Comprehensive Guide To PPO Injection Molding: Techniques, Benefits, And Applications
Comprehensive Guide To PPO Injection Molding: Techniques, Benefits, And Applications
Injection molding has revolutionized the manufacturing industry by allowing for the mass production of precise and complex plastic parts. One of the most significant advancements in this area is using Polyphenylene Oxide (PPO) in injection molding processes. PPO, known for its exceptional mechanical properties and heat resistance, has become a preferred choice for various applications across multiple sectors. This article delves into the nuances of PPO injection molding, discussing its advantages, techniques, applications, and best practices for achieving optimal results.
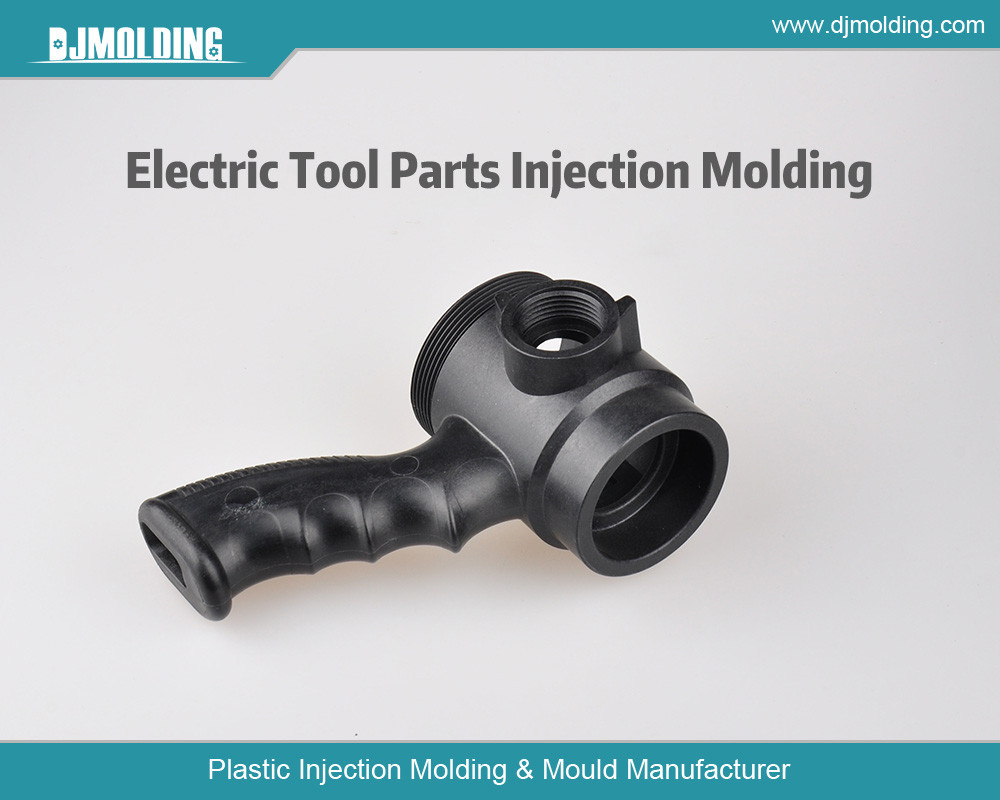
Understanding PPO and Its Properties
What is PPO?
Polyphenylene Oxide (PPO) is an engineering thermoplastic known for its outstanding thermal and mechanical properties. It features high dimensional stability, excellent chemical resistance, and good electrical insulating capabilities, making it suitable for numerous applications. PPO is often blended with polystyrene to enhance its impact resistance and processability.
Key Properties of PPO
- High Thermal Stability: PPO maintains its structural integrity at elevated temperatures, making it ideal for applications requiring thermal resistance.
- Dimensional Stability: The material exhibits minimal shrinkage during cooling, ensuring precision in molded parts.
- Chemical Resistance: PPO is resistant to various chemicals, including oils, solvents, and detergents, which enhances its usability in harsh environments.
- Low Water Absorption: This property prevents swelling and degradation, ensuring longevity in applications exposed to moisture.
- Good Electrical Insulation: PPO’s excellent dielectric properties make it suitable for electrical and electronic applications.
The Injection Molding Process
Overview of Injection Molding
Injection molding is a manufacturing process where molten material is injected into a mold cavity to create a specific shape. The process involves several key steps:
- Material Preparation: PPO pellets are dried to remove moisture, ensuring optimal flow and preventing defects.
- Melting: The dried pellets are heated until they reach a molten state in the injection barrel.
- Injection: The molten PPO is injected into a pre-heated mold under high pressure.
- Cooling: The mold is cooled to solidify the material, allowing the part to maintain its shape.
- Ejection: Once solidified, the part is ejected from the mold.
Advantages of Using PPO in Injection Molding
- Versatility: PPO can be molded into complex shapes and designs, making it suitable for various applications.
- Efficiency: The injection molding process is fast and can produce high volumes of parts, reducing production time and costs.
- Surface Finish: Parts made from PPO exhibit excellent surface quality, which can reduce the need for additional finishing processes.
- Recyclability: PPO can be recycled, aligning with sustainability goals in manufacturing.
Applications of PPO Injection Molding
Automotive Industry
PPO injection molding is widely used in the automotive sector due to its lightweight nature and high strength. Common applications include:
- Electrical Components: PPO’s electrical insulation properties make it ideal for connectors, switch housings, and circuit boards.
- Exterior Trim Parts: Its resistance to UV radiation and chemicals helps maintain the appearance and durability of trim components.
Electrical and Electronics
The electrical and electronics industry benefits significantly from PPO’s insulating properties. Key applications include:
- Insulating Housings: PPO is used for switchgear and breaker housings, providing safety and reliability.
- Circuit Boards: PPO’s thermal stability makes it suitable for manufacturing printed circuit boards.
Consumer Goods
PPO injection molding is prevalent in producing consumer products, including:
- Appliances: Components such as housings for kitchen appliances leverage PPO’s heat resistance.
- Household Items: PPO’s versatility enables producing a wide range of consumer goods, from furniture to toys.
Medical Devices
In the medical field, PPO’s biocompatibility and sterilization capabilities make it a suitable choice for:
- Medical Equipment: Parts that require high cleanliness standards, such as housings and connectors for medical devices.
- Surgical Instruments: PPO’s durability and resistance to sterilization methods make it a preferred instrument material.
Challenges in PPO Injection Molding
Processing Difficulties
While PPO offers numerous advantages, there are challenges in the injection molding process:
- High Processing Temperatures: PPO requires higher temperatures for melting, which may increase energy costs and wear on machinery.
- Moisture Sensitivity: PPO is hygroscopic, meaning it absorbs moisture, which can lead to defects such as bubbling or poor surface finish during molding.
Material Cost
- PPO can be more expensive than other plastics, impacting its feasibility for specific applications. Manufacturers need to weigh the benefits against the material cost to determine suitability.
Best Practices for PPO Injection Molding
Material Preparation
- Drying: Ensure PPO pellets are adequately dried before processing to prevent moisture-related defects.
- Storage: Store PPO in a dry environment to maintain its properties and prevent degradation.
Mold Design Considerations
- Ventilation: Incorporate adequate venting in the mold design to allow trapped air to escape during injection.
- Cooling Channels: Design cooling channels within the mold to ensure even cooling and reduce cycle times.
Process Parameters Optimization
- Temperature Control: Monitor and control the injection and mold temperatures to achieve optimal flow and cooling rates.
- Injection Speed: Adjust the injection speed to minimize shear stress and prevent degradation of PPO during processing.
Future Trends in PPO Injection Molding
Advancements in Material Science
Research in material science is continually evolving, leading to enhanced grades of PPO with improved properties. These advancements may include:
- Blends and Composites: Developing new PPO blends with other materials to enhance performance characteristics.
- Biodegradable Options: As sustainability becomes a priority, researchers are exploring biodegradable alternatives to traditional PPO.
Automation and Industry 4.0
Integrating intelligent technologies and automation in injection molding is set to transform the manufacturing landscape. Future trends may include:
- Predictive Maintenance: Using sensors and data analytics to predict equipment failures and optimize maintenance schedules.
- Real-Time Monitoring: Implementing real-time monitoring systems to improve process control and quality assurance.
Conclusion
PPO injection molding is a highly efficient and versatile manufacturing process, offering numerous benefits across various industries. Its unique properties, such as thermal stability, dimensional accuracy, and chemical resistance, make it a preferred choice for automotive, electronics, consumer goods, and medical device applications. While challenges like processing temperatures and material costs exist, implementing best practices can help manufacturers overcome these hurdles and maximize the advantages of PPO. As technology advances, the future of PPO injection molding looks promising, with ongoing innovations in materials and processes that will further enhance its applications and sustainability. Embracing these advancements will be essential for manufacturers aiming to stay competitive in the evolving landscape of injection molding.
For more about comprehensive guide to ppo injection molding: techniques, benefits, and applications, you can pay a visit to Djmolding at https://www.djmolding.com/ for more info.