Fundamentals of the plastic molding injection process for plastic part manufacturing
Fundamentals of the plastic molding injection process for plastic part manufacturing
Plastic materials have registered an exceptional development over the last 50 years, which exceeds that of any other consumer material.
Currently in Western Europe, the production volume of plastic materials exceeds the production of Steel.
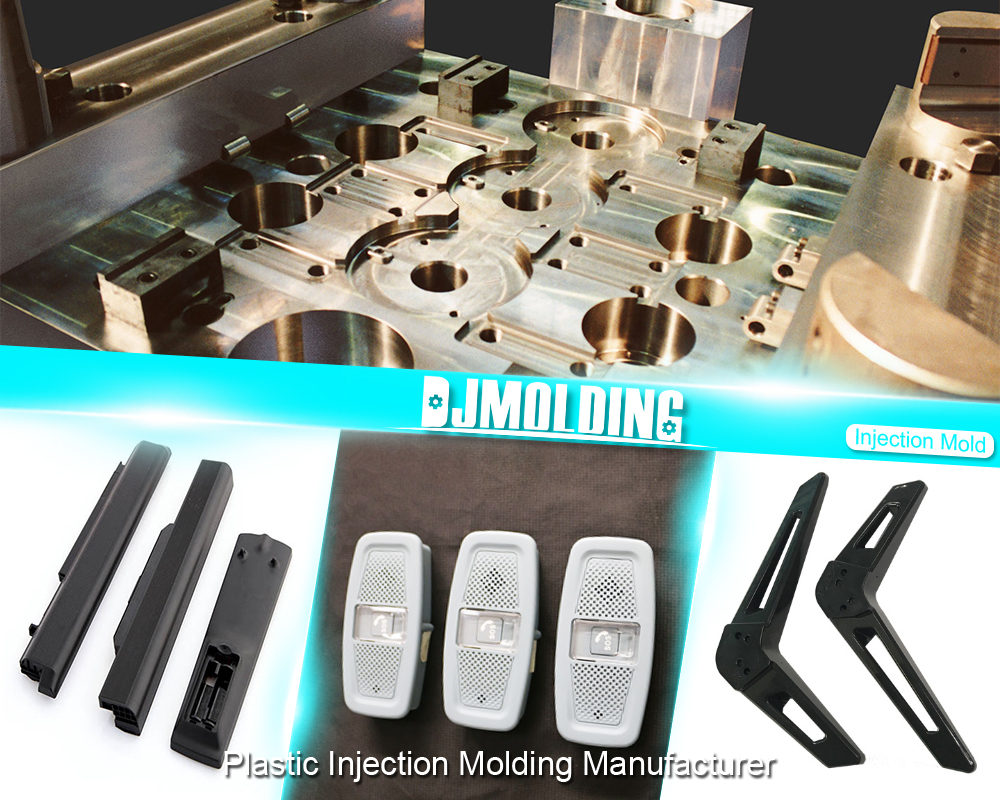
The growth in consumption is mainly explained by the increase in consumer products, having largely replaced plastics, metals and glass as materials for containers, packaging, construction materials, electronics, etc.
The advantages offered by plastic materials compared to other materials are the following:
- They are light and therefore reduce transportation costs.
- They are durable and often stronger and safer.
- They can be manufactured in a myriad of shapes and applications.
- They have excellent characteristics such as thermal, acoustic and electrical insulation.
- You can be used in food applications.
Plastics are standardized based on DIN 7728 and DIN 16780 standards for plastics mixtures.
Plastics are organic materials technically called polymers, which are derived from Petroleum or Natural Gas, which are carriers of Carbon C, hydrogen H, oxygen O and other molecules such as nitrogen N, chlorine CL, sulfur S or CO2. Currently, only 4% of the oil is transformed into plastic materials.
Plastic is extracted from petroleum by thermal distillation process (cracking), in which Ethylene, Propylene, Butylene and other hydrocarbons are split.
Macromolecules, or plastics, are made up of a multitude of simple structural units, called monomers; while the combination of these aided by chemical interactions gives rise to polymers.
What are polymers?
Polymers are produced by the union of hundreds of thousands of small molecules called monometers that form enormously diverse chains.
Plastics Classification:
- Plastics are classified according to different criteria, based on:
- Polymerization mechanism. (polymerization, polycondensation, polyaddition).
- Polymer structure. (crystallinity, superstructures).
Behavior / properties of the polymer. (Commodities, technical plastics, high performance plastics).
Based on the above, plastics are classified into:
- Thermoplastics. (Polyolefins, Vinyl or Acrylic Polymers, Polyamides, Polyesters, etc.)
- Thermostable.
- Elastomers.
The mechanical properties of thermoplastic materials are related to the Degree of Polymerization, which is a quantity that measures the number of links that make up the molecular chain. In fact, the higher the degree of polymerization, the higher the viscosity, the greater the tensile and tear resistance, the greater the hardness, the greater the impact resistance and, conversely, the less tendency to crystallize, less swelling capacity and less stress cracks.
In the case of Elastomeric and Thermoset materials, their properties are conditioned by the Degree of Crosslinking, which measures the percentage of crosslinking points (bonding between molecules) in the polymer system. The higher the degree of crosslinking, the greater the resistance of the material, its rigidity and its thermal resistance.
Plastics are light, they can be easily molded, they offer very good physical and mechanical properties, they can be manufactured in different colors, they can be mixed with other plastics or with inorganic materials, they have very low levels of thermal and electrical conductivity, they are very resistant to chemical agents, are permeable, are reusable and / or recyclable.
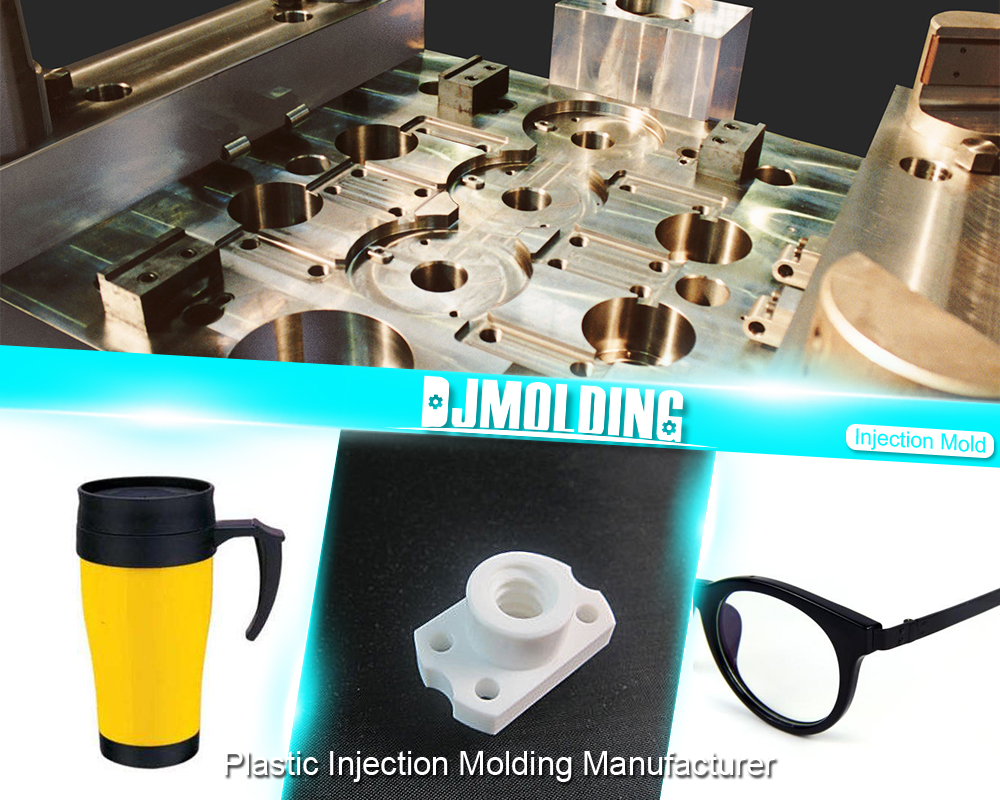
For more about fundamentals of the plastic molding injection process for plastic part manufacturing,you can pay a visit to Djmolding at https://www.djmolding.com/description-of-the-plastic-injection-molding-method-and-manufacturing-process-step-by-step/ for more info.