Maximizing Efficiency And Quality With High Volume Injection Molding For High Volume Manufacturing Companies
Maximizing Efficiency And Quality With High Volume Injection Molding For High Volume Manufacturing Companies
Injection molding plays a crucial role in the manufacturing industry, allowing for the mass production of high-quality plastic parts. As companies strive to meet increasing demand and scale their production, the challenges of high volume manufacturing become apparent, and this is where high volume injection molding comes into play as a solution. In this blog post, we will delve into the fundamentals of high volume injection molding, explore the considerations to keep in mind, discuss essential techniques and best practices, and outline the advantages of adopting this process.
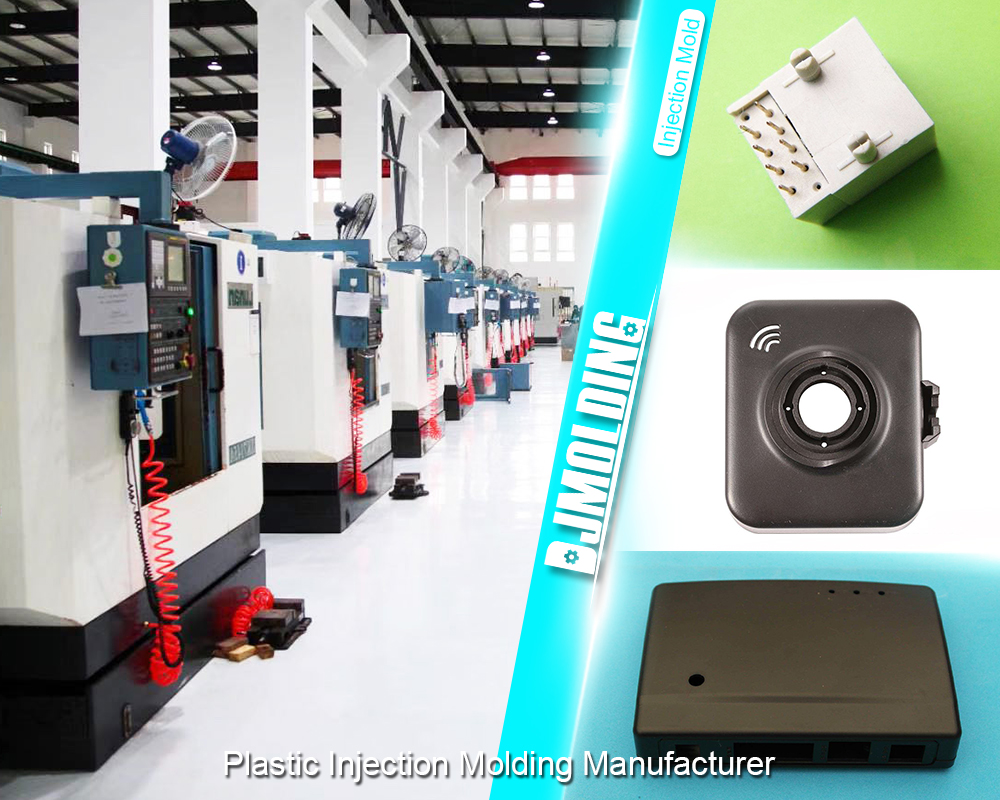
The Basics of High Volume Injection Molding
High volume injection molding is a specialized manufacturing process that enables the production of many plastic parts within a short timeframe. This process distinguishes itself from traditional injection molding by focusing on efficiency and high production volumes. Understanding the key components of high volume injection molding is crucial to harnessing its potential.
- Molds: In high volume injection molding, manufacturers design molds to create multiple identical parts simultaneously. Multi-cavity molds feature several cavities, allowing for increased productivity and efficiency. Manufacturers can significantly accelerate production rates by producing various factors in each cycle.
- Injection Machines: High volume injection molding necessitates using robust and powerful injection machines. These machines can inject molten plastic into the mold cavity at high pressure and speed. Their larger size and increased capabilities enable the efficient production of large parts.
- Materials: Selecting the appropriate materials for high volume injection molding is vital. The chosen materials should possess the necessary properties to produce high-quality parts consistently. Factors such as durability, strength, and stability are critical considerations for material selection.
Benefits of High Volume Production
High volume production through injection molding offers numerous advantages for manufacturers seeking to optimize their operations and achieve efficient and cost-effective production. Let’s explore the key benefits that make high volume production an attractive choice:
Cost-effectiveness
- Economies of Scale: High volume production allows manufacturers to use economies of scale. The cost per unit decreases significantly by producing many parts in a single production run. This reduction attributes to spreading fixed costs, such as tooling and setup expenses, over more significant factors.
- Reduced Labor Costs: High volume production minimizes labor costs per part. With increased automation and efficient processes, manufacturers can streamline production, reducing the need for extensive manual labor. Automated systems and robotics handle parts removal, quality inspection, and packaging, optimizing efficiency and lowering labor expenses.
Scalability
- Meeting Market Demand: High volume production enables manufacturers to meet increasing market demands promptly. Companies can respond effectively to growing customer needs by scaling production, avoiding stock shortages, and capturing market opportunities. This scalability provides a competitive edge and supports business growth.
- Flexibility and Adaptability: With high volume production capabilities, manufacturers can adjust production volumes quickly based on market dynamics. They can ramp up or scale down production in response to fluctuations in demand, reducing lead times and enhancing customer satisfaction.
Consistent Quality and Precision
- Repeatable Processes: High volume production processes, such as injection molding, offer precise control and repeatability. Manufacturers can maintain consistent part quality and dimensional accuracy with automated systems, optimized parameters, and advanced monitoring technologies. This consistency is crucial, particularly for industries with stringent quality requirements.
- Minimized Variations: The precise control provided by high volume production processes minimizes variations in part characteristics. Manufacturers can reduce defects, rejects, and rework by ensuring consistent material distribution, cycle times, and operating parameters. Improving product reliability results in higher customer satisfaction.
Faster Time-to-Market
- Accelerated Production: High volume production allows manufacturers to produce many parts in a shorter timeframe. This accelerated production rate results in faster time-to-market for new products. Manufacturers can capitalize on market opportunities promptly, gain a competitive advantage, and increase their market share.
- Agile Product Development: High volume production processes support agile product development cycles. Manufacturers can quickly iterate and refine designs, conduct rapid prototyping, and perform market testing. This agility enables companies to respond more effectively to customer feedback and evolving market trends.
Enhanced Customer Satisfaction
- Timely Delivery: High volume production ensures timely delivery of products to customers. By meeting demand promptly, manufacturers can avoid backorders, minimize lead times, and build customer trust.
- Consistent Quality: The consistent quality achieved through high volume production processes enhances customer satisfaction. Customers rely on receiving products that meet their expectations consistently, with minimal variations and defects. Consistent quality leads to higher customer loyalty, a positive brand reputation, and increased market share.
- Considerations for High Volume Injection Molding: Specific references should be considered throughout the manufacturing process to fully leverage the benefits of high volume injection molding.
- Mold Design: Careful attention to mold design is essential to optimize production efficiency and part quality. Evaluating factors such as part geometry, gate design, and cooling system integration ensures consistent and precise part formation.
- Material Selection: Choosing the suitable material is critical for successful high volume injection molding. One must consider material properties, flow characteristics, and cost-effectiveness to achieve the desired part quality and performance.
- Process Optimization: Process optimization is crucial in maximizing efficiency and productivity. Techniques like cycle time reduction, automated part removal, and optimized machine settings contributed to streamlined production and reduced manufacturing costs.
- Strategies and Best Practices: Several techniques and best practices can further enhance the efficiency and quality of high volume injection molding.
- Multi-Cavity Molds: Utilizing multi-cavity molds enables the simultaneous production of multiple parts, significantly increasing productivity and reducing cycle times. This approach optimizes machine utilization and minimizes idle time.
- Hot Runner Systems: Hot runner systems are commonly employed in high volume injection molding to eliminate the need for runners and reduce material waste. These systems maintain the plastic material molten, allowing for precise control and faster cycle times.
- Automation and Robotics: Automation plays a vital role in high volume injection molding by streamlining the production process. Robotic systems can handle parts removal, quality inspection, and packaging, reducing labor costs and improving efficiency. Automated processes also minimize the risk of errors and ensure consistency in part production.
- Real-time Monitoring and Data Analysis: Implementing real-time monitoring systems and data analysis tools provides valuable insights into the production process. Manufacturers can identify potential issues and make data-driven adjustments to optimize performance and quality by monitoring key parameters such as temperature, pressure, and cycle times.
- Advantages of High Volume Injection Molding: High volume injection molding offers several benefits that contribute to the success and competitiveness of manufacturing operations.
- Cost Advantages and Economies of Scale: Producing large parts in a single production run reduces the cost per unit. Manufacturers can save and improve profitability by spreading fixed costs over more features.
- Consistent Quality and Precision: High volume injection molding ensures consistent part quality and dimensional accuracy. The precise control provided by automated processes and optimized parameters leads to minimal variations in part characteristics, meeting stringent quality requirements.
- Faster Time-to-Market: Efficiently producing large parts enables faster time-to-market for new products. This competitive advantage allows manufacturers to meet market demand promptly, stay ahead of competitors, and seize business opportunities.
- Increased Customer Satisfaction: High volume injection molding enables manufacturers to deliver products on time, consistently meeting customer demand. Producing high-quality parts with minimal defects enhances customer satisfaction and strengthens business relationships.
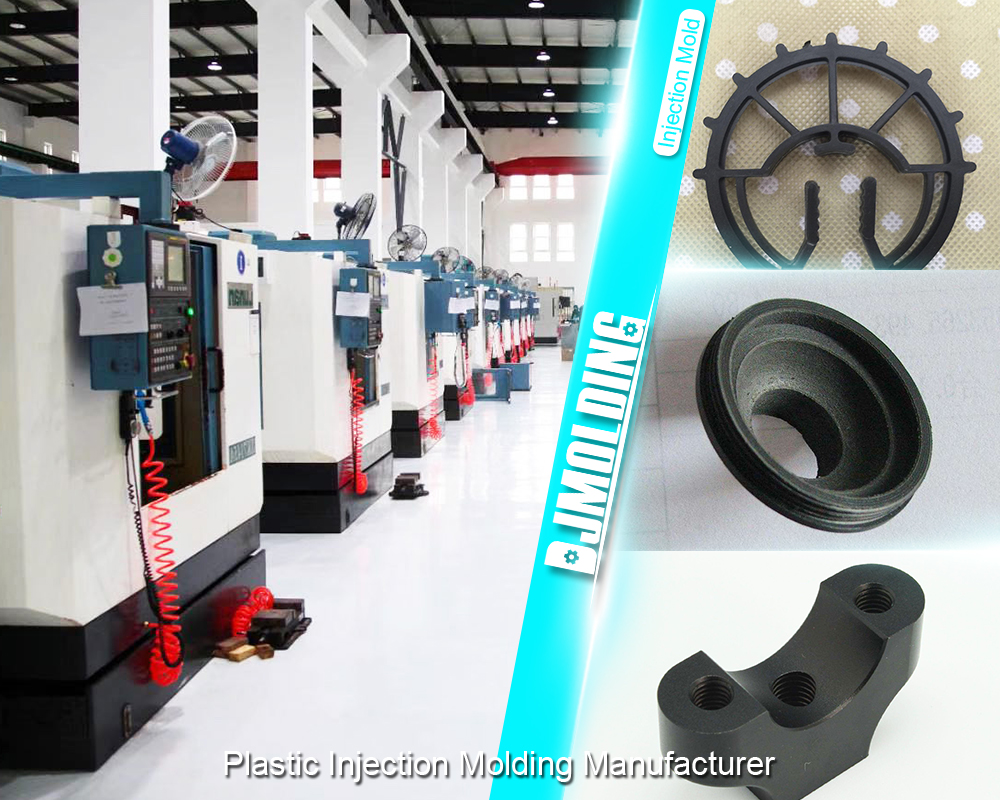
CONCLUSION
High volume injection molding offers a cost-effective solution for manufacturers aiming to maximize production efficiency and maintain high product quality. Companies can optimize their manufacturing operations by understanding the basics of this process, considering key factors, implementing appropriate techniques and best practices, and harnessing its numerous advantages. High volume injection molding empowers manufacturers to scale production, reduce costs, achieve consistent quality, and meet market demands effectively. As the manufacturing landscape continues to evolve, exploring and adopting high volume injection molding can pave the way for sustainable growth and success in the industry.
For more maximizing efficiency and quality with high volume injection molding for high volume manufacturing companies,you can pay a visit to Djmolding at https://www.djmolding.com/high-volume-injection-molding/ for more info.