How Automotive Plastic Injection Molding Is Transforming The Automotive Industry
How Automotive Plastic Injection Molding Is Transforming The Automotive Industry
Plastic injection molding involves injecting molten plastics in a mold cavity to produce different plastic part and components. This process has been widely used in various industries, including the automotive industry, due to its efficiency and versatility.
Plastic injection molding history in the automotive industry dates back several decades. In the early days, metal was the primary material used for automotive parts. However, as the demand for lighter and more cost-effective components grew, manufacturers began exploring alternative materials. This led to the adoption of plastic injection molding, which offered numerous advantages over traditional metal manufacturing processes.
Advantages of Plastic Injection Molding in the Automotive Industry
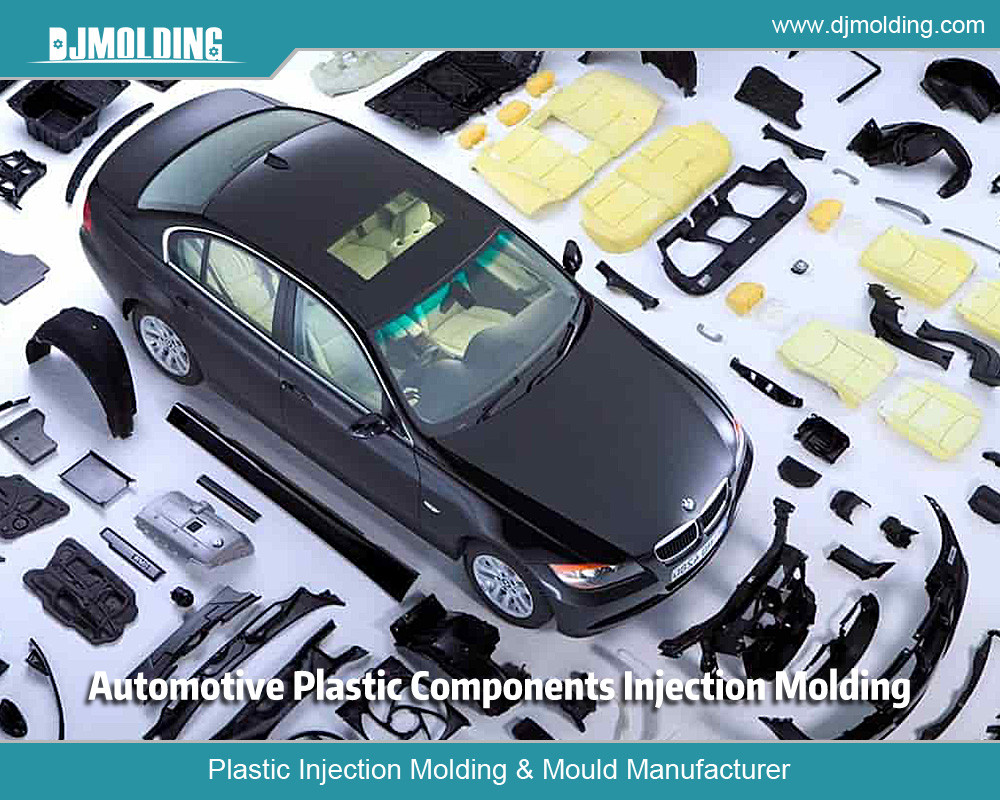
Cost-Effective Manufacturing with Plastic Injection Molding
When comparing plastic injection molding to other manufacturing processes, it becomes evident that it offers significant cost advantages. Machining, for example, requires extensive manual labor and often results in a substantial amount of material waste. On the other hand, plastic injection molding is highly automated, reducing labor costs and minimizing material waste.
Efficiency is another factor that contributes to the cost-effectiveness of plastic injection molding. The process ensures high-speed production, with multiple parts being produced simultaneously. This not only reduces production time but also increases overall output, resulting in lower costs per part.
The automotive industry has witnessed numerous examples of cost-effective plastic injection molding. One such example is the production of interior trim components, such as door panels and dashboard parts. By utilizing plastic injection molding, manufacturers can produce these parts at a fraction of the cost compared to traditional methods like metal stamping or vacuum forming.
Light weighting with Automotive Plastic Injection Molding
Light weighting has become a crucial focus in the automotive industry due to its potential for improving fuel efficiency and reducing emissions. Plastic injection molding plays a significant role in achieving light weighting goals by offering many advantages compared to traditional materials like metal.
Plastic injection molding allows for the creation of lightweight parts without compromising strength or durability. By utilizing advanced engineering plastics, manufacturers can design components that are both lightweight and robust enough to meet stringent safety requirements.
The automotive industry has seen numerous examples of light weighting with plastic injection molding.
One such example is the manufacture of lightweight interior components, such as seats and door panels. By replacing metal with lightweight plastics, manufacturers can significantly reduce the overall weight of the vehicle, resulting in improved fuel efficiency.
Design Flexibility with Plastic Injection Molding
Design flexibility is a key advantage of plastic injection molding in the automotive industry. The process allows for the manufacture of advanced shapes and designs which cannot be achieved with other methods.
The ability to mold intricate shapes and designs opens up a world of possibilities for automotive designers. From sleek exterior body panels to intricate interior components, plastic injection molding enables the manufacture of visually appealing and functional parts.
Furthermore, plastic injection molding offers customization options for automotive parts. Manufacturers can easily incorporate branding elements, such as logos or textures, directly into the mold, eliminating any need for additional post-processing steps.
The automotive industry has witnessed numerous examples of design flexibility with plastic injection molding. One such example is the production of complex exterior body panels, such as fenders and bumpers. By utilizing plastic injection molding, manufacturers can create parts with intricate shapes and contours that enhance aerodynamics and improve vehicle performance.
Improved Durability and Performance with Plastic Injection Molding
Plastic injection molding offers improved durability and performance for automotive parts compared to traditional manufacturing methods. The process allows for the development of parts with enhanced strength and resistance to impact, contributing to overall vehicle performance and safety.
The enhanced strength and durability of plastic parts are achieved through the use of advanced engineering plastics. These materials offer superior mechanical properties, such as high tensile strength and impact resistance, making them ideal for automotive applications.
Furthermore, plastic injection molding allows for the integration of reinforcement structures directly into the mold. This eliminates any need for additional assembly steps, resulting in parts with improved structural integrity and reduced risk of failure.
Environmental Benefits of Automotive Plastic Injection Molding
Plastic injection molding offers several environmental benefits in the automotive industry. The process helps reduce energy consumption, carbon emissions, and waste generation compared to traditional manufacturing methods.
One of the key environmental benefits is the reduced energy consumption associated with plastic injection molding. The process needs less energy compared to other manufacturing methods like machining or casting. Additionally, advancements in machines and technology have further improved energy efficiency, contributing to overall sustainability.
Furthermore, plastic injection molding helps reduce carbon emissions by minimizing material waste and optimizing production efficiency. The ability to mold complex shapes and designs allows for precise material usage, minimizing excess material and reducing waste generation.
Trends and Innovations in Automotive Plastic Injection Molding
The automotive industry is constantly evolving, and plastic injection molding is no exception. Advancements in materials and technology have opened up new possibilities for manufacturers, allowing them to produce innovative parts.
One key trend in automotive plastic injection molding is the development of advanced engineering plastics. These materials offer superior mechanical properties, such as high strength, impact resistance, and heat resistance, making them ideal for demanding automotive applications.
Additionally, the integration of automation and robotics has revolutionized the plastic injection molding process. Automated machinery allows for higher production speeds, improved precision, and reduced labor costs. Robotics further enhance efficiency by automating tasks such as part removal and quality inspection.
The automotive space has witnessed numerous innovations in plastic injection molding. One such innovation is the use of multi-shot or overmolding techniques.
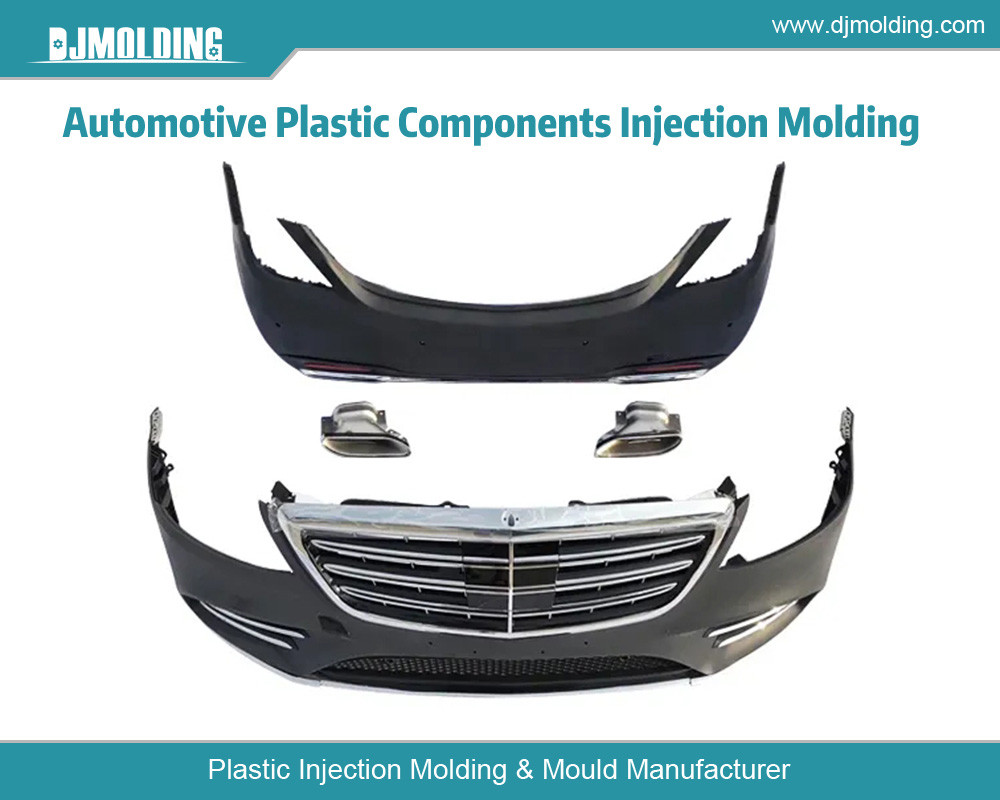
Plastic Injection Molding Impact on the Automotive Industry
In conclusion, plastic injection molding has had a significant impact on the automotive industry. Its advantages in terms of faster production time, lower costs, consistent quality, reduced waste, improved part strength, and durability have made it a preferred manufacturing process for automotive parts.
Plastic injection molding offers cost-effective manufacturing by reducing labor costs, material waste, and production time. It enables lightweighting, which contributes to improved fuel efficiency and reduced emissions. The design flexibility of plastic injection molding allows for the creation of complex shapes and customization options, enhancing both aesthetics and functionality.
Moreover, plastic injection molding offers improved durability and performance for automotive parts, ensuring their reliability and safety. The environmental benefits of plastic injection molding, such as reduced energy consumption, carbon emissions, and recyclability, contribute to overall sustainability.
For more about how automotive plastic injection molding is transforming the automotive industry,you can pay a visit to Djmolding at https://www.djmolding.com/automotive-plastic-components-injection-molding/ for more info.