Complete Guide To Polystyrene (PS) Injection Molding
Complete Guide To Polystyrene (PS) Injection Molding
Polystyrene (PS) injection molding is a highly versatile manufacturing process for creating intricate and durable plastic parts. Due to its efficiency and cost-effectiveness, this process is widespread in industries such as packaging, automotive, electronics, and consumer goods. Understanding the nuances of PS injection molding can significantly impact production quality and cost. This comprehensive guide will delve into the essential aspects of polystyrene injection molding, from the properties of PS to the technical details of the molding process and best practices for achieving optimal results.
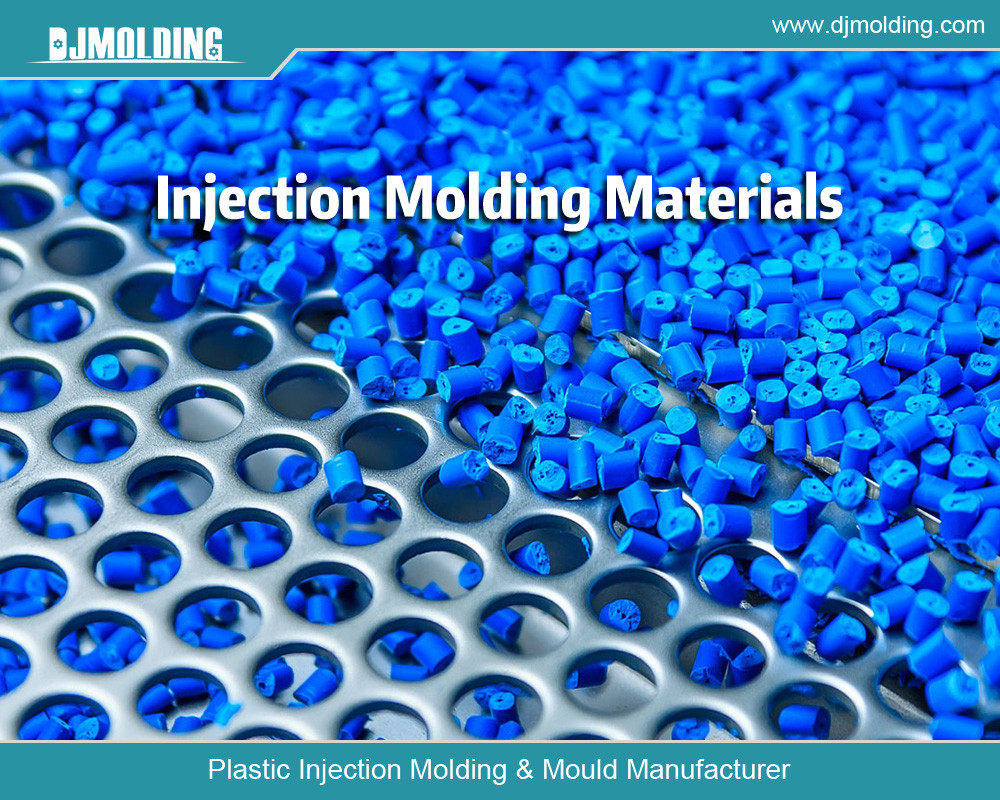
What is Polystyrene (PS)?
Polystyrene is a synthetic aromatic hydrocarbon polymer made from the monomer styrene. It is a lightweight, rigid plastic known for its ease of processing and ability to be molded into various shapes. Polystyrene can be categorized into two main types:
- General Purpose Polystyrene (GPPS): Transparent and glass-like, commonly used in applications like disposable cutlery and CD cases.
- High-impact polystyrene (HIPS): Contains rubber additives to improve its impact resistance. It is used in applications such as refrigerator liners and some packaging materials.
Properties of Polystyrene
Clarity and Gloss:
- PS offers excellent clarity and a glossy finish, making it ideal for applications where visibility is essential.
Rigidity and Brittleness:
- While it is highly rigid, PS is relatively brittle compared to other plastics, affecting its durability.
Thermoformability:
- PS is easy to thermoform, which allows it to be molded into complex shapes with high precision.
Chemical Resistance:
- PS is moderately resistant to chemicals and susceptible to solvents, affecting its longevity in specific environments.
The Injection Molding Process
Injection molding is a manufacturing process where molten plastic is injected into a mold cavity to produce a part. The process is highly automated and suitable for producing large volumes of identical parts. The steps involved include:
Material Preparation:
- Polystyrene pellets are fed into the injection molding machine’s hopper.
- The pellets are then melted in a heated barrel, turning them molten.
Injection:
- The molten polystyrene is injected into a mold cavity under high pressure.
- The pressure ensures that the molten plastic fills all areas of the mold, capturing intricate details.
Cooling:
- Once injected, the plastic is cooled inside the mold to solidify.
- Cooling time depends on the part’s thickness and complexity.
Ejection:
- After cooling, the mold is opened, and the solidified part is ejected.
- Ejection mechanisms include ejector pins, plates, or air blasts.
Post-Processing:
- Parts may require additional finishing processes such as trimming, assembly, or coating.
Critical Advantages of PS Injection Molding
The Complete Guide to Polystyrene (PS) Injection Molding provides an in-depth look at the advantages of this widely used manufacturing process, especially its appeal for high-volume production. Here’s a detailed exploration of the key benefits:
- Cost-Effective: One of the most compelling advantages of PS injection molding is its cost-effectiveness. The process is highly efficient, which translates into lower production costs. Polystyrene is a relatively inexpensive material, and the efficiency of the injection molding process further reduces costs. It makes PS injection molding an ideal choice for producing large quantities of parts without incurring prohibitive expenses. This method offers a clear economic advantage for businesses balancing quality and affordability.
- Precision: Injection molding is celebrated for its accuracy and repeatability. This technique allows for the production of parts with exacting detail and consistency. High-precision molds ensure that each component meets stringent specifications, which is crucial in industries where tolerances are tight, and product consistency is paramount. Whether manufacturing intricate components or large parts, the ability to achieve high precision makes PS injection molding a preferred choice for quality-driven applications.
- Versatility: Polystyrene’s versatility is another critical benefit of injection molding. PS can be molded into various shapes and sizes, accommodating multiple design requirements. This adaptability makes it suitable for different applications, from consumer goods and packaging to automotive and medical components. The flexibility of PS injection molding enables designers and engineers to explore creative solutions and develop products that meet specific functional and aesthetic needs.
- Minimal Waste: A significant advantage of PS injection molding is its efficiency in material use. Compared to other manufacturing methods, the process generates minimal waste. Excess material can often be collected, recycled, and reused in subsequent batches, contributing to sustainability and cost savings. This approach reduces the environmental impact and enhances overall production efficiency, making PS injection molding a more sustainable option.
The Complete Guide to Polystyrene (PS) Injection Molding highlights these key benefits and demonstrates why this technique is favored across various industries. By combining cost-effectiveness, precision, versatility, and minimal waste, PS injection molding is a highly efficient and practical choice for modern manufacturing.
Challenges and Considerations
- Brittleness: The brittleness of PS can be a disadvantage for parts that require impact resistance.
- Temperature Sensitivity: PS can be sensitive to high temperatures, which may limit its use in applications exposed to heat.
- Environmental Impact: Polystyrene is not biodegradable, raising ecological concerns about its disposal and recycling.
Best Practices for PS Injection Molding
Material Selection:
- Choose the correct type of polystyrene-based on the required properties of the end product.
- Ensure that the material is free from contaminants and adequately dried before molding.
Mold Design:
- Design molds with appropriate cooling channels to ensure even cooling and minimize warping.
- Incorporate features like draft angles to facilitate easy ejection of the molded parts.
Machine Settings:
- Optimize temperature settings for melting and injection to ensure consistent material flow and avoid defects.
- Adjust injection pressure and speed to achieve the desired part quality.
Quality Control:
- Implement rigorous quality control measures to inspect molded parts for defects like flash, voids, or warping.
- Regular maintenance of molding equipment is conducted to ensure consistent performance.
Environmental Considerations:
- Explore recycling options for post-consumer and post-industrial PS.
- Consider alternative materials or processes for applications with high environmental impact.
Applications of PS Injection Molding
- Packaging: Polystyrene is widely used for packaging materials such as food containers, cups, and trays.
- Consumer Goods: PS is commonly used to make products like toys, electronic housings, and household items due to its versatility.
- Automotive: PS is used in automotive parts such as interior trims and panels due to its lightweight and easy molding.
- Medical Devices: Certain medical applications use PS for clarity and sterilization ability.
Future Trends and Innovations
The field of injection molding, including PS, is evolving with advancements in technology and materials. Key trends include:
- Sustainable Materials: Development of biodegradable or recyclable alternatives to traditional PS to address environmental concerns.
- Advanced Molding Techniques: Integrating technologies such as 3D printing and intelligent sensors enhances the molding process and improves part quality by providing precise control and detailed insights throughout production.
- Improved Efficiency: Ongoing improvements in molding machinery and processes to reduce cycle times and energy consumption.
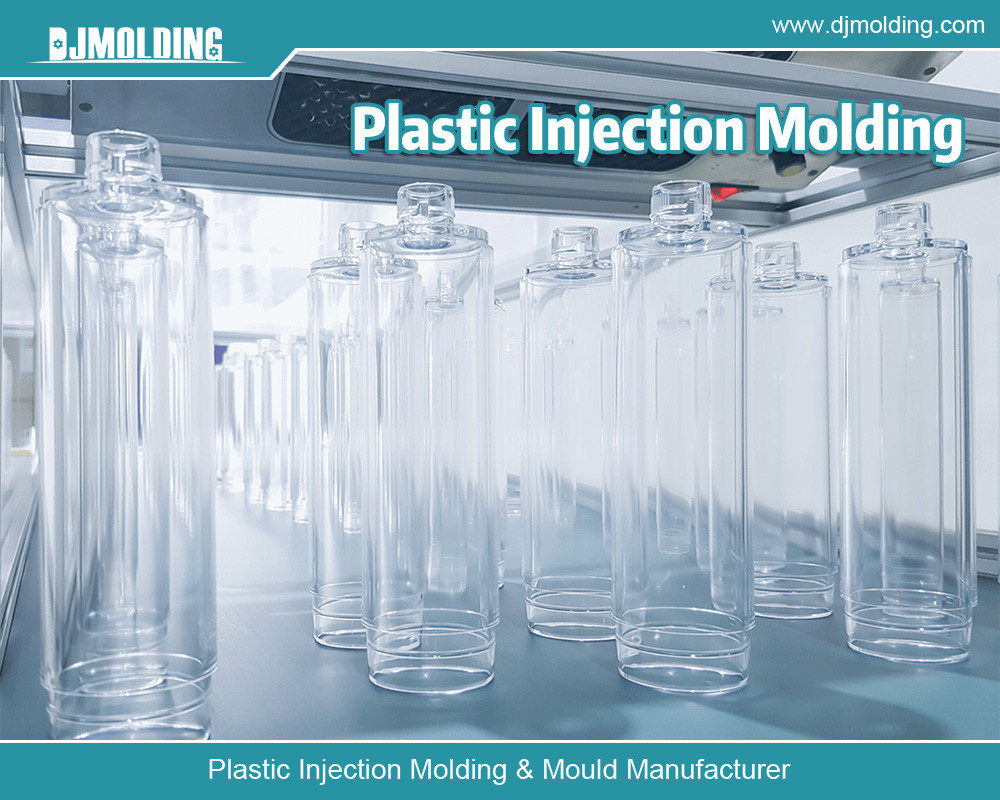
Conclusion
Polystyrene injection molding is a vital process in modern manufacturing, offering a blend of cost-effectiveness, precision, and versatility. Manufacturers can optimize their production processes and achieve high-quality results by understanding PS properties, the molding process’s intricacies, and best practices. As the industry moves towards more sustainable and innovative solutions, staying informed about advancements will be crucial for maintaining competitive advantage and addressing environmental challenges. Whether a seasoned professional or new to the field, this guide provides a solid foundation for mastering PS injection molding and leveraging its benefits in your manufacturing endeavors.
For more about complete guide to polystyrene (ps) injection molding, you can pay a visit to Djmolding at https://www.djmolding.com/molding-service/ for more info.