Injection Molding vs Compression Molding: A Comprehensive Comparison
Injection Molding vs Compression Molding: A Comprehensive Comparison
Manufacturing processes play a crucial role in shaping the products we use daily. Two prominent methods in the plastics industry are injection molding and compression molding. Both techniques have unique advantages, limitations, and applications. This article delves into the specifics of each process, comparing them in terms of mechanics, materials, applications, benefits, and drawbacks.
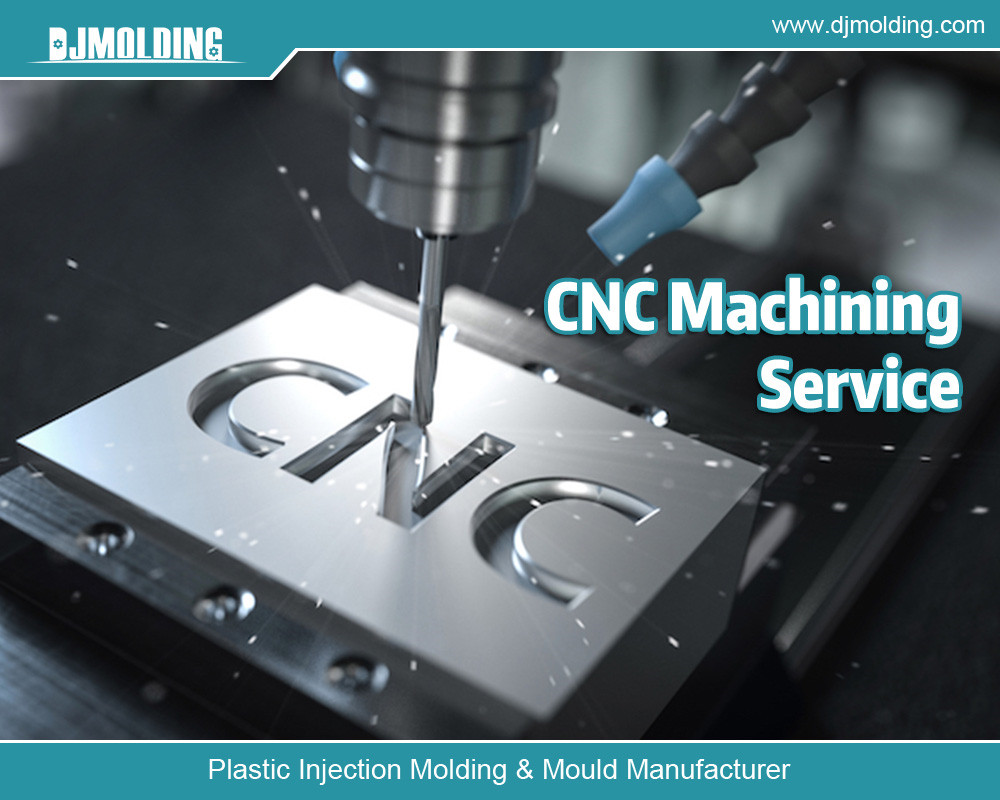
Understanding Injection Molding
The Injection Molding Process
Injection molding is a widely used manufacturing technique where molten material, typically plastic, is injected into a mold cavity. The process involves several key steps:
- Material Preparation: Thermoplastic resins are melted.
- Injection: The molten material is injected into a mold under high pressure.
- Cooling: The material cools and solidifies in the mold.
- Ejection: The finished part is ejected from the mold.
Materials Used in Injection Molding
Injection molding is versatile, accommodating a wide range of materials:
- Thermoplastics: Polyethylene (PE), polypropylene (PP), polystyrene (PS), polyvinyl chloride (PVC), and acrylonitrile butadiene styrene (ABS).
- Thermosetting Plastics: Epoxy, phenolic, and melamine.
- Elastomers: Silicone and rubber.
Applications of Injection Molding
Injection molding is ideal for producing high volumes of identical parts with intricate designs. Common applications include:
- Consumer Goods: Toys, containers, and household items.
- Automotive: Dashboard components, bumpers, and engine parts.
- Medical Devices: Syringes, diagnostic devices, and housings.
- Electronics: Enclosures, connectors, and switches.
Understanding Compression Molding
The Compression Molding Process
Compression molding involves placing a preheated material into a heated mold cavity. The mold is then closed, and pressure is applied to shape the material. The process comprises:
- Material Preparation: Material is often prepared in the form of a preform.
- Molding: The material is placed into the mold cavity.
- Compression: The mold closes, and heat and pressure are applied to shape the material.
- Cooling and Ejection: The part cools and is ejected from the mold.
Materials Used in Compression Molding
Compression molding primarily uses thermosetting plastics and composites, including:
- Thermosets: Phenolic, melamine, and epoxy resins.
- Rubber: Natural and synthetic rubbers.
- Composites: Glass-filled polyester and carbon fiber-reinforced materials.
Applications of Compression Molding
Compression molding is suitable for producing large, durable parts with excellent mechanical properties. Typical applications are:
- Automotive: Body panels, gaskets, and brake components.
- Electrical: Insulators, connectors, and circuit breakers.
- Appliances: Handles, knobs, and housings.
- Industrial Equipment: Seals, washers, and bushings.
Critical Differences Between Injection Molding and Compression Molding
Process Mechanics
Injection Molding:
- Cycle Time: Generally faster due to simultaneous heating and cooling.
- Precision: High precision with complex geometries and fine details.
- Automation: Highly automated, reducing labor costs.
Compression Molding:
- Cycle Time: Slower, involving separate heating and cooling phases.
- Precision: Suitable for simpler shapes with less intricate details.
- Automation: Less automated, often requiring more manual labor.
Material Characteristics
Injection Molding:
- Material Range: There is a wide variety of thermoplastics and some thermosets.
- Waste: Less waste, as excess material, can be reused.
- Consistency: High consistency and uniformity in parts.
Compression Molding:
- Material Range: Primarily thermosets and composites.
- Waste: More waste, especially with flash and trimming.
- Consistency: There may be more variability in part thickness and uniformity.
Cost Considerations
Injection Molding:
- Initial Costs: High due to mold design and manufacturing.
- Production Costs: Lower per part at high volumes due to automation.
- Tooling Costs: Expensive molds that are durable for large production runs.
Compression Molding:
- Initial Costs: Lower initial costs for molds.
- Production Costs: Higher per part due to longer cycle times and manual labor.
- Tooling Costs: Less expensive molds with shorter lifespans.
Part Properties
Injection Molding:
- Surface Finish: Excellent surface finish and appearance.
- Strength: It varies depending on the material but is generally less robust for high-stress applications.
- Complexity: Capable of producing complex, detailed parts.
Compression Molding:
- Surface Finish: Good surface finish, but may require additional finishing.
- Strength: High mechanical strength and durability.
- Complexity: Better suited for simpler, thicker parts.
Advantages and Disadvantages
Advantages of Injection Molding
- High Efficiency: Fast production cycles with minimal labor.
- Precision: Ability to produce complex parts with tight tolerances.
- Material Versatility: A wide range of materials can be used.
- Waste Reduction: Less material waste due to the reusability of excess material.
Disadvantages of Injection Molding
- High Initial Costs: Expensive molds and setup costs.
- Complexity in Mold Design: Requires sophisticated mold design and manufacturing.
- Material Limitations: Less suitable for high-strength applications compared to compression molding.
Advantages of Compression Molding
- Cost-Effective for Low Volumes: Lower initial mold costs make it ideal for small production runs.
- Material Strength: Produces parts with superior mechanical properties.
- Simplicity: Easier mold design and less complex machinery.
- Extensive Part Capability: Suitable for larger, thicker parts that are difficult to produce with injection molding.
Disadvantages of Compression Molding
- Longer Cycle Times: Slower production rates due to separate heating and cooling phases.
- Higher Labor Costs: More manual labor is involved, increasing production costs.
- Limited Detail: Less capable of producing intricate, detailed parts.
Choosing the Right Method
Factors to Consider
When deciding between injection molding and compression molding, several factors need to be considered:
- Volume of Production: Injection molding is more cost-effective for high-volume production, while compression molding is better suited for lower volumes.
- Part Complexity: Injection molding excels in producing complex parts with intricate details, whereas compression molding is ideal for simpler, more significant parts.
- Material Properties: The choice of materials and the required mechanical properties of the final product play a crucial role. Compression molding is preferred for high-strength applications.
- Cost Constraints: Initial setup costs and tooling expenses must be evaluated. Injection molding requires a higher initial investment, but the cost per part decreases significantly with volume.
- Production Speed: If fast production cycles are essential, injection molding is preferred due to its efficiency and automation capabilities.
Industry Examples
Automotive Industry:
- Injection Molding: Producing small, intricate parts like clips, fasteners, and interior components.
- Compression Molding: Manufacturing large, robust parts such as body panels, gaskets, and bumpers.
Consumer Electronics:
- Injection Molding: Fabricating precise, detailed components like connectors, housings, and buttons.
- Compression Molding: Creating durable, high-strength parts like insulators and protective covers.
Medical Devices:
- Injection Molding: Producing high-volume, precise items such as syringes, diagnostic tools, and casings.
- Compression Molding: Manufacturing specialized components like gaskets, seals, and high-strength handles.
Future Trends and Innovations
Advancements in Materials
Continuous development in polymer science is expanding the range of materials suitable for injection and compression molding. Innovations in bioplastics, high-performance polymers, and recyclable materials drive the industry towards more sustainable practices.
Automation and Smart Manufacturing
The integration of Industry 4.0 technologies is revolutionizing manufacturing processes. Automation, artificial intelligence, and the Internet of Things (IoT) enhance the efficiency, precision, and flexibility of injection and compression molding. Intelligent manufacturing systems enable real-time monitoring, predictive maintenance, and optimization of production parameters.
Environmental Sustainability
With growing environmental concerns, the plastics industry focuses on sustainable manufacturing practices. Injection and compression molding processes are optimized to reduce waste, energy consumption, and carbon footprint. Recycling and reuse of materials are becoming integral parts of the production cycle.
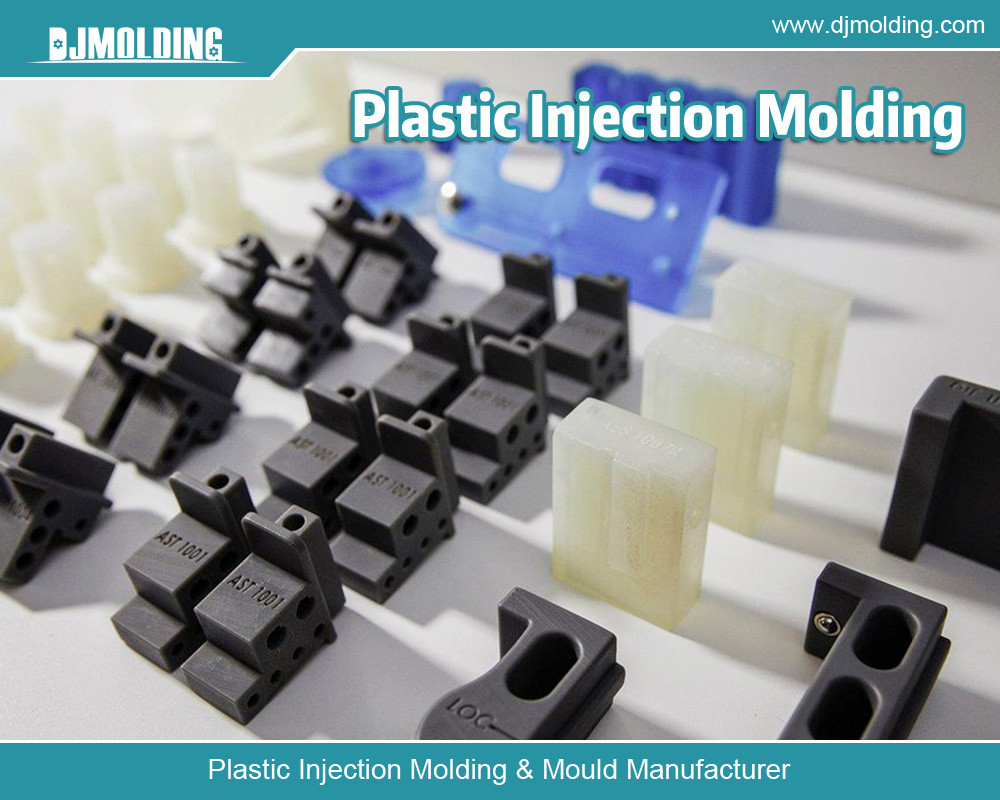
Conclusion
Injection and compression molding are two fundamental techniques in the plastics manufacturing industry, each with distinct advantages and applications. Injection molding offers high precision, efficiency, and versatility, making it ideal for large-scale production of intricate parts. Compression molding, on the other hand, excels in producing robust, high-strength components with lower initial costs.
The correct method depends on various factors, including production volume, part complexity, material properties, cost constraints, and production speed. Understanding each process’s unique characteristics and capabilities is crucial for manufacturers to make informed decisions and optimize their production strategies.
As technology advances and sustainability becomes a priority, injection, and compression molding are poised to evolve, incorporating new materials, automation, and eco-friendly practices. These developments will ensure that these manufacturing techniques continue to meet the demands of various industries, driving innovation and efficiency.
For more about injection molding vs compression molding: a comprehensive comparison,you can pay a visit to Djmolding at https://www.djmolding.com/about/ for more info.