High Volume Injection Molding
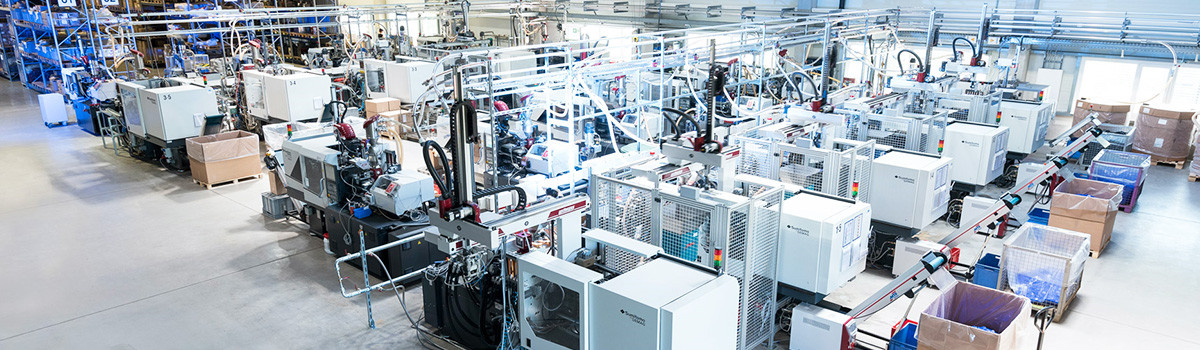
High volume injection molding(High-Volume Production): Plastic Injection Molding
With over thousands of plastic injection molding and plastic manufacturing facilities to choose from all over the word, what are one of the top qualities that make a molding company stand out? When choosing a provider, many factors should be taken into consideration; including capabilities, quality assurance, company reputation, cost, and delivery time. Finding the right plastic injection molder to fit your needs may seem time-consuming but determining your low and high-volume requirements first and how they may shift over time, will help to narrow down your options.
DJmolding’s High-Volume Injection Molding Service
At DJmolding, our production facility is a high-end, efficient operation with several machines and skilled operators. Due to our diverse equipment, we can handle a wide variety of jobs which greatly range in their industries, plastic quality, and the number of pieces produced. Low and high-volumes, from design through manufacturing, can be completed in-house which provides our customers with competitive advantages in cost, quality, and lead times.
DJmolding’s injection molding is a proven technique high-volume manufacturing processes. This is a specialized service offering full production-quality parts in volumes of up to millions of pieces a month. High-volume plastic injection molding allows for high-tolerance precision, low scrap loss, and cost savings.
Much of our high-volume molding equipment is computerized and uses mechanical systems to augment efficiencies and safeguard quality. Make sure to view our “Quality Control System” to see how we ensure quality control is incorporated in all high-volume production. This type of manufacturing is ideal for medium and large-sized businesses or mass production.
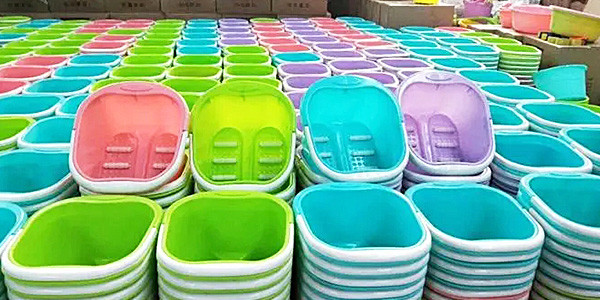
DJmolding’s High-Volume Injection Molding Advantages
*Produces more parts at a faster pace
*Reduce unit costs and cycle time for the manufacturer
*Accurate and consistent, high-quality mass production of parts
*Production can often be automated with solid, reliable machinery, even during non-work hours
*Minimal post-production work
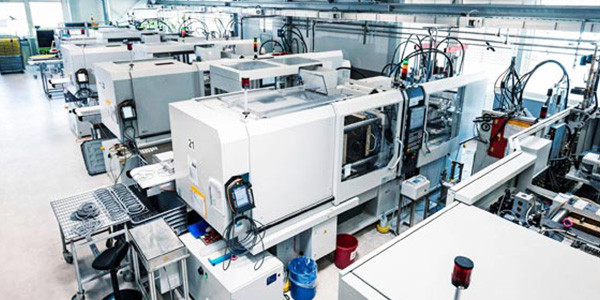
Customized High Volume Molding (Plastic Injection Prodtucts)
DJmolding’s custom molds and high volume molding include everything from prototypes to full production quantities. Our high volume molds, whether short-run, high-volume, or multiple-cavity, are monitored and controlled so you can be assured of all aspects of mold design and build. This attention to production detail certifies the goals, objectives, and preset project outcomes are on schedule throughout each stage of the process. All high volume molding, from design through manufacturing, is completed in house and provide our customers with competitive advantages in cost, quality, and lead times.
DJmolding works with client to design and engineer products, developing the most effective high volume molds for cost efficiency. We provide excellent quality high volume molds exclusive to the plastic injection molding industry, offering a wide range of services. From low volume molding, to insert molding, and pad printing, PTI, Inc. is the brand you can trust for your plastic injection molding services.
DJmolding prototype components for customers in distinct fields such as the medical, electrical, hand tool, communications, and automotive industries. Including injection and compression presses ranging from 85-500 Ton, much of DJmolding’s high volume molding equipment is computerized and uses mechanical systems to augment efficiencies and safeguard quality. At DJmolding we take a partnership attitude on every venture, bringing years of plastic injection molding knowledge and technical expertise in a facility designed to provide a comprehensive plastic injection molding experience.
High volume mold building necessitates a combination of technology, equipment and qualified mold builders to create injection molds quickly with an almost limitless geometry for the plastic components.
From design to delivery, DJmolding can coordinate your entire tool building program from start to finish. Aided by its quality assurance program, PTI’s mission is to provide molded products that fully meet or exceed the requirements and expectations of its customers. Company management is committed to continuous quality advancements. For superior quality and efficient high volume molding services, contact DJmolding. today.
Many companies don’t have the capability to provide such a comprehensive start to finish mold making experience. Whether you’re looking for a few fast prototypes, thousands of market-ready consumer plastics, or a million production parts, DJmolding can provide what you need. Low and high-volume, we proudly insist that each order is of the same level quality. Contact our experts today.
From design to delivery, DJmolding can coordinate your entire tool building program from start to finish. For superior quality and efficient services, Request A Quote by sending your information to info@jasonmolding.com
The manufacturing process of high volume injection molding produces many identical plastic parts. This process is popular because it is cost-effective, efficient, and delivers consistent, high-quality pieces. This blog post will explore everything you need about high volume injection molding, including its advantages, disadvantages, applications, and more.
What is High Volume Injection Molding?
High-volume injection molding is a manufacturing process that produces many identical plastic parts. The process involves injecting molten plastic material into a mold cavity at high pressure and temperature, allowing it to cool and solidify into the desired shape. This highly automated process can produce thousands or even millions of identical parts in a single production run.
A highly efficient production process is the key to successful high-volume injection molding. The process entails utilizing high-speed injection molding machines and automated systems that enable the fast and precise production of parts. Additionally, manufacturers can ensure they make each element to specifications by using high-quality molds and applying specific injection parameters.
One of the most significant advantages of high volume injection molding is its ability to produce large quantities of identical parts quickly and cost-effectively. The manufacturing process is perfect for the automotive, consumer goods, medical devices, and electronics industries.
Another advantage of high volume injection molding is the ability to produce complex parts with tight tolerances. The injection molding process is precise and consistent, resulting in intricate details with minimal variation between pieces.
Despite its many advantages, high volume injection molding does have some limitations. For example, there may be better choices for producing very large or minimal parts, as the cost and complexity of the molds required can be prohibitive. Additionally, high volumes of plastic can have environmental impacts, making it essential for manufacturers to consider sustainability and recycling efforts.
High-volume injection molding is a highly efficient and effective manufacturing process that can produce large quantities of identical plastic parts quickly and cost-effectively. It is an ideal choice for a wide range of industries, and its precision and consistency make it a popular choice for producing complex parts with tight tolerances. While it does have some limitations, the benefits of high volume injection molding make it a valuable tool for manufacturers seeking to produce large quantities of high-quality plastic parts.
How Does High Volume Injection Molding Work?
The process involves several key steps, each critical in producing high-quality parts. This blog post will outline how high volume injection molding works, including its key steps and considerations.
Mold Design and Preparation
The first step in high volume injection molding is to design and prepare the mold the manufacturers will use to produce the parts. Collaborating with a mold maker is necessary to create an accurate design that meets all essential specifications for making the required parts. Typically, manufacturers make the mold from steel or aluminum and design it to withstand the high pressure and temperature of the injection molding process.
Material Preparation
The next step is for the manufacturers to prepare the plastic material they will use to produce the parts. Choosing the suitable plastic resin is crucial to create the desired features, as the type of resin used depends on the specific requirements. The resin is then fed into the injection molding machine, heated, and melted to liquid.
Injection Molding Process
The injection molding process begins when the melted plastic material is injected into the mold cavity at high pressure and temperature. The mold is held closed under pressure until the plastic has cooled and solidified; at this point, the mold is opened, and the part is ejected.
Quality Control
Once the parts have been produced, they undergo a rigorous quality control process to ensure they meet the required specifications. This may include visual inspection, measurement, and testing to verify that each part is consistent in size, shape, and quality.
Considerations for High-Volume Injection Molding
There are several considerations that manufacturers must keep in mind when using high volume injection molding, including:
- Machine Selection: High-speed injection molding machines are typically used for high-volume production runs, as they can quickly and accurately produce parts.
- Mold Design: The mold design is critical to the success of the injection molding process, as it must be precise and able to withstand the high pressure and temperature of the process.
- Material Selection: The choice of plastic resin can impact the quality and performance of the parts being produced, making it essential to select the appropriate material for the job.
- Cost: While high-volume injection molding is a cost-effective manufacturing process, there are still costs associated with mold design, material selection, and production that must be considered.
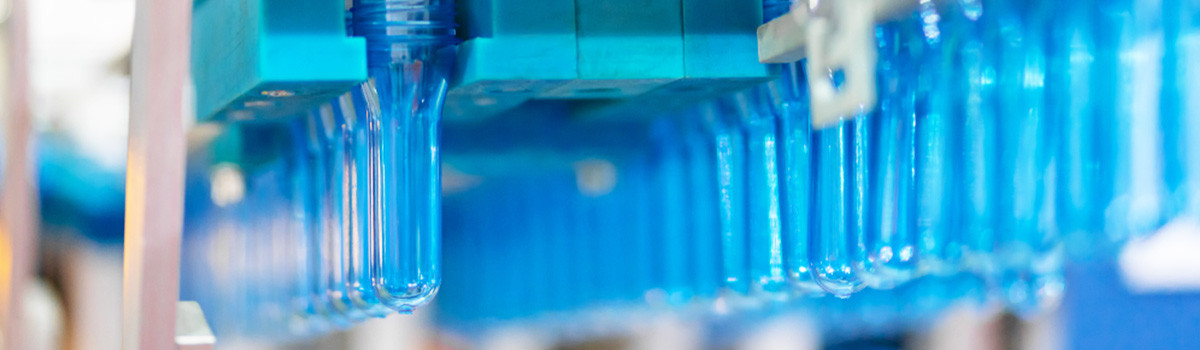
Advantages of High Volume Injection Molding
High-volume injection molding has revolutionized the manufacturing industry by enabling the production of identical plastic parts in large quantities with unparalleled speed and efficiency. The process has gained popularity across various sectors owing to its many advantages, making it a go-to manufacturing method for companies looking to cut costs, reduce waste, and increase production output.
- Cost-Effective Production: High-volume injection molding is highly efficient and automated, making it cost-effective compared to other manufacturing processes. Once the mold is designed and prepared, the production process can run continuously, producing thousands or millions of identical parts with minimal labor or material costs.
- High-Production Output: With high-speed injection molding machines, manufacturers can produce large quantities of exact parts in a short time. This means that production output can quickly increase or decrease to meet changing demand.
- Consistent Quality: The precision and consistency of high-volume injection molding make it ideal for producing parts with tight tolerances and intricate details. The process allows for a high degree of accuracy, ensuring that each part produced is identical to the others.
- Versatility in Part Design: High-volume injection molding can produce parts with a wide range of designs and shapes, including those with complex geometries. This means that manufacturers can have features that meet specific customer requirements and can easily adjust to design or product specifications changes.
- Reduced Waste: The use of high-quality molds and precise injection parameters in high volume injection molding minimizes the amount of scrap or waste produced during the manufacturing process. This means that manufacturers can make parts with minimal material waste, reducing costs and environmental impact.
- Increased Production Efficiency: High-volume injection molding is highly automated, which means that it requires minimal labor and can run continuously with little intervention. This leads to increased production efficiency, as manufacturers can produce parts quickly and efficiently without the need for manual work or supervision.
Disadvantages of High-Volume Injection Molding
High-volume injection molding is a widely-used manufacturing process for producing large quantities of identical plastic parts quickly and cost-effectively. While it has many advantages, such as cost-effectiveness and consistent quality, there are also disadvantages. This blog post will explore some of the disadvantages of high volume injection molding.
- High Initial Investment: One of the primary disadvantages of high volume injection molding is the increased initial investment required to design and manufacture the mold. This cost can be significant, especially for small businesses or those that need customized molds for specific parts.
- Long Lead Times:The process of designing and manufacturing molds for high-volume injection molding can take several weeks or even months, resulting in long lead times. This can be a disadvantage for companies that need to produce parts quickly or respond to changes in demand.
- Limited Material Choices: While many types of plastic resins are available for high volume injection molding, the selection may be limited depending on the specific application. Some plastic resins may not be suitable for high volume production due to their properties, which can restrict material choices.
- Limited Design Flexibility: High-volume injection molding is a precise process requiring molds to be designed with specific specifications. This means there may be limitations on the design of parts produced through this process, especially if the position has complex geometries or other distinctive design requirements.
- High Maintenance and Repair Costs: The molds used in high-volume injection molding must be maintained and repaired regularly to ensure optimal performance. The cost of maintenance and repairs can be significant, mainly if the molds are used frequently or for extended periods.
Despite these disadvantages, high-volume injection molding remains a popular and effective manufacturing process for producing large quantities of identical plastic parts. By carefully considering the advantages and disadvantages of this process, manufacturers can make informed decisions about whether it is the right choice for their specific production needs.
Materials Used in High-Volume Injection Molding
Selecting the appropriate materials for high-volume injection molding is vital to ensure the final product’s quality and performance. This article delves into the materials used in high volume injection molding, their properties, and their applications.
Polypropylene (PP)
Polypropylene is a commonly used thermoplastic polymer in high-volume injection molding due to its low cost, strength-to-weight ratio, and durability. PP is versatile for automotive, packaging, and consumer goods production. The advantages of using PP in injection molding include its lightweight nature, chemical resistance, and dimensional stability, which make it ideal for precision parts.
Acrylonitrile Butadiene Styrene (ABS)
ABS is a thermoplastic polymer known for its toughness, impact resistance, and high gloss finish. This material is commonly used in toys, automotive parts, and electronic housings. ABS’s impact resistance makes it suitable for details subjected to impact or shock. It is also easy to process and has an excellent surface finish, making it ideal for high-volume production runs.
Polycarbonate (PC)
Polycarbonate is a thermoplastic polymer that is highly impact-resistant, optically clear, and heat-resistant. It is a popular material for the automotive, aerospace, and electronics industries. PC’s benefits include excellent impact resistance, optical clarity, and heat resistance, making it ideal for high-temperature applications, lenses, and screens.
Polyethylene (PE)
Polyethylene is a thermoplastic polymer that is flexible, tough, and chemical-resistant. It is commonly used to produce packaging materials, plastic bags, and agricultural films. PE’s chemical resistance, flexibility, and lightweight nature make it ideal for chemical processing equipment, packaging for chemicals, and applications requiring parts to bend or flex.
Polyethylene Terephthalate (PET)
PET is a thermoplastic polymer with a high strength-to-weight ratio, clarity, and barrier properties. It produces beverage bottles, food containers, and packaging materials. PET’s benefits include its strength-to-weight balance, transparency, and barrier properties that make it ideal for applications where strength is necessary, such as beverage bottles and packaging where the contents must be protected from moisture and oxygen.
Polystyrene (PS)
Polystyrene is a thermoplastic polymer that is lightweight, cost-effective and has good insulation properties. PS is commonly used to produce disposable cups, packaging materials, and insulation, and its advantages include low cost, lightweight nature, and good insulation properties.
Types of Injection Molding Machines Used for High Volume Production
The process involves injecting molten plastic material into a mold cavity, where it solidifies and takes the shape of the mold. Injection molding machines come in different types, and each is suited for a specific kind of production. Here are the main types of injection molding machines used for high volume production:
- Hydraulic Injection Molding Machines: These machines use hydraulic pressure to move the mold and inject the molten plastic into the cavity. They are known for their high production output but also have a slow cycle time, limiting their use for high precision and high-speed applications.
- Electric Injection Molding Machines: These machines use electric servo motors to drive the injection unit and the mold. They offer high accuracy and speed, making them ideal for high-tech industries like medical devices and electronics.
- Hybrid Injection Molding Machines: These machines combine the best of both worlds. They use hydraulic and electric systems to drive the injection unit and mold. Hybrid engines are efficient and fast, with a high production output, making them ideal for high volume production.
- Two-Shot Injection Molding Machines: These machines produce complex parts that require two different materials or colors. The device has two injection units that work together to create the final piece. Two-shot injection molding machines are ideal for producing high-quality products with multiple components.
- Multi-Material Injection Molding Machines:These machines produce parts made of different materials. They have multiple injection units that allow them to use other materials simultaneously. Multi-material injection molding machines are ideal for creating pieces that require different properties, such as strength, durability, and flexibility.
- Liquid Injection Molding Machines: These machines are used to produce parts made of liquid silicone rubber (LSR). The machine injects LSR into the mold cavity, where it solidifies and takes the shape of the mold. Liquid injection molding machines are ideal for producing parts that require high precision and durability, such as medical devices and automotive parts.
Injection Molding Process Steps for High-Volume Production
The process involves injecting molten plastic material into a mold cavity, where it solidifies and takes the shape of the mold. Here are the steps involved in the injection molding process for high volume production:
- Material Selection: The first step in the injection molding process is selecting the suitable material for producing the part. The material chosen should have the required properties, such as strength, durability, and flexibility, and be compatible with the injection molding machine.
- Mold Design: TheThe next step is designing the mold once the material has been selected. The mold should be prepared to the exact specifications of the part being produced, including its shape, size, and features. The mold should also take into account the type of injection molding machine being used and the specific requirements of the production process.
- Machine Setup: After the mold has been designed, the injection molding machine is set up. This involves attaching the mold to the device, setting the proper temperature and pressure settings, and verifying that everything works correctly.
- Injection: The injection process begins when the molten plastic material is injected into the mold cavity. This is done using a high-pressure injection unit that forces the material into the mold at a specific rate and pressure.
- Cooling:After the molten plastic material has been injected into the mold cavity, it must be allowed to cool and solidify. This is done by circulating cool air or water through the mold cavity to reduce the temperature of the material.
- Ejection: Once the plastic material has cooled and solidified, the mold is opened, and the part is ejected. The ejection process involves using a mechanical or hydraulic system to push the part out of the mold cavity.
- Quality Control: After the part has been ejected, it undergoes quality control checks to ensure it meets the required specifications. This may involve visual inspection, measurement, and testing to verify that the part is high-quality and defects-free.
Design Considerations for High-Volume Injection Molding
Designing a plastic part for high volume injection molding requires careful consideration of several factors to ensure that the piece can be manufactured efficiently and cost-effectively. Here are some design considerations for high volume injection molding:
- Wall Thickness: The wall thickness of a plastic part is an essential consideration for injection molding. The thickness of the walls should be uniform to prevent uneven cooling and warping of the piece. Thin walls are ideal for high-volume production as they reduce material usage and cycle time, while thick walls are suitable for parts that require extra strength.
- Part Size and Shape: The size and shape of the part will impact the injection molding process. Factors that are too large or complex may require longer cycle times or specialized equipment, increasing production costs. Simple, geometric shapes are best for high volume production.
- Draft Angles: A draft angle is the angle of the mold cavity wall that allows for easy ejection of the part. IncludingIncluding draft angles in the part design are essential to ensure that the piece can be quickly ejected from the mold. Amounts without draft angles can result in costly production issues such as cracking or deformation.
- Gate Location and Size:The location and size of the gate, where the molten plastic material enters the mold cavity, is a critical design consideration for injection molding. The gate location should be placed in an area that will not affect the part’s structural integrity. The gate size should be large enough to allow the material to flow correctly but not so large that it causes defects in the position.
- Material Selection: The selection of the material is essential to ensure that the part can be manufactured efficiently and cost-effectively. Material selection should be based on the specific requirements of the piece, including strength, durability, and flexibility.
- Surface Finish: The part’s surface finish is an essential consideration for injection molding. The surface finish of the amount should be smooth and free from defects, such as warping or sink marks. Proper gate placement, mold design, and material selection can achieve smooth surface finishes.
- Tolerance: Tolerance is the degree of variation allowed in the dimensions of a part. Tolerance should be considered during the part design phase to ensure that the piece can be manufactured accurately and precisely.
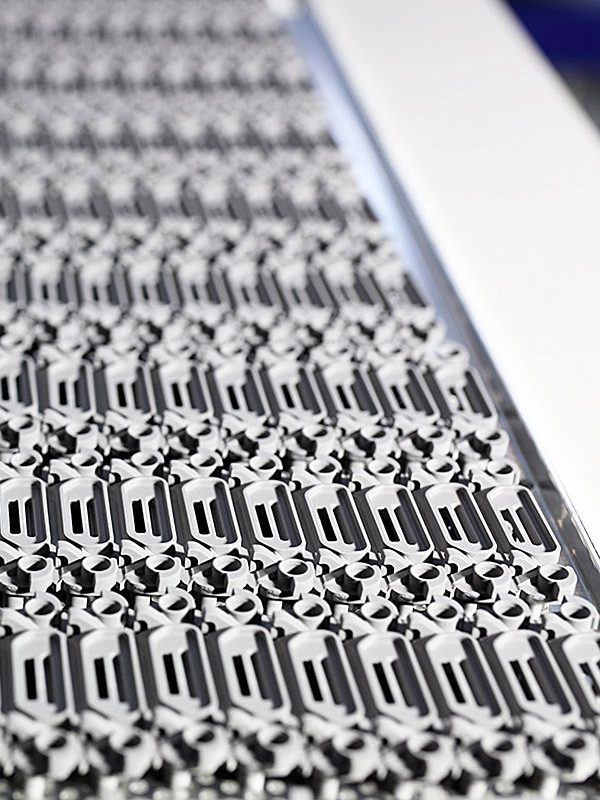
Quality Control Measures in High-Volume Injection Molding
Quality control is essential to high volume injection molding, as it ensures that the parts produced meet the required specifications and are free from defects. Here are some quality control measures used in high volume injection molding:
- Inspection during the Production Process: Regular review during the production process can help to identify defects early and prevent them from becoming more significant issues. This may involve visual inspection, measurement, and testing to verify that the part is being manufactured correctly.
- Statistical Process Control (SPC): SPC is a statistical method used to monitor and control a production process. It involves collecting data on the production process and analyzing it to identify trends and patterns that may indicate issues with the process. SPC can help to detect and correct problems before they result in defective parts.
- Use of Automated Equipment: Automated equipment, such as robots and sensors, can help improve the consistency and accuracy of the production process. Mechanical equipment can also reduce the risk of human error, resulting in fewer defects.
- Mold Maintenance:Proper mold maintenance is critical to ensuring that the parts produced are high quality. This involves cleaning the mold regularly and making any necessary repairs or replacements to ensure that the mold is functioning correctly.
- Post-Production Inspection: After the parts have been produced, they undergo a final inspection to ensure they meet the required specifications. This may involve visual inspection, measurement, and testing to verify that the parts are free from defects.
- Training and Education: Proper training and education of employees can improve the quality of the production process. Employees should be trained on proper production techniques and quality control measures to ensure that they can identify and correct issues as they arise.
- Continuous Improvement: Continuous improvement is essential to quality control in high-volume injection molding. By regularly reviewing the production process and identifying areas for improvement, manufacturers can reduce defects and improve the quality of the parts produced.
Cost Analysis of High-Volume Injection Molding
High-volume injection molding is a cost-effective manufacturing process for producing large quantities of plastic parts. However, the cost of producing parts through injection molding can vary based on several factors. Here are some cost analysis considerations for high volume injection molding:
- Material Cost: The cost of raw materials is one of the most significant factors that affect the price of injection molding. The type and quality of material used will impact the price, with some materials being more expensive than others. Manufacturers should choose the suitable material based on the specific requirements of the part.
- Tooling Cost: The cost of tooling, including the mold and other equipment needed for injection molding, is another significant factor affecting the production cost. The tooling cost can vary depending on the part’s complexity, the mold’s size, and the number of cavities in the mold.
- Labor Cost: Labor costs are a significant factor in injection molding, as the process requires skilled workers to operate the machines and oversee the production process. Labor costs can vary depending on the location and experience of the workers.
- Overhead Cost: Overhead costs, including utilities, rent, and other expenses, can also impact the injection molding cost. These costs can vary depending on the manufacturing facility’s location and the operation’s size.
- Production Volume: The production volume is an essential factor that impacts the injection molding cost. Higher production volumes can result in lower costs per part due to economies of scale.
- Part Design: The design can also impact the injection molding cost. Factors that are complex or require specialized equipment can increase the cost of production.
- Quality Control: The cost of quality control measures, including inspection and testing, can also impact the cost of production. These measures are necessary to ensure that the parts produced meet the required specifications and are defect-free.
Industries that Use High Volume Injection Molding
High-volume injection molding is a widely used manufacturing process that is capable of producing large quantities of plastic parts quickly and efficiently. Here are some industries that heavily rely on high volume injection molding:
- Automotive Industry: The automotive industry is one of the most significant users of high volume injection molding. The process manufactures various plastic components like dashboard parts, door handles, and interior trim pieces.
- Consumer Goods Industry: High-volume injection molding produces various consumer goods, including household appliances, toys, and electronics. The process is preferred because it allows manufacturers to create large parts cheaper.
- Medical Industry: The medical industry requires high-quality and precise plastic components for various medical devices, such as diagnostic equipment, surgical instruments, and disposable medical supplies. High-volume injection molding is preferred because it can produce these parts accurately and consistently.
- Industry:The packaging industry relies heavily on high-volume injection molding to produce a variety of plastic containers, lids, and closures. The process is cost-effective and allows manufacturers to create various shapes and sizes quickly.
- Aerospace Industry: The aerospace industry requires high-performance plastic components that can withstand extreme conditions, such as high temperatures and pressure. High-volume injection molding produces these components, including interior and exterior aircraft parts, avionics, and electronics.
- Construction Industry: The construction industry uses high volume injection molding to produce various plastic components, including window frames, piping, and insulation. The process is preferred because it allows for the production of large quantities of parts that are durable and resistant to environmental factors.
- Sports and Recreation Industry: High-volume injection molding produces various plastic components for the sports and recreation industry, including helmets, protective gear, and toys. The process is preferred because it allows for making lightweight, durable, and aesthetically pleasing parts.
Benefits of High-Volume Injection Molding for the Medical Industry
The medical industry is one of the largest and fastest-growing industries in the world. With the advancements in technology and the increasing demand for medical devices and equipment, there is a need for efficient manufacturing processes that can produce high-quality components. High-volume injection molding is one such process that offers several benefits for the medical industry. Let’s explore some advantages of high volume injection molding in the medical industry.
- Cost-effective: High-volume injection molding is a cost-effective manufacturing process that produces large quantities of plastic components at a lower cost per unit.
- Consistency: High volume injection molding allows for producing parts with high viscosity and accuracy, ensuring that each piece meets the required specifications.
- Customization: The process allows for the customization of features to fit specific requirements, including color, texture, and material.
- Speed: High volume injection molding allows for quick production of positions, reducing lead time and increasing efficiency.
- Quality: The high-volume injection molding process produces high-quality parts that meet the strict standards required for medical devices.
- Sterility: The process is conducted in a sterile environment, ensuring that the parts produced are free from contamination and safe for medical applications.
- Durability: Parts produced using high-volume injection molding are durable and can withstand harsh environments, ensuring they last longer and reducing the need for replacement. Durability is crucial in the medical industry, where devices and equipment must withstand constant use and potential exposure to chemicals and other harsh elements.
- Complexity: The high-volume injection molding process allows for the production of complex parts with intricate designs, ensuring that medical devices can be made to meet the exacting requirements of modern medicine. The process is ideal for producing complex components with unique features and designs essential for medical devices and equipment.
- Versatility: High volume injection molding can produce various parts with varying shapes and sizes, making it ideal for creating components in various medical applications.
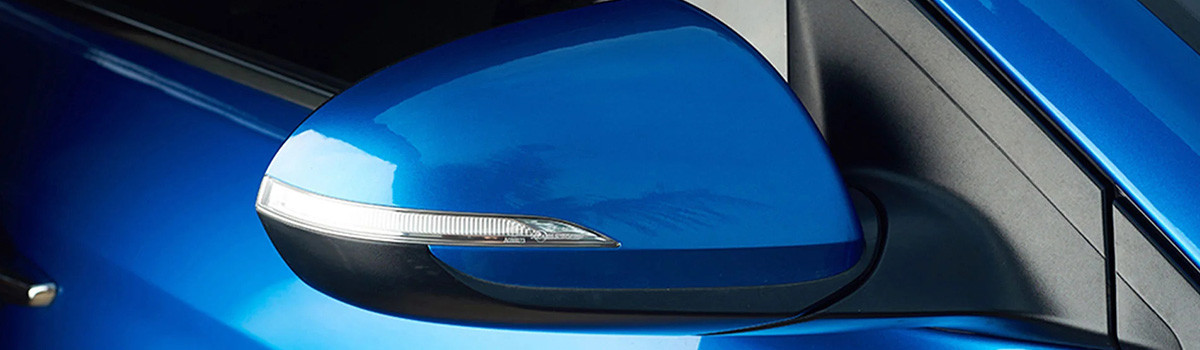
High Volume Injection Molding for Automotive Industry
Injection molding is a manufacturing process that involves injecting molten plastic into a mold cavity to create various plastic components. This process is widely used in the automotive industry to manufacture multiple parts such as door panels, dashboards, instrument panels, interior trims, and exterior body parts. High-volume injection molding is a specialized technique that enables manufacturers to quickly produce large quantities of identical parts.
High-volume injection molding is a highly efficient manufacturing technique that offers several benefits for the automotive industry. Some of these benefits include:
- Reduced production costs – The process is highly automated, which reduces labor costs, and molds allow manufacturers to produce identical parts at a lower price.
- Improved part consistency – High-volume injection molding allows for the production of identical parts, reducing variability and improving texture in the manufacturing process.
- Faster production times – The process is highly automated, which enables manufacturers to produce large quantities of parts quickly, reducing lead times.
- High-quality parts – The use of molds ensures that the parts produced are of high quality, with minimal defects and inconsistencies.
- Design flexibility –Injection molding allows rapid producing complex shapes and designs, giving designers greater flexibility in their plans.
Injection molding is an ideal manufacturing technique for the automotive industry, as it offers numerous benefits that improve efficiency, reduce costs, and improve part quality. High-volume injection molding, in particular, is a specialized technique that enables manufacturers to produce large quantities of identical parts quickly and efficiently.
The automotive industry relies heavily on injection molding to manufacture various car and vehicle components. From exterior body parts to interior trims and dashboards, injection molding has become an essential manufacturing process in the automotive industry. With high volume injection molding, manufacturers can produce large quantities of identical parts at a lower cost, with improved consistency and quality.
High Volume Injection Molding for Consumer Goods Industry
High-volume injection molding is a manufacturing process widely adopted by the consumer goods industry due to its ability to produce large quantities of high-quality parts with excellent precision and consistency. This process is commonly used in manufacturing consumer goods such as toys, kitchenware, and packaging materials, among others. This blog post will explore the benefits of high volume injection molding for the consumer goods industry.
Benefits of High Volume Injection Molding:
- Cost-effective: One of the primary benefits of high volume injection molding is that it is a cost-effective way to manufacture large quantities of parts. The process is highly automated, which reduces labor costs, and the molds can be reused, which reduces material costs.
- Consistency and precision:Injection molding provides excellent accuracy and consistency in producing parts. This is because the molds are designed to the exact specifications of the elements, ensuring that every piece is of the same quality and size.
- Fast production:High-volume injection molding is an immediate process, and large quantities of parts can be produced relatively quickly. This makes it ideal for manufacturing consumer goods that require quick turnaround times.
- Customization: Injection molding allows for the customization of parts using different materials, colors, and surface finishes. This flexibility makes it possible to produce parts that meet consumers’ specific needs and requirements.
Applications of High Volume Injection Molding in the Consumer Goods Industry:
- Packaging materials:Injection molding is widely used to produce packaging materials such as plastic bottles, jars, and containers.
- Toys: Injection molding is a popular toy manufacturing method as it allows for quickly producing large quantities of parts.
- Kitchenware: Injection molding makes various kitchenware items such as cups, plates, and utensils.
- Electronics: Injection molding is used to manufacture various electronic components such as housings, buttons, and switches.
High Volume Injection Molding for Aerospace Industry
The aerospace industry demands high-quality and precise parts to ensure the safety and efficiency of aircraft. High-volume injection molding has become an essential process for the aerospace industry as it provides a cost-effective solution for producing large quantities of high-quality components with consistent quality. This blog post will discuss high volume injection molding for the aerospace industry.
Benefits of High Volume Injection Molding for the Aerospace Industry:
The aerospace industry requires lightweight, durable components that withstand extreme temperatures and pressures. High-volume injection molding offers numerous benefits for producing such elements, including:
- Cost-Effective Production: High-volume injection molding can produce large quantities of parts quickly, resulting in reduced manufacturing costs.
- Consistent Quality: The automated process ensures that each part produced is of the same high quality, which is crucial for the safety and reliability of aircraft components.
- Complex Geometries: The injection molding process produces complex shapes and geometries, which may be difficult to achieve with traditional manufacturing methods.
- Material Selection: High-volume injection molding can process a wide range of materials, including composites, which are ideal for aerospace applications.
- Reduced Waste: The high level of automation and precision in the injection molding process results in less material waste and scrap, which can lead to significant cost savings and environmental benefits.
Applications of High Volume Injection Molding in the Aerospace Industry:
High-volume injection molding is used extensively in the aerospace industry for the production of a variety of components, including:
- Air ducts and ventilation systems
- Interior and exterior aircraft components
- Structural elements such as brackets, clips, and housings
- Electrical and wiring components
- Seals and gaskets
Common Defects in High-Volume Injection Molding
However, like any manufacturing process, injection molding can sometimes result in defects that can affect the quality of the final product. This blog post will discuss some common faults in high volume injection molding and how they can be prevented.
- Sink Marks: Sink marks are depressions or indentations that can occur on the surface of the molded part. They are caused by shrinkage of the plastic material as it cools, resulting in uneven distribution of material. To prevent sink marks, modifying the design of the part and ensuring even wall thickness throughout the entire component is necessary.
- Warping:Warping is the deformation of the molded part due to uneven cooling of the plastic material. It results in a twisted or bent part that does not meet the required specifications. Warping can be prevented by ensuring that the mold temperature is consistent and by incorporating design features that minimize stress on the part during cooling.
- Flash: Flash is excess material that protrudes from the mold joint and can occur when the mold is not aligned correctly or clamped. Flash can be prevented by ensuring that the mold is properly aligned and that the clamping force is sufficient to hold the mold closed during the injection.
- Short Shots: Short shots occur when the plastic material does not fill the entire mold cavity, resulting in an incomplete part. This can be caused by insufficient injection pressure, low melt temperature, or a blocked gate. Short shots can be prevented by optimizing the injection parameters and ensuring the gate is properly designed and positioned.
- Weld Lines: Weld lines occur when two or more flow fronts meet and solidify, resulting in a visible line or seam on the molded part. Weld lines can be prevented by optimizing the mold design and injection parameters to ensure the plastic material flows evenly and smoothly through the cavity.
Troubleshooting Tips for High-Volume Injection Molding
High-volume injection molding is a complex process that requires attention to detail and careful monitoring to ensure that the final product is of the highest quality. A number of common issues can arise during the injection molding process, which can lead to defects in the final product. This post will explore some of the most common troubleshooting tips for high volume injection molding.
- Check the Injection Molding Machine Settings: One of the first things to check when troubleshooting high volume injection molding is the settings on the injection molding machine. Ensure that the temperature, pressure, and cycle time are all set correctly for the specific material used.
- Check for Material Flow Issues: Material flow issues are another common issue with high volume injection molding. Several factors, including incorrect settings on the machine or a blockage in the injection molding machine, can cause this. Ensure that the material flows smoothly through the device and that there are no blockages in the injection molding machine.
- Check for Warping and Shrinkage: Warping and shrinkage are common issues during high volume injection molding. These issues are often caused by uneven cooling of the material, which can lead to warping or shrinkage in the final product. Ensure the cooling time is set correctly for the specific material being used and the system functions properly.
- Check for Air Traps: Air traps are another common issue during high volume injection molding. This happens when the air becomes trapped in the mold cavity, which can cause voids or bubbles in the final product. Make sure that the mold is adequately vented to prevent air traps from occurring.
- Monitor the Process: Finally, closely monitoring the injection molding process is crucial to ensure that any issues are caught and addressed quickly. This can be done by monitoring the machine settings, material flow, and the cooling process. By closely monitoring the process, any issues can be identified and addressed before they lead to defects in the final product.
Maintenance Requirements for Injection Molding Machines
Injection molding machines are essential pieces of equipment in the manufacturing industry. They are used to produce various products, from plastic parts to metal components. However, like any other machine, injection molding machines require regular maintenance to ensure optimal performance and prevent costly breakdowns. This post will explore some of the maintenance requirements for injection molding machines.
- Lubrication: Proper lubrication is one of the most essential aspects of injection molding machine maintenance. The machine’s moving parts, such as the injection and clamping units, must be lubricated regularly to prevent friction and wear. Using the correct lubricant type and following the manufacturer’s recommendations for lubrication intervals is essential.
- Cleaning: Another essential aspect of injection molding machine maintenance is regular cleaning. The machine should be cleaned regularly to remove any dust, debris, or plastic residues that may accumulate on its components. This will help prevent clogging of the machine’s nozzles and filters, which can cause performance issues or even damage the engine.
- Inspection: Regular inspections are also necessary to ensure the machine is in good condition. Assessment should include checking for any signs of wear and tear, such as cracks or broken parts. The electrical components, such as sensors and switches, should also be checked regularly to ensure they function correctly.
- Calibration: Injection molding machines also require calibration to ensure they operate within the correct parameters. This includes checking the machine’s temperature, pressure, and speed settings to ensure they are within the manufacturer’s specifications. Calibration should be performed regularly to ensure that the device is operating at its optimal level.
- Replacement of Worn Parts: Finally, replacing any worn or damaged parts as soon as possible is essential. This can help to prevent further damage to the machine and reduce the risk of costly breakdowns. Replacement parts should be of the same quality as the original parts and installed by qualified technicians.
Sustainability and High Volume Injection Molding
Sustainability has become an increasingly important concern in the manufacturing industry in recent years. As the world becomes more aware of industrial processes’ environmental impact, companies are looking for ways to reduce their environmental footprint while maintaining productivity and profitability. High-volume injection molding is one area where sustainability can make a significant impact.
There are several ways in which sustainability can be incorporated into high volume injection molding:
- Material selection:Choosing suitable materials is essential to achieving sustainability in injection molding. Many options include bioplastics, recycled plastics, and bio-based materials. By selecting materials that are environmentally friendly and have a low carbon footprint, manufacturers can significantly reduce their impact on the environment.
- Energy efficiency: High-volume injection molding requires significant energy to operate. Manufacturers can reduce energy consumption and lower carbon emissions by implementing energy-efficient processes and equipment. This can be achieved by using energy-efficient machines, optimizing production processes, and investing in renewable energy sources.
- Waste reduction: Injection molding can generate significant waste, particularly excess plastic. By implementing waste reduction strategies, manufacturers can minimize the amount of waste generated and improve their sustainability. This can be achieved through recycling, reusing materials, and optimizing the production process to reduce waste.
- Life cycle analysis: Conducting a life cycle analysis can help manufacturers understand the environmental impact of their products throughout their entire life cycle. This analysis can help identify areas where sustainability can be improved and guide decision-making to create more environmentally friendly products.
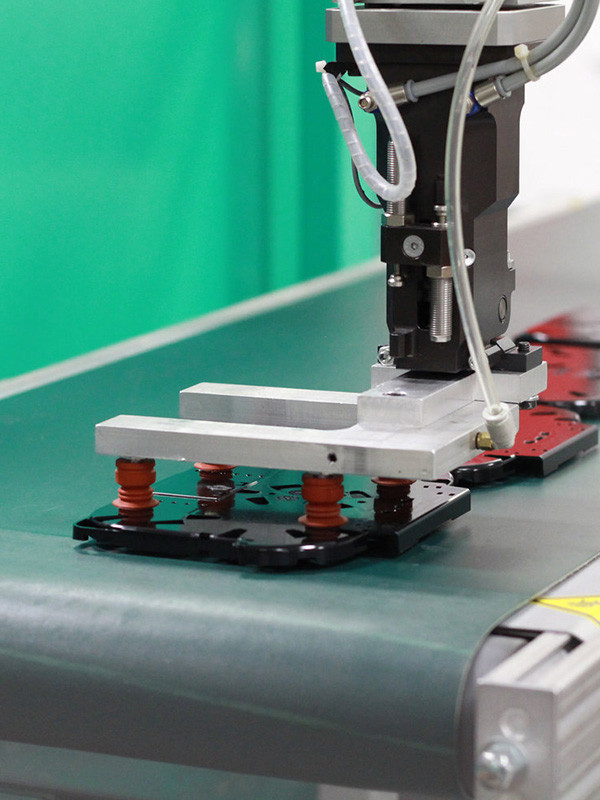
Main Points:
- Material selection plays a crucial role in achieving sustainability in injection molding.
- Energy-efficient processes and equipment can reduce energy consumption and lower carbon emissions.
- Waste reduction strategies, such as recycling and reusing materials, can minimize the amount of waste generated.
- Life cycle analysis can help identify areas where sustainability can be improved.
- Incorporating sustainability into high volume injection molding can benefit manufacturers by reducing costs and appealing to environmentally conscious consumers.
- Future of High-Volume Injection Molding
High-volume injection molding has been a vital manufacturing process for many industries for decades, and it continues to play an essential role in producing a wide range of plastic products. As technology advances and consumer demand shifts towards more sustainable and customizable products, the future of high-volume injection molding looks bright. Here are some of the trends and innovations that are shaping the end of this industry.
- Sustainability: With increasing consumer demand for environmentally friendly products, sustainability has become crucial in high-volume injection molding. Manufacturers are exploring new materials, such as bioplastics and bio-based materials, and implementing waste reduction strategies to minimize the environmental impact of their products.
- Customization: Consumers are looking for products that meet their unique needs and preferences, and high volume injection molding is well-suited to meet this demand. Advances in technology, such as 3D printing, are making it easier and more cost-effective to produce customized parts and products in large volumes.
- Automation: Automation is becoming increasingly prevalent in the manufacturing industry, and high volume injection molding is no exception. Automated processes, such as robotic arms and computer-aided design, can improve production efficiency and reduce costs.
- Industry 4.0: The fourth industrial revolution, Industry 4.0, is transforming the manufacturing industry by integrating advanced technologies such as artificial intelligence, the Internet of Things (IoT), and big data analytics. These technologies make it easier for manufacturers to optimize production processes and improve product quality.
- Medical industry:High-volume injection molding is well-suited for producing medical devices and equipment due to its precision and consistency. The demand for medical products is expected to grow, making this an important area for the injection molding industry.
- Electric vehicles:The shift towards electric cars creates new opportunities for the high-volume injection molding industry. Plastic components, such as battery housings and electrical connectors, are essential for electric cars, and the demand for these components is expected to grow as electric vehicles become more prevalent.
Conclusion:
High-volume injection molding is essential for producing large quantities of plastic parts. By understanding the advantages, disadvantages, materials, machines, methods, design considerations, quality control measures, and applications of high volume injection molding, businesses can optimize their production processes, reduce costs, and improve the quality of their products. Whether you are in the medical, automotive, consumer goods, or aerospace industry, high volume injection molding can benefit your business by providing consistent, high-quality parts at a cost-effective price.