Low Volume Injection Molding: A Cost-Effective Solution For Low Volume Rapid Prototyping Injection Molding
Low Volume Injection Molding: A Cost-Effective Solution For Low Volume Rapid Prototyping Injection Molding
In today’s fast-paced manufacturing industry, prototyping is a crucial step in the product development process. However, traditional injection molding can be expensive, especially for small volume production runs. This is where low-volume injection molding comes in as a cost-effective solution for prototyping. In this blog post, we’ll delve into the advantages of low volume injection molding and why it’s great for companies looking to reduce costs without sacrificing quality.
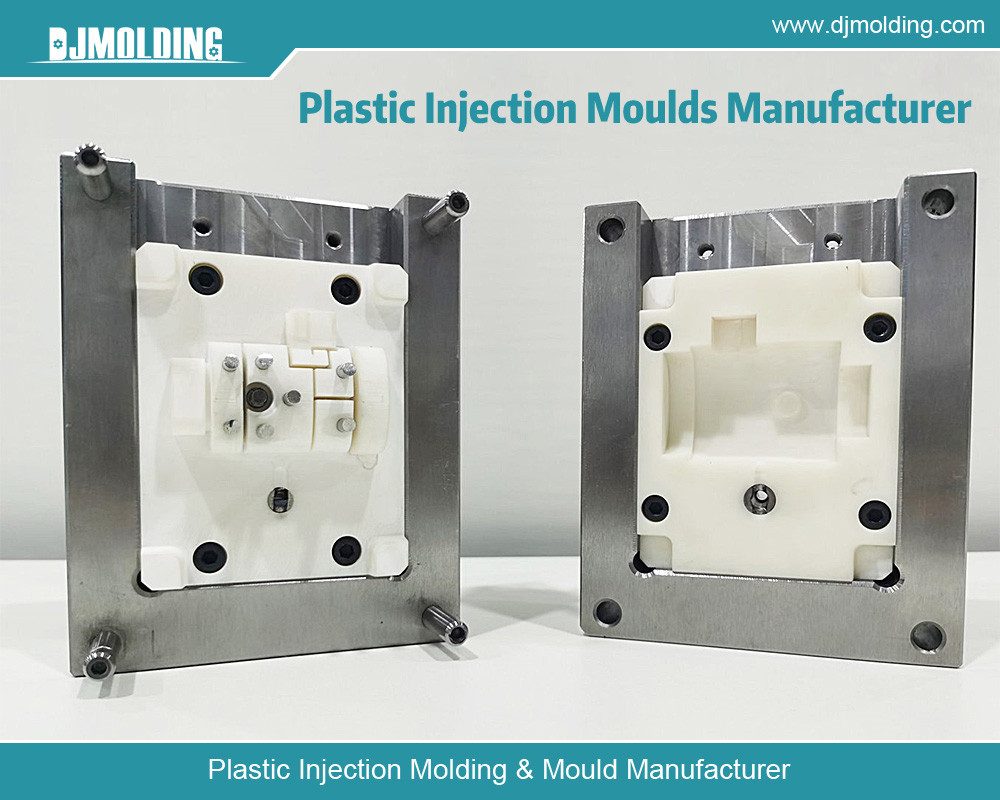
Benefits of Low-Volume Injection Molding for Prototyping
Low-volume molding offers several benefits for prototyping, including cost-effectiveness, faster turnaround time, high-quality parts, and the ability to test and refine designs. It is an ideal solution for small to medium-sized production runs, as it allows designers to produce parts quickly and efficiently.
One of the main benefits of low-volume injection molding is cost-effectiveness. It is a more affordable solution compared to traditional prototyping methods such as CNC machining or 3D printing. Low volume injection molding allows designers to produce parts at a lower cost per unit, making it an ideal solution for small production runs.
Another benefit of low volume molding is faster turnaround time. The process is relatively quick, and parts can be produced in a matter of days. This is a significant advantage for designers who need to test and refine their designs quickly.
Low-volume injection molding also produces high-quality parts. The process allows for tight tolerances and precise dimensions, resulting in parts that are accurate and consistent. This is essential for designers who need to produce parts that meet specific requirements.
Finally, low volume molding allows designers to test and refine their designs. The process allows for the production of small quantities of parts, which can be used for testing and validation. This is an essential part of the product development process, as it allows designers to identify and address any issues before mass production.
How Low-Volume Molding Works
Low-volume injection molding is a specialized process that is used to produce small quantities of plastic parts. This process involves the use of an injection molding machine, which melts plastic pellets and injects them into a mold. Once the mold is cooled, the part is ejected. It involves injecting molten plastic into a mold cavity under high pressure, which then solidifies to form the desired part.
The injection molding machine is a complex piece of equipment that consists of several components, including the hopper, barrel, screw, and mold. The hopper is where the plastic pellets are stored, and the barrel is where they are melted. The screw is used to push the melted plastic into the mold, and the mold is where the part is formed.
The process of low volume molding involves several steps, including mold design, material selection, injection molding, and part finishing. Mold design involves the creation of a mold that is used to produce the part. Material selection involves choosing the right material for the part, based on its properties and requirements. Injection molding involves the production of the part, and part finishing involves any post-processing that is required, such as trimming or painting.
Materials Used in Low-Volume Injection Molding
Low-volume injection molding is a versatile process that accommodates a diverse range of materials, such as thermoplastics, thermosets, and elastomers. Among these materials, thermoplastics are the most prevalent due to their ease of molding and extensive array of properties. Thermosets are used for parts that require high heat resistance, and elastomers are used for parts that require flexibility.
When choosing materials for low volume injection molding, designers must consider several factors, including the part’s properties, requirements, and cost. They must also consider the material’s processing characteristics, such as its melt flow rate and viscosity.
Design Considerations for Low Volume Molding
Design for manufacturing is an essential part of the product development process, and it is especially important for low-volume injection molding. Designers must consider several factors when designing parts for low-volume molding, including wall thickness, draft angles, and gate location.
Wall thickness is an important consideration, as it affects the part’s strength and durability. Parts with uniform wall thickness are easier to mold and produce consistent results.
Draft angles are also important, as they allow the part to be ejected from the mold. Parts with no draft angles are difficult to mold and can result in damage to the mold.
Gate location is another important consideration, as it affects the part’s appearance and quality. Gates should be located in areas that are easy to trim or hide, such as on the part’s underside.
Cost Comparison: Low Volume Injection Molding vs. Traditional Prototyping Methods
Low-volume injection molding is a cost-effective solution for prototyping, compared to traditional prototyping methods such as CNC machining or 3D printing. The cost of low volume injection molding depends on several factors, including the part’s complexity, material selection, and production volume.
CNC machining is a more expensive solution for prototyping, as it requires the use of expensive equipment and materials. 3D printing is also more expensive, as it requires the use of specialized equipment and materials. It is all about deciding which one is ideal for your project.
Applications of Low Volume Injection Molding in Various Industries
Low-volume injection molding is used in various industries, including automotive, aerospace, medical, and consumer goods. In the automotive industry, it is used for the production of interior and exterior parts. In the aerospace industry, it is used for the production of lightweight parts. In the medical industry, it is used for the production of medical devices. In the consumer goods industry, it is used for the production of toys, electronics, and household items.
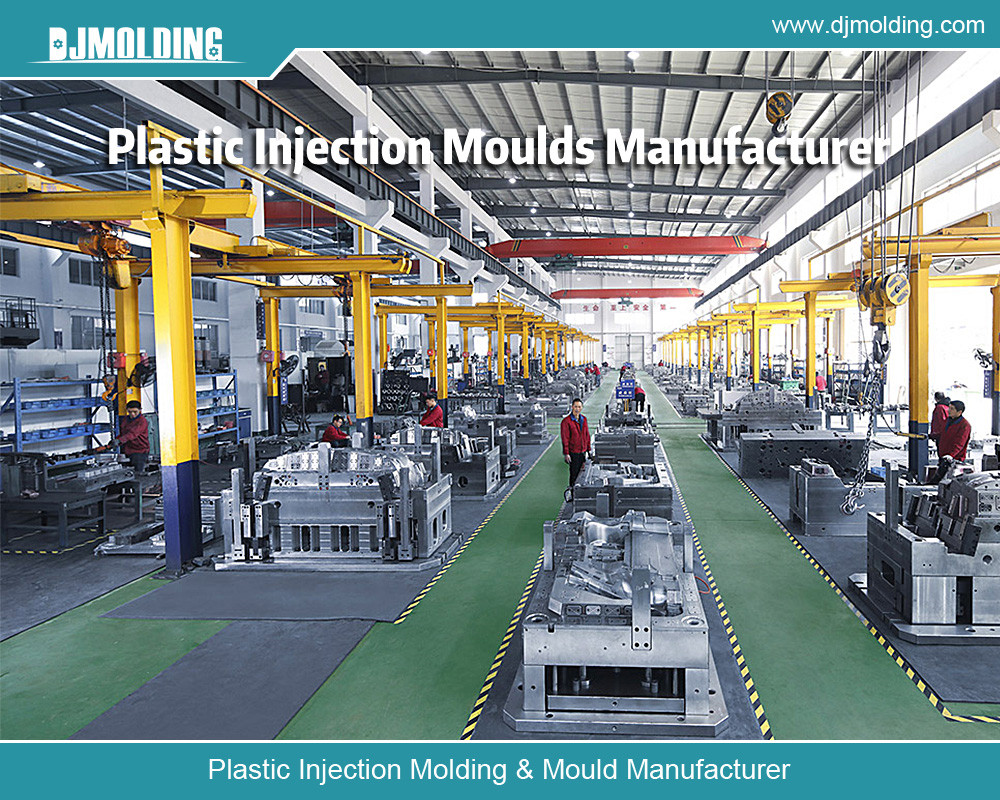
Conclusion
Low-volume injection molding is a cost-effective solution for prototyping, offering several benefits, including cost-effectiveness, faster turnaround time, high-quality parts, and the ability to test and refine designs. It is used in various industries, including automotive, aerospace, medical, and consumer goods. Designers must consider several factors when choosing a service provider, including experience, capabilities, and cost. The future of low volume molding in the prototyping industry looks promising, with potential advancements in technology and materials.
For more about low volume injection molding: a cost-effective solution for low volume rapid prototyping injection molding,you can pay a visit to Djmolding at https://www.djmolding.com/low-volume-injection-molding/ for more info.