Magnet Injection Molding: Revolutionizing the Manufacturing Process
Magnet Injection Molding: Revolutionizing the Manufacturing Process
Magnet injection molding is an innovative manufacturing technique that combines traditional injection molding with the incorporation of magnetic components. This process is increasingly being adopted in various industries, including automotive, electronics, and consumer goods, due to its ability to produce high-quality, precise components with integrated magnetic properties. This article will explore the fundamental principles of magnet injection molding, its benefits, applications, and the challenges associated with this advanced technique.
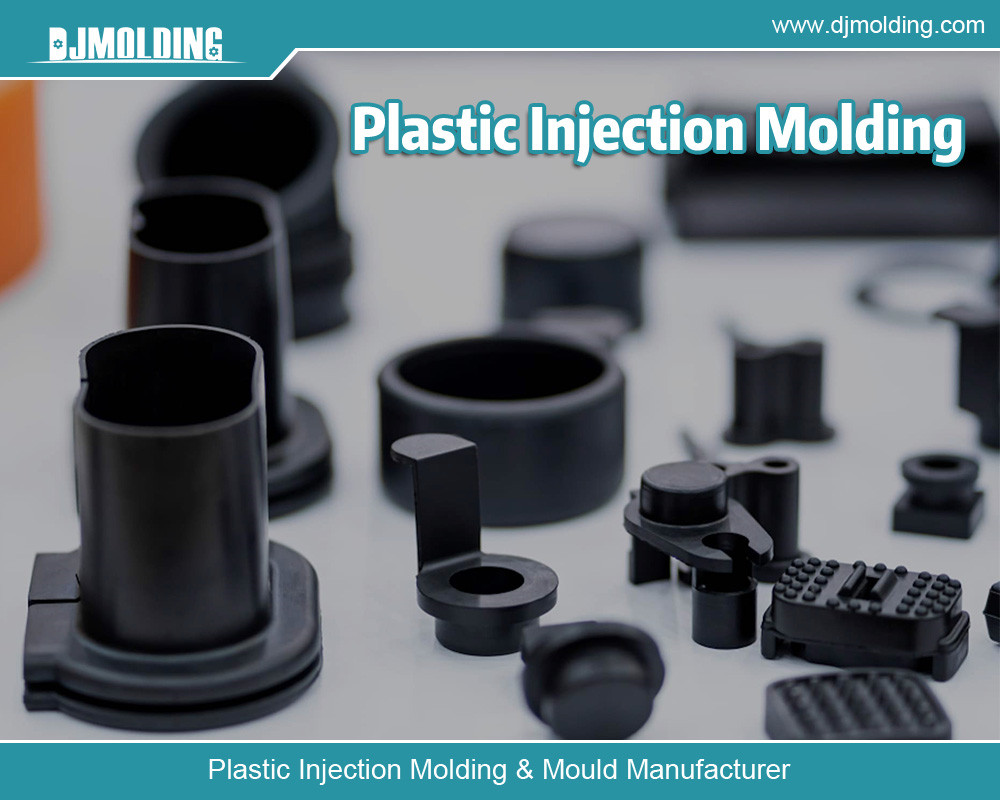
Understanding Magnet Injection Molding
What is Magnet Injection Molding?
Magnet injection molding is a specialized form of injection molding that involves injecting a molten polymer material mixed with magnetic powder into a mold. The process enables the production of parts that not only have structural integrity but also possess inherent magnetic properties. This dual functionality benefits applications where components must simultaneously perform mechanical and magnetic functions.
The Process of Magnet Injection Molding
- Material Selection: The first step involves selecting the appropriate polymer matrix and magnetic materials. Commonly used polymers include thermoplastics such as nylon, polycarbonate, and polypropylene. Magnetic powders may include ferrites, rare earth magnets, or metal powders.
- Compounding: The polymer and magnetic powder are compounded to create a uniform mixture. This step ensures the magnetic properties are evenly distributed throughout the final product.
- Injection Molding: The compounded material is heated until it reaches a molten state and injected into a pre-heated mold. The mold is designed to shape the component and often incorporates features that allow for the precise placement of magnetic elements.
- Cooling and Ejection: Once the molten material fills the mold cavity, it is cooled to solidify. After cooling, the mold is opened, and the finished component is ejected.
- Post-Processing: Some applications may require additional finishing steps, such as surface treatment, machining, or assembly, to meet specific performance criteria.
Types of Magnetic Materials Used
- Ferrites: Commonly used for their low cost and good magnetic properties. Ferrites are often used in applications requiring lower magnetic strength.
- Rare Earth Magnets: Known for their high magnetic strength, rare earth magnets such as neodymium are used in applications that demand compact and powerful magnetic fields.
- Metal Powders: Steel or iron powders can be added to enhance the final product’s magnetic properties and mechanical strength.
Advantages of Magnet Injection Molding
Enhanced Design Flexibility
- Integration of Functions: Magnet injection molding allows for creating components that serve multiple purposes, reducing the need for assembly and minimizing the number of parts required in a product.
- Complex Geometries: The process enables the production of intricate shapes and designs that may be challenging to achieve with traditional manufacturing methods.
Improved Production Efficiency
- Reduced Cycle Times: Magnet injection molding can significantly decrease production cycle times compared to traditional methods, leading to faster product-to-market time.
- Less Waste: The precise control over the material injection minimizes scrap and waste, making the process more sustainable.
Cost-Effectiveness
- Lower Material Costs: By combining multiple functions into a single component, manufacturers can reduce overall material costs.
- Reduced Labor Costs: Fewer parts mean less assembly time and lower labor costs, contributing to overall cost savings.
Applications of Magnet Injection Molding
Automotive Industry
- Sensors and Actuators: Magnet injection molding is widely used to create components such as sensors and actuators, which require precise magnetic properties for optimal performance.
- Magnetic Latches: Components like magnetic latches and closures benefit from the durability and strength of magnet injection molding.
Consumer Electronics
- Magnetic Connectors: This technology produces magnetic connectors and charging systems, enhancing user convenience and device performance.
- Speaker Components: Many consumer electronic devices, including speakers and headphones, utilize magnet injection molding to create lightweight and efficient magnetic assemblies.
Medical Devices
- Magnetic Drug Delivery Systems: Innovative medical applications involve using magnet injection molding to create components for targeted drug delivery systems.
- Diagnostic Equipment: Magnetic components in diagnostic devices, such as MRI machines, can be produced using this method for improved precision and functionality.
Challenges in Magnet Injection Molding
Material Compatibility
- Magnetic Powder Distribution: Achieving a uniform distribution of magnetic powder within the polymer matrix can be challenging, impacting the component’s final magnetic properties.
- Polymer-Magnetic Interaction: The interaction between the polymer and magnetic materials can affect the final product’s mechanical properties, necessitating careful selection and testing.
Process Complexity
- Mold Design: Designing molds that can accommodate the unique requirements of magnetic components can be more complex than traditional molds, requiring specialized knowledge and expertise.
- Quality Control: Ensuring consistent quality and performance across all produced components can be challenging, mainly when dealing with multiple materials.
Production Costs
- Initial Investment: The cost of equipment and molds for magnet injection molding can be higher than traditional injection molding, potentially impacting initial investment decisions.
- Material Costs: While combining functions can save costs in the long run, the initial costs of high-quality magnetic materials may still be a barrier for some manufacturers.
Future Trends in Magnet Injection Molding
Advancements in Materials
- Innovative Materials: Ongoing research is focused on developing new innovative materials that can provide enhanced magnetic properties and additional functionalities, such as shape memory effects.
- Biodegradable Polymers: The rise of sustainable manufacturing practices has led to the exploration of biodegradable polymers that can be used in magnet injection molding without compromising performance.
Integration with Automation
- Industry 4.0: Incorporating automation and data analytics in magnet injection molding processes can enhance efficiency, reduce errors, and streamline production workflows.
- Robotics in Manufacturing: Robotic systems for handling and processing materials can improve precision and reduce labor costs in magnet injection molding operations.
Broader Applications
- Renewable Energy: The potential use of magnet injection molding in renewable energy technologies, such as wind turbines and electric vehicles, could drive demand for more efficient and powerful magnetic components.
- Consumer Products: The trend towards miniaturization and multifunctionality in consumer products will likely increase the adoption of magnet injection molding for innovative applications.
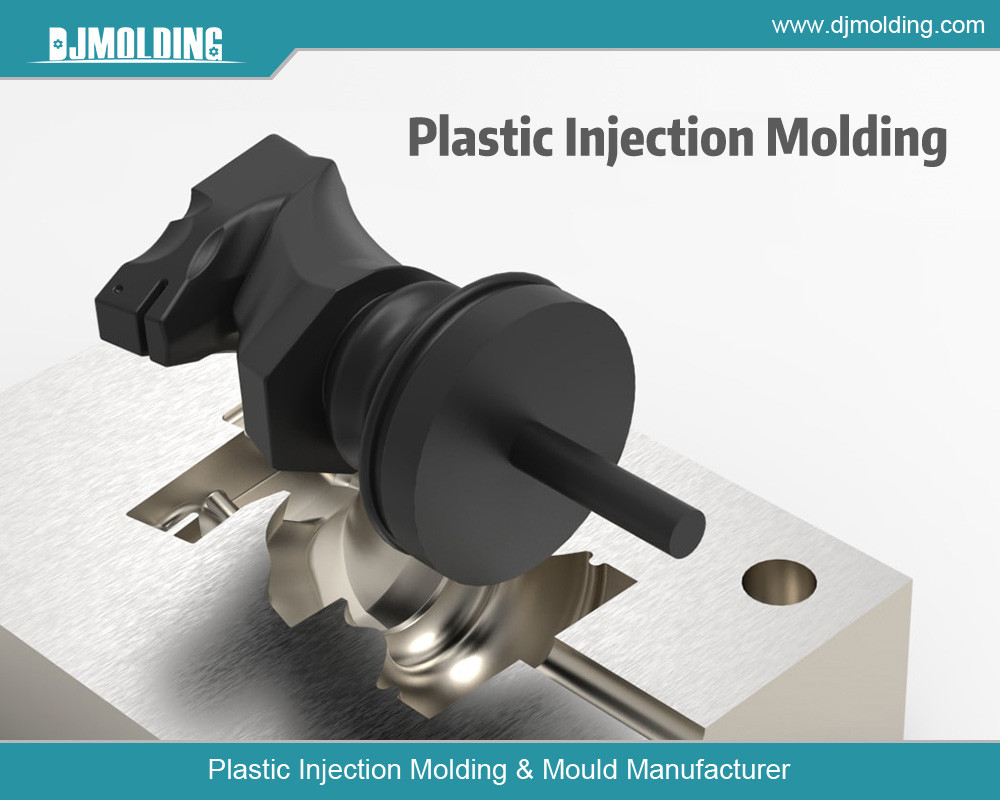
Conclusion
Magnet injection molding is poised to transform the manufacturing landscape by enabling the production of highly functional components with integrated magnetic properties. With its numerous advantages, including enhanced design flexibility, improved production efficiency, and cost-effectiveness, this technology is gaining traction across various industries. Despite challenges related to material compatibility, process complexity, and production costs, ongoing advancements in materials and automation promise a bright future for magnet injection molding. As industries continue to explore innovative applications and sustainable practices, magnet injection molding is likely to play a crucial role in shaping the future of manufacturing.
For more about the magnet injection molding: revolutionizing the manufacturing process, you can pay a visit to Djmolding at https://www.djmolding.com/ for more info.