PC Injection Molding: Techniques, Benefits, And Applications
PC Injection Molding: Techniques, Benefits, And Applications
Polycarbonate (PC) injection molding has become an integral part of modern manufacturing due to its unique properties, such as its exceptional impact resistance, optical clarity, and thermal stability. These attributes make the PC an ideal choice for various applications in industries ranging from automotive to medical devices. This article will explore PC injection molding in detail, covering the material’s properties, the injection molding process, and its applications.
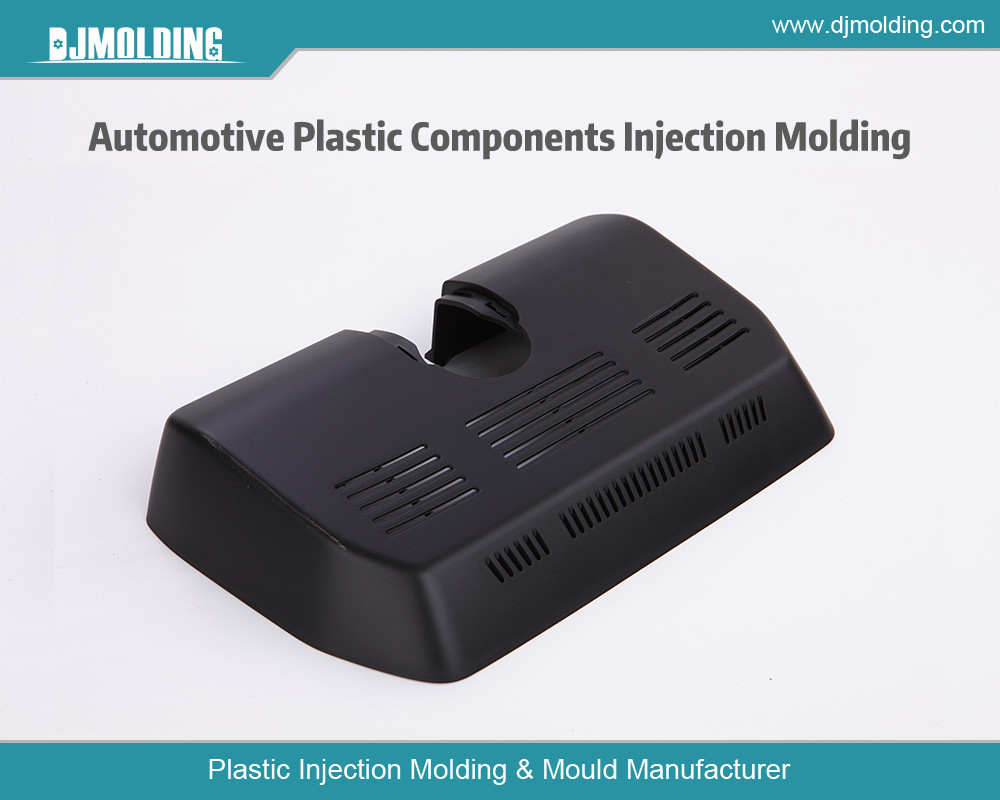
Understanding Polycarbonate (PC)
Polycarbonate is a durable thermoplastic with a wide range of physical properties that make it suitable for applications where toughness, clarity, and high-temperature resistance are crucial. Its unique structure allows for extensive customization in terms of color, finish, and shape, making it one of the most versatile materials for injection molding.
Key Properties of Polycarbonate
Polycarbonate is highly regarded for its unique combination of properties, including:
- Impact Resistance: PC is exceptionally tough and resilient, capable of withstanding high-impact forces without breaking or cracking. This makes it ideal for safety applications like protective equipment and bullet-resistant windows.
- Transparency: The PC has excellent optical clarity, making it suitable for transparent applications like lenses, screens, and covers.
- Heat Resistance: Polycarbonate’s high glass transition temperature ensures that it maintains its strength and dimensional stability at elevated temperatures.
- Electrical Insulation: PCs are good electrical insulators and are valuable in electronics and electrical housings.
- Flame Retardant: Many grades of polycarbonate are inherently flame-resistant, allowing them to meet stringent fire safety standards.
The PC Injection Molding Process
Injection molding is a manufacturing process that allows the mass production of complex shapes and designs by injecting molten material into a mold. When working with polycarbonate, specific process parameters must be considered to ensure quality and durability in the final product.
Injection Molding Equipment
Manufacturers typically use hydraulic or electric injection molding machines to mold polycarbonate. These machines are categorized by clamping force, with higher tonnage machines suitable for larger or thicker PC parts.
Mold Design
Mold design is crucial in PC injection molding as polycarbonate has a high melting point and requires precise temperature control. Here are some key considerations:
- Cooling Systems: A properly designed cooling system is essential to achieve uniform cooling and prevent warping or shrinkage.
- Ventilation: Polycarbonate emits gases during molding, so adequate ventilation in the mold design helps avoid burn marks and defects.
- Gate Design: Direct or tunnel gates are common choices for PC injection molding, depending on the part’s size and wall thickness.
Process Parameters for PC Injection Molding
Optimizing the injection molding process for polycarbonate involves fine-tuning several parameters:
- Temperature Control: PC requires high injection and mold temperatures for proper flow and filling. Melt temperatures typically range from 280°C to 330°C, while mold temperatures are around 80°C to 110°C.
- Injection Pressure and Speed: High injection pressure is essential for PC, as the material is relatively viscous. Faster injection speeds are generally preferred to reduce cooling in the mold.
- Cooling Time: Polycarbonate parts require a carefully controlled cooling cycle to avoid stress marks and ensure dimensional stability.
Benefits of Using PC in Injection Molding
Polycarbonate injection molding offers numerous benefits for applications due to its unique properties. Here are some of the advantages of using PC in injection molding:
Durability and Impact Resistance
PC’s high impact resistance suits parts undergoing mechanical stress or potential impacts. This property is valuable in the automotive, electronics, and construction industries, where parts are subject to frequent use and possible wear and tear.
Transparency and Aesthetic Quality
PC’s transparency is on par with glasses, making it ideal for optical clarity applications, such as eyewear lenses and medical devices. Furthermore, PCs can be colored and customized, providing additional aesthetic options for consumer goods.
Thermal Stability
Due to its high thermal stability, PCs can withstand prolonged exposure to elevated temperatures without warping or losing their strength. This makes them suitable for components exposed to heat, such as lighting fixtures and electronic housings.
Versatility in Design
PC injection molding allows for the production of intricate, complex shapes, including thin-walled parts, that would be difficult to create with other materials. This flexibility makes polycarbonate attractive for designers and engineers seeking lightweight, versatile solutions.
Electrical Insulating Properties
PCs’ insulating properties make them ideal for use in electrical components, protecting sensitive electronics from environmental factors and ensuring user safety.
Applications of PC Injection Molding
The adaptability and performance of PCs have led to its adoption across a wide range of industries. Here are some of the primary applications:
Automotive Industry
In the automotive sector, polycarbonate injection molding is used for:
- Headlamp Covers: The PC’s transparency and impact resistance are ideal for headlamp lenses and covers.
- Instrument Panels: The material’s strength and durability ensure that panels and housings remain intact and reliable.
- Sunroofs and Window Panels: Transparent and resistant to UV rays, polycarbonate panels are often used as a lighter alternative to glass in sunroofs and windows.
Electronics and Electrical Industry
Polycarbonate is widely used in electronics for components such as:
- Switch Covers and Housings: The PC’s insulating properties and flame resistance make it ideal for electrical housings and switch panels.
- Optical Discs: Polycarbonate is used for CDs, DVDs, and Blu-ray discs due to its excellent optical clarity.
- Connectors and Battery Cases: PCs’ high-impact resistance and stability make them suitable for battery cases and connector housings in portable electronic devices.
Medical Devices
In the medical field, polycarbonate injection molding enables the creation of:
- Surgical Instruments: PC’s biocompatibility, transparency, and sterilization ability suit surgical tools.
- Diagnostic Equipment: Transparent PC parts are used in diagnostic equipment housings, where visibility and durability are crucial.
- Drug Delivery Devices: PC is lightweight and durable, so it is often used in drug administration devices such as syringes and inhalers.
Consumer Goods
Polycarbonate is also widely used in consumer products, particularly those requiring transparency and durability:
- Eyewear Lenses: PC’s optical clarity and impact resistance make it a popular choice for lenses in eyeglasses and sunglasses.
- Water Bottles and Food Containers: BPA-free polycarbonate grades are used in reusable water bottles and food containers.
- Sporting Equipment: PC’s durability makes it suitable for protective gear and equipment used in sports and outdoor activities.
Construction Industry
Polycarbonate sheets and molded parts are also popular in construction, where they’re used for:
- Roofing and Skylights: PC’s UV resistance, strength, and transparency make it an ideal material for roofing applications.
- Windows and Barriers: Polycarbonate is lightweight and shatter-resistant, so it is often used in safety windows and barriers in high-traffic areas.
Challenges in PC Injection Molding and How to Overcome Them
Despite the many benefits of polycarbonate, there are challenges to consider in the injection molding process, including high melt temperatures and susceptibility to stress cracking. Here’s how manufacturers can address some of these challenges:
Managing High-Processing Temperatures
One of the primary challenges in molding PCs is the high temperature required for processing. This can stress equipment and molds, potentially leading to increased maintenance. Solution: Use specialized machines designed for high-temperature materials and invest in temperature-resistant molds.
Avoiding Stress Cracking
Polycarbonate is prone to stress cracking if not appropriately molded. High pressure, quick cooling, or incompatible additives can lead to this issue. Solution: Control mold temperature, cooling rate, and injection speed to reduce internal stress within the molded part.
Gas Emission and Venting Issues
Polycarbonate emits gases when heated, which can cause burn marks and surface defects if not properly vented. Solution: Ensure proper mold ventilation and use adequate gate size and position to allow gas to escape from the cavity.
Surface Finish and Aesthetics
PC parts can be prone to surface imperfections due to high viscosity and stress during molding. Solution: Use well-designed molds with smooth surface finishes and optimize injection parameters to ensure uniform filling and cooling.
Future Trends in PC Injection Molding
With continuous advancements in material science and molding technology, the future of polycarbonate injection molding is poised for exciting developments. Some emerging trends include:
- Recyclable and Eco-Friendly PC Blends: Increasing emphasis on sustainability has led to development of recyclable and biodegradable polycarbonate blends for eco-friendly applications.
- Nanotechnology-Enhanced PC: Adding nanomaterials to polycarbonate can improve its strength, scratch resistance, and thermal conductivity, broadening its application potential.
- Advanced Molding Techniques: New injection molding techniques, such as gas-assisted and micro-injection, enable manufacturers to create complex, lightweight parts with superior strength and accuracy.
- Additive Manufacturing Integration: 3D printing technologies are being integrated with traditional injection molding to create hybrid manufacturing processes that are faster and more cost-effective.
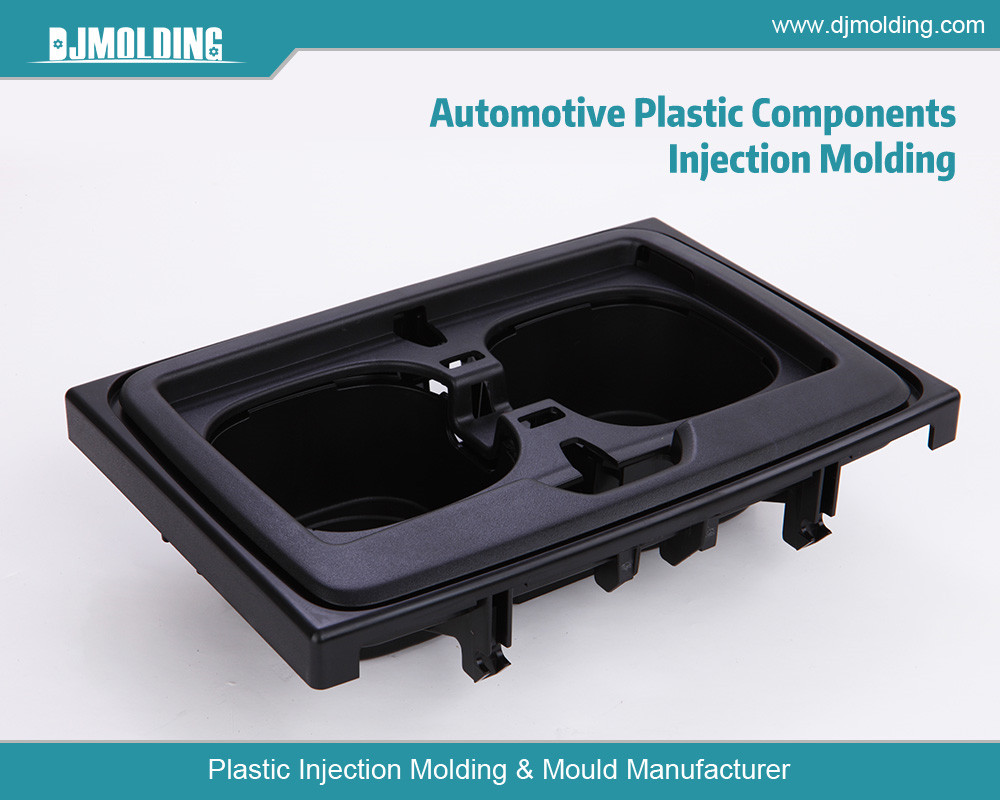
Conclusion
PC injection molding plays a significant role in modern manufacturing, providing industries with versatile, high-quality solutions for complex components. Polycarbonate remains a valuable material in various industries, from its impressive impact resistance and optical clarity to its wide range of applications. As technology advances and new materials are developed, the versatility and functionality of PC injection molding are likely to grow, leading to further innovations in product design and application.
For more about the pc injection molding: techniques, benefits, and applications, you can pay a visit to Djmolding at https://www.djmolding.com/ for more info.