Injection Molding vs. Casting: A Comprehensive Comparison
Injection Molding vs. Casting: A Comprehensive Comparison
Manufacturing processes are the backbone of modern industry, crucial in producing everything from everyday household items to complex aerospace components. Two prevalent manufacturing techniques, injection molding, and casting, are often used to create parts with intricate shapes and detailed features. Despite their similarities, these processes have distinct differences in materials, applications, benefits, and limitations. This article delves into the nuances of injection molding and casting, providing a comprehensive comparison to help manufacturers, engineers, and designers choose the appropriate method for their specific needs.
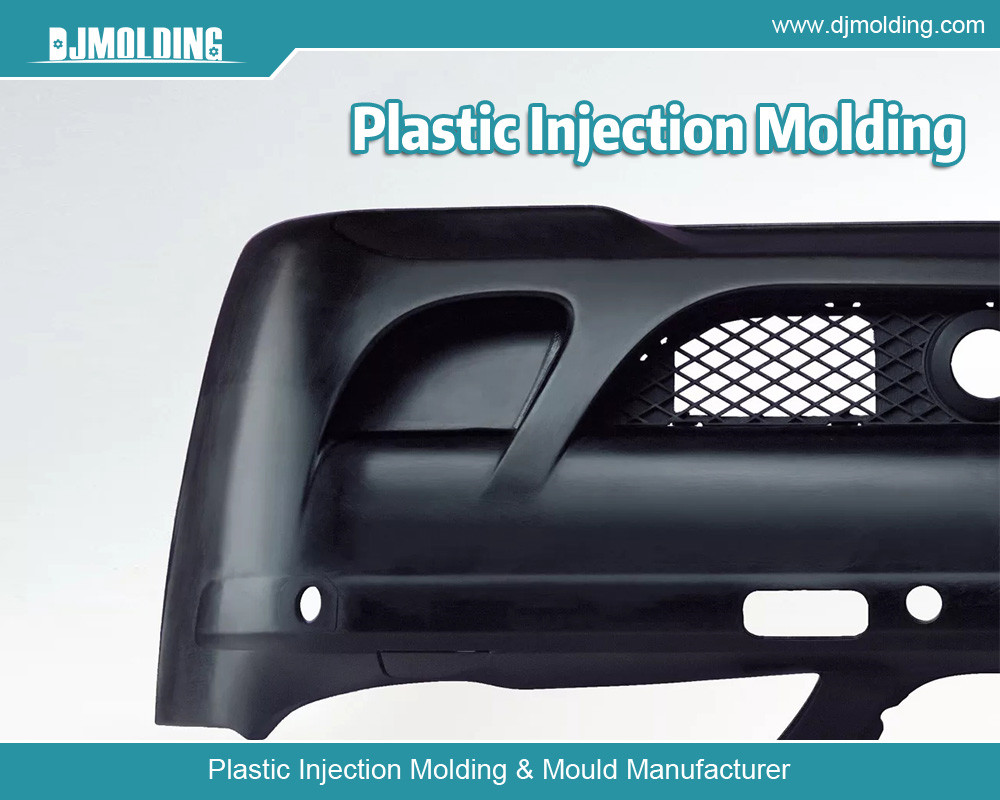
Understanding Injection Molding
What is Injection Molding?
Injection molding is a manufacturing process used to produce parts by injecting molten material into a mold. The process involves several steps:
- Material Preparation: Raw plastic materials, usually pellets, are heated until they reach a molten state.
- Injection: The molten plastic is injected into a mold cavity under high pressure.
- Cooling: The material cools and solidifies in the shape of the mold.
- Ejection: The final product is ejected from the mold once sufficiently cooled and hardened.
Materials Used in Injection Molding
Injection molding predominantly uses thermoplastic polymers, although thermosetting plastics and elastomers can also be employed. Common materials include:
- Polypropylene (PP)
- Polyethylene (PE)
- Acrylonitrile Butadiene Styrene (ABS)
- Polycarbonate (PC)
- Nylon (PA)
Applications of Injection Molding
Injection molding is highly versatile and used in various industries, such as:
- Automotive: Components like dashboards, bumpers, and various under-the-hood parts.
- Consumer Goods: Toys, kitchen utensils, and electronic housings.
- Medical: Syringes, vials, and diagnostic devices.
- Packaging: Caps, containers, and lids.
Advantages of Injection Molding
- High Efficiency and Speed: The production process is fast once the mold is made, allowing for high-volume manufacturing.
- Consistency and Precision: Provides high repeatability and tight tolerances, ensuring uniformity in mass production.
- Material Versatility: Capable of molding complex shapes and integrating multiple features in a single part.
- Reduced Waste: Excess material can often be recycled and reused, minimizing waste.
Limitations of Injection Molding
- High Initial Cost: Mold creation is expensive, making it less cost-effective for low-volume production.
- Design Restrictions: Certain design complexities may require additional steps or modifications to the mold.
- Long Lead Times: The development and fabrication of molds can be time-consuming.
Understanding Casting
What is Casting?
Casting is a manufacturing process in which a liquid material is poured into a mold containing a hollow cavity of the desired shape and then solidified. The process consists of the following steps:
- Pattern Making: Creating a pattern that represents the geometry of the final product.
- Mold Making: Forming a mold cavity based on the pattern.
- Melting: Heating the material (usually metal) until it becomes liquid.
- Pouring: Pouring the molten material into the mold.
- Cooling and Solidification: Allowing the material to cool and solidify into the shape of the mold.
- Removal: Extracting the solidified part from the mold.
Materials Used in Casting
Casting predominantly uses metals but can also work with certain plastics, ceramics, and even glass. Common casting materials include:
- Iron and Steel
- Aluminum
- Copper Alloys
- Zinc
- Magnesium
Applications of Casting
Casting is utilized across numerous industries, including:
- Aerospace: Engine components, turbine blades, and structural parts.
- Automotive: Engine blocks, gearboxes, and suspension components.
- Construction: Pipes, fittings, and architectural elements.
- Jewelry: Intricate designs and custom pieces.
- Art: Sculptures and decorative objects.
Advantages of Casting
- Complex Geometry: Proving intricate shapes and detailed features that might be difficult or impossible with other methods.
- Material Variety: Suitable for many materials, including metals that cannot be molded.
- Cost-Effectiveness for Large Parts: Economical for producing large, heavy parts in small to medium quantities.
- Versatility: Applicable to a broad spectrum of industries and product types.
Limitations of Casting
- Surface Finish and Precision: Additional finishing processes may be required to achieve the desired surface quality and dimensional accuracy.
- Long Cooling Times: Cooling and solidification can be slow, impacting production speed.
- Potential for Defects: Susceptible to issues such as porosity, shrinkage, and inclusions, which can affect the integrity of the final product.
- Tooling Wear: Molds and tools can wear out faster due to high temperatures and abrasive materials.
Comparing Injection Molding and Casting
Cost Considerations
- Initial Investment: Injection molding has higher upfront costs due to mold fabrication, making it more suitable for high-volume production. Casting, especially sand casting, has lower initial costs, making it ideal for low to medium volumes.
- Per-Unit Cost: Injection molding becomes more cost-effective at higher volumes while casting remains cost-effective for smaller production runs.
Production Speed
- Injection Molding: Known for its high production speed once the mold is ready. Capable of producing thousands of parts per day.
- Casting: Generally slower due to the time required for cooling and solidification. Production speed can vary significantly based on the casting method used.
Design Flexibility
- Injection Molding: Offers excellent design flexibility, allowing for complex shapes and integrated features. However, certain design limitations exist due to the molding process.
- Casting: Excels in creating complex geometries and large, intricate parts. More accommodating of design changes, especially in the prototype stage.
Material Properties
- Injection Molding: Primarily limited to plastics, with some use of metals and ceramics. Offers a range of material properties, including impact resistance, flexibility, and transparency.
- Casting: Predominantly used for metals, providing excellent mechanical properties such as strength, durability, and heat resistance.
Quality and Precision
- Injection Molding: Known for high precision and consistency, it suits parts requiring tight tolerances and smooth finishes.
- Casting: While capable of producing high-quality parts, it may require additional machining and finishing to achieve the same level of precision and surface finish as injection molding.
Environmental Impact
- Injection Molding: Generates less waste due to the recyclability of excess material. However, the energy consumption for mold creation and production can be high.
- Casting: Can produce significant waste material and requires energy-intensive processes, particularly for melting metals. Sand casting can reuse sand, but other methods may generate more waste.
Choosing the Right Process
Factors to Consider
- Volume: High-volume production favors injection molding while casting suits lower volumes.
- Material: The choice of material often dictates the process, with plastics favoring injection molding and metals leaning towards casting.
- Part Size and Complexity: Larger and more complex parts may be better suited for casting.
- Cost Constraints: Budget considerations, including initial investment and per-unit cost, are crucial in decision-making.
- Lead Time: The urgency of the production timeline can influence the choice, with injection molding generally offering faster turnaround times once the mold is ready.
Case Studies
- Automotive Industry: An automaker might use injection molding to produce plastic interior components due to the high volume and precision required. Conversely, casting would be used for engine blocks where metal’s material strength and durability are essential.
- Consumer Electronics: A company producing plastic housings for electronic devices would benefit from the high efficiency and consistency of injection molding. However, casting might be the preferred method for custom metal parts, such as heatsinks.
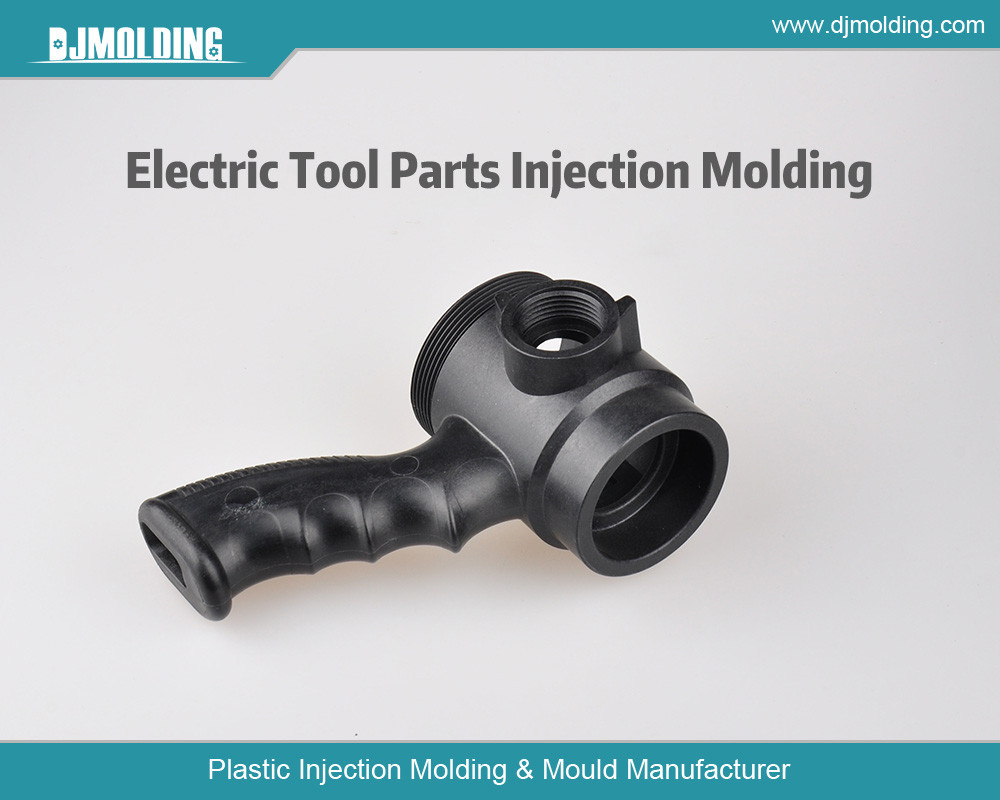
Conclusion
Injection molding and casting are indispensable manufacturing processes, each with unique advantages and limitations. Injection molding is ideal for high-volume production of plastic parts, offering precision, efficiency, and versatility. On the other hand, casting excels in producing large, complex metal parts, accommodating a wide range of materials and geometries.
Understanding a project’s specific requirements, including material properties, production volume, cost constraints, and design complexity, is essential in choosing the most appropriate manufacturing process. By carefully evaluating these factors, manufacturers can optimize their production strategies, ensuring the quality, efficiency, and cost-effectiveness of their operations.
For more about injection molding vs. casting: a comprehensive comparison,you can pay a visit to Djmolding at https://www.djmolding.com/what-is-the-difference-of-die-casting-vs-injection-molding/ for more info.