Injection Molding vs Extrusion Molding: A Comparative Analysis
Injection Molding vs Extrusion Molding: A Comparative Analysis
Injection molding and extrusion molding are two of the plastic industry’s most widely used manufacturing processes. Both techniques have distinct advantages and applications, making them suitable for different production requirements. This article compares:
- Injection molding and extrusion molding, exploring their process.
- Exploring drawbacks and ideal use cases. Und.
- Ideal the different
CES and similarities between these methods can help manufacturers choose the most appropriate technique.
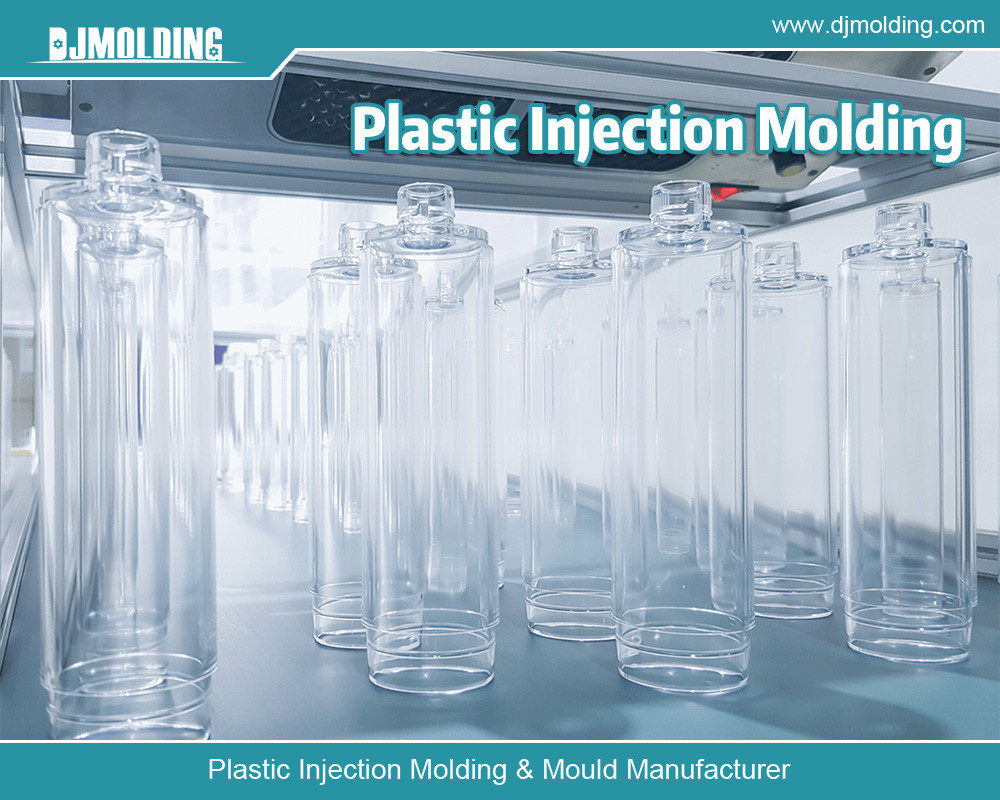
The Basics of Injection Molding
What is Injection Molding?
Injection molding is a manufacturing process that produces parts by injecting molten material into a mold. This technique is commonly used to make a variety of plastic products, from small components to large parts. The process involves several stages: material preparation, melting, injecting, cooling, and ejection.
The Injection Molding Process
- Material Preparation: Plastic pellets or granules are dried and pre-conditioned to remove moisture.
- Melting: The plastic material is fed into a heated barrel, where it is melted by the combined effects of heat and the shearing action of a rotating screw.
- Injecting: The molten plastic is injected into a mold cavity under high pressure. The mold is designed to form the shape of the final product.
- Cooling: The mold and the injected material are cooled, allowing the plastic to solidify into the desired shape.
- Ejection: The solidified part is ejected from the mold, and the process can be repeated.
Advantages of Injection Molding
- High Precision and Complex Geometries: Injection molding allows for the creating of intricate and highly detailed parts with tight tolerances.
- Efficiency and Speed: The process is highly automated and can quickly produce large quantities of parts.
- Material Versatility: A wide range of thermoplastic and thermosetting materials can be used.
- Low Waste: Excess material can often be recycled and reused, reducing waste.
Disadvantages of Injection Molding
- High Initial Costs: The cost of designing and manufacturing molds can be very high.
- Material Limitations: Some materials may not be suitable for injection molding due to their viscosity or thermal properties.
- Part Size Limitations: This method may make Extensive parts difficult or impractical to produce.
The Basics of Extrusion Molding
What is Extrusion Molding?
Extrusion molding is a continuous manufacturing process that creates objects with a fixed cross-sectional profile. Unlike injection molding, which produces discrete parts, extrusion molding produces long, continuous shapes that can be cut to desired lengths. This process is commonly used for making pipes, tubing, sheets, and profiles.
The Extrusion Molding Process
- Material Preparation: Unlike injection molding, plastic pellets or granules are dried and conditioned.
- Melting: The plastic material is fed into a heated barrel and melted.
- Extruding: The molten plastic is forced through a die that shapes the material into a continuous profile.
- Cooling: The extruded profile is cooled using air or water baths.
- Cutting: The continuous profile is cut into desired lengths or shapes.
Advantages of Extrusion Molding
- Cost-Effective for Long Runs: Ideal for producing long, continuous shapes with consistent cross-sections.
- Efficiency: The constant nature of the process can lead to high production rates.
- Versatility in Shapes: Can produce a wide variety of shapes and sizes.
- Material Efficiency: Minimal waste as the process can be fine-tuned to produce precisely the needed amount of material.
Disadvantages of Extrusion Molding
- Limited to Uniform Cross-Sections: Only parts with a consistent cross-sectional profile can be produced.
- Dimensional Tolerances: These may not achieve the exact tight tolerances as injection molding.
- Cooling Challenges: Uniform cooling can be complicated, potentially leading to warping or other defects.
Comparative Analysis
Production Capabilities
Injection Molding:
- Best suited for high-precision parts with complex geometries.
- Capable of producing a wide range of part sizes but generally limited to smaller components.
- Ideal for high-volume production of discrete parts.
Extrusion Molding:
- It is best suited for continuous shapes with uniform cross-sections.
- Can produce large quantities of material efficiently.
- Ideal for products like pipes, tubes, and profiles.
Material Considerations
Injection Molding:
- Suitable for a wide variety of materials, including both thermoplastics and thermosets.
- Allows multiple materials to be used in a single part (co-injection molding).
Extrusion Molding:
- Primarily uses thermoplastic materials due to their ease of melting and shaping.
- Limited in the variety of materials compared to injection molding.
Cost Factors
Injection Molding:
- High initial costs due to mold design and manufacturing.
- Cost-effective for high-volume production runs where the mold cost can be amortized over many parts.
Extrusion Molding:
- Lower initial costs as it typically involves more superficial dies compared to injection molds.
- Cost-effective for continuous production runs and extended profiles.
Flexibility and Versatility
Injection Molding:
- Highly versatile in terms of part complexity and material use.
- Capable of producing parts with intricate details and varying thicknesses.
Extrusion Molding:
- Versatile in producing a wide range of continuous shapes and sizes.
- Limited to producing parts with uniform cross-sections, making it less versatile in terms of part complexity.
Applications of Injection Molding and Extrusion Molding
Injection Molding Applications
- Consumer Products: Toys, household items, electronic housings, and automotive components.
- Medical Devices: Syringes, surgical instruments, and diagnostic components.
- Industrial Parts: Gears, brackets, and enclosures.
- Packaging: Lids, caps, and containers.
Extrusion Molding Applications
- Building and Construction: Pipes, window frames, and siding.
- Automotive: Tubing, weatherstripping, and interior trim.
- Packaging: Film, sheets, and bags.
- Electrical: Cable insulation and conduit.
Environmental Impact
Injection Molding
Like many manufacturing processes, injection molding can have a significant environmental impact. The energy required to heat and melt plastic, coupled with the production of molds, contributes to its carbon footprint. However, advancements in technology and materials are helping to mitigate these effects. For instance, using recycled plastics and biodegradable materials is becoming more common. Moreover, the precision of injection molding can lead to less material waste than other processes.
Extrusion Molding
Extrusion molding also has environmental considerations. The continuous nature of the process can lead to material efficiency, but it also requires significant energy for heating and extruding the plastic. Cooling methods, such as water baths, can also have environmental impacts, mainly if not appropriately managed. However, extrusion molding typically produces less waste than other molding methods, and many facilities are implementing recycling programs to reduce their environmental footprint further.
Future Trends and Innovations
Innovations in Injection Molding
- Advanced Materials: Developing new polymers and composites with superior performance and sustainability.
- Automation and AI: Increasing automation and artificial intelligence use to enhance precision, reduce waste, and improve efficiency.
- Sustainable Practices: Greater focus on using recycled and biodegradable materials to reduce environmental impact.
Innovations in Extrusion Molding
- Enhanced Cooling Techniques: Developing more efficient cooling methods to improve product quality and reduce energy consumption.
- Material Advancements: Introduction of new materials that offer better properties and recyclability.
- Smart Manufacturing: IoT and innovative technologies are integrated to monitor and optimize the real-time extrusion process.
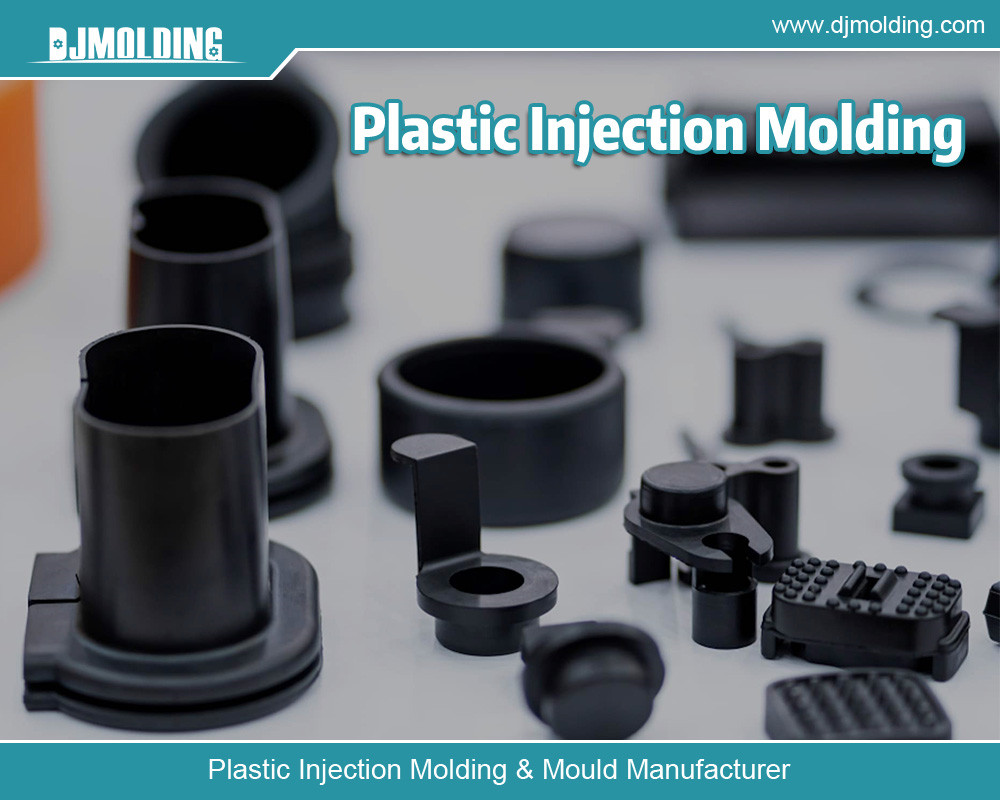
Conclusion
Injection and extrusion molding are essential manufacturing processes in the plastics industry, each with unique strengths and limitations. Injection molding excels in producing high-precision, complex parts in large volumes, making it ideal for various applications, from consumer goods to medical devices. On the other hand, extrusion molding is best suited for creating long, continuous shapes with consistent cross-sections, such as pipes and tubing, offering cost-efficiency and high production rates.
Choosing between these two processes depends on the product’s specific requirements, including its shape, material, volume, and precision. Understanding the nuances of each method allows manufacturers to make informed decisions, optimizing production efficiency, cost, and environmental impact.
As technology advances, injection, and extrusion molding are poised to become even more efficient and environmentally friendly, ensuring their continued relevance in the evolving manufacturing landscape.
For more about injection molding vs extrusion molding: a comparative analysis,you can pay a visit to Djmolding at https://www.djmolding.com/the-difference-between-plastic-injection-molding-and-extrusion/ for more info.