Injection Molding vs Blow Molding: A Comprehensive Comparison
Injection Molding vs Blow Molding: A Comprehensive Comparison
Plastic manufacturing has revolutionized various industries, offering versatile solutions for creating a wide range of products. Among the numerous methods used to shape plastics, injection, and blow molding are two of the most prominent techniques. Each has unique advantages, applications, and processes, making them suitable for different types of products. This article delves into the intricacies of injection and blow molding, comparing their processes, applications, benefits, and limitations.
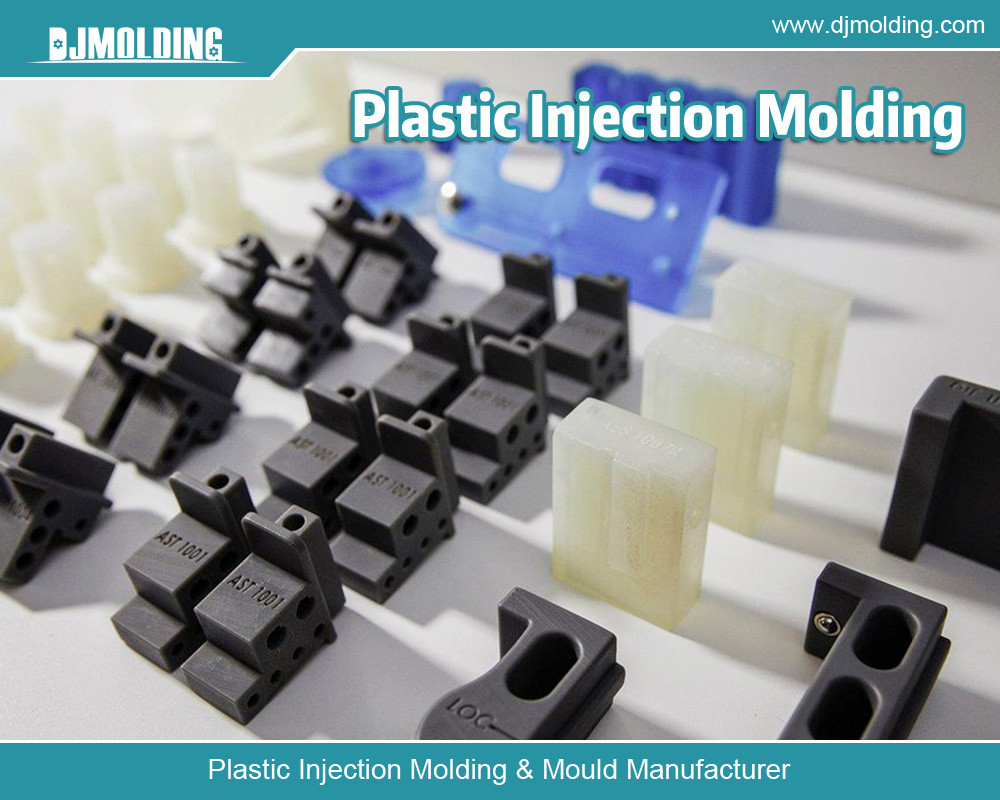
Overview of Injection Molding
What is Injection Molding?
Injection molding is a manufacturing process for producing parts by injecting molten material into a mold. It is widely used to create plastic products, from small components to large automotive parts. The process involves melting plastic pellets and injecting the molten plastic into a precisely machined mold cavity. Once the plastic cools and solidifies, the mold opens to eject the finished part.
Process of Injection Molding
- Clamping: The injection mold comprises two halves, which are securely clamped together.
- Injection: Plastic pellets are fed into a heated barrel and melted. The molten plastic is then injected into the mold cavity.
- Cooling: The plastic fills the mold cavity and begins to cool and solidify.
- Ejection: Once the plastic part is sufficiently cooled, the mold opens, and the part is ejected.
Applications of Injection Molding
Injection molding is used in various industries due to its precision and efficiency. Common applications include:
- Consumer Goods: Toys, household items, and electronic housings.
- Automotive: Bumpers, dashboards, and various internal components.
- Medical: Syringes, surgical instruments, and diagnostic devices.
- Packaging: Caps, lids, and containers.
Overview of Blow Molding
What is Blow Molding?
Blow molding is a manufacturing process used to produce hollow plastic parts. It involves inflating a heated plastic tube, a parison, inside a mold cavity. The air pressure forces the plastic to conform to the shape of the mold, creating a hollow part once it cools and solidifies.
Process of Blow Molding
- Extrusion: Plastic pellets are melted and extruded to form a parison.
- Blowing: The parison is clamped into a mold, and air is blown into it, expanding the plastic to fit the cavity.
- Cooling: The plastic cools and solidifies in the shape of the mold.
- Ejection: The mold opens, and the finished hollow part is ejected.
Applications of Blow Molding
Blow molding is ideal for producing hollow objects and is commonly used in the following areas:
- Packaging: Bottles, containers, and jugs.
- Automotive: Fuel tanks, ducts, and reservoirs.
- Household Products: Detergent bottles, water containers, and toys.
- Medical: Medical containers and pharmaceutical packaging.
Comparing Injection Molding and Blow Molding
Material Use and Efficiency
Injection molding is highly efficient for producing solid parts with minimal material waste. The process can handle complex geometries and multiple cavities within a single mold, optimizing production cycles. Blow molding, on the other hand, is specialized for hollow parts, utilizing materials efficiently to create lightweight and robust containers. Both methods offer high material utilization, but the choice depends on the product requirements.
Production Speed and Volume
Injection molding typically offers faster cycle times than blow molding, especially for high-volume production runs. This makes it suitable for mass production of intricate parts. Blow molding, while generally slower, is the preferred choice for producing large volumes of hollow items like bottles and containers, where the molding process naturally aligns with the product’s design.
Design Flexibility
Injection molding provides exceptional design flexibility, allowing for intricate details, tight tolerances, and complex geometries. Incorporating multiple features into a single part is a significant advantage. Blow molding, while more limited in design complexity, creates uniform, hollow shapes. It can accommodate variations in wall thickness and handle undercuts better than injection molding.
Cost Considerations
The cost of tooling and molds is typically higher for injection molding due to the precision and complexity of creating detailed mold cavities. However, the per-unit cost decreases significantly with higher production volumes, making it cost-effective for large-scale manufacturing. Blow molding molds are generally more straightforward and less expensive, making it an economical choice for producing large, hollow items, even in lower quantities.
Quality and Strength
Injection molding produces parts with excellent surface finish, dimensional accuracy, and structural integrity. This makes it ideal for applications requiring high precision and durability. Blow molding also produces high-quality parts, particularly for containers requiring consistent wall thickness and lightweight strength. However, the nature of hollow parts means they may match a different level of detail and surface finish than injection-molded parts.
Technological Advancements
Injection Molding Innovations
Recent advancements in injection molding technology include:
- 3D Printing of Molds: Rapid prototyping of molds using 3D printing reduces lead times and costs.
- Multi-Material Molding: The ability to mold parts with multiple materials or colors in a single cycle.
- Micro-Molding: Precision molding of tiny, detailed parts for medical and electronic applications.
Blow Molding Innovations
Blow molding has also seen significant technological improvements, such as:
- Continuous Extrusion: Enhancements in continuous extrusion processes for higher efficiency.
- Improved Parison Control: Better control over parison thickness for more consistent wall thickness.
- Sustainable Materials: Development of biodegradable and recyclable materials for eco-friendly packaging solutions.
Environmental Considerations
Sustainability in Injection Molding
Injection molding companies are increasingly adopting sustainable practices, including:
- Recycling: Reusing scrap plastic and incorporating recycled materials into production.
- Energy Efficiency: Implementing energy-efficient machines and processes to reduce carbon footprint.
- Biodegradable Plastics: Using biodegradable and bio-based plastics for environmentally friendly products.
Sustainability in Blow Molding
Blow molding also contributes to sustainability through the following:
- Material Optimization: Designing products with minimal material use without compromising strength.
- Recyclability: Producing recyclable containers and using post-consumer recycled plastics.
- Energy Savings: Investing in energy-efficient blow molding equipment and processes.
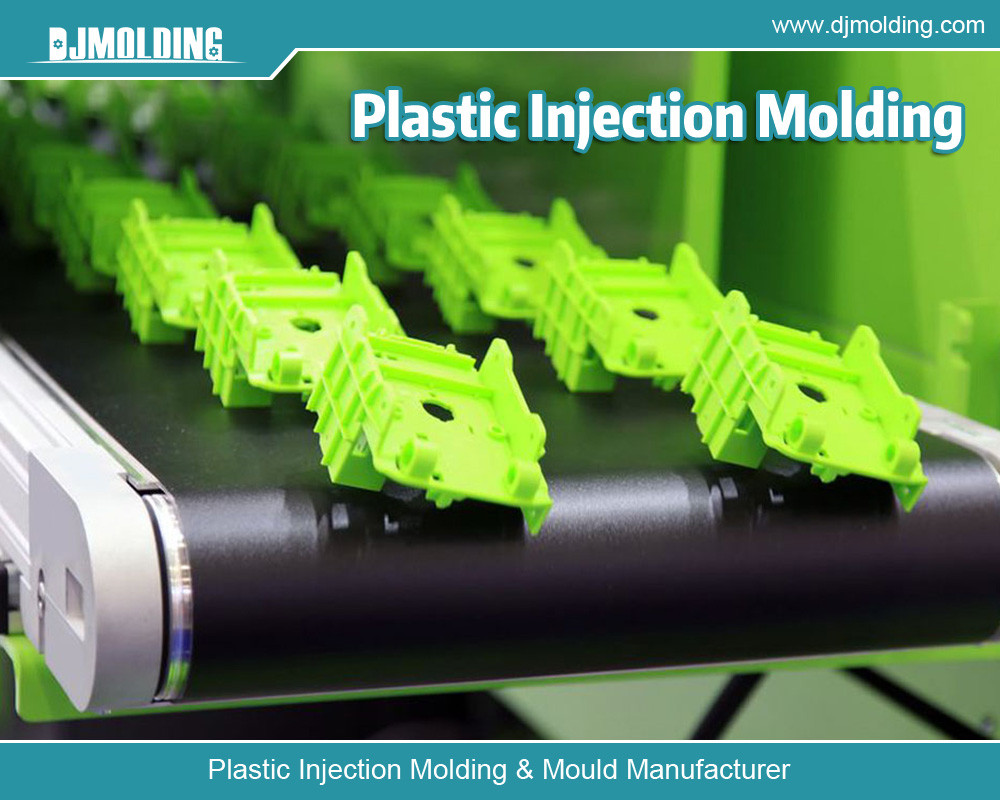
Conclusion
Both injection and blow molding are indispensable in plastic manufacturing, each offering unique advantages tailored to specific applications. Injection molding produces intricate, solid parts with high precision and efficiency, making it ideal for various industries. Blow molding, which creates hollow, lightweight products, is essential for packaging and automotive applications.
Choosing between injection molding and blow molding depends on various factors, including product design, material requirements, production volume, and cost considerations. Understanding the strengths and limitations of each process enables manufacturers to make informed decisions, ensuring optimal product quality, efficiency, and sustainability.
In the ever-evolving landscape of plastic manufacturing, technological advancements and a growing emphasis on sustainability continue to shape the future of injection molding and blow molding, driving innovation and eco-friendly practices across industries. Whether crafting intricate components or essential containers, these molding techniques will remain at the forefront of plastic production, meeting the diverse needs of modern markets.
For more about injection molding vs blow molding: a comprehensive comparison,you can pay a visit to Djmolding at https://www.djmolding.com/the-difference-between-plastic-injection-molding-and-extrusion/ for more info.