Custom Plastic Injection Molding Suppliers : Everything You Need to Know
Custom Plastic Injection Molding Suppliers: Everything You Need to Know
Custom plastic injection molding is a manufacturing process that involves the creation of custom plastic parts according to specific requirements. The process involves injecting molten plastic material into a mold under high pressure, resulting in a solidified plastic part. This blog post will provide an in-depth guide to custom plastic injection molding, including its benefits, applications, materials, process, quality control, tips for success, typical applications, and the industry’s future.
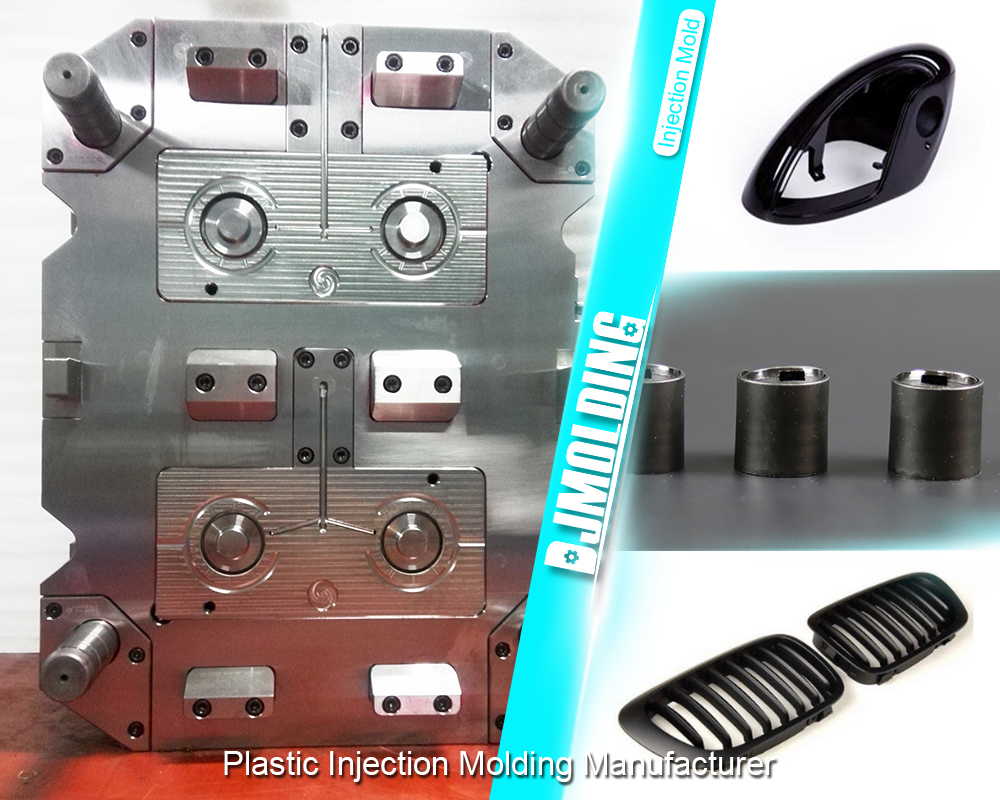
What is Custom Plastic Injection Molding?
- Defining custom plastic injection molding: Custom plastic injection molding creates custom plastic parts by injecting molten plastic into a mold. The process is highly versatile, allowing for the creation parts in various sizes, shapes, and complexities.
- Different applications of custom plastic injection molding: Plastic injection molding is a universal manufacturing process widely used in the automotive, medical, and consumer products industries. The process creates gears, housings, knobs, and other intricate components.
The Benefits of Custom Plastic Injection Molding
- Cost-effectiveness and efficiency: Custom plastic injection molding is highly cost-effective and efficient. It allows for high-volume production of parts, reducing production costs per unit. Additionally, the process is automated, reducing labor costs and increasing efficiency.
- Customization and flexibility: Custom plastic injection molding offers a high degree of customization and flexibility, allowing for creation of unique parts tailored to specific requirements. The process allows for easy modifications to the design or mold.
- High accuracy and consistency: Custom plastic injection molding offers high accuracy and consistency in part production, resulting in parts with high precision and uniformity.
The Materials Used in Custom Plastic Injection Molding
- Thermoplastics and thermosetting plastics: When it comes to custom plastic injection molding, there are two types of plastics used: thermoplastics and thermosetting plastics. Thermoplastics are plastics that can be melted and reshaped multiple times without losing their properties. On the other hand, thermosetting plastics undergo a chemical reaction during molding, making them more complex and rigid.
- Standard plastic materials used in custom injection molding: Common plastic materials used in custom injection molding include polypropylene, polycarbonate, acrylonitrile-butadiene-styrene (ABS), polyethylene, and nylon. Each plastic material offers unique properties, making them suitable for different applications.
The Process of Custom Plastic Injection Molding
- Designing the mold: The first step in custom plastic injection molding is creating the mold. The mold is designed based on the specific requirements of the part that needs to be manufactured. We consider material selection, part geometry, and tooling during mold design.
- The injection molding machine and its components: It consists of various parts, including the injection unit, clamping unit, and mold. The injection unit melts and injects the plastic material into the mold while the clamping team holds the mold in place during the process.
- The plastic material and its properties: The material used in custom injection molding is chosen based on the specific properties required for producing the part. We consider strength, flexibility, and heat resistance properties when selecting plastic material.
The custom plastic injection molding process
The custom plastic injection molding process involves the following steps:
- The operator loads the plastic material into the hopper of the injection molding machine.
- The material is melted and injected into the mold cavity under high pressure.
- The plastic material is cooled and solidified in the mold.
- The operator opens the mold and ejects the part from the mold.
Quality Control in Custom Plastic Injection Molding
Ensuring quality control in custom plastic injection molding
Quality control is critical to custom plastic injection molding to ensure the final product meets the required specifications. Quality control includes inspection and testing of the plastic parts during and after production. Operators monitor the injection molding machine during production to ensure the process runs smoothly and produces correctly molded parts. After production, the pieces are inspected for defects and tested for functionality.
The importance of inspection and testing
Inspection and testing ensure the final product meets the required specifications. The examination involves visually examining the parts for defects such as cracks, warpage, and sink marks. Testing involves functional testing of the components to ensure they perform as intended.
Tips for Successful Custom Plastic Injection Molding
Proper design and preparation of the mold and plastic material
One of the critical factors in ensuring the success of a custom plastic injection molding project is proper mold design and preparation. Before starting the manufacturing process, it is essential to ensure the mold design is suitable for the plastic material used and meets the required specifications. The mold design should also consider part geometry, material flow, and cooling time to minimize defects and improve overall quality.
Similarly, the plastic material must be prepared adequately before being injected into the mold. We dry and condition the fabric to eliminate any moisture that can cause defects in the final part. It is also essential to ensure the material is within the required temperature range for optimal flow and consistency.
Choosing the suitable injection molding machine and process parameters
The choice of injection molding machine and process parameters can significantly impact the quality and consistency of the final product. Selecting the appropriate device for material usage, part geometry, and production volume requirements is essential. The process parameters, including injection speed, pressure, and temperature, should also be optimized to achieve the desired results.
Regular maintenance and inspection of the equipment
Proper maintenance and inspection of the injection molding machine and mold are crucial for preventing defects and ensuring the longevity of the equipment. Regular cleaning, lubrication, and machine calibration can avoid wear and tear and maintain accuracy and consistency. Similarly, inspecting the mold for wear, damage, or buildup of contaminants can help identify and address issues before they affect production.
Common Applications of Custom Plastic Injection Molding
Custom plastic injection molding has a wide range of applications across various industries, including:
Automotive industry
The automotive industry uses custom plastic injection molding to produce parts for cars and trucks, such as dashboards, interior trims, and exterior body components. The process is beneficial for making parts with complex shapes and tight tolerances, which can be difficult or expensive to manufacture using traditional methods.
Medical devices
Manufacturers use custom plastic injection molding to produce a range of medical devices, including syringes, tubing, and connectors. The process offers high accuracy and consistency, making it ideal for creating parts with critical dimensions and specifications required for medical applications.
Consumer products
Manufacturers use custom plastic injection molding to produce various consumer products, including toys, kitchenware, and electronics. The process allows for high customization and flexibility, enabling manufacturers to create parts with unique shapes, colors, and textures.
The Future of Custom Plastic Injection Molding
New technologies and advancements in custom plastic injection molding are continually emerging, providing opportunities for innovation and growth in the industry. Some of the trends shaping the future of custom plastic injection molding include the following:
New materials
Advancements in material science are leading to the development of new plastics with improved properties, such as enhanced durability, strength, and flexibility. These new materials can enable manufacturers to produce more robust and functional parts, expanding the range of applications for custom plastic injection molding.
Automation and Industry 4.0
Automation and Industry 4.0 technologies are increasingly adopted in custom plastic injection molding to improve efficiency, reduce waste, and increase productivity. These technologies enable real-time monitoring of production processes, predictive maintenance, and data-driven decision-making, leading to better quality control and cost savings.
Sustainability and eco-friendliness
As environmental concerns continue to grow, using sustainable and eco-friendly materials and manufacturing processes is becoming more critical in custom plastic injection molding. Using recycled plastics, biodegradable materials, and energy-efficient production methods that reduce waste and carbon footprint is essential.
Choosing the Right Custom Plastic Injection Molding Partner
When it comes to custom plastic injection molding, choosing the right partner is crucial to the success of your project. Here are some factors to consider when selecting a custom plastic injection molding partner:
- Experience: Look for a partner with a proven track record in custom plastic injection molding. An experienced partner will have the knowledge, expertise, and equipment to produce high-quality plastic parts that meet your requirements.
- Quality Control: Make sure that your partner has a robust quality control process in place. This process should include inspection and testing at various stages of the production process to ensure that your parts meet your exact specifications.
- Customization: Choose a partner who works closely with you to understand your unique needs and requirements. A good partner should be able to provide customized solutions tailored to your specific needs.
- Production Capacity: Ensure your partner has the production capacity to handle your project. You must have sufficient machinery, workforce, and resources to meet your production needs.
- Communication: Effective communication is vital to a successful custom plastic injection molding project. Choose a partner who is easy to communicate with and keeps you informed throughout the production process.
Benefits of working with a trusted and experienced partner
Working with a trusted and experienced custom plastic injection molding partner offers several benefits, including:
- Reduced Costs: A professional partner will have the knowledge and expertise to optimize the production process and reduce costs. They can help you avoid costly mistakes and ensure your project stays within budget.
- Faster Time to Market: A trusted partner can help you get your product to market faster by providing quick turnaround times and efficient production processes.
- High-Quality Parts: A reliable partner will have a robust quality control process to ensure that your parts meet your specifications. You can trust that your information will be of the highest quality and reliability.
- Flexibility: A good partner will be flexible and able to adjust to your changing needs and requirements. They should be able to provide customized solutions tailored to your specific needs.
- Expertise: An experienced partner will have the knowledge, expertise, and equipment to produce high-quality plastic parts that meet your specific requirements. They can offer valuable insights and recommendations that can help you improve the design and functionality of your pieces.
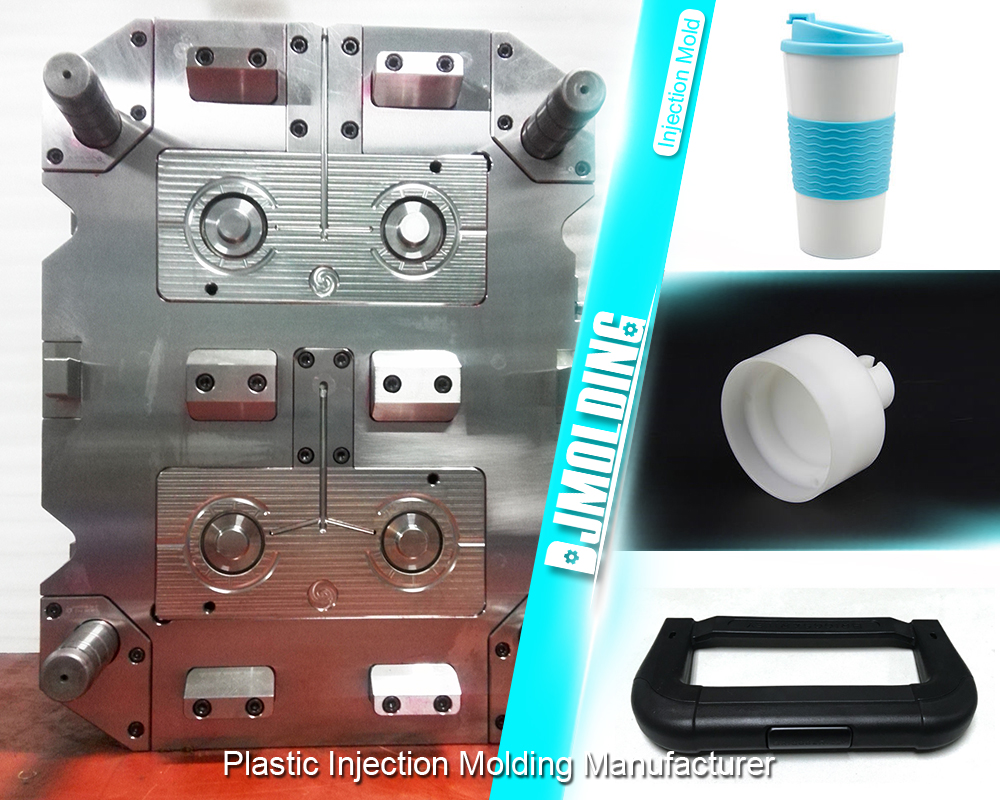
CONCLUSION
Custom plastic injection molding is a highly effective and efficient manufacturing process offering many benefits. Whether you produce custom plastic parts for the automotive industry, medical devices, or consumer products, custom plastic injection molding can help you achieve your goals. You can create high-quality custom plastic parts that meet your specific needs by understanding the materials, processes, and applications of custom plastic injection molding. Remember to work with a trusted and experienced partner to ensure the success of your project. With the right partner, you can take your custom plastic injection molding project to the next level.
For more about custom plastic injection molding suppliers,you can pay a visit to Djmolding at https://www.djmolding.com/custom-plastic-injection-molding/ for more info.