Discover The Benefits Of Low And High-Volume Plastic Injection Molding Service
Discover The Benefits Of Low And High-Volume Plastic Injection Molding Service
Which type of plastic injection molding low or high volume is better for you?
One popular manufacturing technique used to create different kinds of plastic components and products is injection molding. You have to take into account a number of associated factors when getting ready for injection molding assignments. It involves taking into account the experience and knowledge of the service provider. The likely volume involved in injection molding is one of the important factors to take into account. This factor will assist you in determining which service provider has the necessary resources, technical expertise, and experience to complete the molding assignments as effectively as possible. One can have a low, medium, or large production volume. Below are comparisons between low-volume and high-volume injection of plastic molding.
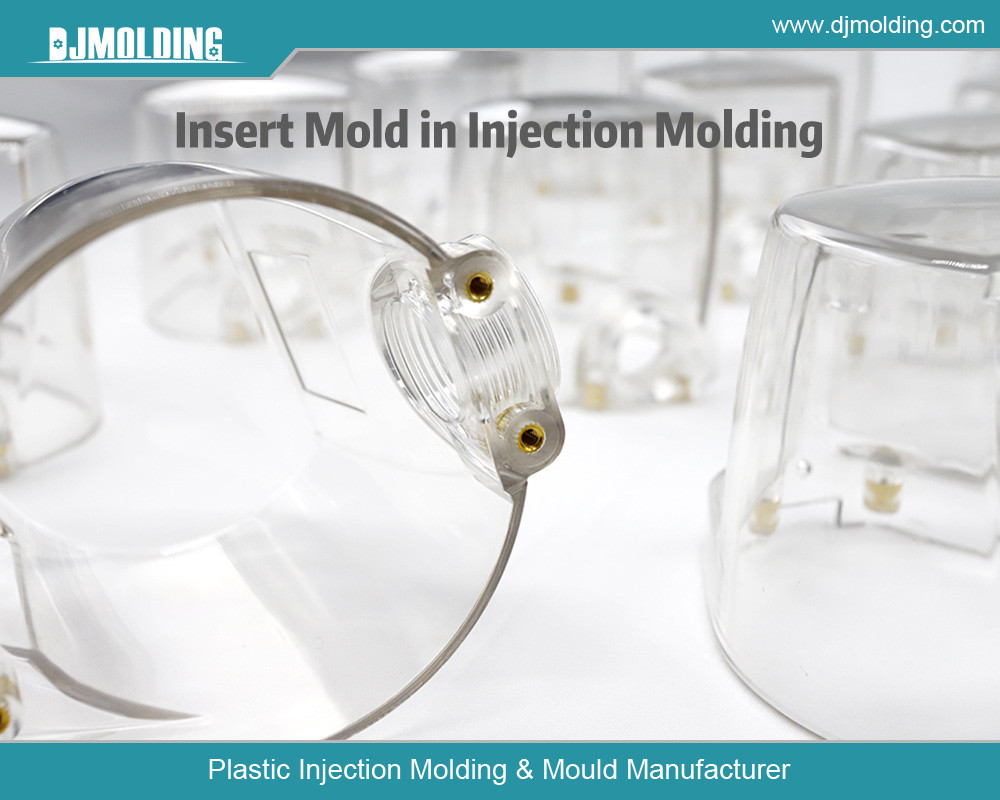
Which characteristics make up Low-Volume Injection Molding?
When manufacturing needs are less than 10,000 pieces, low-volume molding by injection is the best option. The procedure followed determines the precise count. The logical choice for large-scale manufacturing is steel tools; however, aluminum is used in low-volume injection-molding processes instead.
The following advantages of low-volume molding are cast in comparison to high-volume injection molding:
Minimal turnaround time at lower tooling costs:
The cost of tooling is one of the most notable benefits of low-volume tooling. This explains why the cost of aluminum tools is less than that of steel ones. The best thing happens to be that aluminum tools have the shortest turnaround times and are simpler to make. As a result, even if you must replace the aluminum application you can do it as quickly as possible. It guarantees the least amount of production loss when a tool needs to be changed.
Maximum Design Flexibility: Low-volume tools have lower production costs and a shorter manufacture time. It enables molding businesses to explore further with the design. As a result, service providers can quickly alter the design to suit the requirements of the project without increasing the cost of production. Overall, it helps to maintain the good’s cost within levels that are competitive.
Simple market entry: Low-volume molding equipment provide the least amount of production complexity and a greater range of design options. There is a higher market demand for it. For start-ups, small and medium-sized businesses, and organizations with strict production budgets, it is a more financially viable solution.
Due to its benefits, low-volume injection molding is now preferred by the majority of enterprises when high-volume molding is absolutely necessary.
Which applications of minimal-volume molding are the best fit?
Among the following use cases, low-volume injection molding with plastic finds the best application:
Pilot Manufacturing and Market Studies:
Low-volume molding by injection is ideal for the pilot manufacturing and testing market for new designs since it is a simpler and less expensive production technique. Businesses should ideally rely on the low-volume molding technique when establishing high-volume injection molding to maintain manufacturing activity.
Prototyping:
Organizations use low-volume molding to create prototypes in order to evaluate appropriate, form, and function due to its faster production times and lower costs.
Required minimum production:
Up to 10,000 pieces can be efficiently produced with low-volume molding. It renders the procedure ideal for businesses with minimal production requirements.
A synopsis of Plastic Injection Molding at High Volume
High-volume injection molding entails large-scale production, as the name suggests. This is the method that manufacturers use when they have to make hundreds or millions of units. The use of steel tools is this procedure’ most notable characteristic. Steel instruments are more all-encompassing, strong, and long-lasting to meet demanding manufacturing requirements. This procedure works best when it needs to generate between 75,000 and 100,000 units at once.
Comparison of both small and large volume injections head-to-head The following observations are supported by molding:
The best procedure to manage big capacities in the shortest amount of time is: It is possible to make thousands to millions of pieces at once with high-volume injection molding. For businesses that manage high production numbers on a daily basis, this makes it the only applicable injection molding technique.
Minimum Unit Cost:
High-volume injection molding considerably lowers the cost per unit even though it requires a larger setup fee. A million pieces are continuously produced by a high-volume molding setup because steel tools are durable and require little maintenance. As a result, there is a large overall decrease in unit cost. However, the actual number of units produced has a huge impact on the unit cost.
Ideal for Automation:
Experts say that high-volume injection molding is the ideal combination for automation. Once an automated process is established, it will further increase production capacity and drastically reduce cost per unit.
In your situation, which injection molding method is the best?
Both low volume and high-volume injection molding have benefits and drawbacks. A number of variables must be taken into account when making this decision:
manufacturing needs:
Until the manufacturing need is fewer than 75 thousand units at a time, it is not justified to use high-volume injection molding. It suggests that for limited production capacity, low-volume molding by injection is the optimum option.
The requirements for the design:
low-volume injection molding makes sense if the design is exclusive since it enables affordable tool experimentation.
manufacturing cost:
Prototyping and mechanization should be the business’s primary priorities when the cost for producing per unit continues to rise. Because high-volume injection molding drastically reduces manufacturing expenses, it is the only choice accessible in such cases.
Set-up budget:
Since a high-volume process will require a significant upfront expenditure, it is unavoidable to start using low-volume injection molding when there is a set-up budget constraint. Heavy-volume molding with steel tools results in longer production times and higher material costs.
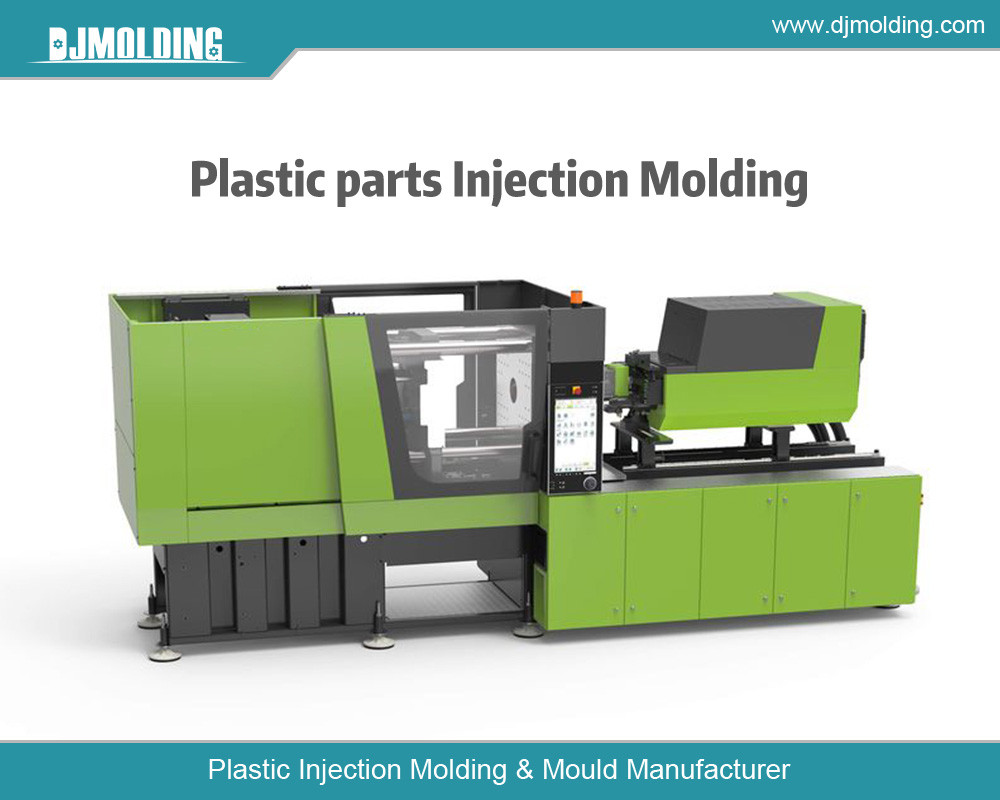
In summary
It will assist you to get professional advice if you are unable to choose which molding procedure is best for your situation. One crucial consideration is that the injection molding process you use must perfectly meet your production requirements. A mismatch will complicate things and raise the cost of production. It will eventually lead to manufacturing constraints and make it more difficult for you to offer premium goods at affordable prices. In due course, it will assist you in strengthening client involvement.
For more about the benefits of low and high-volume plastic injection molding service,you can pay a visit to Djmolding at https://www.djmolding.com/ for more info.