Everything You Need to Know About Thermoplastic Polyurethane (TPU) Injection Molding
Everything You Need to Know About Thermoplastic Polyurethane (TPU) Injection Molding
Thermoplastic Polyurethane (TPU) is a versatile material that has gained popularity across various industries due to its unique properties and adaptability. It belongs to a class of thermoplastic elastomers, which combines the elasticity of rubber with the toughness and durability of thermoplastics. TPU is used in various applications, from automotive components to medical devices, owing to its excellent wear resistance, flexibility, and ability to withstand extreme temperatures.
Injection molding, a highly efficient and widely used manufacturing process, is one of the primary methods for processing TPU. This article delves into everything you need to know about TPU injection molding, including the material’s properties, process, advantages and challenges, and applications.
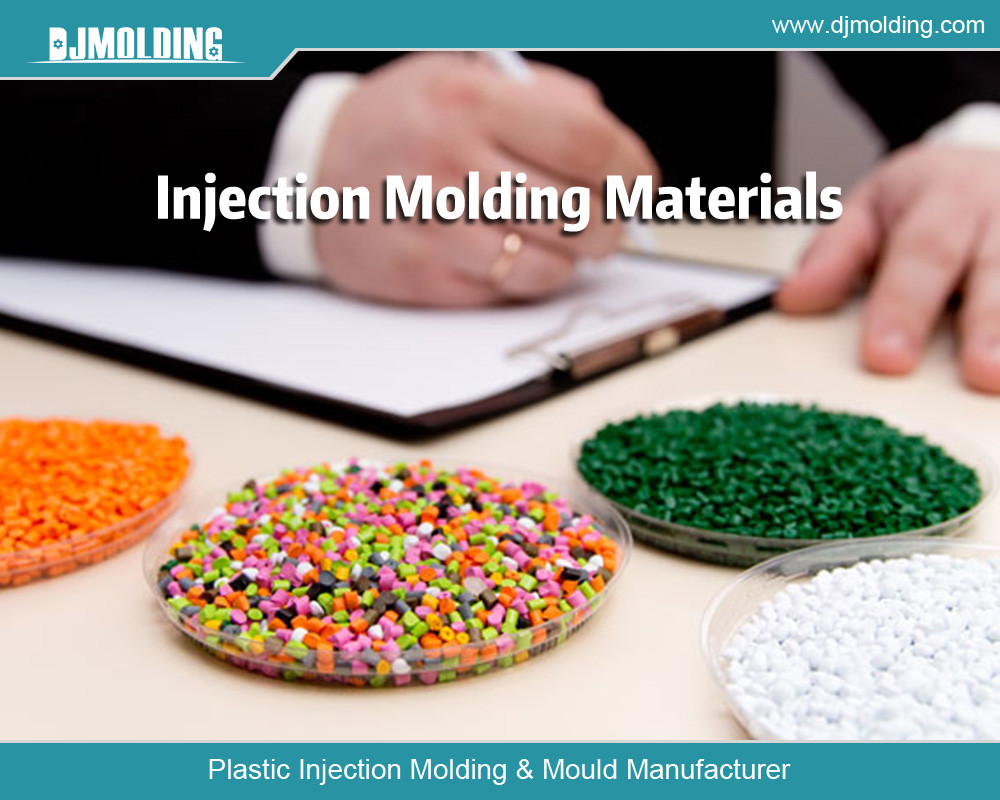
Properties of Thermoplastic Polyurethane (TPU)
Understanding the properties of TPU is essential for appreciating its suitability for injection molding and various applications. The following vital properties characterize TPU:
- Elasticity and Flexibility: TPU exhibits rubber-like elasticity, making it ideal for applications that require flexibility and the ability to return to its original shape after deformation. This property is particularly beneficial in footwear, seals, and gaskets applications.
- Durability and Toughness: TPU is known for its exceptional durability and toughness, contributing to its resistance to abrasion, impact, and wear. This makes TPU an excellent choice for automotive parts, industrial components, and protective covers.
- Chemical and Oil Resistance: TPU demonstrates good resistance to various chemicals, including oils, greases, and solvents. This property makes it suitable for applications in the automotive and industrial sectors where exposure to such substances is daily.
- Temperature Stability: TPU can withstand a wide temperature range, typically from -40°C to 80°C (-40°F to 176°F). Specific grades of TPU can even handle higher temperatures, making it versatile for applications in extreme conditions.
- Transparency and Colorability: TPU is naturally transparent, allowing for the production of clear or translucent parts. It can also be quickly colored, providing designers with the flexibility to create products in a variety of colors.
- Biocompatibility: Certain grades of TPU are biocompatible, making them suitable for medical and healthcare applications, including catheters, tubing, and medical devices.
The TPU Injection Molding Process
Injection molding is a manufacturing process in which molten material is injected into a mold cavity, which cools and solidifies to form a desired part. The process is widely used to produce parts from thermoplastic materials, including TPU. The TPU injection molding process involves several key steps:
- Material Preparation: Before the injection molding process begins, TPU granules or pellets are dried to remove any moisture that may have been absorbed during storage. Moisture can lead to defects in the final product, such as bubbles or incomplete molding.
- Melting and Plasticizing: The dried TPU is fed into the injection molding machine’s hopper, which is gradually heated to its melting point. A rotating screw then conveys the molten TPU to the front of the injection unit, where it is plasticized and homogenized.
- Injection: Once the TPU is wholly plasticized, it is injected into the mold cavity under high pressure. The mold, typically made of steel or aluminum, is precisely designed to form the desired shape of the part. The injection process must be carefully controlled to ensure the molten TPU fills the mold without causing defects such as voids or short shots.
- Cooling: After filling the mold, the TPU can cool and solidify. Cooling is a critical step, as it determines the final part’s dimensional accuracy and mechanical properties. The mold temperature and cooling time must be optimized for the best results.
- Ejection: Once the TPU has solidified and cooled sufficiently, the mold opens, and the part is ejected using ejector pins or other mechanisms. The part is removed from the mold, and any excess material, such as sprues or runners, is trimmed off.
- Post-Processing: Depending on the application, the molded TPU part may undergo additional post-processing steps, such as surface finishing, painting, or assembly. Quality control checks are also performed to ensure the part meets the required specifications.
Advantages of TPU Injection Molding
TPU injection molding offers several advantages, making it a preferred manufacturing method for producing high-quality parts. These advantages include:
- Design Flexibility: Injection molding allows for the exact production of complex and intricate shapes. TPU’s flow characteristics make it suitable for molding parts with thin walls, undercuts, and fine details.
- High Production Efficiency: Injection molding is a highly efficient process that massively produces parts with consistent quality. The cycle time for each part is relatively short, making it ideal for high-volume production.
- Material Versatility: TPU’s wide range of properties, including hardness, elasticity, and chemical resistance, can be tailored to meet specific application requirements. This versatility allows manufacturers to choose the suitable TPU grade for their needs.
- Low Waste Generation: Injection molding generates minimal waste, as excess material can often be recycled and reused in subsequent production runs. TPU’s thermoplastic nature allows it to be re-melted and reprocessed multiple times without significant degradation.
- Cost-Effective Production: The efficiency of the injection molding process, combined with TPU’s recyclability, contributes to cost-effective production. Although the initial investment in molds and machinery can be high, the long-term benefits of reduced waste and high production rates offset these costs.
Challenges of TPU Injection Molding
While TPU injection molding offers numerous advantages, it also presents specific challenges that manufacturers must address to achieve optimal results. These challenges include:
- Moisture Sensitivity: TPU is hygroscopic, meaning it absorbs environmental moisture. Moisture can cause defects such as bubbles, voids, or degradation during molding. Proper drying and storage of TPU granules are essential to prevent moisture-related issues.
- Mold Design Considerations: Designing molds for TPU injection molding requires careful consideration of shrinkage, venting, and cooling factors. TPU’s elasticity and flow characteristics can lead to challenges in achieving uniform filling and cooling, which may result in defects or dimensional inaccuracies.
- Processing Temperature Control: TPU’s processing window is relatively narrow, and precise temperature control is crucial to prevent degradation, burning, or incomplete melting. Overheating can lead to material degradation, while insufficient heating can cause incomplete mold filling.
- Cycle Time Optimization: TPU’s cooling rate can vary depending on the part’s geometry and thickness. Balancing the need for rapid cooling with the requirement for dimensional stability can be challenging. Cycle time optimization is necessary to achieve consistent quality while maintaining production efficiency.
- Material Compatibility: TPU’s properties vary significantly based on its formulation, including hardness, elasticity, and chemical resistance. Selecting the appropriate TPU grade for a specific application requires careful consideration of the material’s compatibility with the intended use.
Applications of TPU Injection Molding
TPU injection molding is widely used in various industries due to its versatility and ability to meet specific performance requirements. Some typical applications of TPU injection molding include:
- Automotive Industry: TPU is used in the automotive industry to produce seals, gaskets, bushings, and interior trim parts. Its durability, flexibility, and resistance to chemicals and oils make it ideal for these applications.
- Footwear Industry: TPU is a popular material in the footwear industry for manufacturing soles, midsoles, and other shoe components. Its elasticity, abrasion resistance, and comfort properties make it suitable for sports shoes, casual footwear, and safety boots.
- Medical Devices: Certain grades of TPU are biocompatible and used in medical devices such as catheters, tubing, and implantable components. TPU’s flexibility, transparency, and resistance to bodily fluids make it ideal for these applications.
- Consumer Electronics: TPU is commonly used to produce protective cases, covers, and housings for consumer electronics such as smartphones, tablets, and wearable devices. Its impact resistance and ability to provide a secure grip make it a preferred choice for these products.
- Industrial Components: TPU injection molding is used to manufacture various industrial components, including conveyor belts, hoses, seals, and gaskets. TPU’s durability, chemical resistance, and ability to withstand harsh environments suit these demanding applications.
- Sporting Goods: TPU produces sporting goods such as protective gear, inflatables, and equipment components. Its flexibility, impact resistance, and ability to maintain performance in extreme conditions make it a valuable material in this industry.
Future Trends and Innovations in TPU Injection Molding
As industries evolve, so does the demand for advanced materials and manufacturing processes. TPU injection molding is no exception, with several trends and innovations shaping its future:
- Sustainable TPU Formulations: With increasing emphasis on sustainability, developing eco-friendly TPU formulations is gaining traction. Manufacturers are exploring bio-based TPU derived from renewable resources and recyclable TPU grades that can reduce the environmental impact of production.
- Advanced Mold Design and Simulation: Innovations in mold design and simulation technology enable manufacturers to optimize the injection molding process for TPU. Advanced software tools allow for precise material flow, cooling, and shrinkage prediction, leading to improved part quality and reduced defects.
- Additive Manufacturing Integration: Integrating additive manufacturing (3D printing) with injection molding opens new possibilities for TPU production. Hybrid processes that combine 3D printing with injection molding can produce complex geometries, prototypes, and small-batch production runs with greater flexibility and speed.
- High-Performance TPU Grades: Ongoing research and development efforts are focused on creating high-performance TPU grades with enhanced properties such as increased temperature resistance, improved abrasion resistance, and excellent chemical compatibility. These advancements will expand TPU’s applications in demanding industries such as aerospace and automotive.
- Smart Manufacturing and Industry 4.0: Adopting Industry 4.0 technologies, including automation, data analytics, and IoT (Internet of Things), transforms TPU injection molding. Intelligent manufacturing systems enable real-time monitoring and control of the molding process, leading to increased efficiency, reduced downtime, and improved product quality.
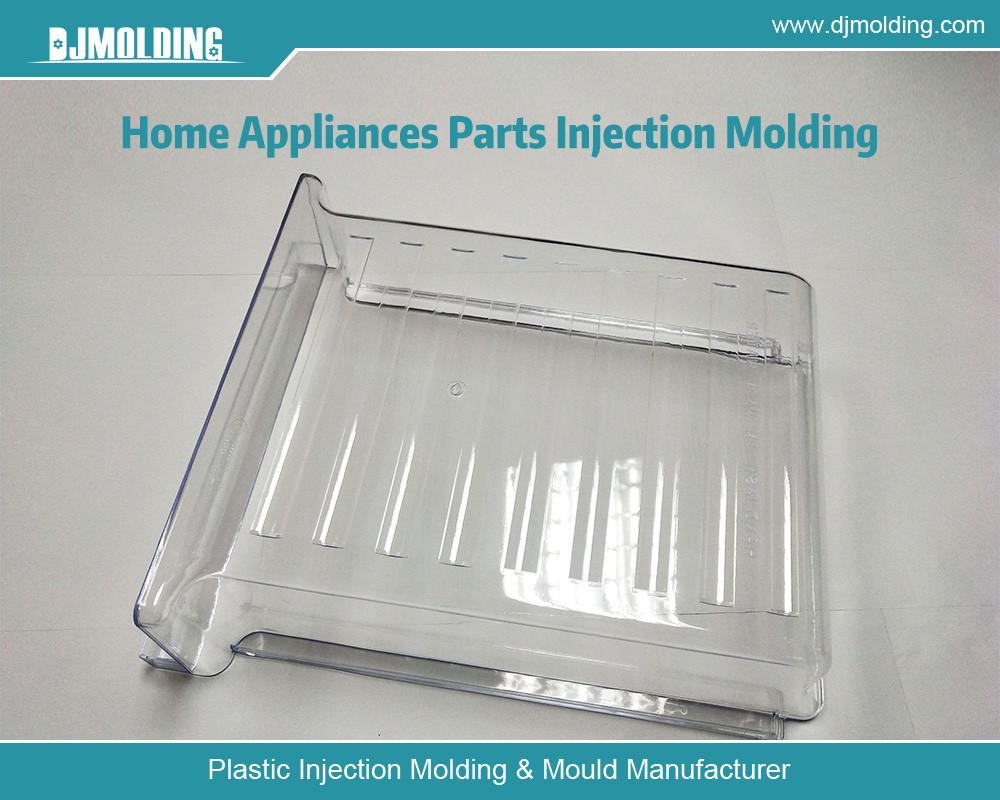
Conclusion
Thermoplastic Polyurethane (TPU) injection molding is a versatile and efficient manufacturing process that produces high-quality parts with a wide range of properties. TPU’s unique combination of elasticity, durability, chemical resistance, and temperature stability makes it an ideal material for applications in industries such as automotive, footwear, medical devices, and consumer electronics.
Despite the challenges associated with TPU injection molding, advances in material formulations, mold design, and process control continue to enhance its capabilities and broaden its applications. As industries evolve and demand for innovative materials grows, TPU injection molding is poised to play a crucial role in meeting future needs.
Understanding the intricacies of TPU injection molding, from material properties to processing techniques, is essential for manufacturers looking to leverage this technology for their products. By staying informed about the latest trends and innovations, manufacturers can continue pushing the boundaries of what’s possible with TPU and injection molding, creating products that meet the highest quality, performance, and sustainability standards.
For more about everything you need to know about thermoplastic polyurethane (tpu) injection molding, you can pay a visit to Djmolding at https://www.djmolding.com/thermoplastic-injection-molding/ for more info.