Overmolding vs. Insert Molding: A Complete Guide
Overmolding vs. Insert Molding: A Complete Guide
In plastic manufacturing, two processes stand out for their innovative approach to creating complex and durable products: Overmolding and insert Molding. Both techniques have revolutionized industries ranging from automotive and consumer electronics to medical devices and packaging. By enabling the combination of multiple materials and components into a single part, these processes enhance product functionality, durability, and aesthetic appeal. However, while they may seem similar, Overmolding and insert Molding, each offers unique advantages and applications. This comprehensive guide will explore the differences between Overmolding and insert Molding, examining their processes, benefits, materials, and typical uses. Whether you’re a product designer, engineer, or manufacturer, understanding these distinctions will help you decide which method best suits your project’s needs.
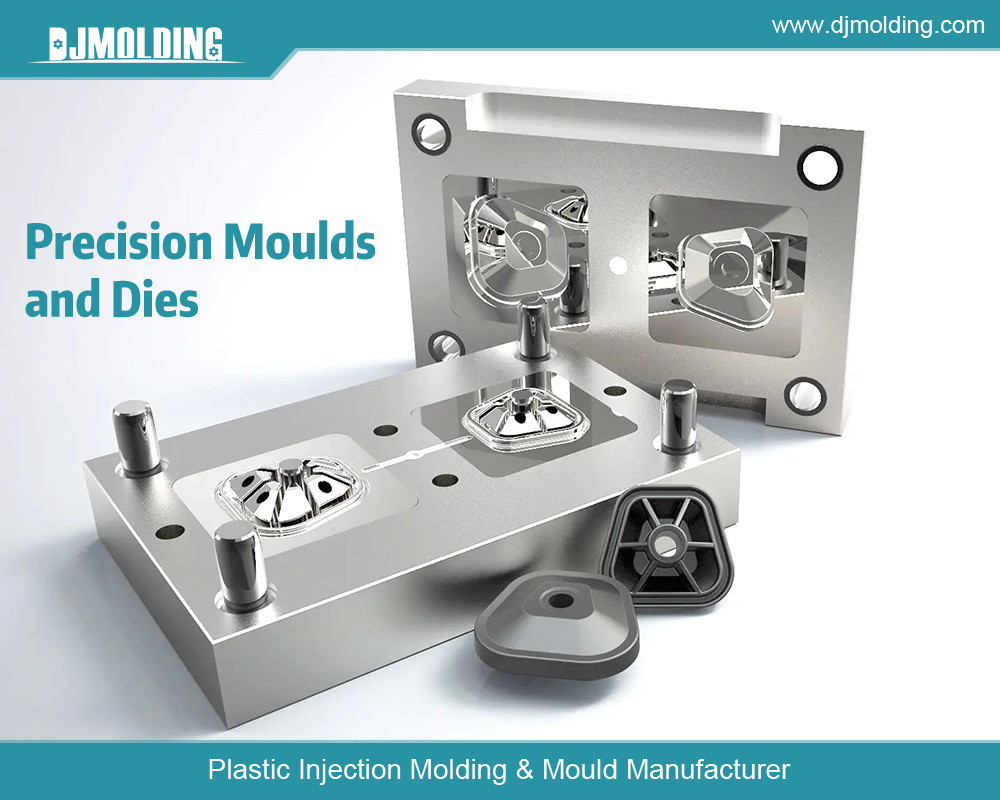
What is Overmolding?
Overmolding is a manufacturing process that involves molding a second material over a substrate or primary part to enhance the functionality and aesthetics of the final product. This highly versatile technique can be used in various industries to produce products with enhanced grip, improved ergonomics, or additional color accents.
How Overmolding Works
- Initial Molding: The process begins by creating the substrate or base part, typically using standard injection molding techniques. Depending on the desired characteristics of the final product, this substrate can be made from a variety of materials, such as metals or plastics.
- Secondary Molding: Once the substrate is prepared, it is placed into an injection mold, where a second material is molded. This secondary material is often a thermoplastic elastomer (TPE), which provides flexibility, grip, and a soft-touch finish.
- Bonding: The key to successful overmolding is achieving a strong bond between the substrate and the overmold material. It is typically accomplished through heat, pressure, and, sometimes, chemical adhesion.
Benefits of Overmolding
- Enhanced Product Functionality: Overmolding can add features like grips, seals, and vibration dampening to products.
- Improved Aesthetics: The process allows for adding colors and textures that enhance the final product’s appearance.
- Cost Efficiency: By combining multiple functions into a single part, overmolding can reduce assembly costs and complexity.
Common Applications of Overmolding
- Consumer Electronics: Adding grips and protective layers to smartphones and remote controls.
- Automotive Components: Enhancing the durability and tactile feel of interior parts like knobs and handles.
- Medical Devices: Providing ergonomic grips and seals for syringes, surgical tools, and diagnostic equipment.
What is Insert Molding?
Insert Molding is a similar but distinct process that involves inserting a pre-formed component into the mold before injecting plastic around it. This method is primarily used to integrate metal components, such as threads and bushings, into plastic parts, thus enhancing the structural integrity and functionality of the product.
How to Insert Molding Works
- Component Placement: The process begins by placing an insert, typically made of metal, ceramic, or another material, into the mold cavity. This insert becomes an integral part of the final product.
- Plastic Injection: Plastic is injected into the mold, encapsulating the insert. The molten plastic fills the cavity and solidifies, bonding with the insert to form a cohesive unit.
- Cooling and Ejection: After the plastic has cooled and solidified, the mold opens, and the finished part is ejected.
Benefits of Insert Molding
- Enhanced Structural Integrity: The process allows for the integration of metal components, providing the product with strength and durability.
- Design Flexibility: Insert Molding enables the creation of complex parts with integrated features, reducing the need for additional assembly steps.
- Material Versatility: The process supports a wide range of materials for the insert and the surrounding plastic, allowing customized solutions.
Common Applications of Insert Molding
- Automotive: Producing gears, bushings, and threaded components with enhanced wear resistance and strength.
- Electronics: Integrating connectors, sockets, and circuit components into plastic housings.
- Medical Devices: Creating durable parts with metal components for surgical tools and diagnostic equipment.
Overmolding vs. Insert Molding: Key Differences
Material Compatibility
- Overmolding: Primarily involves two types of plastic materials. The primary consideration is the chemical compatibility between the substrate and the overmold material to ensure proper adhesion.
- Insert Molding: Often involves combining metal inserts with plastic, requiring careful consideration of thermal expansion rates and bonding mechanisms.
Process Complexity
- Overmolding: Generally requires more complex tooling to accommodate the additional step of adding a second material. This complexity can lead to longer cycle times and higher tooling costs.
- Insert Molding: While it involves placing inserts into the mold, the process is typically more straightforward than Overmolding and can be faster in cycle time.
Design Considerations
- Overmolding: Offers greater flexibility in adding features like soft grips or aesthetic accents. Designers can create intricate shapes and multi-material designs that enhance function and appearance.
- Insert Molding: Focuses on integrating functional components like metal threads or bushings. The design must accommodate the placement and encapsulation of inserts, often prioritizing structural integrity over aesthetics.
Cost Implications
- Overmolding: This may incur higher costs due to more complex tooling and longer cycle times. However, it can reduce overall production costs by eliminating the need for separate assembly steps.
- Insert Molding: Generally offers lower tooling costs and faster production times. Adding metal components to plastic parts can be cost-effective without secondary operations.
Typical Industries and Applications
- Overmolding: Widely used in consumer products, automotive, and medical devices for applications requiring enhanced grip, aesthetics, or additional features.
- Insert Molding: Insert Molding is common in industries like automotive, electronics, and medical devices, where structural integrity and integrated components are critical.
Material Selection in Overmolding and Insert Molding
Material selection is crucial in both Overmolding and insert molding, as it directly affects the final product’s performance, durability, and cost.
Overmolding Material Options
- Thermoplastic Elastomers (TPEs): TPEs are commonly used in Overmolding due to their flexibility, soft-touch feel, and ability to bond with various substrates. They are ideal for creating grips, seals, and vibration-dampening components.
- Polyurethanes: Polyurethanes are often used in Overmolding applications that require a high level of wear resistance. They are known for their excellent abrasion resistance and durability.
- Silicone: Silicone materials are used for Overmolding applications requiring high heat resistance and flexibility, making them suitable for seals and gaskets.
Insert Molding Material Options
- Metals: Steel, brass, and aluminum are commonly used as inserts in insert molding. They provide strength, wear resistance, and electrical conductivity to the final product.
- Ceramics: Ceramic inserts offer excellent thermal resistance and are used in applications requiring high-temperature performance.
- Plastics: Some insert molding applications involve plastic inserts, especially in cases where weight reduction is a priority.
Factors to Consider
- Bonding Compatibility: Ensuring chemical compatibility between materials is crucial for achieving strong adhesion and preventing delamination.
- Thermal Expansion: Matching the thermal expansion rates of materials can prevent warping or stress during temperature changes.
- Mechanical Properties: The selected materials should provide the required mechanical properties, such as strength, flexibility, or impact resistance, for the intended application.
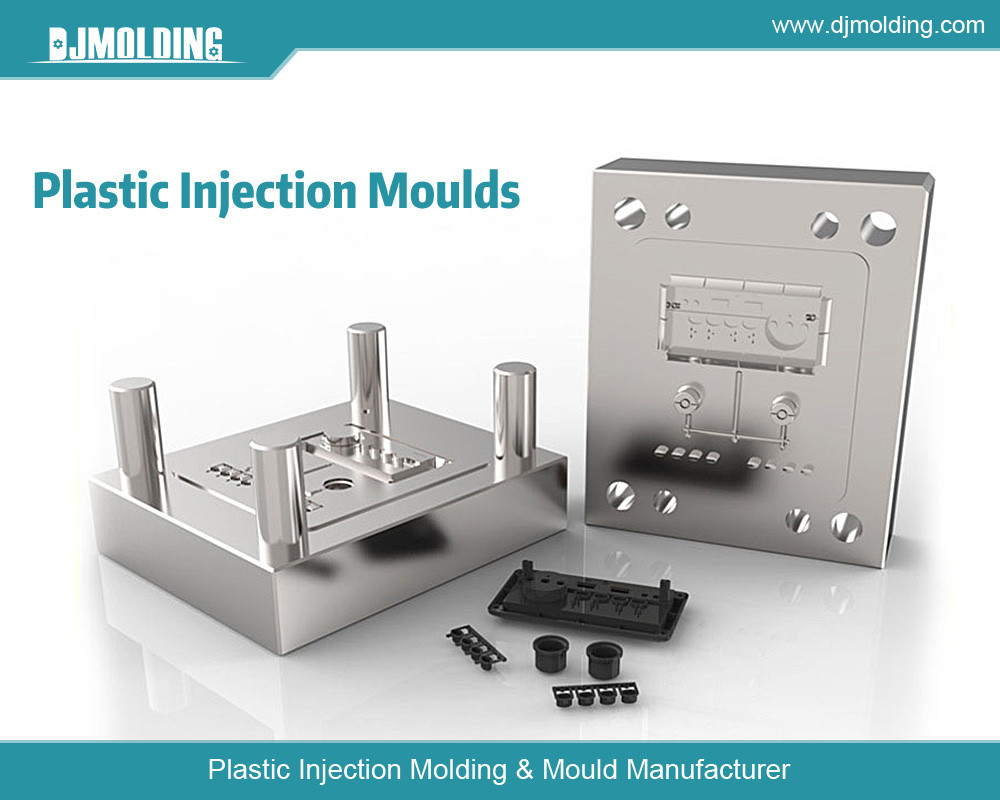
Conclusion
In the dynamic field of plastic manufacturing, both Overmolding and insert Molding have emerged as powerful techniques that enable the creation of complex, high-performance products. By understanding each process’s unique characteristics, benefits, and applications, manufacturers can make informed decisions that enhance product quality, functionality, and cost-effectiveness. Whether the goal is to create ergonomic consumer products with improved aesthetics or durable industrial components with integrated metal features, Overmolding and insert molding offer versatile solutions that can be tailored to meet diverse industry needs. By leveraging these innovative processes, manufacturers can continue to push the boundaries of design and performance, delivering products that exceed customer expectations and drive market success.
For more about overmolding vs. insert molding: a complete guide, you can pay a visit to Djmolding at https://www.djmolding.com/insert-injection-molding/ for more info.