Nylon vs ABS Injection Molding: What’s Their Difference?
Nylon vs ABS Injection Molding: What’s Their Difference?
Injection molding is a prevalent manufacturing process used to create complex and precise parts by injecting molten material into molds. Among the various materials used in injection molding, Nylon, and ABS (Acrylonitrile Butadiene Styrene) are two of the most popular choices due to their distinct properties and applications. This article explores the differences between Nylon and ABS in injection molding, providing insights into their characteristics, applications, advantages, and limitations.
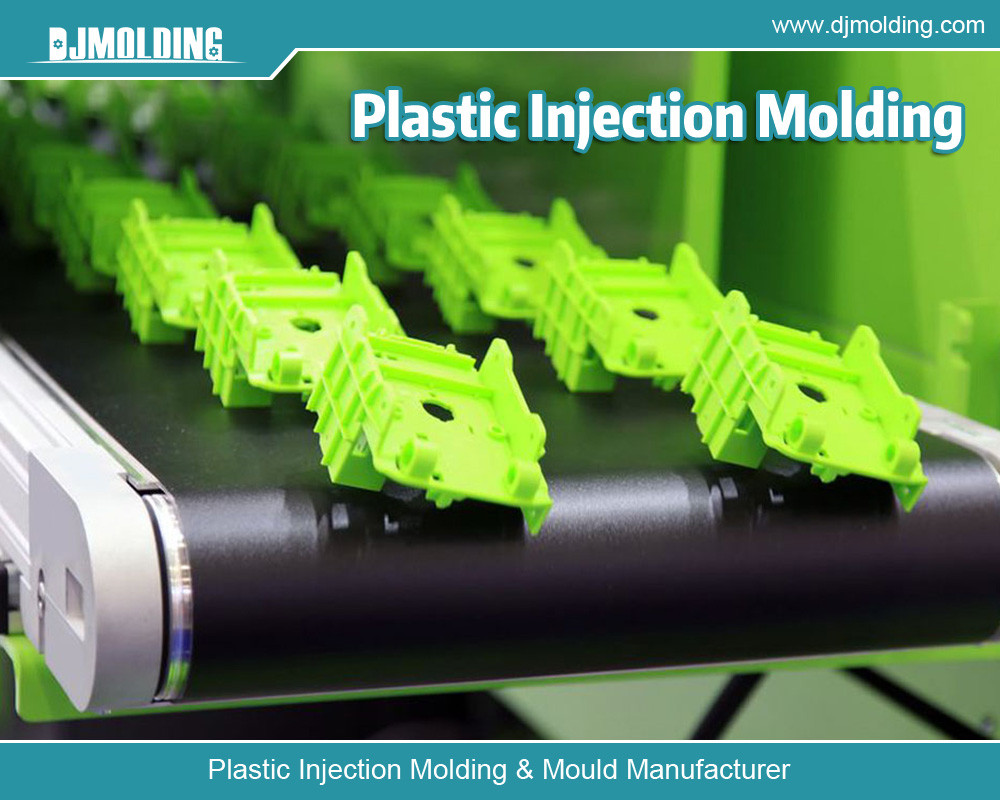
1. Material Properties
1.1 Nylon
Nylon, a polyamide, is a synthetic polymer known for its high strength, durability, and resistance to abrasion. It is commonly used in various industrial applications due to its excellent mechanical properties. Some key characteristics of Nylon include:
- Strength and Durability: Nylon is known for its high tensile strength and impact resistance. It can withstand significant mechanical stress and is highly durable, making it suitable for heavy-duty applications.
- Flexibility: It possesses a certain degree of flexibility and elasticity, which allows it to absorb shocks and resist deformation under stress.
- Chemical Resistance: Nylon offers good resistance to many chemicals, including oils and solvents, although it may be susceptible to hydrolysis (degradation by water) under certain conditions.
- Heat Resistance: Its high melting point allows it to maintain its properties at elevated temperatures.
1.2 ABS
ABS is a thermoplastic polymer combining acrylonitrile, butadiene, and styrene properties. It is widely used in various consumer and industrial applications due to its balance of strength, rigidity, and ease of processing. Critical characteristics of ABS include:
- Impact Resistance: ABS is known for its excellent impact resistance, making it suitable for applications requiring high durability against physical stress.
- Rigidity: It provides a good balance between rigidity and toughness, which makes it ideal for parts that need to retain their shape under stress.
- Chemical Resistance: ABS has moderate chemical resistance and can withstand exposure to certain acids, bases, and oils.
- Heat Resistance: Although ABS has a lower melting point than Nylon, it offers reasonable heat resistance for many applications.
2. Injection Molding Process
2.1 Nylon Injection Molding
Nylon injection molding involves melting Nylon pellets and injecting the molten material into a mold cavity to form a solid part. The process requires precise control over temperature and pressure to achieve optimal results. Critical aspects of Nylon injection molding include:
- Drying: Nylon is hygroscopic, meaning it absorbs moisture from the environment. Before molding, Nylon pellets must be dried to prevent defects such as bubbles or weak spots in the final product.
- Processing Temperature: The processing temperature for Nylon is typically higher than that for ABS. This requires specialized equipment capable of maintaining the required temperature ranges.
- Mold Design: The mold design for Nylon parts must account for the material’s tendency to shrink as it cools. Proper venting and cooling channels are essential to ensure uniform cooling and minimize warping.
2.2 ABS Injection Molding
ABS injection molding is a well-established process that involves melting ABS pellets and injecting them into a mold cavity. The process is generally more straightforward compared to Nylon, with several notable features:
- Moisture Sensitivity: ABS is less moisture-sensitive than Nylon, simplifying the pre-molding preparation process.
- Processing Temperature: ABS is processed at lower temperatures than Nylon, which can reduce energy consumption and simplify the molding equipment.
- Mold Design: ABS has lower shrinkage compared to Nylon, which can result in fewer issues related to dimensional accuracy and warping.
3. Applications
3.1 Nylon Applications
Due to its superior mechanical properties, Nylon is used in various demanding applications, including:
- Automotive Parts: Due to its strength and durability, Nylon is commonly used for components such as gears, bearings, and fuel system parts.
- Industrial Equipment: Components such as conveyor belts, rollers, and machine parts benefit from Nylon’s abrasion resistance and mechanical strength.
- Consumer Goods: Nylon is often used for zippers, sporting goods, and various household products due to its toughness and flexibility.
3.2 ABS Applications
ABS is favored for applications that require a good balance of strength, impact resistance, and ease of processing, including:
- Consumer Electronics: ABS is used for housings and enclosures of electronic devices due to its impact resistance and aesthetic finish.
- Automotive Components: ABS is often used for parts such as dashboards, trim pieces, and bumpers because of its rigidity and ease of molding.
- Toys and Household Products: ABS is commonly used to manufacture toys and various household items due to its strength and ability to be easily colored and finished.
4. Advantages and Limitations
4.1 Advantages of Nylon
- High Strength and Durability: Nylon’s mechanical properties make it suitable for applications requiring high strength and resistance to wear.
- Flexibility and Elasticity: Its ability to absorb shock and resist deformation under stress adds to its versatility.
- Chemical Resistance: Nylon’s resistance to many chemicals enhances its utility in various industrial environments.
4.2 Limitations of Nylon
- Moisture Absorption: Nylon’s hygroscopic nature requires careful handling and drying to avoid processing issues.
- Cost: Nylon is generally more expensive than ABS, which can impact the overall cost of production.
4.3 Advantages of ABS
- Ease of Processing: ABS’s lower processing temperature and reduced moisture sensitivity make it easier to mold and handle.
- Good Impact Resistance: ABS’s ability to withstand physical stress makes it suitable for consumer and industrial products.
- Cost-Effective: ABS is generally less expensive than Nylon, which can lower production costs.
4.4 Limitations of ABS
- Lower Heat Resistance: ABS’s heat resistance is lower than Nylon’s, which may limit its use in high-temperature applications.
- Chemical Resistance: ABS has moderate chemical resistance, which may not be sufficient for all industrial applications.
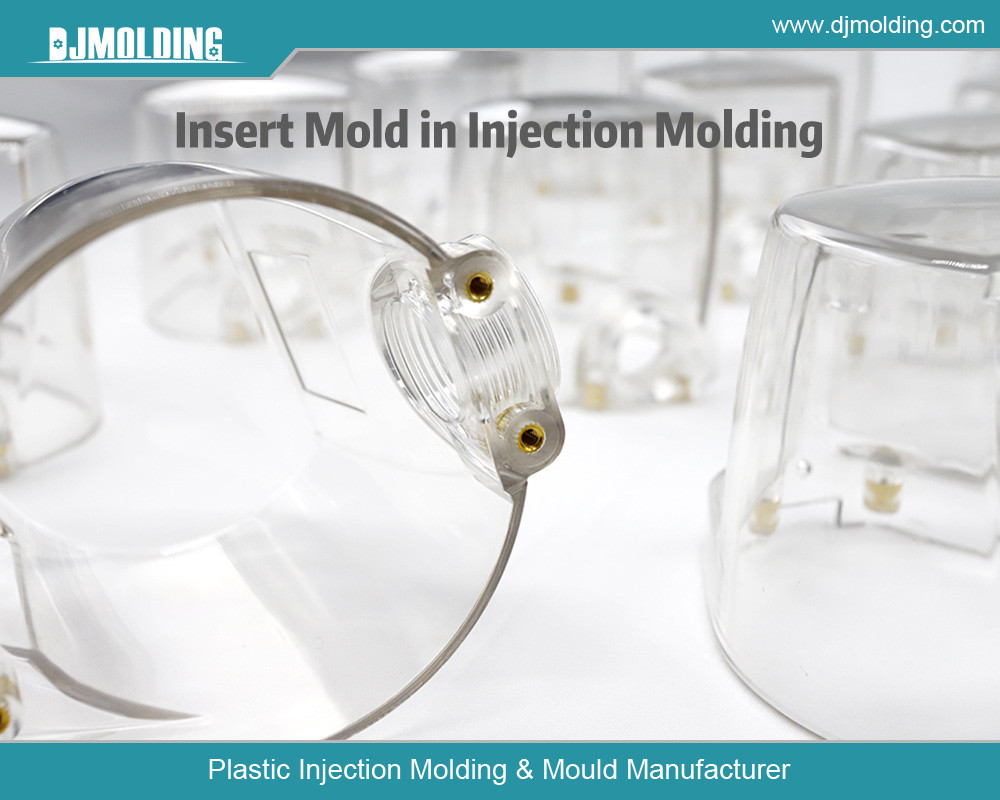
Conclusion
In summary, Nylon and ABS are both valuable materials in the world of injection molding, each with its properties and applications. Nylon excels in applications requiring high strength, durability, and chemical resistance but requires careful handling due to its moisture sensitivity and higher cost. However, ABS offers ease of processing, good impact resistance, and cost-effectiveness, though it may not match Nylon’s performance in high-temperature or highly demanding environments.
Understanding the differences between these materials is crucial for selecting the suitable material for a specific application. By evaluating mechanical properties, processing requirements, and cost, manufacturers can make informed decisions to optimize their injection molding processes and achieve the desired performance in their end products.
For more about nylon vs abs injection molding: what’s their difference, you can pay a visit to Djmolding at https://www.djmolding.com/complete-guide-to-nylon-plastic-injection-molding-service/ for more info.