High-Volume Manufacturing With High Volume Injection Molding: Streamlining Mass Production Efficiency
High-Volume Manufacturing With High Volume Injection Molding: Streamlining Mass Production Efficiency
Unleashing the Power of Efficiency in Mass Production In today’s fast-paced manufacturing landscape, efficiency is paramount. The ability to produce high-quality products quickly and cost-effectively is a goal shared by manufacturers worldwide. One method that has revolutionized mass production is high volume injection molding. By leveraging this technique, manufacturers can streamline operations and achieve remarkable efficiency. This article will delve into high volume injection molding, shedding light on its benefits, processes, and optimization strategies for enhanced manufacturing efficiency.
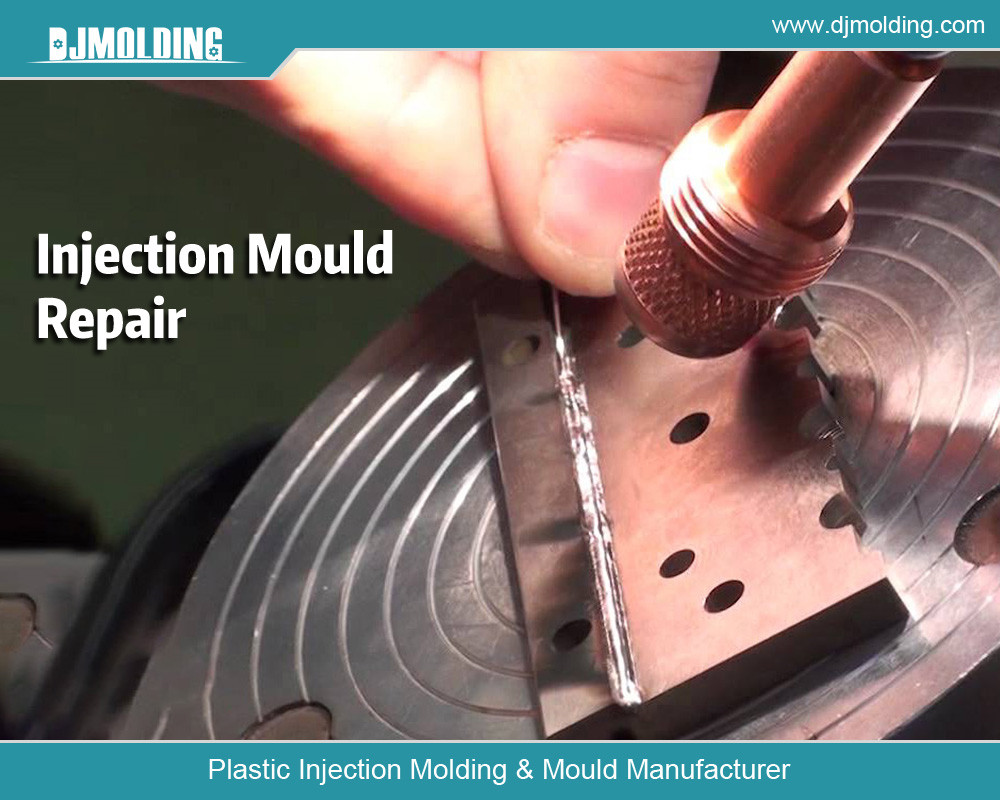
Applications of High Volume Injection Molding in Various Industries
High volume injection molding is a popular manufacturing process that involves injecting molten material into a mold cavity at high pressures. Here are some essential points to understand about this method:
- High volume injection molding is a versatile process suitable for various materials, including plastics, metals, and composites.
- The process involves injecting molten material into a mold cavity at high pressures, solidifying it, and producing a finished product.
- This method offers several advantages, including cost-effectiveness in mass production, high efficiency, design flexibility, and versatility.
- The per-unit cost decreases significantly with larger production volumes, making it ideal for mass production.
- High volume injection molding enables the production of complex and intricate designs with high precision and consistent quality.
- Various industries use this method to produce identical parts with high precision and quality standards.
- Products suitable for high volume injection molding include consumer goods, automotive components, medical devices, and electronic enclosures.
Techniques and Considerations for High Volume Injection Molding
High volume injection molding is a complex process that requires careful consideration of several factors, including material selection, design optimization, tooling, and automation. Here are some crucial points to keep in mind:
Material Selection and Design Optimization
- Material selection is critical in achieving the end product’s desired properties and performance requirements.
- When choosing materials, one should consider strength, flexibility, heat resistance, and durability.
- Design optimization techniques such as part consolidation, ribbing, and wall thickness optimization can enhance injection molding by improving mold filling and minimizing defects.
- Manufacturers must balance material selection and design optimization to achieve efficient production while meeting cost targets.
Tooling and Automation
- Tooling is a fundamental aspect of high volume injection molding and directly impacts the final product’s quality and consistency.
- High-quality molds that can withstand the pressures and temperatures involved in injection molding are crucial.
- Automation can improve production efficiency by handling tasks such as material feeding, mold closing, and part ejection, reducing manual labor and enhancing overall productivity.
- Regular maintenance and quality control are essential to ensure optimal performance and minimize downtime.
- Manufacturers must invest in the proper tooling and automation systems to achieve their production goals while staying within budget constraints.
Process Optimization and Cycle Time Reduction
Efficiency is essential in high-volume injection molding, and process optimization is crucial in achieving efficiency and streamlining mass production. Manufacturers can analyze and adjust variables such as injection speed, pressure, temperature, and cooling time to optimize the process. By precisely controlling these variables, manufacturers can improve part quality, reduce waste, and minimize cycle times. Here are some techniques that can help in process optimization and cycle time reduction:
- Scientific molding techniques: Scientific molding is a systematic approach to injection molding that involves analyzing and controlling process variables to improve part quality and consistency. Manufacturers can optimize the process by adjusting variables such as injection speed, pressure, temperature, and cooling time through scientific molding techniques.
- Hot runner systems: Hot runner systems can improve productivity and reduce cycle times by eliminating the need for runners and gates. This system allows for directly injecting molten plastic into the mold cavity, reducing waste and improving part quality.
- Rapid mold cooling: Rapid mold cooling can help reduce cycle times by improving cooling time. Manufacturers can speed up the cooling process and shorten cycle times by using a cooling system that quickly circulates cool water through the mold.
Streamlining mass production efficiency requires process optimization and cycle time reduction. Manufacturers can improve part quality, reduce waste, and minimize cycle times by analyzing and adjusting injection speed, pressure, temperature, and cooling time. Hot runner systems and rapid mold cooling can enhance productivity and shorten cycle times, increasing efficiency and profitability.
Key strategies for process optimization
- Design for Manufacturability (DFM): Collaborate with designers and engineers to optimize the product design for injection molding. Consider factors such as draft angles, wall thickness, and parting lines to facilitate smooth mold filling and ejection.
- Scientific Molding: Adopt scientific molding principles to establish robust and repeatable processes. The process involves collecting and analyzing data to ensure consistent part quality and dimensional accuracy. We use this data to make informed decisions about optimizing process parameters.
- Mold Flow Analysis: Utilize computer-aided engineering (CAE) software to simulate the injection molding process and identify potential issues beforehand. Mold flow analysis helps optimize gate placement, minimize warpage, and ensure balanced mold filling for uniform part quality.
- Lean Manufacturing Practices: Implement lean manufacturing principles to eliminate waste and improve efficiency. Techniques such as 5S (Sort, Set in Order, Shine, Standardize, Sustain), Kanban systems, and continuous improvement methodologies like Six Sigma can optimize workflows and minimize non-value-added activities.
Ensuring Quality and Minimizing Defects in Injection Molding
Maintaining consistent quality is crucial in high volume injection molding, and quality assurance measures should be implemented throughout production. Here are some of the quality control measures that can help ensure high-quality products and minimize defects:
- Raw material inspection and testing: Regular inspection and testing of raw materials are necessary to ensure that they meet the required specifications and standards.
- In-process inspections: Inspection of the product during manufacturing is essential to identify any issues early on and prevent further production of defective products.
- Final product validation: By validating the final product, we ensure it meets the required specifications and standards before shipping it to the customer.
- Statistical process control (SPC) techniques: SPC techniques can help monitor and control process variations, reducing the likelihood of defects.
To minimize defects, manufacturers can also employ specific techniques, such as:
- Gate optimization: Ensuring the proper flow of plastic through the gate can reduce part stress, resulting in better part quality.
- Venting: Preventing air traps and gas entrapment through venting can help improve part quality.
- Mold temperature control: Controlling the mold temperature can minimize warpage and improve dimensional stability, resulting in better quality parts.
Emphasizing quality control measures such as using automated inspection systems, implementing traceability systems, and conducting periodic audits ensures adherence to quality standards and customer requirements. Manufacturers can increase customer satisfaction, reduce waste, and improve their bottom line by prioritizing quality assurance and defect minimization.
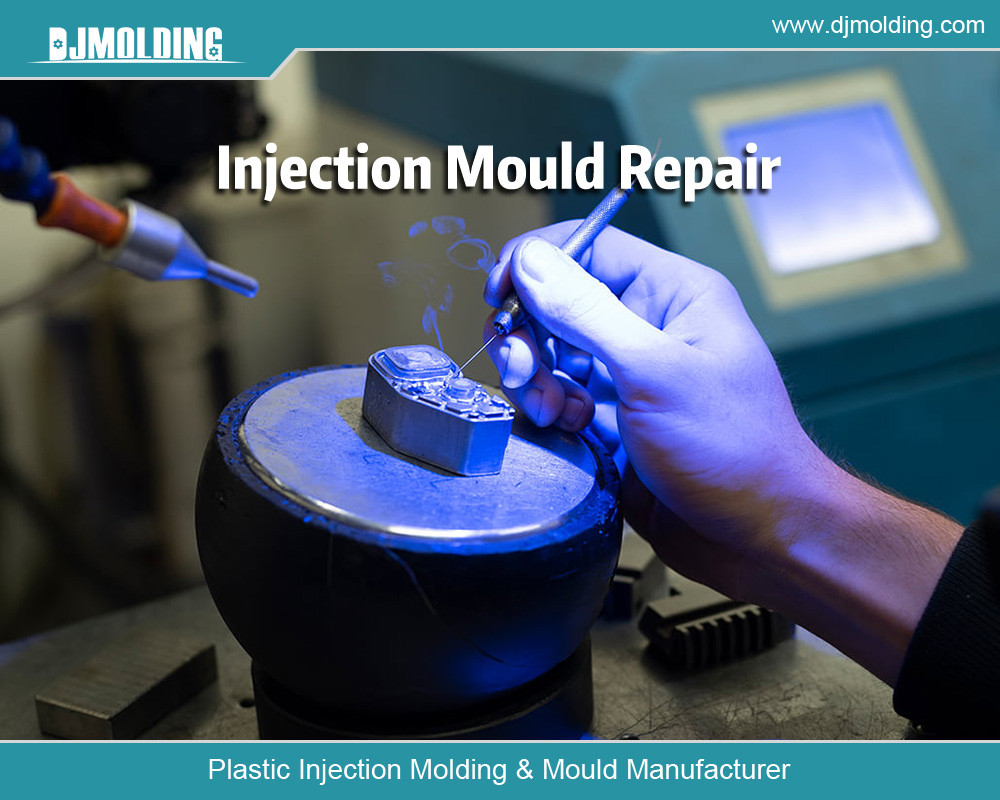
Conclusion
High volume injection molding is a powerful technique streamlining mass production processes, enabling manufacturers to achieve unparalleled efficiency, cost-effectiveness, and superior product quality. By understanding the principles and advantages of high volume injection molding, considering material selection and design optimization, leveraging tooling and automation, and implementing process optimization and quality control strategies, manufacturers can unlock the full potential of this method.
For more about high-volume manufacturing with high volume injection molding: streamlining mass production efficiency,you can pay a visit to Djmolding at https://www.djmolding.com/high-volume-injection-molding/ for more info.