PEEK Injection Molding: A High-Performance Polymer Manufacturing Process
PEEK Injection Molding: A High-Performance Polymer Manufacturing Process
Introduction to PEEK Injection Molding
Polyether ether ketone, or PEEK, is a high-performance engineering thermoplastic renowned for its excellent mechanical and thermal properties. PEEK injection molding is widely used in demanding aerospace, automotive, medical, and electronics applications. The unique properties of PEEK make it an ideal choice where strength, heat resistance, and chemical stability are crucial. This article delves into the PEEK injection molding process, its benefits, challenges, and applications.
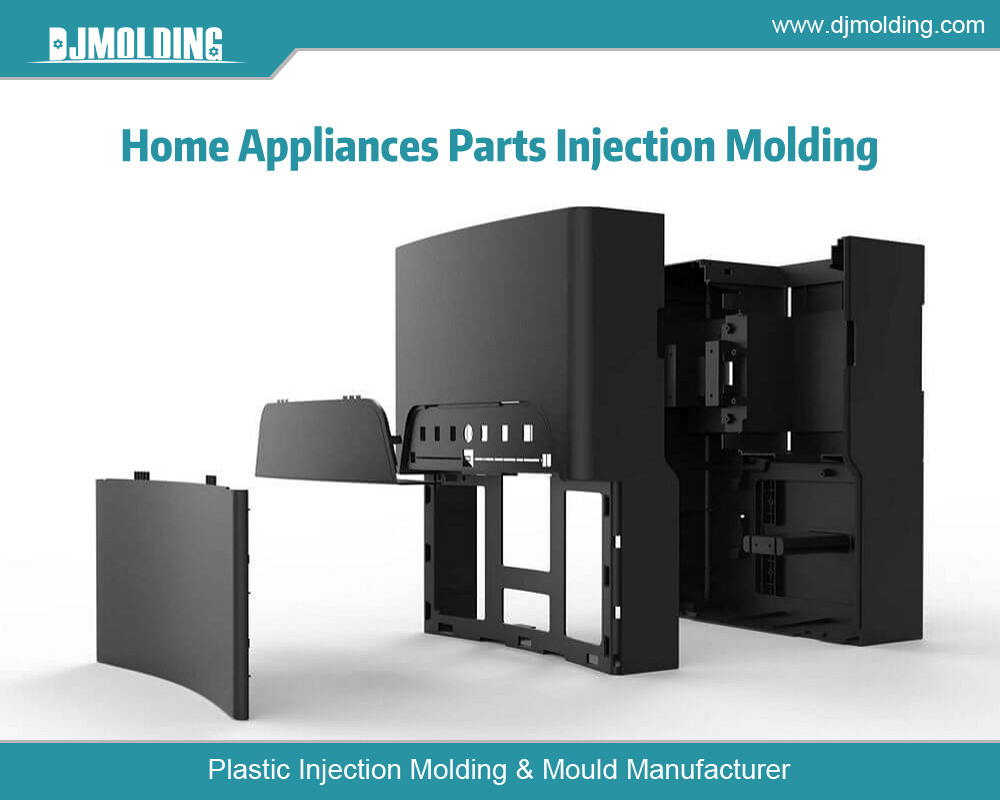
Understanding PEEK: What Makes It Special?
PEEK is a semi-crystalline thermoplastic with a high melting temperature (up to 343°C or 649°F). Its combination of properties makes it stand out:
- Thermal Stability: PEEK maintains its mechanical properties in high temperatures, with a continuous-use temperature of around 250°C (482°F).
- Chemical Resistance: PEEK is resistant to most chemicals, including acids, oils, and solvents, making it suitable for harsh environments.
- Mechanical Strength: This polymer has high tensile strength and stiffness, comparable to metals for specific applications.
- Low Moisture Absorption: Low moisture absorption (<0.1%) ensures stable performance in humid or wet environments.
- Biocompatibility: PEEK is biocompatible, making it an excellent choice for medical implants and devices.
These properties enable PEEK to perform in extreme conditions, making it ideal for parts that withstand high stresses, temperatures, and chemical exposures.
The PEEK Injection Molding Process
Injection molding is a widely used manufacturing process for producing complex plastic parts in large volumes. PEEK injection molding is similar to standard injection molding but requires specialized equipment and process parameters due to PEEK’s high melting temperature and viscosity. Here’s an outline of the critical steps and considerations involved in PEEK injection molding.
Material Preparation
The PEEK resin is usually in pellet form and must be dried thoroughly to prevent moisture-related defects. Since PEEK is highly hygroscopic, even a tiny amount of moisture can result in bubbles and poor surface finish. The drying temperature for PEEK is around 150°C (302°F), typically needing 3-4 hours to ensure complete drying.
Mold Design
Mold design is critical in PEEK injection molding, as it determines the final product’s quality, shape, and durability. Key considerations include:
- High-Temperature Tolerant Mold Materials: PEEK requires molds that can withstand temperatures above 200°C (392°F), often made from materials like hardened steel.
- Ventilation and Ejector Design: Adequate ventilation is essential to prevent trapped gases, and the ejector mechanism must be strong enough to handle PEEK’s high stiffness.
- Cooling System: PEEK parts need uniform cooling to avoid warping and maintain dimensional accuracy. A well-designed cooling system ensures consistent part quality.
Injection Molding Machine Settings
Due to PEEK’s high melting point and viscosity, specialized injection molding machines or high-temperature-resistant configurations are often used. Critical parameters include:
- Temperature Control: The barrel temperature should be between 350 and 400°C (662-752°F), with the mold temperature maintained at around 160 to 200°C (320-392°F).
- Injection Pressure and Speed: PEEK requires high injection pressure, usually around 10,000-20,000 psi, due to its high viscosity. However, injection speed should be carefully controlled to prevent premature solidification and voids.
- Cycle Time: PEEK’s cooling time is generally longer than standard plastics, increasing the overall cycle time. This factor should be considered in production planning.
Post-Molding Processes
After molding, PEEK parts may require additional processes to ensure optimal performance, such as:
- Annealing reduces internal stresses and enhances crystallinity, improving the material’s mechanical properties and thermal stability.
- Deburring and Finishing: Some applications require a smooth finish or tight tolerances so that parts may be polished or machined post-molding.
Challenges in PEEK Injection Molding
PEEK’s unique properties present several challenges during the injection molding process:
High-Temperature Requirements
PEEK’s high melting point means that standard injection molding machines cannot process it without modifications. The equipment must have high-temperature-resistant components, which can increase setup and maintenance costs.
Mold, Wear and Tear
PEEK is a highly abrasive material, especially in filled forms (e.g., glass or carbon fiber-filled PEEK). Over time, this can wear down the mold, leading to increased maintenance and shorter mold life.
Shrinkage and Warpage
PEEK exhibits moderate shrinkage (around 1.2%—2.4%) but can be prone to warpage if cooled unevenly. Careful control of cooling and mold design is required to minimize dimensional instability.
Limited Color Options
PEEK is naturally a beige or brown color, and it is challenging to dye or pigment without compromising its properties. This can limit design flexibility, particularly in applications where aesthetics are essential.
High Material and Production Costs
Due to its high performance, PEEK is considerably more expensive than most engineering plastics. Additionally, the cost of high-temperature molding equipment and longer cycle times can contribute to overall higher production costs.
Applications of PEEK Injection Molding
The unique characteristics of PEEK make it suitable for a variety of demanding applications across multiple industries:
Aerospace and Defense
PEEK is widely used in aerospace applications due to its strength-to-weight ratio, flame resistance, and ability to withstand extreme temperatures. Typical applications include:
- Structural Components: Parts that require high strength without added weight.
- Electrical Connectors: High dielectric strength makes PEEK ideal for connectors and insulators.
- Fasteners: Used in high-stress areas to reduce weight without compromising performance.
Automotive
The automotive industry uses PEEK in applications that demand high temperature and wear resistance, especially in engines and exhaust systems. Key applications include:
- Bearing and Wear Components: PEEK’s low friction and wear resistance make it suitable for gears, bushings, and seals.
- Under-the-Hood Components: These parts, such as fuel system parts and engine housings, are exposed to high temperatures and chemical exposure, where PEEK performs exceptionally well.
Medical Devices
PEEK is biocompatible, making it suitable for medical applications such as implants and surgical instruments. It can also be sterilized using various methods, including autoclaving, which is essential for medical environments.
- Implants: Dental implants, spinal implants, and orthopedic devices often use PEEK due to its compatibility with the human body and ability to withstand stress without degrading.
- Surgical Instruments: PEEK’s high strength, lightweight, and stability make it an ideal material for reusable surgical instruments.
Electronics
PEEK’s excellent electrical insulating properties and resistance to heat and chemicals make it a popular choice for electrical and electronic applications.
- Semiconductor Manufacturing: PEEK parts are used in semiconductor manufacturing processes due to their stability at high temperatures and chemical resistance.
- Insulators and Connectors: PEEK is used in connectors, bushings, and other electrical components that must withstand high temperatures and have low dielectric loss.
Advantages of PEEK Injection Molding
While PEEK injection molding can be challenging, its benefits in part performance and longevity make it worthwhile in many applications.
- Long-Lasting Durability: Parts molded from PEEK are highly durable and have a long operational life, reducing replacement costs in the long run.
- Precision and Complexity: Injection molding allows for the production of exact and complex parts with minimal post-processing.
- Consistency in High-Volume Production: Injection molding ensures consistent quality across high volumes, making it ideal for applications where reliability is critical.
- Eco-Friendly and Recyclable: PEEK can be recycled and repurposed, and its longevity often results in less material waste over time.
Future of PEEK Injection Molding
The demand for PEEK injection molding is growing as industries seek high-performance materials that can withstand extreme conditions. With advancements in injection molding technology and material science, PEEK’s applications will likely expand further.
- Automated Molding Processes: Automation in PEEK injection molding could reduce production costs and increase efficiency, making PEEK more accessible.
- Innovative Mold Materials: Developing mold materials that can better resist wear from PEEK could reduce maintenance and enhance mold longevity.
- Enhanced Blends and Additives: Research into PEEK blends with carbon or glass fibers could improve its properties for specific applications.
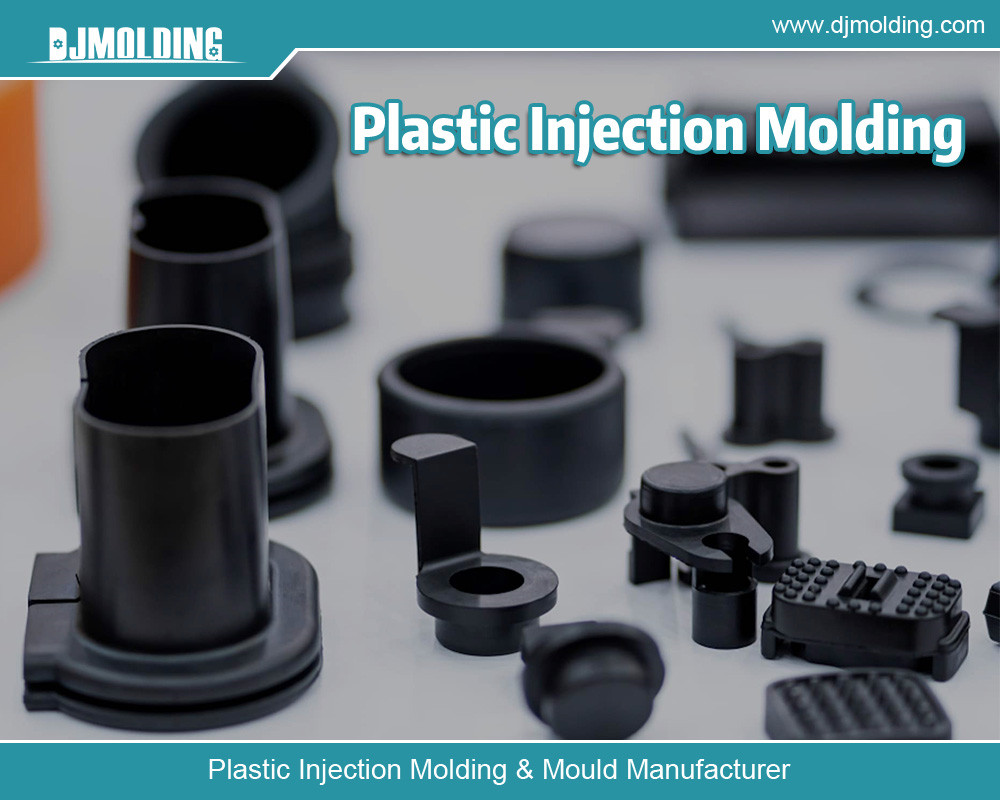
Conclusion
PEEK injection molding offers an effective solution for producing high-performance parts that meet stringent industry standards. Although the process presents unique challenges, such as high-temperature requirements, potential mold wear, and material costs, the resulting components’ strength, heat resistance, and chemical stability make PEEK invaluable across aerospace, automotive, medical, and electronics industries.
As technology and materials evolve, PEEK injection molding will likely become more efficient, expanding the scope of this versatile polymer’s applications and further solidifying its role in high-performance manufacturing.
For more about peek injection molding: a high-performance polymer manufacturing process, you can pay a visit to Djmolding at https://www.djmolding.com/ for more info.