Learn The Basics Of Plastic Injection Moulding Process Step By Step
Learn The Basics Of Plastic Injection Moulding Process Step By Step
Injection moulding is a widely used manufacturing process in which molten material is injected into a mould to create a desired shape. It is commonly used for the production of plastic parts and products, and it offers numerous advantages such as high production efficiency, cost-effectiveness, and the ability to create complex shapes with precision.
Learning the basics of injection moulding process is crucial for anyone involved in the manufacturing industry, as it provides a foundation for understanding the intricacies of this widely used technique.
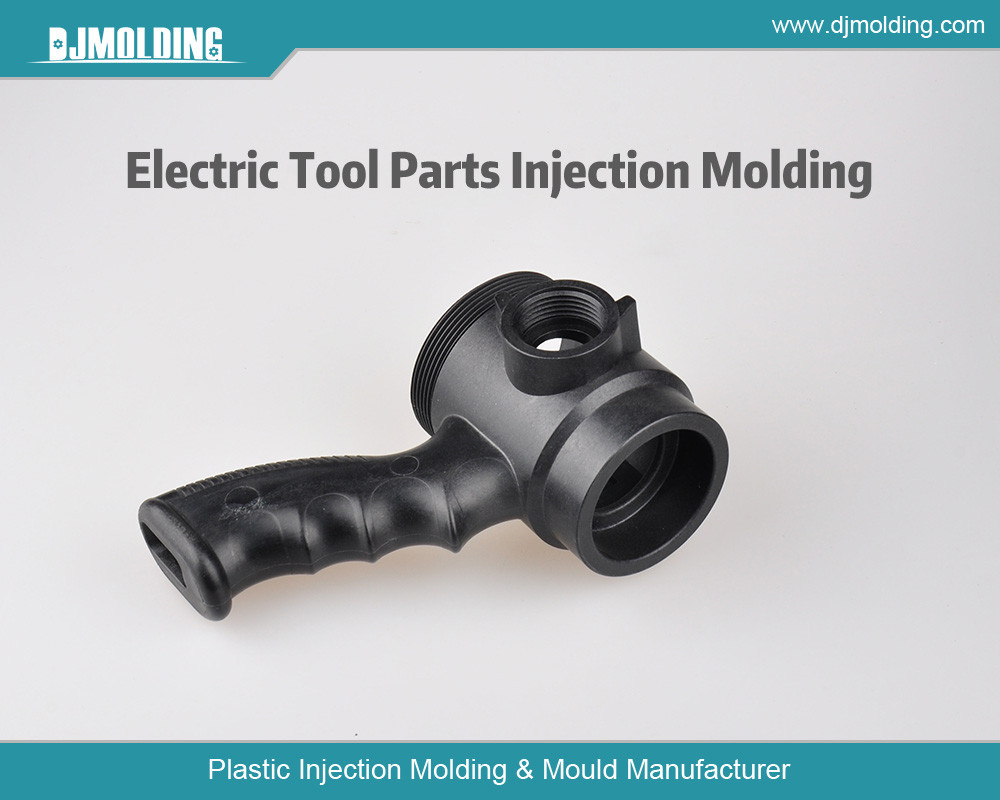
Understanding the Components of Injection Moulding Machine
An injection moulding machine consists of several major components that work together to facilitate the injection moulding process. These components include the hopper, screw, barrel, nozzle, clamping unit, and the mould itself.
The hopper is where the raw material is stored and fed into the machine. The barrel is heated to melt the material, and the screw is responsible for moving the molten material forward and injecting it into the mould through the nozzle. The clamping unit holds the mould in place during the injection process.
Each component plays a crucial role in the injection moulding process. The hopper ensures a steady supply of material, while the barrel and screw work together to melt and move the material forward. The nozzle controls the flow of molten material into the mould, and the clamping unit ensures that the mould remains securely closed during injection. Understanding how each component functions is essential for troubleshooting any issues that may arise during the injection moulding process.
Material Selection for Injection Moulding
Selecting the right material is crucial for successful injection moulding. Factors such as chemical resistance, mechanical properties, temperature resistance, and cost should be considered when choosing a material.
Common materials used in injection moulding include thermoplastics such as polypropylene (PP), polyethylene, polystyrene (PS), and acrylonitrile butadiene styrene (ABS). These materials offer a good balance of properties and are widely available.
Other factors to consider when selecting materials for injection moulding include the color options, desired surface finish, and any specific requirements for the end product. It is important to work closely with material suppliers and conduct thorough testing to ensure that the selected material meets all the necessary criteria for the intended application.
Preparing the Mould for Injection Moulding
Proper preparation of the mould is essential for successful injection moulding. The mould must be cleaned and inspected for any defects or damage before use. Any residue or contaminants should be removed to ensure that the final product is free from defects. Additionally, proper lubrication should be applied to ensure smooth operation during the injection process.
The mould should also be properly aligned and securely fastened to the clamping unit of the injection moulding machine. This ensures that the mould remains in place during the injection process and prevents any leakage or misalignment that could result in defective parts. Taking the time to properly prepare the mould before injection moulding can greatly improve the quality and consistency of the final product.
Injection Moulding Process Step by Step
The injection moulding process consists of several steps that must be followed in a precise sequence to achieve the desired results. The first step is material preparation, where the raw material is loaded into the hopper and fed into the barrel of the injection moulding machine. The material is then heated and melted, and the screw moves it forward towards the nozzle.
Once the material is molten and ready for injection, the clamping unit closes the mould and holds it securely in place. The molten material is then injected into the mould through the nozzle, filling up the cavities and taking on the shape of the desired product. After a cooling period, the mould is opened, and the solidified part is ejected from the mould.
Injection Moulding Parameters and Settings
Proper selection of injection moulding parameters and settings is crucial for achieving consistent and high-quality results. Key parameters to consider include injection speed, injection pressure, melt temperature, and holding pressure. These parameters can be adjusted based on factors such as material type, part design, and desired product specifications.
Injection pressure determines how forcefully the molten material is injected into the mould, while injection speed controls how quickly it fills up the cavities. Melt temperature affects the viscosity of the material and its flow characteristics. Cooling time allows for proper solidification of the part, while holding pressure ensures that there are no voids or defects in the final product.
Troubleshooting Injection Moulding Process
Despite careful preparation and selection of parameters, issues can still arise during the injection moulding process. Common problems include flash, sink marks, warping, short shots, and dimensional variations. Flash occurs when excess material escapes from the mould, resulting in unwanted excess material on the part. Sink marks are depressions or indentations on the surface of the part caused by uneven cooling.
Warping refers to the distortion or bending of the part due to uneven cooling or improper mould design. Short shots occur when the mould does not completely fill up with material, resulting in incomplete parts. Dimensional variations can occur due to variations in material shrinkage or improper mould design. Troubleshooting these issues requires a thorough understanding of the injection moulding process and careful analysis of the root causes.
Post-Injection Moulding Operations
After the injection moulding process is complete, there are several post-injection moulding operations that may be required depending on the specific application. These operations include trimming, deburring, surface finishing, and assembly. Trimming involves removing any excess material or flash from the part to achieve the desired final shape. Deburring is the process of removing any sharp edges or burrs that may be present on the part.
Surface finishing operations such as polishing, painting, or coating may be required to enhance the appearance and functionality of the part. Assembly operations involve joining multiple injection-moulded parts together to create a final product. These post-injection moulding operations are essential for ensuring that the final product meets all the necessary requirements and specifications.
Quality Control and Inspection in Injection Moulding
Quality control and inspection play a crucial role in ensuring that the injection moulding process produces parts that meet all the necessary requirements and specifications. This involves conducting regular inspections throughout the production process to identify any defects or deviations from the desired standards. Inspection methods may include visual inspection, dimensional measurement, and functional testing.
Quality control measures should be implemented at every stage of the injection moulding process, from material selection to post-injection moulding operations. This helps to identify and address any issues early on, preventing costly rework or rejection of parts. Implementing a robust quality control system is essential for maintaining consistent product quality and customer satisfaction.
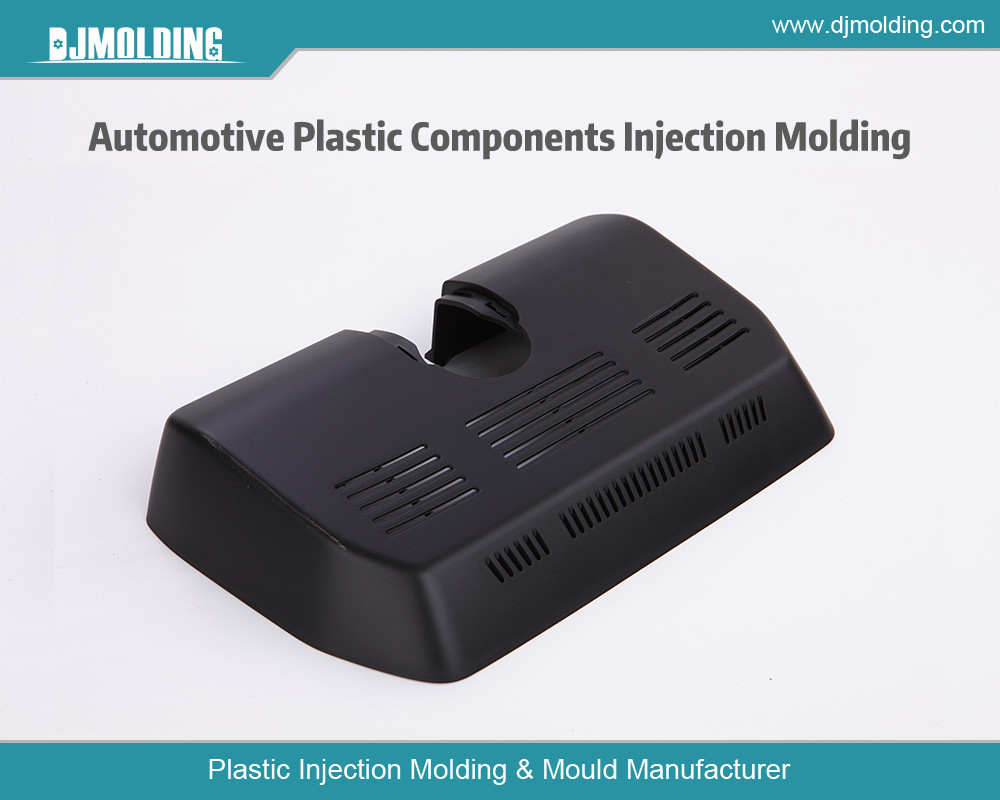
Future of Injection Moulding Technology
The field of injection moulding technology is constantly evolving, with new advancements and innovations being introduced regularly. One of the key areas of development is the use of advanced materials, such as composites and biodegradable plastics, which offer improved sustainability and performance characteristics. Additionally, advancements in automation and robotics are making the injection moulding process more efficient and cost-effective.
For more about the basics of plastic injection moulding process step by step,you can pay a visit to Djmolding at https://www.djmolding.com/a-step-by-step-manufacturing-guide-to-plastic-injection-molding-process/ for more info.