PE Injection Molding: A Comprehensive Guide
PE Injection Molding: A Comprehensive Guide
Polyethylene (PE) injection molding is a widely used manufacturing process that shapes polyethylene materials into various products and components with high precision. PE is a versatile, durable, and cost-effective polymer, making it ideal for producing household goods and complex industrial parts. This article delves into the fundamentals, benefits, techniques, and applications of PE injection molding.
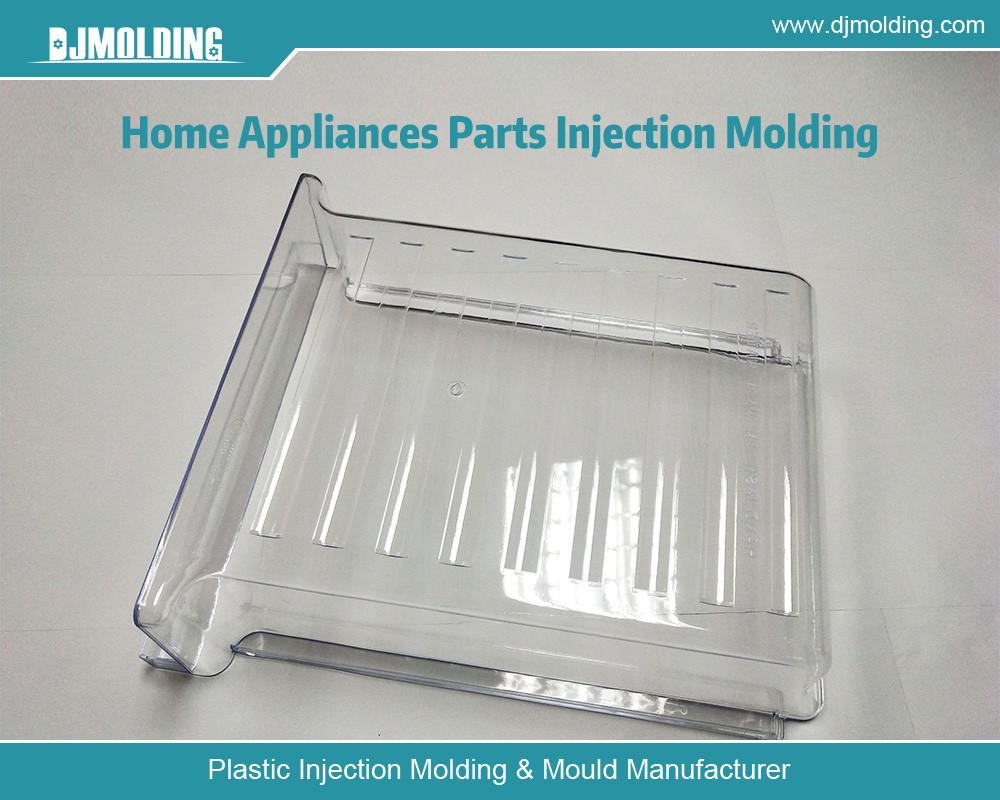
Table of Contents
- Understanding Polyethylene (PE) and Its Types
- The PE Injection Molding Process
- Advantages of PE Injection Molding
- Applications of PE Injection Molding
- Challenges and Considerations in PE Injection Molding
- Future Trends in PE Injection Molding
Understanding Polyethylene (PE) and Its Types
Polyethylene is one of the most commonly used thermoplastic polymers globally, valued for its durability, chemical resistance, and versatility. Composed primarily of ethylene monomers, PE comes in several types, each with unique properties suitable for different applications. The main types of polyethylene used in injection molding are:
Low-Density Polyethylene (LDPE)
LDPE is known for its flexibility, chemical resistance, and transparency. Typical applications include plastic bags, squeeze bottles, and packaging films. However, LDPE is softer and less heat-resistant than other PE types, limiting its use in high-strength applications.
High-Density Polyethylene (HDPE)
HDPE is more rigid, durable, and impact-resistant, making it suitable for heavy-duty products like containers, crates, and pipes. Its higher melting point enhances its resistance to temperature variations.
Linear Low-Density Polyethylene (LLDPE)
LLDPE combines the flexibility of LDPE with improved strength and durability. It is commonly used for films, stretch wraps, and other packaging applications that require resilience.
Ultra-High Molecular Weight Polyethylene (UHMWPE)
UHMWPE is a high-strength, wear-resistant type of polyethylene with a molecular weight significantly higher than standard HDPE. It is ideal for applications demanding high-impact resistance, such as medical implants, ballistic materials, and industrial gears.
Depending on the final product’s required properties, each of these PE types can be used in injection molding.
The PE Injection Molding Process
The PE injection molding process involves several stages that convert raw polyethylene material into a finished product. Here’s a step-by-step overview:
Step 1: Material Preparation
PE granules, often in pellet form, are dried to remove any moisture that could interfere with molding. Additives like colorants or stabilizers may also be mixed into the PE granules to achieve the desired properties.
Step 2: Melting the Material
The dried PE pellets are loaded into the injection molding machine’s hopper. They are then transported to a heated barrel, where they are melted by screw rotation. The screw’s rotation creates friction and heat, further melting the PE material to reach a fluid state suitable for injection.
Step 3: Injection
The molten PE material is injected into a mold cavity at high pressure. The mold is specifically designed to produce a precise shape. The material fills the cavity, taking on its shape, and is held under pressure until it solidifies.
Step 4: Cooling
Once injected, the PE material must cool within the mold. Cooling is crucial because it solidifies the molten material, giving it structural integrity. Cooling rates vary based on the thickness and type of PE material used.
Step 5: Ejection
After sufficient cooling, the mold opens, and the molded part is ejected. Ejection pins may be used to push the part out without damaging it. Once ejected, the mold is ready for the next cycle, making the process highly efficient.
Step 6: Post-Processing
Additional post-processing, such as trimming excess material, polishing, or applying surface treatments, may be needed to achieve the desired finish.
Advantages of PE Injection Molding
PE injection molding is preferred for several reasons, mainly due to the material’s intrinsic properties and the versatility of the injection molding process.
Cost-Effective Production
Polyethylene is relatively inexpensive compared to many other polymers. Additionally, the high production rate of injection molding allows for the mass production of parts, reducing per-unit costs.
Versatility and Flexibility
PE injection molding can be tailored to produce a wide range of products. By adjusting the mold and additives, manufacturers can create products of different shapes, colors, and textures, meeting various industry requirements.
High Durability and Chemical Resistance
PE is known for its robustness and resistance to chemicals, moisture, and impact. Its products are long-lasting and can withstand harsh conditions, making them suitable for various industrial and consumer applications.
Recyclable and Environmentally Friendly
Polyethylene is recyclable, and scrap material from injection molding can often be reprocessed and reused. This reduces waste and contributes to environmentally conscious manufacturing practices.
Precision and Consistency
Injection molding provides high precision and repeatability, ensuring that each part produced meets strict specifications. This is particularly important for industries requiring high accuracy, such as the automotive, medical, and electronics sectors.
Applications of PE Injection Molding
Polyethylene’s flexibility and durability make it suitable for various industry applications. Some of the prominent applications include:
Packaging Industry
PE injection molding is extensively used in packaging to create containers, caps, closures, and bottles. LDPE and HDPE’s flexibility and strength are ideal for rigid and flexible packaging solutions.
Consumer Goods
Many household items, including storage containers, toys, kitchenware, and furniture parts, are produced using PE injection molding. The durability and safety of PE materials make them suitable for everyday use.
Automotive Industry
In the automotive sector, PE injection molding produces fuel tanks, fluid containers, and protective casings. HDPE, in particular, is chosen for automotive parts due to its impact resistance and durability.
Medical Industry
Due to its wear resistance and biocompatibility, UHMWPE is often used in medical applications, such as hip and knee implants. Other PE grades produce medical-grade containers, tubing, and components requiring chemical resistance and durability.
Industrial Applications
Industrial parts, such as pipes, gears, and seals, benefit from PE injection molding due to the material’s strength and resistance to wear. With its superior toughness, UHMWPE is ideal for parts subject to intense abrasion and stress.
Construction
PE injection molding produces fittings, pipes, and protective barriers in construction. HDPE’s corrosion resistance and environmental conditions are ideal for outdoor and underground applications.
Challenges and Considerations in PE Injection Molding
Despite its numerous advantages, PE injection molding presents some challenges and considerations:
Shrinkage
PE materials are prone to shrinkage during cooling, which can affect the final dimensions and shape of the molded part. Mold design and precise temperature control are essential to minimize shrinkage.
Warping
Warping occurs when different areas of the part cool at different rates, causing distortions. Proper mold design and even cooling systems are required to prevent warping.
Material Properties
While PE is resistant to many chemicals, it may not perform well under high temperatures. Polyethylene can also be susceptible to stress cracking, particularly when exposed to certain chemicals or environmental conditions.
Environmental Concerns
Although PE is recyclable, improper disposal and recycling of PE products can contribute to environmental pollution. Manufacturers are encouraged to adopt sustainable practices, such as reusing PE scrap and reducing production waste.
Process Control
The injection molding process requires precise control over temperature, pressure, and cooling time to produce high-quality parts. Variations in these parameters can lead to defects in the final product, so monitoring and quality control are crucial.
Future Trends in PE Injection Molding
The injection molding industry is continually evolving, with new technologies and trends shaping the future of PE molding:
Advanced Mold Design
New technologies, such as 3D printing and simulation software, allow for rapid prototyping and optimization of molds. This helps reduce design errors and achieve faster turnaround times for complex molds.
Sustainable Practices
As environmental concerns increase, more companies focus on reducing waste and using recycled polyethylene. Research into biodegradable additives and improved recycling processes is expected to make PE injection molding more sustainable.
Automation and Industry 4.0
Automation in injection molding, such as using robotic arms for part handling and quality checks, increases efficiency and consistency. Additionally, Industry 4.0 principles, including real-time data monitoring and machine learning, are improving quality control and reducing downtime.
High-Performance Polyethylene (HPP) Materials
Advancements in polymer technology are leading to the development of high-performance PE materials with enhanced mechanical properties, opening up new applications in the aerospace, medical, and defense industries.
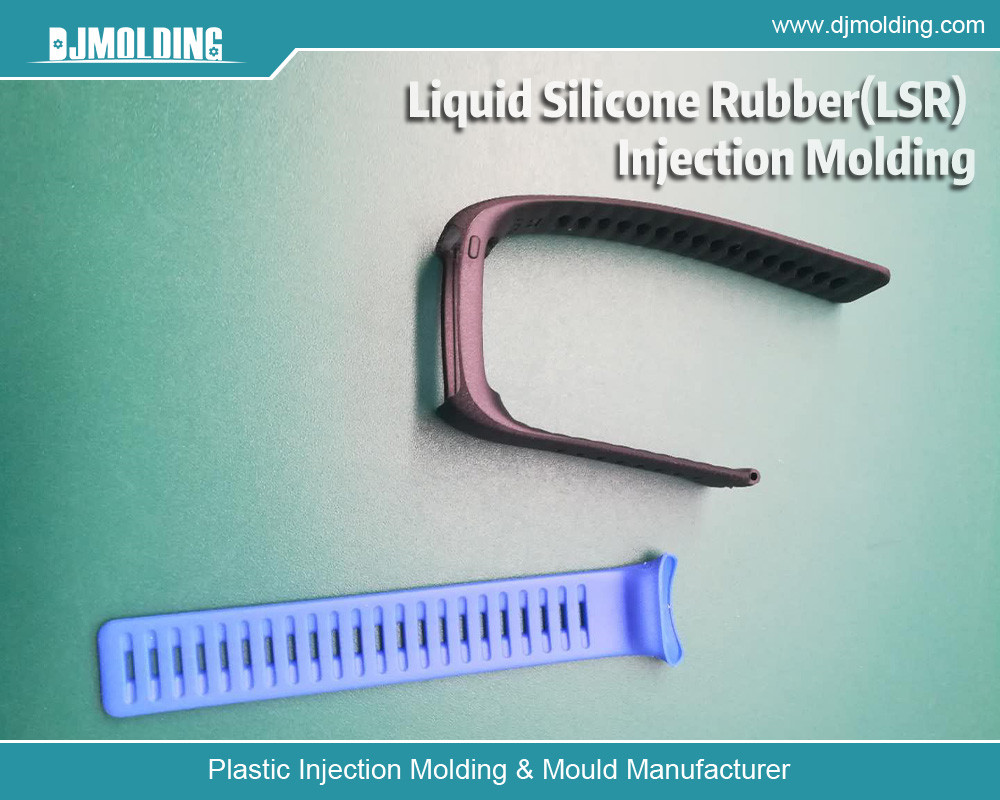
Conclusion
PE injection molding is a robust and versatile manufacturing process that efficiently produces high-quality polyethylene products. The material’s strength, affordability, and chemical resistance make it ideal for various industries, from packaging and consumer goods to automotive and medical applications. However, consideration of shrinkage, warping, and environmental impact should be managed carefully to ensure optimal performance and sustainability.
With ongoing technological advancements and an emphasis on sustainable practices, the future of PE injection molding looks promising. Enhanced mold designs, automated production lines, and high-performance materials will continue to expand the applications of polyethylene, making PE injection molding a mainstay in modern manufacturing.
For more about pe injection molding: a comprehensive guide, you can pay a visit to Djmolding at https://www.djmolding.com/ for more info.