High Volume Plastic Injection Molding For High-Volume Manufacturing: What It Is And How It Works
High Volume Plastic Injection Molding For High-Volume Manufacturing: What It Is And How It Works
High volume injection molding is a manufacturing process that uses an injection molding machine to create large quantities of plastic parts quickly and efficiently. This process is ideal for producing complex parts with tight tolerances, making it a popular choice for various industries. In this blog post, we will discuss what high volume injection molding is, the benefits of using this method, how it works, and the materials commonly used.
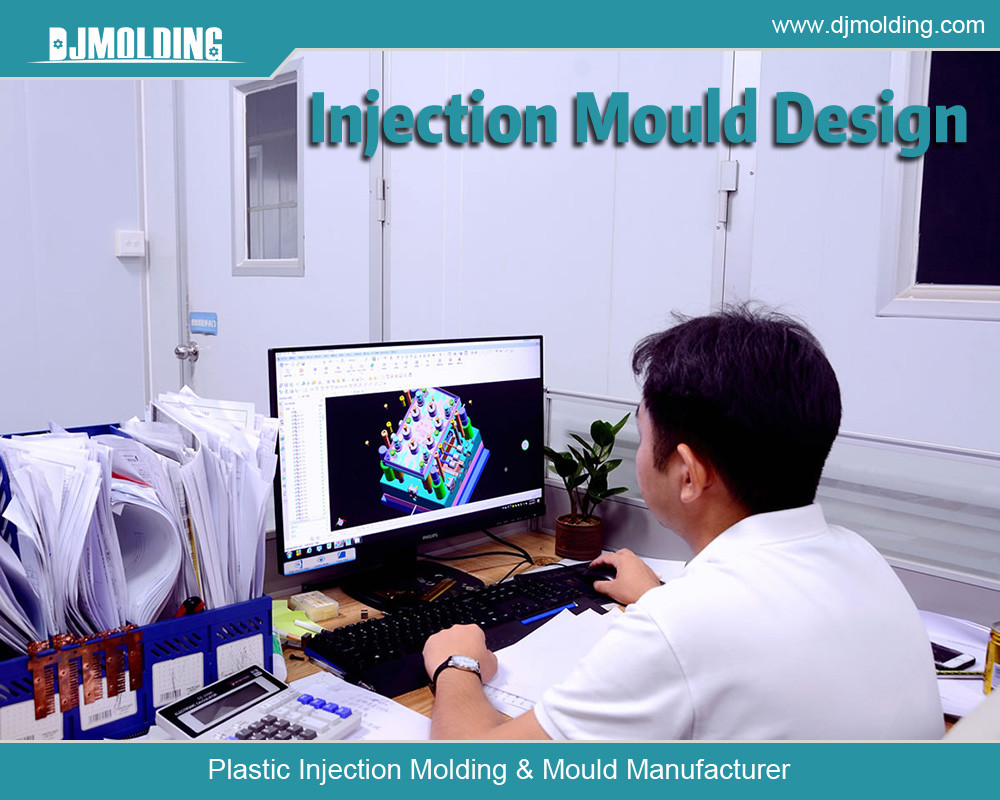
What is High Volume Injection Molding?
Definition and Explanation
High volume injection molding is a manufacturing process that involves injecting molten plastic into a mold to create a specific shape. Under high pressure, the injection of molten plastic into the mold fills it and produces the desired part. Manufacturers use this process to create large quantities of plastic parts quickly and efficiently.
Benefits of High Volume Injection Molding
High volume injection molding offers a wide range of benefits, including:
- Cost-effective: This process efficiently produces large quantities of plastic parts at a low cost per unit.
- High accuracy: The process has high-quality parts, making it ideal for complex parts with tight tolerances.
- Large production capacity: This process can produce large quantities of features quickly and efficiently.
- Repeatable quality: The process has parts with consistent quality, ensuring that every piece is the same.
Common Applications
Various industries utilize high volume injection molding, including automotive, electronics, medical, and consumer products. Common applications include:
- Automotive parts: Plastic parts used in cars, such as dashboards, consoles, and door panels.
- Electronic parts: Plastic parts used in electronics, such as casings for phones and computers.
- Medical parts: Plastic parts used in medical equipment, such as syringes, tubing, and connectors.
- Consumer products: Plastic parts used in household products, such as toys, kitchen appliances, and furniture.
How High Volume Injection Molding Works
High volume injection molding is a highly efficient manufacturing process used to create large quantities of plastic parts quickly and effectively. To understand how high volume injection molding works, one must take a closer look at the various components of the machine, the steps involved in the injection molding process, and the role of the mold.
The Injection Molding Machine
The injection molding machine consists of three main parts: the injection unit, the mold, and the clamp unit. The injection unit is responsible for melting the plastic and injecting it into the mold while the mold shapes the plastic into the desired form. The clamp unit holds the mold and applies pressure to the plastic as it cools and solidifies. These three parts work together to create a seamless manufacturing process.
The Injection Molding Process
The injection molding process comprises several vital steps, including clamping, injection, cooling, and ejection. Each step is critical to ensuring a successful and efficient manufacturing process. During the clamping stage, the clamp unit holds the mold in place. Next, the plastic is melted in the injection unit and injected into the mold under high pressure. The plastic cools and solidifies in the mold, and then we eject the finished part.
The Role of the Mold
The mold plays a critical role in the injection molding process, determining the shape and size of the finished part. We can make it from various materials, including steel, aluminum, and copper. The mold is designed to withstand the high pressures and temperatures involved in the injection molding process and must be carefully constructed and maintained to ensure consistent, high-quality parts.
Materials Used in High Volume Injection Molding
Types of Plastic Materials
The plastic materials used in high volume injection molding must have specific characteristics to ensure a successful manufacturing process. These characteristics include melt flow rate, shrinkage, and thermal conductivity. Some of the commonly used plastics include:
- Polypropylene (PP)
- Acrylonitrile Butadiene Styrene (ABS)
- Polycarbonate (PC)
- Polyethylene (PE)
- Polyvinyl Chloride (PVC)
Additives and Fillers
To enhance the properties of the plastic material, additives, and fillers are often added during the injection molding process. These include flame retardants, colorants, and reinforcements like glass or carbon fibers. Adding these materials can improve the final product’s strength, durability, and aesthetics.
Comparison of Materials
Different materials have strengths and weaknesses; manufacturers must choose the best material for their specific application. For example, ABS is a popular choice for automotive parts due to its impact resistance and ability to withstand extreme temperatures. Meanwhile, packaging often utilizes PP (polypropylene) due to its flexibility and low cost.
Factors to Consider in High Volume Injection Molding
Cost Considerations
Cost is critical in high volume injection molding, and manufacturers must consider several factors affecting the overall cost. These factors include the part’s complexity, the material used, and the size of the production run. High volume injection molding can be efficient and cost-effective, and some projects may have better choices. Manufacturers must weigh these factors against the potential benefits of using high volume injection molding.
Some cost considerations to keep in mind when using high volume injection molding include the following:
- The part’s complexity: Complex features require more time and resources to manufacture, which can increase the cost.
- The material used: Certain materials may be more expensive than others, and the cost can vary depending on the type of material and its properties.
- The size of the production run: The larger the production run, the more cost-effective high volume injection molding becomes.
By carefully evaluating these factors, manufacturers can determine whether high volume injection molding is the most cost-effective choice for their project.
Design Considerations
Design is a crucial factor in high volume injection molding, as it can significantly impact the quality and consistency of the final product. Designers must consider wall thickness, draft angles, and gate placement to ensure a successful manufacturing process. Using computer-aided design (CAD) software can help designers optimize their designs for injection molding.
Some design considerations to keep in mind when using high volume injection molding include the following:
- Wall thickness: Thicker walls can increase the strength and durability of the part but can also increase the cost of the molding process.
- Draft angles: Draft angles help the part release from the mold more efficiently, reducing the risk of defects and improving the final product’s quality.
- Gate placement: The placement of the gate can affect the flow of plastic into the mold, which can impact the quality and consistency of the part.
By carefully considering these design factors, manufacturers can optimize their designs for high volume injection molding and achieve the desired quality and consistency in the final product.
Quality Considerations
Ensuring consistent quality is essential in high volume injection molding. Manufacturers must carefully monitor the injection molding process, including controlling the temperature and pressure of the molding machine and inspecting the parts for defects. Quality control measures can minimize waste and ensure the final product meets the specifications.
Some quality considerations to keep in mind when using high volume injection molding include the following:
- Temperature and pressure control: The temperature and pressure of the molding machine can significantly impact the quality and consistency of the final product. Manufacturers must carefully monitor and control these factors to ensure consistent quality.
- Inspection: Inspecting the parts for defects is critical to ensure consistent quality. Manufacturers may use automated or visual inspection equipment to identify weaknesses and prevent them from being shipped to customers.
- Continuous improvement: High volume injection molding is an iterative process, and manufacturers should continuously evaluate and improve their processes to ensure consistent quality and minimize waste.
By implementing these quality control measures, manufacturers can optimize their high volume injection molding process and achieve the desired quality and consistency in the final product.
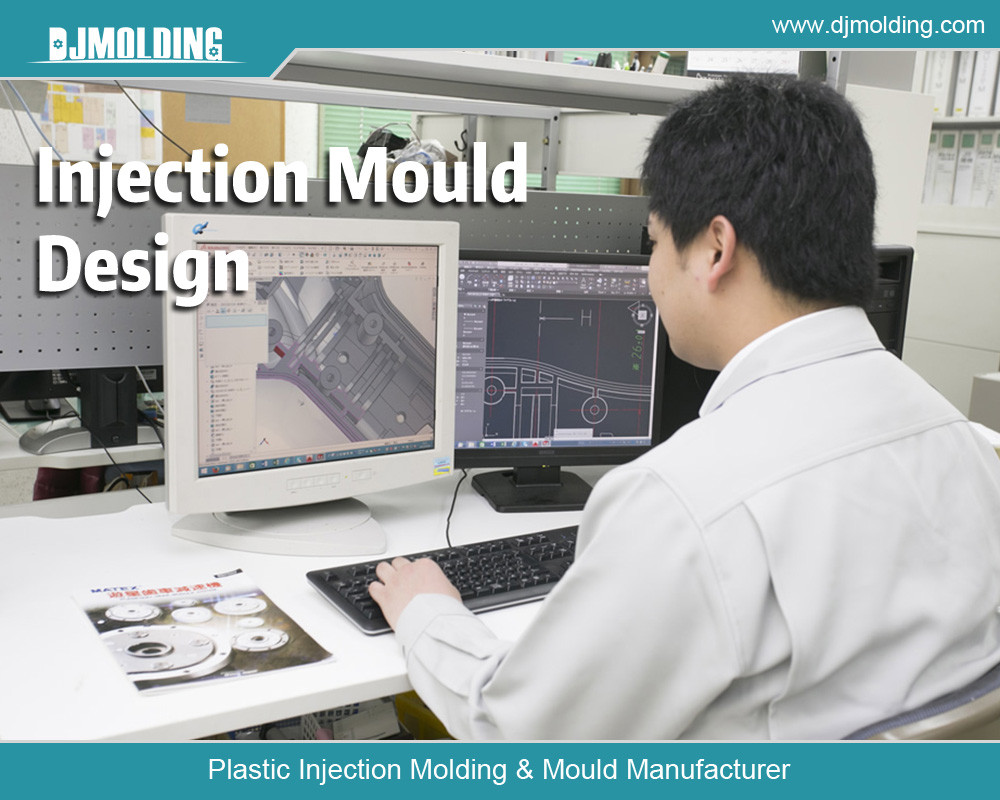
Conclusion
High volume injection molding is a versatile and efficient process for producing large quantities of plastic parts with consistent quality. By understanding the process and the materials involved, manufacturers can make informed decisions about whether high volume injection molding is the right choice for their product. With its ability to produce complex parts with tight tolerances, this process offers various industries a wide range of benefits.
For more about high volume plastic injection molding for high-volume manufacturing: what it is and how it works,you can pay a visit to Djmolding at https://www.djmolding.com/high-volume-injection-molding/ for more info.