Hot Runner Vs. Cold Runner In Injection Mold Design
Hot Runner Vs. Cold Runner In Injection Mold Design
Injection molding is a pivotal process in manufacturing, particularly for plastic components. The injection mold design significantly influences the efficiency, quality, and cost of production. One critical aspect of mold design is choosing between hot and cold runner systems. Each system has distinct advantages and disadvantages, making the decision highly dependent on the project’s specific requirements. This article delves into the details of hot and cold runner systems, comparing their functionalities, benefits, drawbacks, and applications.
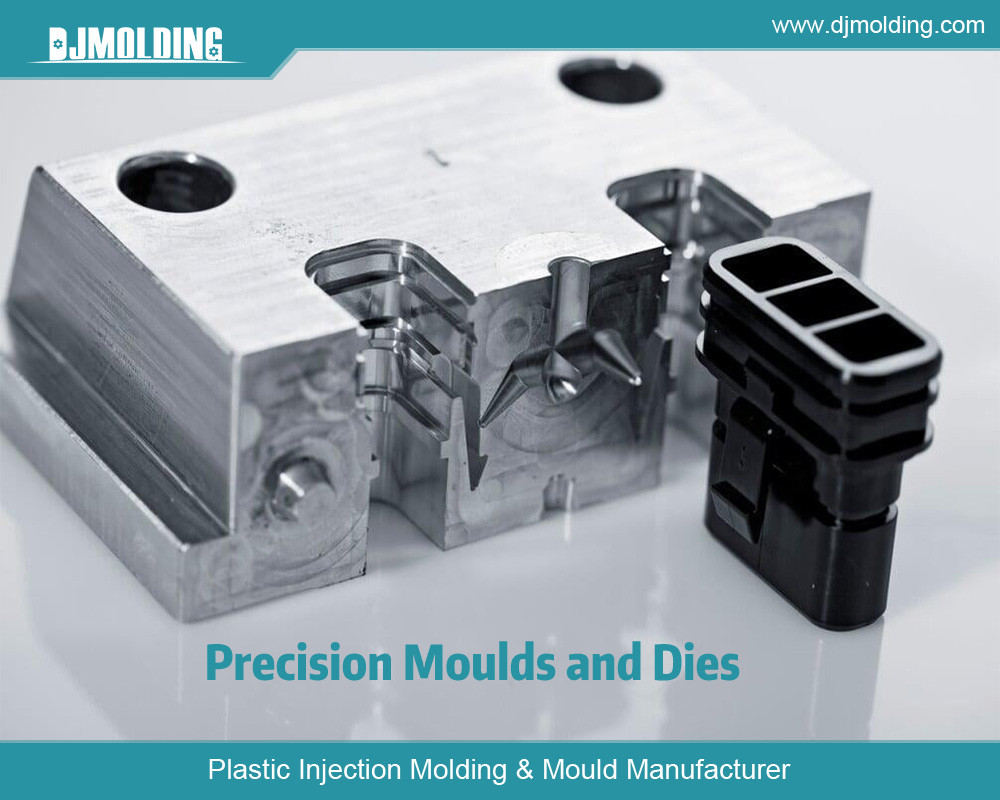
Understanding Injection Molding
Before exploring the differences between hot runner and cold runner systems, it’s essential to understand the basics of injection molding. Injection molding involves injecting molten plastic into a mold cavity, which cools and solidifies into the desired shape. The process is repeated to produce multiple identical parts, making it ideal for mass production. The runner system is crucial in this process, as it guides the molten plastic from the injection unit to the mold cavities.
Hot Runner Systems
Definition and Components
A hot runner system keeps the plastic in a molten state within the runner, allowing continuous flow into the mold cavities without solidifying. This system consists of several key components:
- Manifold: Distributes the molten plastic to various cavities through channels.
- Heated Nozzles: Direct the molten plastic into the mold cavities while maintaining temperature.
- Temperature Controllers: Ensure precise temperature regulation to prevent material degradation.
Advantages
- Reduced Waste: Since the runner remains hot and molten, there is no solidified plastic to discard, minimizing material waste.
- Improved Efficiency: Eliminating runner solidification reduces cycle time, enhancing production efficiency.
- Better Quality: Consistent temperature control reduces defects such as warping, shrinkage, and surface blemishes.
- Design Flexibility: Allows for more complex part designs due to the precise flow and temperature control.
Disadvantages
- Higher Initial Cost: Hot runner systems are more expensive to design, manufacture, and install.
- Complex Maintenance: The system requires regular maintenance to ensure proper functioning, adding to operational costs.
- Potential for Thermal Degradation: High temperatures can degrade the plastic material if not adequately controlled, affecting part quality.
Applications
Hot runner systems are ideal for high-volume production of complex, high-quality parts, such as automotive components, consumer electronics, and medical devices. They are particularly beneficial when reducing material waste and cycle time is critical.
Cold Runner Systems
Definition and Components
In contrast, A cold runner system allows the runner’s plastic to solidify along with the parts. The system typically includes:
- Sprue: The main channel through which the molten plastic enters the runner system.
- Runners: Channels that distribute the plastic to various mold cavities.
- Gates: Small openings that direct the plastic from the runner into the mold cavities.
Advantages
- Lower Initial Cost: Cold runner systems are more straightforward and cheaper to design and manufacture.
- Ease of Maintenance: Maintenance is straightforward and less costly, with fewer components and no need for heating elements.
- Versatility: Suitable for a wide range of materials, including those that are heat-sensitive.
Disadvantages
- Increased Waste: The runner solidifies with each cycle, resulting in material waste unless the runner is recycled.
- Longer Cycle Time: The need to cool and eject the solidified runner extends the cycle time, reducing production efficiency.
- Quality Issues: Variability in cooling can lead to defects such as warping and shrinkage, affecting part quality.
Applications
Cold runner systems are suitable for low to medium-volume production and are commonly used for simpler parts. They are prevalent in industries with significant cost constraints, such as consumer goods and packaging.
Comparative Analysis
Cost Considerations
While hot runner systems have higher upfront costs, they offer long-term savings through reduced material waste and shorter cycle times. Cold runner systems, being cheaper to set up, incur higher operational costs over time due to material waste and longer production cycles. The choice depends on the balance between initial investment and long-term operational efficiency.
Production Volume and Part Complexity
Hot runner systems are generally more advantageous for high-volume production of complex parts. They support intricate designs and ensure consistent quality across large batches. Cold runner systems are more suited for lower volume production and more superficial parts, where the complexity of a hot runner system may not be justified.
Material Considerations
Some materials are more sensitive to temperature and can degrade if subjected to prolonged heat, making cold runner systems preferable. Conversely, materials that can withstand the heat without degradation benefit from the efficiency of hot runner systems.
Environmental Impact
Hot runner systems are more environmentally friendly due to reduced material waste. Cold runner systems can mitigate their environmental impact by incorporating recycling processes for the solidified runners.
Technological Advances and Innovations
Enhanced Temperature Control
Advances in temperature control technology have made hot runner systems more reliable and efficient. Modern temperature controllers offer precise regulation, reducing the risk of material degradation and improving part quality.
Hybrid Runner Systems
Some manufacturers are exploring hybrid systems that combine hot and cold runner systems elements. These systems aim to optimize both benefits, offering improved efficiency and flexibility in various production scenarios.
Simulation Software
Injection molding simulation software has become an invaluable tool for mold designers. These programs allow for the virtual testing of both hot and cold runner systems, helping designers identify potential issues and optimize the mold design before production begins.
Case Studies
Automotive Industry
Hot runner systems have proven highly effective in the automotive industry, where high-volume production and part complexity are expected. For instance, producing intricate dashboard components and under-the-hood parts benefits from the reduced cycle time and improved quality control offered by hot runner systems.
Medical Devices
The medical device industry demands high precision and quality. Hot runner systems are often preferred for producing complex medical components, such as surgical instruments and diagnostic devices, where material waste and defects are unacceptable.
Consumer Goods
Cold runner systems are often the go-to choice for lower-volume production and simpler designs in the consumer goods industry. Items such as plastic containers, household items, and toys are commonly produced using cold runner systems due to their cost-effectiveness and simplicity.
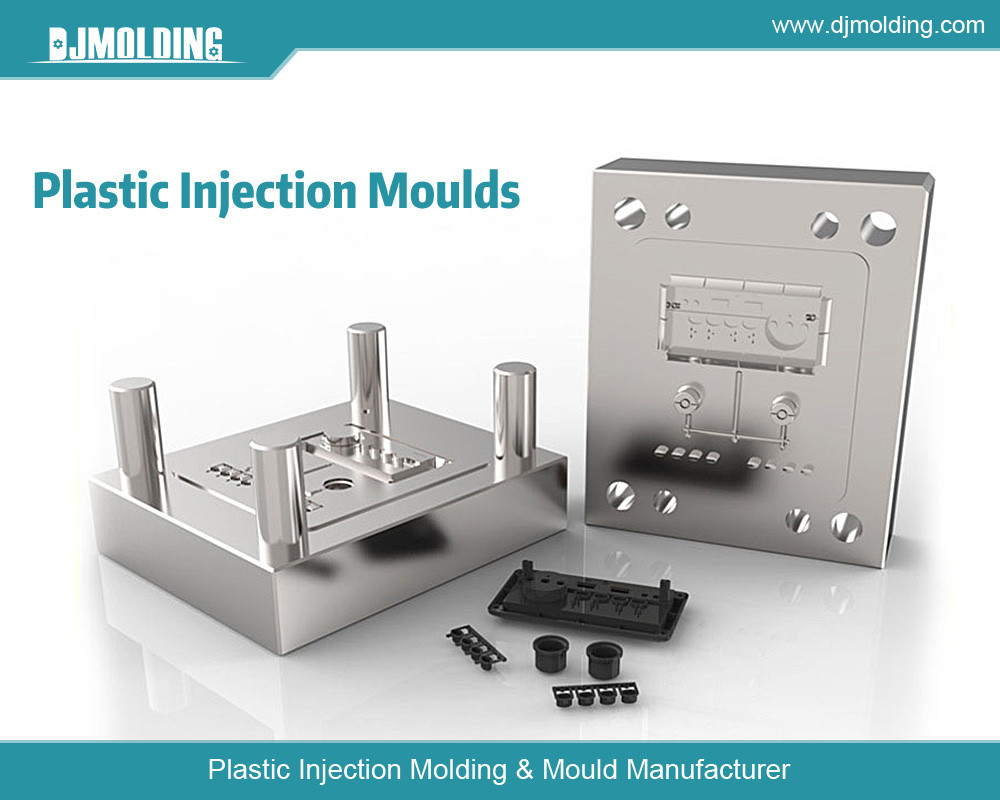
Conclusion
Choosing between hot and cold runner systems in injection mold design is a critical decision that impacts production efficiency, cost, and product quality. Hot runner systems offer significant advantages in reduced waste, improved efficiency, and superior part quality, making them ideal for high-volume and complex parts. However, they come with higher initial costs and maintenance complexity. Cold runner systems, while more straightforward and cheaper to set up, may incur higher operational costs due to material waste and longer cycle times. Still, they are versatile and easier to maintain.
Ultimately, the decision should be based on a thorough analysis of the specific production requirements, including volume, part complexity, material properties, and budget constraints. By understanding the strengths and weaknesses of each system, manufacturers can make informed choices that optimise their production processes and meet their quality standards.
For more about hot runner vs. cold runner in injection mold design,you can pay a visit to Djmolding at https://www.djmolding.com/everything-you-need-to-know-about-hot-runner-plastic-injection-molding/ for more info.