool and solidify. Here are some advantages of plastic injection molding:
- High Efficiency and Productivity Plastic injection molding is a highly efficient and automated process that can produce large volumes of parts with high consistency and quality. With advanced automation technology, the production cycle time can be reduced to seconds, which allows for high-volume production of complex and intricate parts.
- High Accuracy and Precision Injection molding increases accuracy and precision in producing complex and intricate parts. Computer-controlled machinery and advanced software enable tight tolerances with high repeatability and accuracy.
- Versatility Injection molding is a versatile process that can produce a wide range of plastic parts of different sizes, shapes, and complexity. The process can be used to make everything from small pieces with intricate details to large amounts with complex geometries.
- Material Flexibility Injection molding can use a wide range of plastic materials, including thermoplastics, thermosets, and elastomers. This allows for producing parts with various mechanical, thermal, and chemical properties.
- Low Waste Production Injection molding is a low-waste production process as it generates minimal waste during production. Any excess material can be easily recycled and reused in production, making it an environmentally friendly manufacturing process.
- Reduced Labor Costs The high degree of automation in injection molding minimizes the need for labor-intensive processes, significantly reducing labor costs. This also reduces the risk of human error, improving the final product’s quality and consistency.
- Reduced Post-Production Operations Injection molding produces parts with high accuracy and consistency, reducing the need for post-production operations such as trimming, drilling, or milling. This reduces the production time and cost of the final product.
- Consistency and Quality Injection molding produces parts with a high level of consistency and quality. Advanced technology and computer-controlled machinery ensure that every detail is identical in shape, size, and quality.
- Design Flexibility Injection molding offers a high degree of design flexibility, as it allows for producing parts with complex geometries, undercuts, and intricate details. This will enable designers to create pieces with unique shapes and functions that cannot be made using other manufacturing processes.
- Cost-effective for High-Volume Production Injection molding is a cost-effective process for producing plastic parts. The initial tooling cost can be high, but the cost per part decreases as the volume of production increases. This makes it an ideal process for producing large quantities of parts.
Plastic injection molding offers many advantages, making it a popular choice for producing plastic parts. Its high efficiency, accuracy, versatility, material flexibility, low waste production, reduced labor costs, and consistency and quality make it an ideal process for various applications. The ability to produce complex and intricate parts with high design flexibility and cost-effectiveness for high-volume production makes it a highly sought-after manufacturing process.
Disadvantages of Plastic Injection Molding
Plastic injection molding is a widely used manufacturing process that involves injecting molten plastic into a mold cavity to produce a wide range of plastic parts and products. Although plastic injection molding has numerous benefits, there are also several disadvantages. Here are some of the main disadvantages of plastic injection molding:
- High tooling costs: The cost of designing and producing a mold for plastic injection molding can be very high. This is because the mold needs to be made from high-quality materials and precisely machined to create the desired part. Additionally, the cost of designing and manufacturing the mold may be prohibitive for small-scale production runs, making plastic injection molding less economical for low-volume manufacturing.
- Long lead times: The process of designing and producing a mold for plastic injection molding can take a long time, which can delay the production of plastic parts. This can be particularly problematic for businesses that need to quickly respond to changes in market demand or rapidly develop new products.
- Limited flexibility: Once the mold is designed and produced, it is easier and cheaper to change the design or modify the production process. This can limit the flexibility of plastic injection molding and make it less suitable for producing custom or one-of-a-kind products.
- Environmental concerns: Plastic injection molding relies on large amounts of plastic, which can have negative ecological impacts. Plastic waste is a major environmental issue, and plastic injection molding can contribute to this problem. Additionally, the process of manufacturing plastic products requires the use of energy and natural resources, which can further impact the environment.
- High scrap rates: Plastic injection molding can produce significant scrap material, which can be expensive to dispose of or recycle. Additionally, the production of scrap material can increase the overall production cost and reduce the manufacturing process’s efficiency.
- Limited material options: Plastic injection molding is primarily used for producing parts and products from thermoplastic materials, which have limited properties compared to other materials such as metals or ceramics. This can make plastic injection molding less suitable for applications that require high strength, temperature resistance, or other advanced properties.
Limitations of Plastic Injection Molding
While plastic injection molding offers numerous advantages, certain limitations are also associated with the process. Here are some limitations of plastic injection molding:
High Initial Tooling Cost: The initial cost of designing and manufacturing the mold can be increased. The mold needs to be precise and durable to withstand the repeated injection molding process, and this can require a substantial upfront investment, especially for complex or large molds.
Lead Time: The lead time for manufacturing the mold can be significant, ranging from weeks to months, depending on the complexity and size of the mold. This can cause delays in the production timeline, particularly for time-sensitive projects.
Design Constraints: Injection molding has certain design limitations that must be considered. For instance, achieving uniform wall thickness throughout the part is critical to ensure proper filling and cooling. Additionally, draft angles are required on vertical surfaces to enable easy ejection from the mold.
Part Size Limitations: Injection molding is most suitable for producing small to medium-sized parts. Large parts may require specialized equipment and larger molds, adding to the cost and complexity.
Material Selection: While injection molding allows for a wide range of plastic materials, the choice of material is still limited compared to other manufacturing processes. Materials with high melting points or poor flow characteristics may not be suitable for injection molding.
Surface Finish: The injection molding process may result in visible knit lines or parting lines on the part’s surface. Achieving a high-quality surface finish can be challenging, and other methods, such as polishing or coating, may be required.
Limited Undercuts: Undercuts are features or details on a part that prevent it from being easily removed from the mold. Undercuts can complicate the ejection process and require additional mold features or secondary operations to achieve the desired part geometry.
Limited Repair Options: If a mold is damaged or needs modification, it can be costly and time-consuming to repair or alter the existing mold. Sometimes, a completely new mold may need to be manufactured, leading to additional expenses and delays.
Despite these limitations, plastic injection molding remains a highly versatile and widely used manufacturing process for producing plastic parts. By carefully considering these limitations during the design and production planning stages, it is possible to mitigate their impact and effectively leverage the advantages of injection molding.
Applications of Plastic Injection Molding
Plastic injection molding is a versatile manufacturing process that can produce a wide range of plastic parts. Here are some of the applications of plastic injection molding:
- Consumer Products: Injection molding is widely used to produce various products, such as toys, kitchenware, and electronics. The process can produce high-quality parts with intricate geometries and precise dimensions, making it ideal for products that require tight tolerances and complex shapes.
- Automotive Parts: Many automobile plastic components, such as dashboard components, door handles, and lighting, are produced using injection molding. The process allows for high production volumes and consistent quality, making it a cost-effective option for automotive manufacturers.
- Medical Devices: Injection molding is commonly used to produce medical devices, such as syringes, inhalers, and diagnostic equipment. The process can produce parts with high precision and consistency, ensuring the quality and reliability of the devices.
- Packaging: Injection molding is widely used to produce plastic packaging, such as containers, lids, and caps. The process can have parts with consistent dimensions and high-quality finishes, making it ideal for packaging with an attractive appearance and a secure fit.
- Aerospace and Defense: Injection molding produces various aerospace and defense components, such as aircraft interiors, lighting, and communication systems. The process can have parts with lightweight, durable materials, making them suitable for applications that require high strength-to-weight ratios.
- Construction: Injection molding can produce various construction materials, such as plastic tiles, roofing, and siding. The process can have parts with consistent dimensions and high-quality finishes, making it an attractive option for construction companies.
- Sports and Recreation: Injection molding is widely used in producing sports equipment, such as golf clubs, tennis rackets, and bicycle components. The process can produce parts with lightweight materials and precise geometries, ensuring the performance and durability of the equipment.
Overall, plastic injection molding is a versatile and widely used manufacturing process that can produce high-quality plastic parts for various applications. The process can be tailored to meet specific design and production requirements, making it an attractive option for manufacturers in multiple industries.
Automotive Industry and Plastic Injection Molding
The automotive industry is a significant user of plastic injection molding technology. The process of plastic injection molding has revolutionized the production of automotive parts and components, making it possible to produce complex shapes with high precision and accuracy. Here are some of the ways plastic injection molding is used in the automotive industry:
- Interior parts: Plastic injection molding produces many internal factors, including dashboard components, door panels, trim pieces, and more. These parts can be designed with intricate shapes and textures and customized to match each vehicle model’s style and functionality requirements.
- Exterior parts: Plastic injection molding is also used to produce various exterior features, including bumpers, grilles, side mirrors, and more. These parts can be designed to withstand extreme weather conditions and are made in multiple colors and finishes.
- Under-the-hood components: Plastic injection molding produces many under-the-hood features, including engine covers, air intake systems, and cooling system parts. These components require high temperature and chemical resistance, which can be achieved with thermoplastic materials.
- Electrical and electronic components: Plastic injection molding produces various electrical and electronic components, including connectors, housings, and sensors. These components require high precision and reliability, which can be achieved with the accuracy and consistency of plastic injection molding.
- Lightweighting: Plastic injection molding is often used to produce lightweight parts that help reduce the overall weight of a vehicle, improving fuel efficiency and reducing emissions. Lightweighting can also improve the handling and performance of a vehicle.
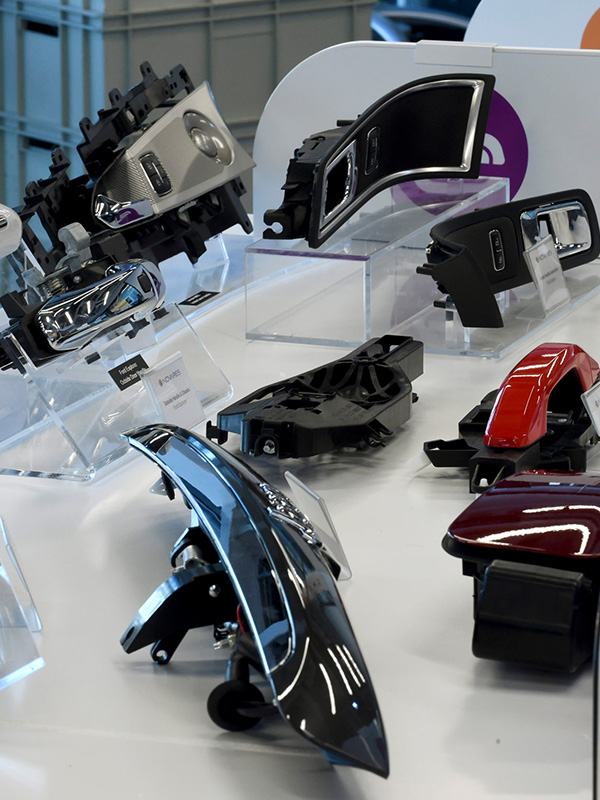
Medical Industry and Plastic Injection Molding
Plastic injection molding is widely used in the medical industry to produce a variety of medical devices and components. The process of plastic injection molding allows for the production of complex shapes with high precision and accuracy, making it an ideal manufacturing method for many medical applications. Here are some of the ways plastic injection molding is used in the medical industry:
- Medical devices: Plastic injection molding produces various medical devices, including surgical instruments, diagnostic tools, drug delivery systems, etc. These devices often require high precision and accuracy, and plastic injection molding can meet these requirements.
- Implants: Plastic injection molding is also used to produce a variety of implants, including joint replacements, dental implants, and more. These implants can be designed to match the patient’s anatomy and produced with biocompatible materials.
- Laboratory equipment: Plastic injection molding produces pipettes, microplates, and test tubes. These components require high precision and accuracy to ensure reliable results.
- Packaging: Plastic injection molding is used to produce packaging for medical devices, including sterile barrier systems and custom packaging for individual products. These packaging solutions can help maintain the medical device’s sterility and integrity.
- Single-use devices: Plastic injection molding often produces single-use devices such as syringes, needles, and catheters. These devices can be made in high volume at a low cost and can help to prevent the spread of infections in healthcare settings.
Consumer Products and Plastic Injection Molding
Plastic injection molding is widely used in the production of consumer products due to its versatility, efficiency, and cost-effectiveness. The process of plastic injection molding allows for the production of complex shapes with high precision and accuracy, making it an ideal manufacturing method for many consumer applications. Here are some of the ways plastic injection molding is used in the production of consumer products:
- Toys: Plastic injection molding produces a wide range of toys, from small figurines to larger playsets. The process allows for creating intricate designs and details and making toys in various colors and materials.
- Household goods: Plastic injection molding produces various household goods, including kitchen utensils, storage containers, and cleaning supplies. These products can be designed to be durable, lightweight, and easy to use.
- Electronics: Plastic injection molding produces many electronic components, including computer housings, phone cases, and chargers. The precision and accuracy of the process ensure that these components are made with a high degree of consistency and reliability.
- Personal care products: Plastic injection molding produces unique care products, including toothbrushes, razors, and hairbrushes. These products require high precision and accuracy to ensure ease of use and safety.
- Automotive accessories: Plastic injection molding produces a range of automotive accessories, including dashboard components, cup holders, and more. These components can be designed to be lightweight, durable, and resistant to the wear and tear of daily use.
Environmental Considerations in Plastic Injection Molding
Plastic injection molding is a widely used manufacturing process but has significant environmental implications. Here are some of the ecological considerations in plastic injection molding:
- Material selection: The choice of plastic material used in injection molding can significantly impact the environment. Some materials are biodegradable or recyclable, while others are not. Using biodegradable or recyclable materials can help reduce the environmental impact of plastic injection molding.
- Energy consumption: Plastic injection molding requires significant energy to melt the plastic and inject it into the mold. Energy-efficient equipment and processes, such as electric machines and closed-loop systems, can reduce energy consumption and environmental impact.
- Waste management: Plastic injection molding generates waste from excess material, defective parts, and packaging. Proper waste management practices, such as recycling and reusing waste material, can help to reduce the environmental impact of plastic injection molding.
- Chemical usage: Some chemicals in plastic injection moldings, such as mold release agents and cleaning solvents, can harm the environment. Using environmentally friendly alternatives or minimizing the use of these chemicals can help to reduce the environmental impact.
- End-of-life considerations: Plastic products produced through injection molding often end up in landfills, which can take hundreds of years to degrade. Designing products for recyclability or biodegradability can reduce the environmental impact of plastic injection molding.
Future of Plastic Injection Molding
The future of plastic injection molding looks promising, as advances in technology and materials are expected to make the process even more efficient, cost-effective, and sustainable. Here are some of the trends and developments that are likely to shape the future of plastic injection molding:
- Additive manufacturing: Additive manufacturing, also known as 3D printing, is an emerging technology that can potentially transform plastic injection molding. By using 3D printing to create molds, manufacturers can significantly reduce the time and cost associated with traditional mold-making techniques.
- Smart manufacturing: Smart manufacturing, which involves automation, data analytics, and machine learning, is expected to revolutionize plastic injection molding. Manufacturers can improve efficiency, reduce waste, and increase productivity by using sensors and data analytics to optimize processes.
- Sustainable materials: Sustainable materials, such as bioplastics and recycled plastics, are becoming increasingly popular in the plastic injection molding industry. These materials offer environmental benefits and can help manufacturers to meet sustainability goals.
- Micro molding: Micro molding, which involves producing small parts with high precision, is becoming more critical in industries such as healthcare and electronics. Advances in technology and materials are expected to make micro molding more accessible and cost-effective.
- Customization: As consumers demand more personalized products, plastic injection molding is expected to become more flexible and customizable. Advances in technology, such as real-time feedback and machine learning, will enable manufacturers to produce custom products quickly and efficiently.
Conclusion:
Plastic injection molding is a highly versatile and efficient manufacturing process that has revolutionized the production of a wide range of products. From medical devices to automotive components, plastic injection molding offers numerous advantages over other manufacturing processes, including high production rates, design flexibility, and cost-effectiveness. With continuous advancements in technology and materials, the future of plastic injection molding looks bright, and this process will likely play an even more significant role in the manufacturing industry in the coming years.