Custom Plastic Injection Molding Manufacturer : Creating Precision Custom Plastic Parts For Various Industries
Custom Plastic Injection Molding Manufacturer : Creating Precision Custom Plastic Parts For Various Industries
Custom plastic injection molding is a versatile and essential process in various industries. This process involves injecting molten plastic into a mold cavity and allowing it to solidify to produce a finished product. The process offers several advantages: cost-effectiveness, design flexibility, and consistent quality. This article will explore the definition, benefits, applications, processes, challenges, and considerations of custom plastic injection molding.
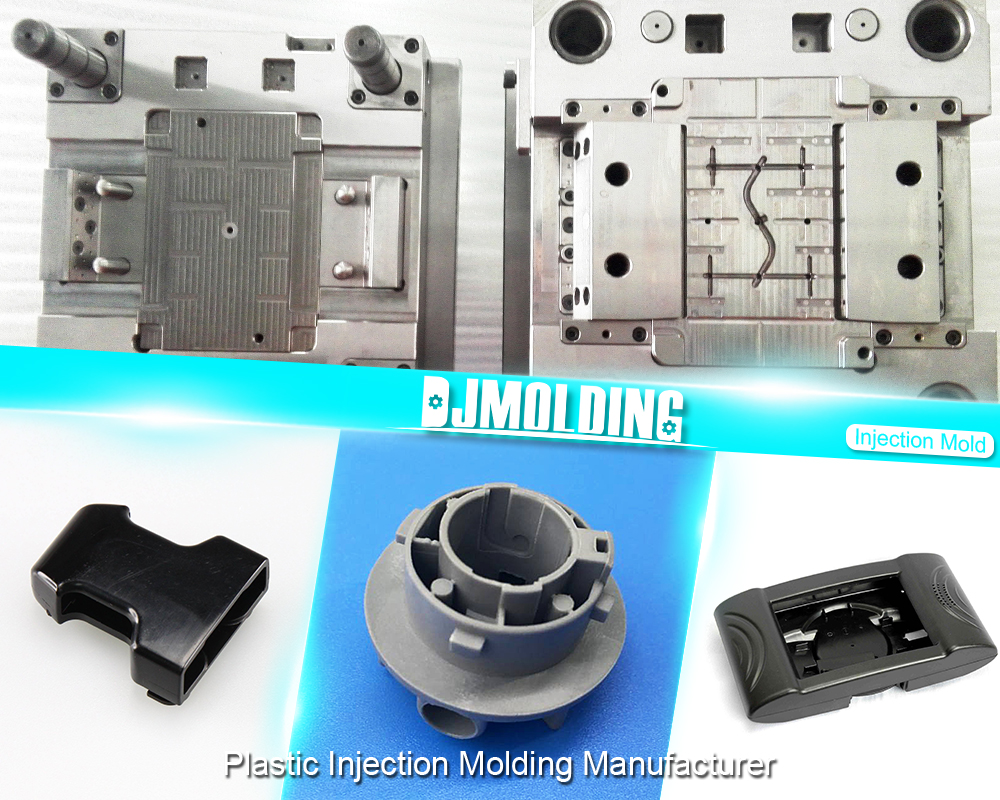
What is Custom Plastic Injection Molding?
Definition and Explanation of the Process
Custom plastic injection molding is a manufacturing process that produces high-precision parts and components for various industries. The process involves melting plastic pellets or granules and injecting them into a mold cavity at high pressures using a specialized machine. The plastic then solidifies and takes the shape of the mold.
Key Components of the Process
The key components of custom plastic injection molding include the mold, the injection molding machine, and the plastic Material. The injection molding machine melts the plastic and injects it into the mold cavity while designing the mold to the desired shape and making it from hardened steel or aluminum. The plastic material selection is made carefully based on its strength, flexibility, and durability.
Importance of Precision and Accuracy
Custom plastic injection molding requires high precision and accuracy to produce consistent and high-quality parts. The designer must ensure the mold has the correct dimensions and features while the operator calibrates the injection molding machine to ensure accurate pressure, temperature, and cooling times.
Advantages of Custom Plastic Injection Molding
Custom plastic injection molding has several advantages, making it a popular choice for manufacturing precision parts for various industries. Here are some of the benefits of this process:
Cost-effectiveness in Mass Production
Custom plastic injection molding is a cost-effective option for mass production. Although the initial tooling costs can be higher, the per-unit cost decreases significantly with larger production volumes. This cost reduction makes it ideal for manufacturing large quantities of identical parts.
Design Flexibility and Versatility
Custom plastic injection molding provides manufacturers with design flexibility and versatility. The process can produce complex and intricate designs with varying sizes, shapes, and features, making it suitable for various industries. Manufacturers can also modify and refine the creation of molds for better efficiency and production optimization.
Consistent Quality and Precision
Custom plastic injection molding provides consistent quality and precision. It is an ideal manufacturing process for industries that require identical parts with high precision and quality standards. The process allows for high repeatability and fast cycle times, increasing productivity. Manufacturers can achieve tight tolerances with high accuracy, ensuring the finished parts meet the required specifications.
Applications of Custom Plastic Injection Molding
Custom plastic injection molding is a versatile manufacturing process that finds applications in various industries. Here are some of the initiatives that benefit from this process:
Automotive Industry
Custom plastic injection molding is widely used in the automotive industry to produce parts such as dashboards, bumpers, and interior components. The process offers several advantages, including design flexibility, high precision, and consistency in quality, making it an ideal choice for producing automotive parts.
- Benefits of custom plastic injection molding in the automotive industry:
- Reduced production costs for mass production
- High strength and durability of parts
- Low maintenance and easy to clean
Medical Devices and Equipment
Custom plastic injection molding is used in the medical industry to produce components for devices and equipment such as syringes, inhalers, and medical tubing. The process ensures high precision and accuracy in producing parts, making them safe and reliable for medical use.
- Benefits of custom plastic injection molding in the medical industry:
- Ability to produce complex and intricate parts with high precision
- Consistent quality and reliability
- Cost-effectiveness for mass production
Consumer Goods
Custom plastic injection molding produces consumer goods such as toys, household appliances, and kitchenware. The process offers design flexibility and versatility, making creating parts with intricate designs and shapes possible.
- Benefits of custom plastic injection molding in the production of consumer goods:
- Ability to produce high-quality, aesthetically pleasing parts
- Faster production times and reduced lead times
- Cost-effectiveness for mass production
Electronics and Technology
Custom plastic injection molding produces electronic enclosures, connectors, and other components. The process offers the ability to produce parts with complex geometries and tight tolerances, making them suitable for producing electronic components.
- Benefits of custom plastic injection molding in the electronics and technology industry:
- High precision and consistency in quality
- Ability to produce parts with intricate designs and shapes
- Cost-effectiveness for mass production
The Custom Plastic Injection Molding Process
- Designing the Mold: The first step in the custom plastic injection molding process is designing the mold. To make a part, one must create a 3D model and develop the mold to meet the required specifications.
- Material Selection and Preparation: The next step is selecting and preparing the plastic Material. The Material is carefully chosen based on its properties and is then melted and injected into the mold cavity.
- Injection Molding Process: Once the molten plastic fills the mold, the cooling process occurs, and the injection molding machine ejects the finished part. To create numerous identical parts, they repeat the procedure.
Choosing the Right Custom Plastic Injection Molding Manufacturer
- Experience and expertise: Choosing the right custom plastic injection molding manufacturer is crucial to the success of any project. Selecting a manufacturer with extensive Experience and expertise in the field is essential. A manufacturer with a proven track record of successful projects and satisfied customers is likelier to deliver high-quality parts.
- Quality control measures: The manufacturer must have robust quality control measures to ensure the final product meets the required specifications. Quality control measures may include testing the parts for dimensional accuracy, strength, durability, and other properties.
- Customer service and communication: Effective communication between the manufacturer and the customer is essential for a successful project. The manufacturer must respond to customer needs and requirements and regularly update the project’s progress.
Challenges and Considerations in Custom Plastic Injection Molding
- Environmental impact and sustainability: The custom plastic injection molding process can have a significant environmental impact, particularly in energy consumption and waste generation. Manufacturers must adopt sustainable practices and explore alternative materials and techniques to reduce their ecological footprint.
- Material waste and recycling: Material waste is an inherent challenge in the custom plastic injection molding process. Manufacturers must adopt strategies to minimize waste, such as optimizing the mold design and production process, reusing and recycling materials, and exploring alternative materials.
- Mold maintenance and repair: Mold maintenance and repair are critical for ensuring consistent quality and precision in the final product. Manufacturers must have a complete maintenance and repair program to ensure the molds are correctly maintained and repaired.
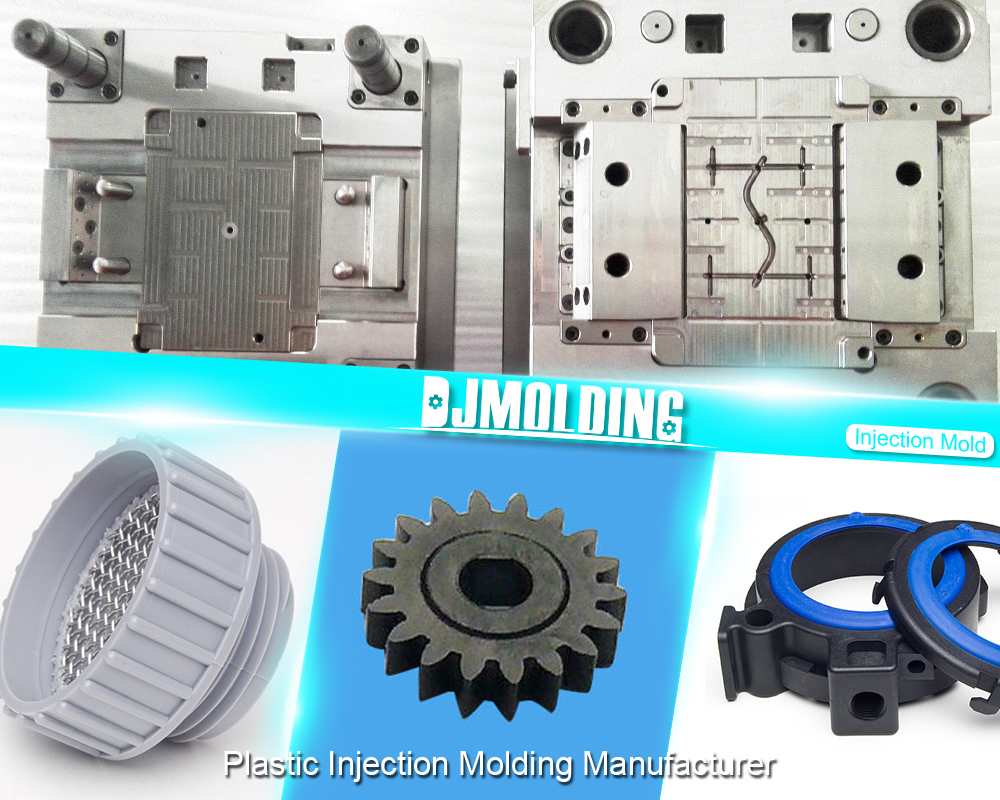
Conclusion
Custom plastic injection molding is a highly versatile and cost-effective manufacturing process that enables the production of high-quality, precision parts for a wide range of industries. The process offers numerous advantages, including design flexibility, cost-effectiveness in mass production, and consistent quality and precision. However, it is essential to choose the proper manufacturer and consider the environmental impact of the process. Manufacturers can ensure the success of their custom plastic injection molding projects by adopting sustainable practices, minimizing waste, and maintaining the molds properly. We encourage readers to explore the possibilities of custom plastic injection molding for their businesses and find a reliable and experienced manufacturer to help them achieve their goals.
For more about custom plastic injection molding manufacturer,you can pay a visit to Djmolding at https://www.djmolding.com/custom-plastic-injection-molding/ for more info.