How To Speed Up Injection Molding Cooling And Cycle Time
How To Speed Up Injection Molding Cooling And Cycle Time
Injection molding is a widely used manufacturing process that involves injecting molten plastic into a mold to create various parts and products. One of the critical aspects of this process is cooling, which directly affects the cycle time and, consequently, production efficiency and cost. Optimizing the cooling phase can significantly improve cycle time, product quality, and overall productivity. This article explores various strategies and technologies to speed up the cooling and cycle time of injection molding.
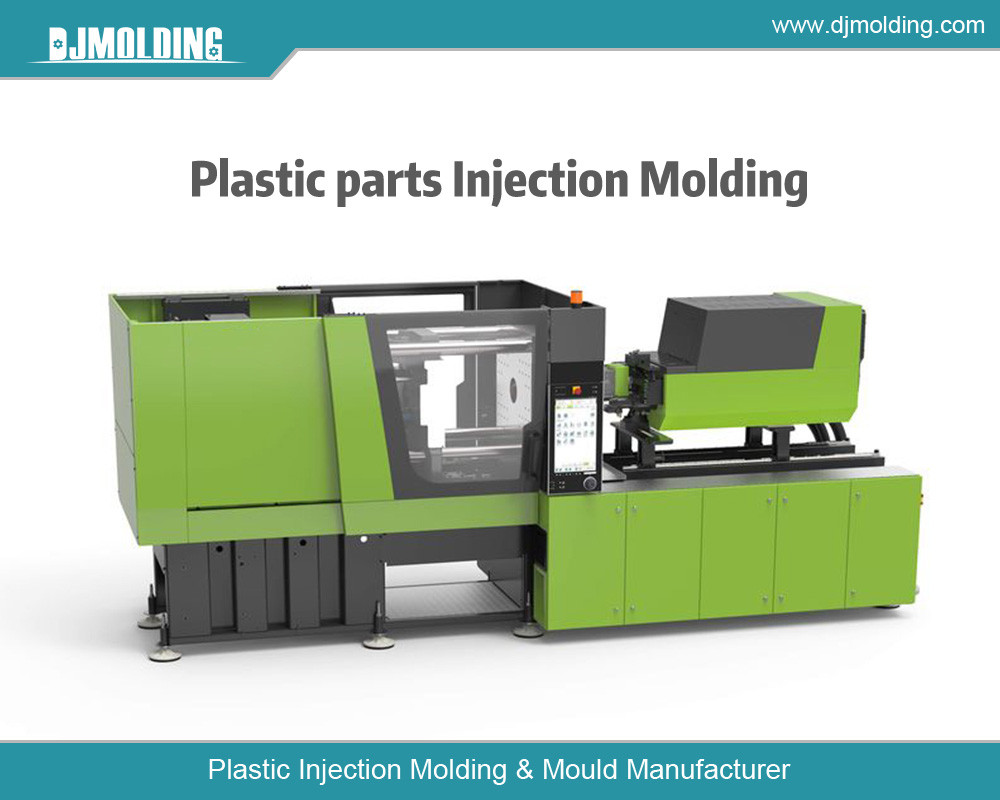
Understanding the Injection Molding Process
Overview of Injection Molding
Injection molding consists of several stages: melting the plastic material, injecting it into the mold, cooling the material, and finally ejecting the finished part. The cooling phase is crucial because it often consumes much of the total cycle time. Efficient cooling is essential to achieve high-quality products with minimal defects.
Importance of Cooling in Injection Molding
Cooling is critical for solidifying the molten plastic and ensuring the final product retains its desired shape and properties. Inadequate cooling can lead to defects such as warping, shrinkage, and internal stresses, compromising product quality. Therefore, optimizing the cooling phase is vital for reducing cycle time and enhancing product quality.
Factors Affecting Cooling Time
Material Properties
Different plastic materials have varying thermal properties, which influence cooling time. For instance, crystalline plastics like polypropylene and polyethylene cool more slowly than amorphous plastics like polystyrene and ABS. Understanding the material’s thermal properties is essential for optimizing the cooling process.
Mold Design
The design of the mold plays a significant role in determining cooling efficiency. Factors such as mold material, wall thickness, and cooling channels impact how quickly heat is dissipated from the molten plastic. Molds with efficient cooling channels can significantly reduce cooling time.
Cooling System
The effectiveness of the cooling system is crucial for rapid heat dissipation. The cooling system typically involves water or other cooling fluids circulated through channels in the mold. The cooling fluid’s flow rate, temperature, and pressure all influence the cooling efficiency.
Strategies to Speed Up Cooling Time
Optimizing Mold Design
Incorporating Conformal Cooling Channels
Conformal cooling channels are designed to follow the contours of the mold cavity, providing more uniform and efficient cooling. Unlike traditional straight-line cooling channels, conformal channels enhance heat transfer and reduce cooling time. Additive manufacturing techniques like 3D printing can create molds with complex conformal cooling channels.
Using High Thermal Conductivity Materials
Mold materials with high thermal conductivity, such as aluminum or beryllium-copper alloys, can significantly enhance cooling efficiency. These materials allow faster heat transfer from the plastic to the cooling fluid, reducing cooling time.
Enhancing Cooling System Efficiency
Improving Cooling Fluid Flow
Increasing the flow rate of the cooling fluid can enhance heat transfer and reduce cooling time. However, it is essential to balance flow rate with pressure and temperature to prevent issues such as cavitation and erosion of cooling channels.
Utilizing Advanced Cooling Fluids
Advanced cooling fluids with better thermal properties than water, such as glycol-water mixtures or specialized thermal oils, can improve cooling efficiency. These fluids have higher heat capacities and thermal conductivities, leading to faster cooling.
Implementing Advanced Technologies
Heat Pipes and Heat Exchangers
Heat pipes and heat exchangers can be integrated into the mold to improve heat dissipation. Heat pipes use the phase change of a working fluid to transfer heat efficiently, while heat exchangers can provide a large surface area for heat transfer. These technologies can significantly reduce cooling time by enhancing heat removal from the mold.
Rapid Heat and Cool Molding
Rapid heat and excellent molding involve rapidly heating the mold surface during the injection phase and cooling it quickly during the cooling phase. This technique reduces cycle time and improves part quality by minimizing defects such as weld lines and surface marks. Advanced heating methods, such as induction and high-frequency electrical heating, can achieve rapid mold heating.
Process Optimization Techniques
Simulation and Modeling
Using simulation software to model the injection molding process can help identify areas for improvement in cooling efficiency. Simulations can predict temperature distribution, cooling times, and potential defects, allowing for optimization of mold design and cooling system parameters.
Process Monitoring and Control
Implementing advanced process monitoring and control systems can enhance cooling efficiency. Sensors can monitor temperature, pressure, and flow rates in real-time, allowing for precise control of the cooling process. Automated systems can adjust cooling parameters dynamically to maintain optimal conditions and reduce cycle time.
Benefits of Reducing Cooling and Cycle Time
Increased Production Efficiency
Reducing cooling and cycle time directly increases production efficiency by allowing more parts to be produced in a given period. This leads to higher output and lower per-unit costs, enhancing overall profitability.
Improved Product Quality
Optimizing the cooling process can improve product quality by reducing defects such as warping, shrinkage, and internal stresses. Uniform and efficient cooling ensures that parts have consistent dimensions and mechanical properties.
Reduced Energy Consumption
Efficient cooling systems consume less energy, saving costs and reducing environmental impact. By optimizing the cooling phase, manufacturers can achieve more sustainable production processes.
Competitive Advantage
Manufacturers who can quickly and efficiently produce high-quality parts gain a competitive advantage in the market. Reducing cycle time and improving product quality can attract and retain new customers.
Case Studies and Real-World Examples
Case Study 1: Implementing Conformal Cooling Channels
A plastic parts manufacturer implemented conformal cooling channels in their molds using 3D printing technology. The new molds reduced cooling time by 30%, leading to a 20% increase in production efficiency. Additionally, the improved cooling uniformity reduced defects, enhancing product quality.
Case Study 2: Utilizing Advanced Cooling Fluids
Another manufacturer switched from water to a glycol-water mixture as the cooling fluid. The advanced cooling fluid improved heat transfer and reduced cooling time by 25%. The change also resulted in more consistent product quality and reduced energy consumption.
Case Study 3: Rapid Heat and Cool Molding
A company producing automotive components adopted rapid heat and cool molding technology. By rapidly heating the mold surface during injection and cooling it quickly, they reduced cycle time by 40% and significantly improved the parts’ surface finish and dimensional accuracy.
Challenges and Considerations
Cost Implications
Implementing advanced cooling technologies and optimizing mold designs can involve significant upfront costs. Manufacturers must weigh the potential benefits against the required investment and consider the long-term return on investment.
Technical Expertise
Advanced cooling techniques and technologies require specialized knowledge and expertise. Manufacturers may need to invest in training and hire skilled personnel to implement and maintain these systems effectively.
Maintenance and Reliability
Enhanced cooling systems and molds with complex designs may require more frequent maintenance and monitoring. Ensuring their reliability and longevity is essential to avoid disruptions in production.
Future Trends in Injection Molding Cooling
Integration of IoT and Industry 4.0
Integrating the Internet of Things (IoT) and Industry 4.0 technologies in injection molding is expected to revolutionize the cooling process. Smart sensors and connected devices can provide real-time data and insights, enabling more precise control and optimization of the cooling phase.
Development of New Materials
Advances in material science may lead to the development of new mold materials and cooling fluids with superior thermal properties. These innovations can further enhance cooling efficiency and reduce cycle time.
Adoption of AI and Machine Learning
Artificial intelligence (AI) and machine learning can analyze data from the injection molding process and optimize cooling parameters dynamically. These technologies can predict and prevent defects, improving product quality and reducing cycle time.
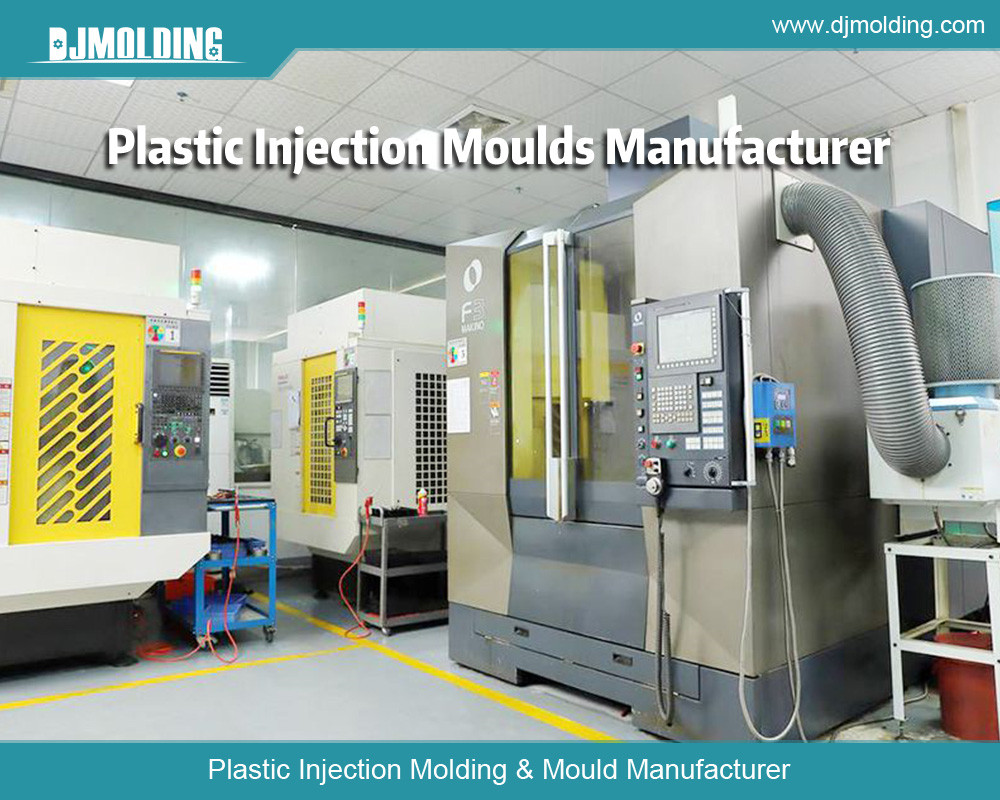
Conclusion
Speeding up injection molding cooling and cycle time is crucial for enhancing production efficiency, reducing costs, and improving product quality. Manufacturers can significantly improve their injection molding processes by optimizing mold design, enhancing cooling system efficiency, and implementing advanced technologies. The future holds exciting possibilities with the integration of IoT, new materials, and AI, promising even more significant advancements in cooling efficiency and cycle time reduction. As manufacturers continue to innovate and adopt these strategies, the injection molding industry will become more efficient, sustainable, and competitive.
For more about how to speed up injection molding cooling and cycle time, you can pay a visit to Djmolding at https://www.djmolding.com/what-is-the-plastic-injection-molding-cycle-time/ for more info.