CNC Machining Service
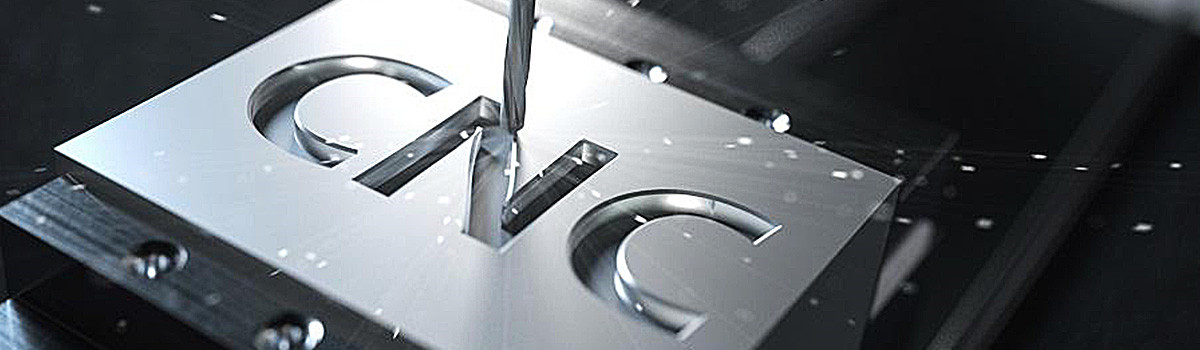
What Is CNC Machining
CNC stands for computer numerical control, which is a technology to control the machining tools automatically by applying a microcomputer that is attached to the tool. CNCs machines would operate according to the coded programmed instructions, such as the movement of the machines, the feed rate of materials, the speed, and so on. There is no need for operators to control the machine manually, thus, CNC helps to improve the efficiency and precision to a large extent.
DJmolding CNC machining capabilities
On-demand CNC machining for rapid prototyping and production parts, experienced and thoroughly vetted DJmolding CNC machine shops.
We operate almost every kind of CNC mill and turning center, and pride ourselves on being able to machine whatever you need, from simple, ‘as-machined’ workholdings to complex, organic geometries with tight tolerances. On request, we can also produce parts with EDM and grinders. Build envelopes, minimum feature sizes and design guidelines vary for milling and turning.
CNC Milling Service
Acording the customer’s CAD files, receive an instant CNC milling quote in 24 hours.
CNC Turning Service
Acording the customer’s CAD files, receive an instant CNC turning quote in 24 hours.
DJmolding CNC milling service capabilities
From prototyping to full production runs. Our 3 axis, 3+2 axis and full 5-axis milling centers will allow you to produce highly accurate and quality parts to meet even your most stringent requirements.
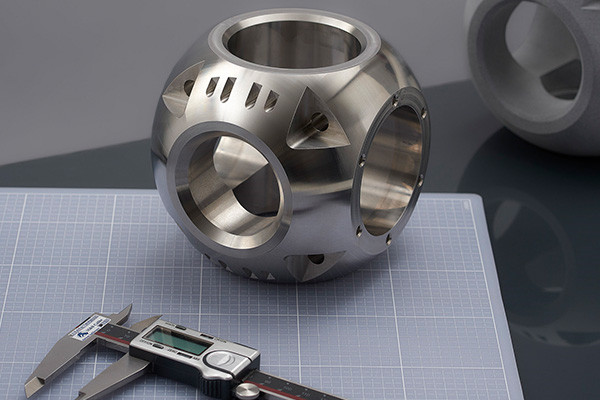
Gallery of CNC machined parts
We machine rapid prototypes and low-volume production orders for customers in multiple industries: aerospace, automotive, defense, electronics, hardware startups, industrial automation, machinery, manufacturing, medical devices, oil & gas and robotics.
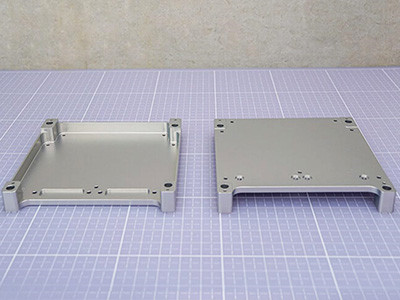
Aluminum 7075-T6
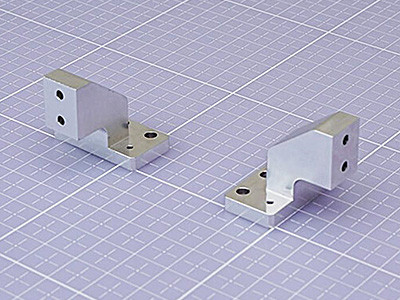
Aluminum 6061-T6
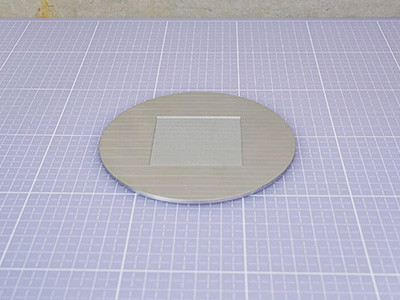
Aluminum 6082
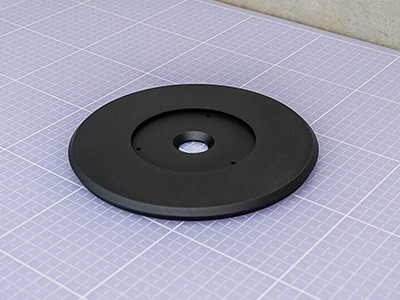
Aluminum 6063
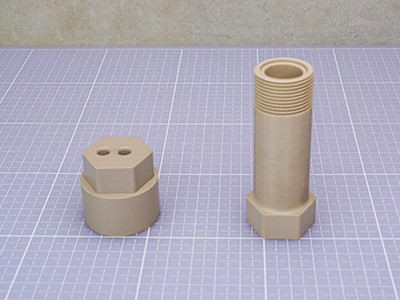
PEEK
Skilled machinists operate a CNC machine by programming tool paths based on the geometry of the final machined parts. The part geometry information is provided by a CAD (computer-aided design) model. CNC machines can cut almost any metal alloy and rigid plastic with high precision and repeatability, making custom machined parts suitable for nearly every industry, including aerospace, medical, robotics, electronics, and industrial. DJmolding provides CNC services and offers custom CNC quotes on over 40 materials ranging from commodity aluminum and acetal to advanced titanium and engineered plastics like PEEK and Teflon.
Available surface finishes for CNC machining
Surface finishes are applied after machining and can change the appearance, surface roughness, hardness and chemical resistance of the produced parts.
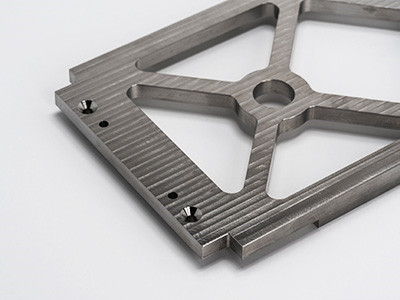
As machined (Ra 3.2μm / Ra 126μin)
This is our standard finish. Parts are machined and deburred, sharp edges are chamfered.
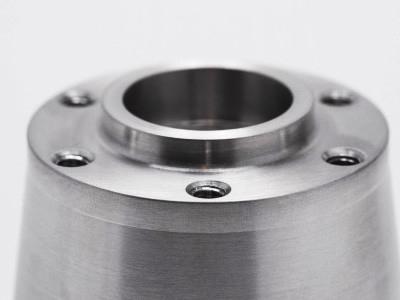
Smooth machining (Ra 1.6μm / Ra 63μin)
Smooth machining is like an ‘As machined’ finish but with slightly less evident machine marks. Parts are machined at a lower feed, no hand polishing is applied.
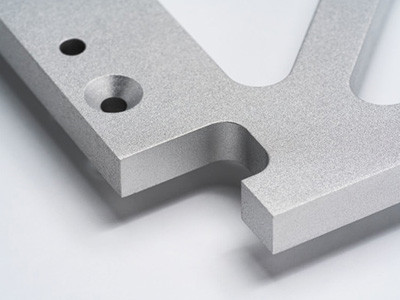
Bead Blasted
Parts are bead blasted with glass beads which results in a grainy texture.
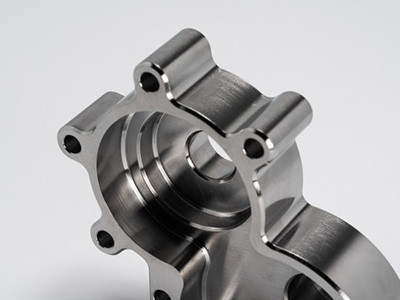
Brushed + Electropolished (Ra 0.8μm / Ra 32μin)
Parts are brushed and electropolished. Ideal to reduce the micro-roughness of the part.
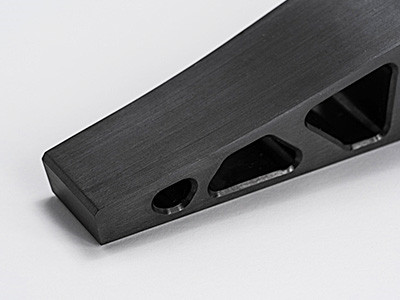
Black oxide
Applicable on steels, black oxide is a conversion coating used to improve corrosion resistance and minimize light reflection.
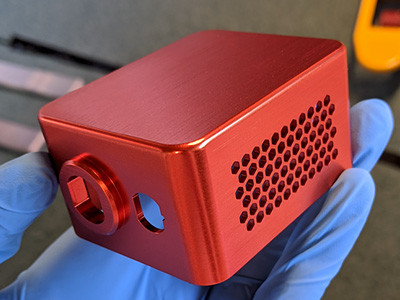
Brushed + Anodized type II (Glossy)
Parts are brushed and then anodized type II. Ideal for increasing the corrosion resistance of the part. Typically results in a glossy color.
CNC (Computer Numerical Control) machines are the backbone of modern manufacturing. They have revolutionized the manufacturing process by offering precision, speed, and flexibility to produce complex parts and components. However, to ensure that CNC machines operate at their optimal level, they require regular maintenance, repairs, and servicing. CNC machine service providers offer a range of services to ensure that these machines operate efficiently and effectively. In this blog post, we will discuss the various aspects of CNC machine service and how it benefits manufacturing businesses.
What is CNC Machine Service?
CNC stands for Computer Numerical Control, which refers to a machine controlled by a computer program. CNC machines are used for various tasks, including cutting, drilling, milling, and turning.
CNC machine services involve using these machines to perform highly accurate and repeatable precision tasks. These services are often used in manufacturing, requiring precise and consistent parts.
To use a CNC machine, a program is first created using computer-aided design (CAD) software. The program is then uploaded to the machine, which uses the instructions to perform the desired operation on a piece of material.
CNC machines can be used with various materials, including metal, plastic, wood, and composites. They offer many benefits, including faster production times, higher accuracy, and the ability to create complex shapes and features.
Why is CNC Machine Service Important?
CNC (Computer Numerical Control) machines have become essential in manufacturing industries, especially in automotive, aerospace, and medical device production. These machines are automated, so they can operate for extended periods without human intervention. CNC machines can produce complex parts with high precision and accuracy, making them crucial in manufacturing.
CNC machine service is essential for several reasons. First and foremost, it ensures that the machines are operating at their optimal level. CNC machines have many moving parts that require regular maintenance to prevent wear and tear, which could lead to machine breakdowns and production downtime. Routine maintenance and servicing help detect and address potential issues before they become significant problems.
Secondly, CNC machine service helps improve the lifespan of the machine. Regular servicing ensures that the devices operate within their designed parameters, reducing the risk of premature wear and tear. This extends the machine’s lifespan, saving the manufacturer money in replacement and repair costs.
Thirdly, CNC machine service helps maintain consistent quality in production. CNC machines are programmed to produce parts with high precision and accuracy, which is essential in aerospace and medical device production. Regular servicing ensures the machines function correctly, creating pieces that meet the required specifications and maintaining consistent output quality.
Fourthly, CNC machine service helps improve safety in the workplace. CNC machines are powerful tools that require careful handling to prevent accidents. Regular servicing helps identify potential safety hazards, which can be addressed before they cause harm to operators or damage to machines.
Types of CNC Machines
CNC (Computer Numerical Control) machines are widely used in various industries for precision manufacturing. These machines use computerized control systems to automate and execute complex machining operations with high accuracy and efficiency. There are several types of CNC machines available, each designed for specific applications. Here are some of the most common types:
CNC Milling Machines
- Vertical Machining Centers (VMC):These machines have a vertically oriented spindle and are suitable for cutting and shaping solid materials.
- Horizontal Machining Centers (HMC):HMCs have a horizontally oriented spindle and are ideal for machining large and heavy workpieces.
- 5-Axis Machines:These machines offer simultaneous movement in five axes, enabling complex and intricate machining operations.
CNC Lathe Machines
Turning Centers:These machines are used for precision turning operations, where the workpiece rotates while cutting tools shape the material.
- Swiss-Type Lathes:Swiss-type lathes are designed for high-precision and small-diameter workpieces. They feature a sliding headstock and guide bushing for enhanced accuracy.
CNC Plasma Cutters
- Plasma cutting machines use a high-velocity jet of ionized gas to cut through electrically conductive materials like steel, aluminum, and copper. They are commonly used in metal fabrication and industrial applications.
CNC Laser Cutting Machines
- Laser cutting machines utilize a focused laser beam to melt, burn, or vaporize materials, resulting in precise and clean cuts. They are versatile and can handle various materials such as metal, wood, acrylic, and plastics.
CNC Router Machines
- CNC routers are primarily used for cutting, shaping, and engraving materials like wood, plastic, and foam. They are widely used in woodworking, signage production, and prototyping.
CNC EDM Machines
- Electrical Discharge Machining (EDM) machines use electrical discharges to remove material from the workpiece. They are commonly used for complex shapes and hardened materials like hardened steel and titanium.
CNC Grinding Machines
- Grinding machines are used to achieve high-precision surface finishes and accurate dimensions. They utilize abrasive wheels to remove material from the workpiece.
CNC Press Brakes
- Press brakes are used for bending and shaping sheet metal. CNC-controlled press brakes offer precise control over the bending process, resulting in accurate and repeatable results.
Common CNC Machine Problems
While CNC machines are highly efficient and reliable, they can still experience certain issues that can affect their performance and productivity. Understanding and addressing these common problems is essential for ensuring smooth operation. Here are some of the typical CNC machine problems:
Programming Errors
- Incorrect or incomplete programming instructions can lead to errors in machining operations.
- Improper tool paths or incorrect tool selection can result in poor surface finish, dimensional inaccuracies, or tool breakage.
Mechanical Issues
Worn or damaged components like bearings, belts, or ball screws can cause excessive play, leading to inaccurate cuts and reduced precision.
- Poor lubrication or inadequate maintenance can result in increased friction, overheating, and premature wear of machine parts.
Electrical and Electronic Problems
Power fluctuations or electrical interference can cause erratic machine behavior, such as sudden stops, resets, or incorrect positioning.
- Faulty sensors or limit switches may lead to incorrect machine movements or false error readings.
Tooling Problems
- Dull or improperly installed cutting tools can cause poor surface finish, chatter, or excessive tool wear.
- Incorrect tool offsets or tool length measurements can result in dimensional inaccuracies.
Cooling and Chip Removal Issues
- Insufficient coolant flow or improper chip evacuation can lead to heat buildup, tool overheating, and reduced tool life.
- Inadequate chip removal can cause chip clogging, which affects surface finish and can damage the workpiece or machine.
Software and Control System Errors
- Software glitches or compatibility issues can disrupt machine operation and result in unexpected errors or crashes.
- Inaccurate calibration or incorrect parameter settings within the control system can lead to positioning errors or incorrect feed rates.
Environmental Factors
- Temperature variations, humidity, or dust can affect the performance and accuracy of CNC machines.
- Improper installation or positioning of the machine in relation to environmental factors can impact its stability and reliability.
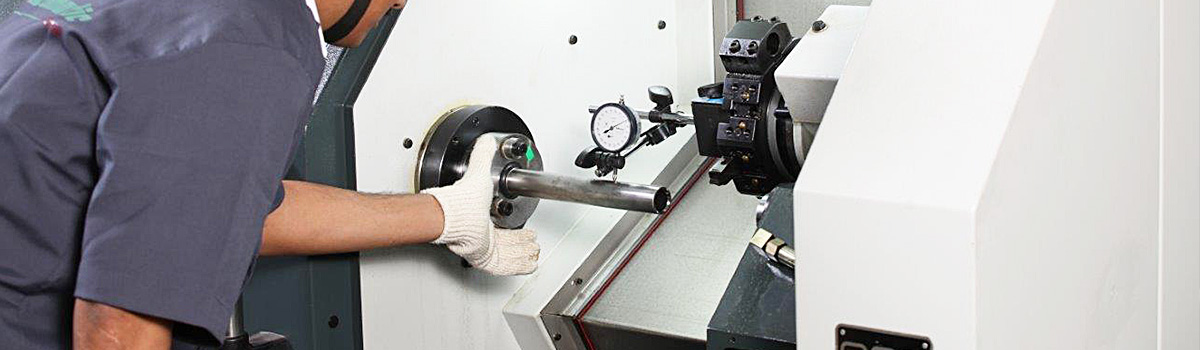
Preventive Maintenance for CNC Machines
Implementing a proactive preventive maintenance program is essential for maximizing the performance, reliability, and lifespan of CNC (Computer Numerical Control) machines. Regular maintenance helps identify potential issues before they become major problems, reduces downtime, and ensures optimal machine operation. Here are some key areas to focus on when performing preventive maintenance for CNC machines:
Lubrication
- Regularly lubricate machine components such as bearings, ball screws, slideways, and gears according to manufacturer guidelines.
- Use the appropriate lubricants and ensure proper lubrication intervals to minimize friction, reduce wear, and maintain smooth operation.
Cleaning
- Keep the machine and its surrounding area clean from chips, coolant residues, and debris.
- Regularly clean filters, coolant tanks, and chip trays to maintain optimal coolant performance and prevent clogging.
Inspection and Calibration
Perform routine inspections of critical components such as spindles, tool holders, and fixtures to identify signs of wear or damage.
- Calibrate and check the accuracy of machine axes, tool offsets, and positioning systems to ensure precise machining.
Electrical and Electronic Components
- Inspect electrical connections, cables, and wiring for any signs of damage or loose connections.
- Check and test sensors, limit switches, and safety interlocks to ensure proper functionality.
Cooling Systems
- Maintain and clean coolant systems regularly to prevent contamination and ensure proper cooling.
- Monitor coolant levels, pH balance, and concentration, and replenish or replace coolant as necessary.
Software and Control System
- Regularly update and maintain the CNC machine’s software and control system with the latest versions and patches.
- Verify and calibrate the control system parameters, such as feed rates and acceleration, to ensure accurate machining.
Tooling and Spindle
- Inspect and clean tool holders, collets, and spindle tapers regularly to ensure proper tool clamping and minimize runout.
- Check and replace worn or damaged cutting tools to maintain optimum cutting performance and surface finish.
Operator Training and Documentation
- Provide comprehensive training to machine operators on proper operation, maintenance procedures, and safety protocols.
- Maintain detailed records of maintenance activities, inspections, and repairs for reference and analysis.
Routine Inspection of CNC Machines
Regular inspection and maintenance of CNC (Computer Numerical Control) machines is crucial to ensure their optimal performance and longevity. By conducting routine inspections, potential issues can be identified early on and preventive measures can be taken to avoid costly breakdowns and production delays. Here are some key points to consider during the routine inspection of CNC machines:
Visual Inspection
- Begin by visually inspecting the machine for any signs of wear, damage, or loose components.
- Check for leaks, such as oil or coolant, which may indicate a problem with the machine’s fluid systems.
- Look for any abnormal noise or vibration during machine operation.
Lubrication
- Verify that all lubrication points are adequately lubricated to ensure smooth movement of machine components.
- Check lubricant levels and top them up if necessary.
- Ensure proper lubrication of ball screws, guide rails, and other critical components.
Axis Calibration
Verify the accuracy of the machine’s axes by performing calibration tests.
- Check for any deviations from the specified tolerances and adjust if required.
- Calibrate the machine’s probing system, if applicable, to ensure accurate measurement.
Spindle Inspection
- Inspect the spindle for any signs of wear, damage, or misalignment.
- Check the spindle bearings and replace them if necessary.
- Verify the spindle runout to ensure concentricity during machining operations.
Tooling and Tool Changer
- Inspect the tooling system, including holders, collets, and cutting tools, for any signs of wear or damage.
- Check the tool changer mechanism for smooth operation and proper alignment.
- Clean and lubricate the tool changer components as per manufacturer guidelines.
Control System
- Inspect the CNC control unit and monitor for any error messages or malfunctions.
- Ensure all cables and connections are secure and in good condition.
- Update the machine’s software, if applicable, to the latest version provided by the manufacturer.
Safety Features
- Verify the functionality of safety features, such as emergency stop buttons and interlocks.
- Check the condition of protective covers and barriers to ensure operator safety.
- Test the machine’s alarm system to confirm proper functioning.
Documentation:
Maintain a detailed record of inspection dates, findings, and any maintenance or repairs performed.
- Follow the manufacturer’s recommended maintenance schedule and guidelines.
- Keep a log of any spare parts used and their corresponding serial numbers.
CNC Machine Repairs
When a CNC (Computer Numerical Control) machine experiences issues or malfunctions, prompt repairs are essential to minimize downtime and maintain productivity. Repairing CNC machines requires expertise and attention to detail to ensure the machines are restored to their optimal working condition. Here are some key points to consider when conducting repairs on CNC machines:
Diagnostics
- Begin by thoroughly diagnosing the problem to identify the root cause of the malfunction.
- Inspect the machine’s components, such as motors, drives, sensors, and control system, to pinpoint the faulty part.
- Utilize diagnostic tools and software to assist in identifying the issue accurately.
Replacement of Faulty Components
- Once the problem has been identified, replace the faulty components with new or properly functioning ones.
- Source genuine parts from reputable suppliers to ensure compatibility and reliability.
- Follow the manufacturer’s guidelines for replacing specific components and calibrate them if required.
Electrical and Mechanical Repairs
- Conduct electrical repairs, including fixing faulty wiring, connectors, or damaged circuit boards.
- Repair or replace damaged mechanical components, such as belts, gears, pulleys, and bearings.
- Ensure proper alignment of mechanical parts to maintain precision and accuracy.
Software Updates and Configuration
- Update the machine’s software to the latest version provided by the manufacturer.
- Configure the CNC control system parameters and settings according to the machine’s specifications.
- Test and validate the machine’s performance after software updates or configuration changes.
Calibration and Alignment
Calibrate the machine’s axes and ensure they are properly aligned to achieve accurate machining.
- Verify the spindle runout and alignment to ensure concentricity during operations.
- Check and adjust the machine’s tool offsets and tool length compensation for precise cutting.
Testing and Validation
Conduct comprehensive testing of the repaired machine to ensure it functions correctly.
- Verify the machine’s accuracy and repeatability by performing test cuts or using calibration artifacts.
- Monitor the machine’s performance during various machining operations to ensure stability and reliability.
Preventive Maintenance
Recommend and perform routine preventive maintenance tasks to minimize future breakdowns.
- Clean and lubricate machine components regularly to prevent wear and improve longevity.
- Keep a record of maintenance activities, including dates, performed tasks, and any replaced parts.
Training and Support
Provide training to machine operators on proper usage and maintenance to prevent common issues.
- Offer ongoing technical support and guidance to troubleshoot minor problems that may arise.
- Promote a culture of proactive machine care and encourage operators to report any abnormalities promptly.
CNC Machine Upgrades
CNC (Computer Numerical Control) machines are designed to be durable and long-lasting, but with advancements in technology, upgrading them can improve their performance and capabilities. Upgrading CNC machines can enhance their efficiency, speed, and accuracy, providing businesses with a competitive edge. Here are some key points to consider when upgrading CNC machines:
Assessing the Current State
Begin by assessing the current state of the machine, including its hardware and software.
- Evaluate the machine’s age, condition, and compatibility with the latest upgrades.
- Determine the desired outcomes of the upgrade, such as improved speed, accuracy, or additional functionality.
Identifying Upgrade Options
- Research the latest technology and advancements to identify suitable upgrades for the machine.
- Consult with the machine’s manufacturer or third-party vendors to determine the best upgrades for the specific machine model.
- Consider options such as improved controllers, spindle systems, tool changers, and sensors.
Upgrading Hardware Components
- Upgrade hardware components such as motors, drives, and control systems to improve speed and accuracy.
- Install new sensors and probes to enhance measurement accuracy and automate certain functions.
- Replace worn or outdated parts with new ones to improve machine durability and longevity.
Upgrading Software
- Upgrade the machine’s software to the latest version to improve functionality and performance.
- Install new software modules to enable additional functions or improve existing ones.
- Configure the software to match the specific machine’s requirements.
Testing and Validation
- Test the upgraded machine to ensure it functions correctly and meets the desired outcomes.
- Validate the machine’s accuracy and repeatability by performing test cuts or using calibration artifacts.
- Monitor the machine’s performance during various machining operations to ensure stability and reliability.
Training and Support
- Provide training to machine operators on the new features and functionalities of the upgraded machine.
- Offer ongoing technical support and guidance to troubleshoot any issues that may arise.
- Promote a culture of proactive machine care and encourage operators to report any abnormalities promptly.
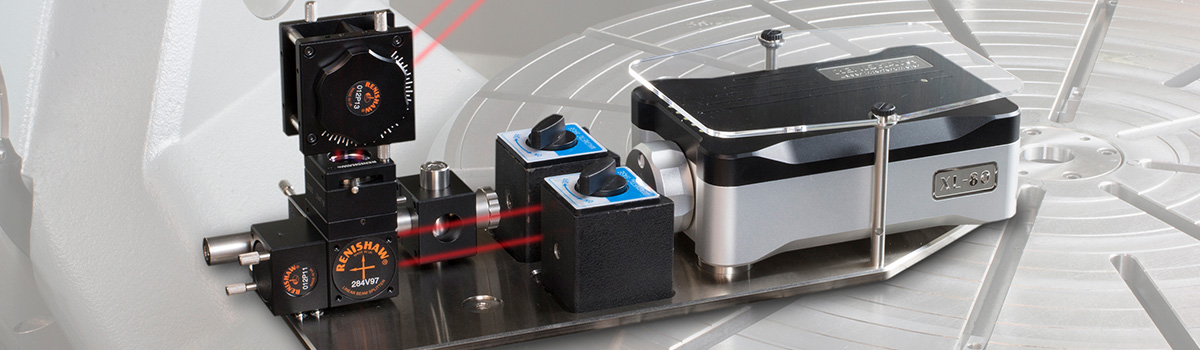
CNC Machine Calibration
Calibration is a crucial process in maintaining the accuracy and precision of CNC (Computer Numerical Control) machines. Regular calibration ensures that the machine’s axes, spindle, and tooling systems are aligned correctly, resulting in accurate machining operations. Here are some key points to consider when performing CNC machine calibration:
Axis Calibration
- Calibrate each axis of the machine to ensure accurate positioning and movement.
- Use precision measurement tools, such as laser interferometers or ball bar systems, to measure deviations and perform adjustments.
- Verify that the machine’s linear and angular movements align with the specified tolerances.
Spindle Runout Measurement:
- Measure the spindle runout to ensure concentricity during machining operations.
- Use a dial indicator or laser-based tool to measure any eccentricity or wobbling in the spindle.
- Adjust the spindle components or replace worn parts to minimize runout and maximize accuracy.
Tool Length and Tool Offset Calibration
- Calibrate the tool length measurement system to ensure accurate tool positioning.
- Use calibration artifacts or height gauges to measure the actual tool length and compare it with the machine’s measurements.
- Adjust the tool length offset values in the machine’s control system to compensate for any discrepancies.
Tool Diameter Compensation
- Perform tool diameter compensation calibration to account for variations in tool diameters.
- Measure the actual tool diameter using a micrometer or caliper and compare it with the machine’s programmed values.
- Adjust the tool offset or tool compensation values to compensate for any differences and achieve accurate cuts.
Probing System Calibration
- If the machine has a probing system, calibrate it to ensure precise part measurement and alignment.
- Perform calibration routines to verify the accuracy of the probing system and adjust if necessary.
- Confirm that the probing system accurately detects workpiece locations and dimensions.
Spindle Speed Calibration
- Calibrate the spindle speed to ensure it matches the specified RPM (Rotations Per Minute).
- Use a tachometer or spindle speed sensor to measure the actual spindle speed during operation.
- Adjust the speed control parameters in the machine’s control system to achieve the desired RPM.
Documentation and Records
- Maintain a detailed record of calibration activities, including dates, performed tasks, and any adjustments made.
- Follow the manufacturer’s recommended calibration schedule and guidelines.
- Keep a log of any calibration artifacts used and their corresponding certifications.
CNC Machine Alignment
Proper alignment is crucial for CNC (Computer Numerical Control) machines to operate with accuracy and precision. Misalignment of the machine’s components, such as the spindle, tooling systems, and axes, can result in errors and inconsistencies in the machining process. Here are some key points to consider when aligning CNC machines:
Checking the Machine’s Condition
Before aligning the machine, check its condition, including the condition of its components.
- Inspect the machine’s ways, leadscrews, and other mechanical components for wear and damage.
- Verify the condition of the spindle and tooling systems.
Alignment of the Spindle
- The spindle is a crucial component that must be aligned accurately.
- Use precision measurement tools, such as a dial indicator or laser-based tool, to measure the spindle’s alignment.
- Adjust the spindle’s position and components, such as the bearings, to achieve proper alignment.
Checking the Axes
- Check the alignment of each axis of the machine to ensure accurate movement and positioning.
- Use precision measurement tools to measure the deviation in each axis and perform adjustments.
- Verify that the axes move in a straight line and align with the specified tolerances.
Aligning the Tooling Systems
- The tooling systems, including the tool holders and tool changers, must be aligned correctly to ensure accurate tool positioning.
- Use precision measurement tools to measure the tooling systems’ alignment and perform adjustments if necessary.
- Verify that the tooling systems align with the machine’s axes and spindle.
Testing and Validation
- After aligning the machine, perform test cuts to ensure its accuracy and precision.
- Use calibration artifacts or other measurement tools to validate the machine’s alignment and accuracy.
- Monitor the machine’s performance during various machining operations to ensure its stability and reliability.
Maintenance and Care
- Regularly inspect and maintain the machine’s mechanical components to prevent misalignment and wear.
- Train machine operators to report any abnormalities promptly and perform routine maintenance tasks.
- Follow the manufacturer’s recommended maintenance schedule and guidelines.
Proper alignment of CNC machines is essential for achieving accurate and precise machining operations. By adhering to proper alignment procedures and performing regular maintenance, operators can ensure their machines consistently produce high-quality parts with minimal errors and rework.
Lubrication of CNC Machines
Proper lubrication is crucial for the smooth and efficient operation of CNC (Computer Numerical Control) machines. Lubricants minimize friction, reduce wear and tear, dissipate heat, and protect the machine’s components from damage. Regular lubrication maintenance helps prolong the lifespan of the machine and ensures optimal performance. Here are some key points to consider when lubricating CNC machines:
Selection of Lubricants
- Choose lubricants recommended by the machine’s manufacturer for specific components and systems.
- Consider factors such as temperature, speed, load, and environment when selecting lubricants.
- Use appropriate lubricants for different machine components, such as spindle bearings, guide rails, and ball screws.
Lubrication Schedule
- Follow the manufacturer’s recommended lubrication schedule for each component of the machine.
- Establish a regular lubrication routine based on machine usage and operating conditions.
- Take into account factors such as operating hours, intensity of use, and environmental conditions.
Lubrication Points
- Identify and mark all lubrication points on the machine, including oil ports, grease fittings, and reservoirs.
- Ensure that all lubrication points are easily accessible and visible for efficient lubrication.
Lubrication Methods
- Use the appropriate lubrication methods for each component, such as oil baths, oil mist systems, or manual grease application.
- Follow proper lubrication techniques, such as applying the right amount of lubricant and ensuring even distribution.
- Utilize automated lubrication systems, if available, for consistent and precise lubrication.
Lubricant Application
- Clean the lubrication points before applying lubricant to remove dirt, debris, and old lubricant residues.
- Use the recommended lubricant applicators, such as brushes, grease guns, or oil cans, to apply lubricants accurately.
- Ensure that the lubricant reaches all necessary areas, such as bearings, gears, and sliding surfaces.
Lubricant Quantity
- Apply the appropriate amount of lubricant as specified by the machine’s manufacturer.
- Avoid over-lubrication, as excess lubricant can cause contamination and clog vital components.
- Monitor lubricant levels regularly and replenish as needed to maintain the required lubrication.
Lubricant Quality
- Use high-quality lubricants that meet industry standards and specifications.
- Monitor the condition of lubricants, such as viscosity, cleanliness, and oxidation level, and replace them when necessary.
- Store lubricants properly to maintain their quality and effectiveness.
Record Keeping
- Maintain a detailed record of lubrication activities, including dates, lubricants used, and lubrication points addressed.
- Keep track of lubricant consumption, including quantities used and restocked.
- Use the record as a reference for future lubrication maintenance and troubleshooting.
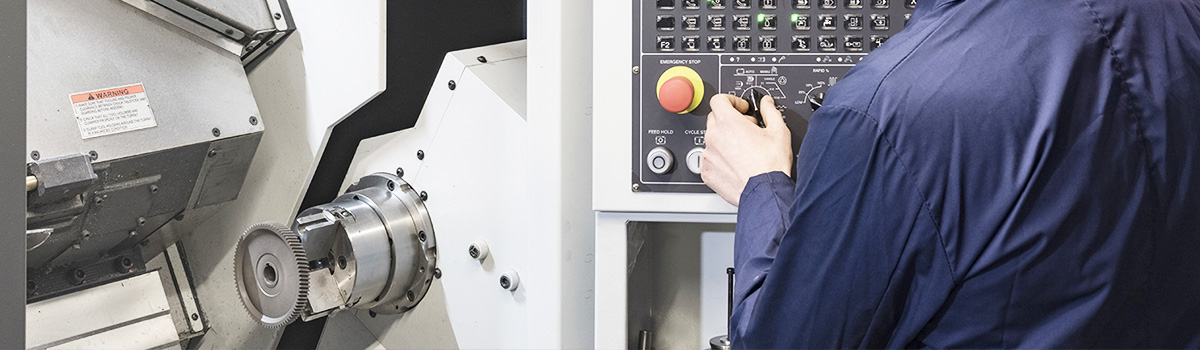
Replacement of CNC Machine Parts
Over time, CNC (Computer Numerical Control) machines may require the replacement of certain parts due to wear, damage, or the need for upgrades. Prompt and accurate replacement of CNC machine parts is essential to maintain the machine’s performance and minimize downtime. Here are some key points to consider when replacing CNC machine parts:
Identify the Problem
- Thoroughly diagnose the machine to identify the faulty or damaged part.
- Analyze the symptoms, error messages, or abnormal machine behavior to pinpoint the problem.
- Utilize diagnostic tools and consult the machine’s documentation or manufacturer’s guidelines for troubleshooting.
Source Genuine Parts
- Purchase replacement parts from reputable suppliers or directly from the machine’s manufacturer.
- Ensure the parts are genuine and match the specifications of the original parts.
- Consider factors such as quality, compatibility, and warranty when selecting replacement parts.
Disassembly and Installation
- Follow proper procedures and guidelines for disassembling the machine and removing the faulty part.
- Take necessary precautions to protect sensitive components and ensure personal safety during disassembly.
- Carefully install the replacement part, following the manufacturer’s instructions and recommended torque specifications.
Calibration and Testing
- After replacing the part, calibrate the machine to ensure proper functioning and alignment.
- Perform necessary adjustments or alignments to ensure accuracy and precision.
- Conduct thorough testing to verify that the replacement part has resolved the issue and the machine operates correctly.
Documentation and Record Keeping
- Maintain detailed records of the replaced parts, including the date, part number, and supplier information.
- Keep a log of the machine’s maintenance history, including all replacements, repairs, and upgrades.
- Use the documentation as a reference for future maintenance and troubleshooting.
Preventive Maintenance
- Regularly inspect and maintain the machine to identify potential issues before they lead to part failures.
- Follow the manufacturer’s recommended preventive maintenance schedule for the machine and its components.
- Replace parts proactively based on usage, expected lifespan, or known vulnerabilities.
Training and Support
- Provide training to machine operators and maintenance personnel on proper part replacement procedures.
- Offer ongoing technical support and guidance to troubleshoot any issues that may arise during or after part replacement.
- Foster a culture of proactive maintenance and encourage operators to report any abnormalities promptly.
By following these key points and working with reputable suppliers and experienced technicians, the replacement of CNC machine parts can be conducted effectively. Timely and accurate part replacement helps ensure the machine’s optimal performance, extends its lifespan, and minimizes disruptions to production schedules.
Servicing of CNC Machine Spindles
CNC (Computer Numerical Control) machine spindles play a crucial role in the precision and performance of machining operations. To ensure optimal functionality and longevity, regular servicing of CNC machine spindles is essential. Here are some key points to consider when it comes to the servicing of CNC machine spindles:
Preventive Maintenance
- Scheduled maintenance is critical to avoid unexpected downtime and costly repairs.
- Create a maintenance schedule that includes regular inspections and servicing tasks.
- Follow the manufacturer’s recommendations for maintenance intervals and procedures.
Cleaning and Lubrication
- Clean the spindle regularly to remove debris, dust, and coolant residue that can affect performance.
- Use appropriate cleaning agents and techniques recommended by the manufacturer.
- Lubricate the spindle components according to the specified guidelines to ensure smooth operation and prevent wear.
Belt and Bearing Inspection
- Check the condition of belts for signs of wear, cracks, or damage. Replace them if necessary.
- Inspect bearings for excessive noise, vibration, or heat buildup, which may indicate a need for replacement or adjustment.
- Properly align and tension belts to maintain optimal power transmission.
Coolant System Maintenance
- Regularly clean and maintain the coolant system to prevent contamination and clogging.
- Check coolant levels, filters, and pumps for proper operation.
- Monitor coolant quality and replace it when necessary to maintain optimal cutting conditions and prevent spindle damage.
Spindle Runout and Balance
- Measure spindle runout using precision tools to ensure concentricity and accuracy.
- Balance the spindle if excessive vibration or uneven cutting is observed.
- Address any issues promptly to avoid potential damage to the spindle or workpiece.
Electrical System Inspection
- Check the electrical connections, wiring, and sensors for signs of damage or malfunction.
- Test spindle motor and drive performance to ensure proper functioning.
- Calibrate speed control systems to maintain accurate spindle RPM.
Expert Assistance
- Engage qualified technicians or manufacturers’ representatives for complex servicing or repairs.
- Regularly train operators and maintenance staff on proper handling and maintenance procedures.
- Seek professional advice for troubleshooting issues beyond routine maintenance.
CNC Machine Electrical System Inspection
The electrical system of a CNC machine is a critical component that directly affects its performance and reliability. Regular inspection of the electrical system is necessary to ensure safe operation and optimal functionality. Here are some key points to consider when conducting an electrical system inspection for CNC machines:
Visual Inspection
- Start by visually inspecting the electrical components for signs of damage, such as loose wires, frayed cables, or burnt connectors.
- Check for any loose connections or terminals that may affect the electrical conductivity.
- Look for evidence of overheating, such as discoloration or melting of components.
Power Supply
- Ensure that the machine is receiving the correct voltage and that the power supply is stable and properly grounded.
- Inspect the main power cables and connections for any signs of wear or damage.
- Test the functionality of the circuit breakers and fuses to ensure they are providing adequate protection.
Control Cabinet
- Open the control cabinet and inspect the internal components, such as the circuit boards, relays, and contactors.
- Look for signs of overheating, such as burnt marks or a strong smell of burnt insulation.
- Check that all cables and connectors are securely fastened and properly labeled.
Motor and Drive Systems
- Inspect the motors and drives for any signs of damage, such as loose wires or worn-out brushes.
- Test the functionality of motor drives and ensure that they are providing smooth and precise motion control.
- Measure the motor current to ensure it is within the specified range for proper operation.
Emergency Stop System
- Test the emergency stop buttons to ensure they are functioning correctly and can immediately halt the machine in case of an emergency.
- Check the wiring and connections of the emergency stop system for any faults or loose connections.
Communication Interfaces
- Inspect the communication interfaces, such as Ethernet or serial ports, to ensure they are working correctly.
- Test the communication links with external devices, such as computers or programmable logic controllers (PLCs), to ensure proper data transfer.
Grounding System
- Verify that the machine’s grounding system is properly installed and connected.
- Check the integrity of the grounding wires and connections to prevent electrical hazards and ensure electrical noise reduction.
Regular Maintenance
- Establish a regular maintenance schedule for the electrical system, including cleaning, tightening connections, and inspecting cables.
- Follow the manufacturer’s guidelines for recommended maintenance procedures and intervals.
- Train operators and maintenance staff on electrical safety and proper handling of the CNC machine.
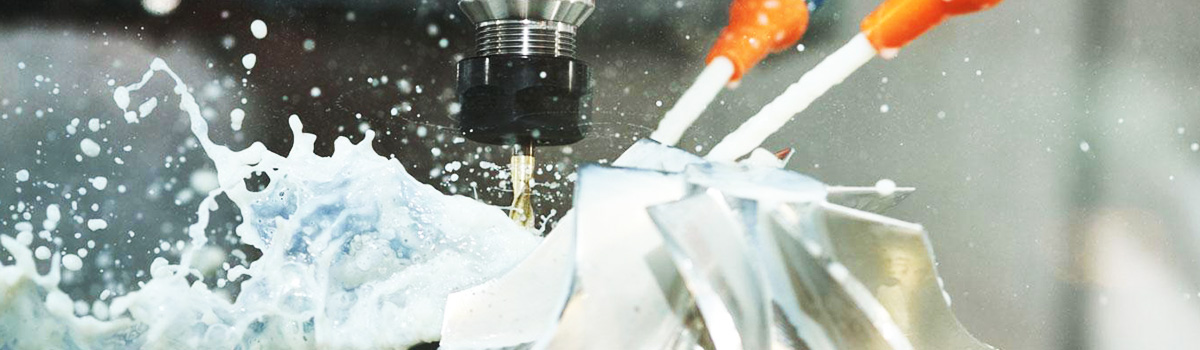
Cooling System Maintenance for CNC Machines
The cooling system of CNC (Computer Numerical Control) machines plays a crucial role in maintaining optimal operating temperatures, prolonging tool life, and ensuring machining accuracy. Proper maintenance of the cooling system is essential to prevent overheating, maintain coolant quality, and avoid potential damage to the machine. Here are some key points to consider when it comes to cooling system maintenance for CNC machines:
Regular Cleaning
- Clean the coolant tank, filters, and cooling channels regularly to remove debris, chips, and sludge.
- Use appropriate cleaning agents and techniques recommended by the machine manufacturer.
- Flush the system periodically to ensure the coolant flow is not obstructed.
Coolant Concentration
- Monitor and maintain the proper concentration of coolant in the system according to the manufacturer’s specifications.
- Test the coolant regularly using refractometers or test kits to ensure it meets the recommended levels.
- Adjust the concentration by adding fresh coolant or water as necessary.
Filtration System
- Check and clean the coolant filters regularly to remove contaminants and prevent clogging.
- Replace the filters according to the recommended intervals or when they become excessively dirty or damaged.
- Consider using high-quality filters or magnetic separators to improve filtration efficiency.
Coolant Quality
- Monitor the coolant’s pH level, viscosity, and chemical composition to ensure it remains within the acceptable range.
- Test for bacterial growth or contamination that can lead to foul odors or deteriorated coolant performance.
- Replace the coolant if it shows signs of degradation or fails to meet the required performance standards.
Pump and Flow Rate
- Inspect the coolant pump for proper operation, checking for any leaks, unusual noise, or reduced flow rate.
- Clean or replace the pump impeller if it becomes worn or damaged.
- Verify that the coolant flow rate is within the recommended range to ensure effective cooling.
Coolant Temperature Control
- Check the temperature control system, such as the chiller or heat exchanger, to maintain the coolant temperature within the specified range.
- Inspect sensors, valves, and control mechanisms to ensure accurate temperature regulation.
- Clean or replace heat exchanger fins if they become clogged with dirt or debris.
Operator Training
- Provide training to machine operators on proper coolant handling, including refilling, adjusting concentration, and reporting coolant-related issues.
- Instruct operators on recognizing signs of coolant degradation or system malfunction and how to respond appropriately.
- Promote a culture of cleanliness and proactive coolant system maintenance among operators.
Servicing CNC Machine Controls and Software
Regular servicing of the CNC machine controls and software is crucial to ensure optimal performance and avoid potential issues. Here are some key points to consider when it comes to servicing CNC machine controls and software:
Software Updates
- Regularly update the CNC machine’s software to benefit from the latest features, bug fixes, and performance improvements.
- Follow the manufacturer’s guidelines and recommendations for updating the software.
- Create backups of the machine’s current software version before performing updates.
Calibration and Alignment
- Periodically calibrate and align the CNC machine controls to maintain accuracy and precision.
- Check and adjust axes alignment, tool offsets, and workpiece zero positions.
- Verify the accuracy of probe systems, if applicable, and recalibrate if necessary.
Backup and Restore
- Regularly back up critical machine parameters, settings, and programs to prevent data loss.
- Keep multiple copies of backups on external devices or cloud storage for added security.
- Test the restoration process periodically to ensure backups are reliable and accessible.
Control Panel Inspection
- Visually inspect the control panel for any signs of damage, such as broken buttons, loose connectors, or malfunctioning indicators.
- Clean the control panel and buttons regularly to remove dust or debris that may affect operation.
- Test the functionality of the control panel by verifying each button, switch, and display.
Electrical Connections
- Inspect the electrical connections within the control cabinet for any loose or corroded wires.
- Tighten any loose connections and replace damaged cables or connectors.
- Perform a thorough electrical system inspection to ensure proper grounding and minimize the risk of electrical faults.
Maintenance of Input Devices
- Check the functionality of input devices, such as keyboards, mice, or touchscreens.
- Clean input devices to remove dirt or residue that may interfere with their operation.
- Replace worn-out or malfunctioning input devices to maintain smooth and accurate control.
Operator Training
- Provide operators with comprehensive training on CNC machine controls and software.
- Familiarize operators with the various functions, menus, and parameters of the control interface.
- Instruct operators on the proper use of software features and troubleshooting techniques.
Regular System Checks
- Conduct periodic system checks to identify potential software or control issues.
- Monitor error logs, alarms, and diagnostic messages for any anomalies.
- Perform system diagnostic tests and follow the manufacturer’s guidelines for troubleshooting and resolving issues.
CNC Machine Safety Checks
Ensuring the safety of operators and the workplace is of utmost importance when working with CNC (Computer Numerical Control) machines. Here are some key points to consider when conducting CNC machine safety checks:
Machine Enclosure
- Inspect the machine enclosure to ensure it is intact, properly secured, and free from any cracks or damage.
- Verify that all access doors, panels, and safety interlocks are functioning correctly.
- Check for proper visibility of warning signs, labels, and emergency stop buttons.
Emergency Stop System
- Test the emergency stop buttons to ensure they immediately halt machine operation when pressed.
- Verify that the emergency stop system is in proper working condition and easily accessible to operators.
- Train operators on the correct use of emergency stop buttons and their locations.
Electrical Safety
- Inspect the electrical components for any exposed wires, loose connections, or damaged insulation.
- Ensure that the electrical system is properly grounded to minimize the risk of electrical shocks.
- Regularly check that circuit breakers and fuses are in good working order.
Tooling and Workpiece Safety
- Inspect tooling, such as cutting tools or clamps, for damage, wear, or incorrect installation.
- Check workpieces for secure positioning and proper clamping to avoid displacement during machining.
- Monitor tool wear and replace tools as necessary to maintain safe and efficient cutting.
Emergency Lighting
- Ensure that the workplace has adequate emergency lighting in case of power outages or other emergencies.
- Test emergency lighting regularly to ensure it functions properly and illuminates the area effectively.
Fire Safety
- Verify the availability and functionality of fire extinguishers in the vicinity of the CNC machine.
- Train operators on the proper use of fire extinguishers and the evacuation procedures in case of a fire.
- Clear the area around the CNC machine of any flammable materials or debris.
Operator Training and Awareness
- Provide comprehensive training to operators on safe operating procedures and potential hazards specific to the CNC machine.
- Promote a culture of safety awareness and encourage operators to report any safety concerns promptly.
- Conduct regular safety meetings or toolbox talks to address safety topics and reinforce safe practices.
Compliance with Safety Standards
- Ensure that the CNC machine meets relevant safety standards and regulations in the operating jurisdiction.
- Stay updated on any changes or updates to safety standards and incorporate them into the safety checks.
- Engage with safety professionals or consultants, if necessary, to ensure compliance and best practices.
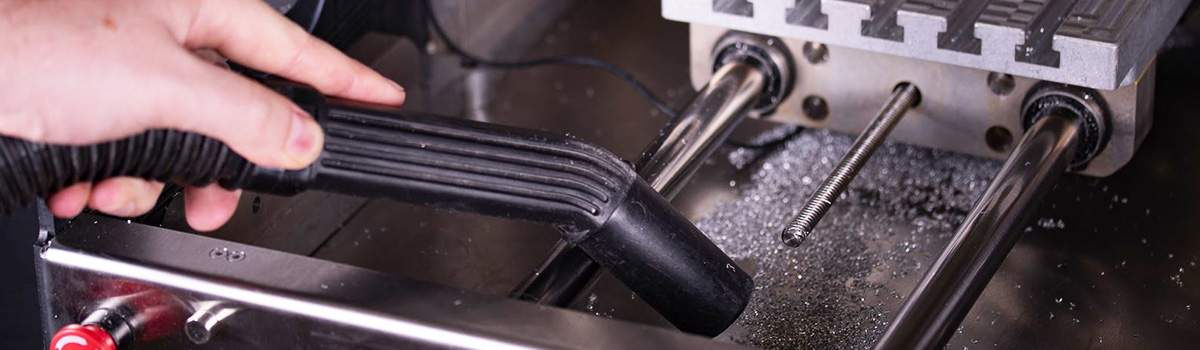
CNC Machine Cleaning
Regular cleaning and maintenance of CNC machines are crucial for their efficiency, accuracy, and overall lifespan. By following these cleaning practices, operators can ensure that their CNC machines remain in optimal condition, minimizing downtime and maximizing productivity.
- Maintaining a clean and well-maintained CNC (Computer Numerical Control) machine is essential for its optimal performance and longevity. Regular cleaning of the machine helps to prevent the buildup of debris, dust, and chips that can lead to mechanical issues and inaccuracies in machining.
- Start by turning off the machine and disconnecting it from the power source to ensure safety during the cleaning process.
- Begin by removing any loose chips, debris, or cutting fluids from the work area using a vacuum or brush. Pay attention to hard-to-reach areas, such as crevices and corners, where debris tends to accumulate.
- Wipe down the machine surfaces with a clean, lint-free cloth and a mild detergent solution. Avoid using abrasive cleaners that can damage the machine’s finish. Be thorough in cleaning all exposed surfaces, including the table, spindle, tool holders, and enclosure.
- Clean the coolant tank and replace the cutting fluids regularly. Dirty or contaminated cutting fluids can affect the machine’s performance and the quality of the finished products.
- Inspect the filters and screens in the coolant system, air filtration system, and lubrication system. Clean or replace these components as necessary to ensure proper filtration and fluid flow.
- Pay special attention to the machine’s spindle and tool changer mechanisms. Remove any debris or buildup that may interfere with their smooth operation. Lubricate these components according to the manufacturer’s guidelines to maintain optimal performance.
- Check the cover and bellows for any signs of damage or wear. Replace them if necessary to protect the machine’s internals from contamination.
- Finally, inspect the electrical connections, cables, and wiring. Ensure that they are secure and free from damage. Clean the control panel and buttons with a mild cleaner to remove any dirt or grime.
- Keep a regular cleaning schedule and document maintenance activities. This helps in tracking the cleaning frequency and identifying any potential issues early on.
CNC Machine Training and Support
By providing comprehensive training and ongoing support, operators can develop the necessary skills and confidence to operate CNC machines effectively. A well-trained workforce contributes to improved productivity, reduced downtime, and higher quality outputs.
- Proper training and ongoing support are essential for operators to effectively utilize CNC (Computer Numerical Control) machines and maximize their potential. Training programs provide operators with the knowledge and skills necessary to operate, program, and troubleshoot CNC machines.
- Start by providing comprehensive training on the basics of CNC technology, including understanding machine components, tooling, and programming fundamentals. This foundation helps operators grasp the core concepts and terminology associated with CNC machines.
- Introduce operators to CAD/CAM software used for creating part designs and generating machining programs. Training on these software tools enables operators to efficiently program CNC machines and optimize machining processes.
- Provide hands-on training sessions where operators can practice setting up the machine, loading tools, and running machining operations. This practical experience helps build confidence and familiarity with the machine’s operation.
- Emphasize safety protocols and best practices during training. Operators should be trained on proper machine startup and shutdown procedures, handling of cutting tools, and the use of personal protective equipment (PPE) to ensure a safe working environment.
- Offer training on machine maintenance and preventive care. Operators should learn how to inspect and maintain critical components, such as spindles, way covers, and lubrication systems, to keep the machine running smoothly.
- Provide ongoing support through manuals, documentation, and online resources. A comprehensive user manual that covers machine operation, programming examples, troubleshooting guides, and maintenance procedures can serve as a valuable reference for operators.
- Establish a support system where operators can seek assistance and guidance when encountering challenges or issues. This can be in the form of a dedicated support team, technical helpline, or online forums where operators can connect with experienced CNC users.
- Conduct periodic refresher training sessions to reinforce knowledge and skills. CNC technology evolves over time, so keeping operators up to date with the latest advancements and techniques ensures they can make the most of the machine’s capabilities.
- Encourage operators to participate in industry events, trade shows, and workshops to expand their knowledge and network with other professionals in the field. These events provide opportunities for learning about new technologies, sharing experiences, and gaining insights into best practices.
Cost of CNC Machine Service
Understanding the cost factors associated with CNC machine service is essential for budgeting and planning.
- The cost of CNC (Computer Numerical Control) machine service can vary depending on several factors, including the type of service required, the complexity of the machine, and the service provider’s rates. Understanding these factors is crucial for budgeting and ensuring a cost-effective maintenance plan.
- Routine preventive maintenance is a common service for CNC machines. It typically includes tasks such as inspection, cleaning, lubrication, and calibration. The cost of preventive maintenance can range from a few hundred to several thousand dollars per year, depending on the machine’s size and complexity.
- Emergency or unscheduled repairs are another aspect of CNC machine service that can affect costs. These repairs are often unforeseen and require immediate attention to minimize downtime. The cost will depend on the severity of the issue, the availability of replacement parts, and the expertise required to resolve the problem. Emergency repairs can range from a few hundred to several thousand dollars.
- Some service providers offer service contracts or maintenance plans that cover both routine preventive maintenance and emergency repairs. These contracts can provide cost savings and peace of mind by ensuring prompt service and reducing the risk of unexpected expenses. The cost of service contracts varies based on factors such as the machine’s age, complexity, and the level of coverage provided.
- Spare parts and consumables are additional costs to consider when servicing CNC machines. Components such as motors, sensors, belts, and bearings may need replacement over time. The cost of these parts will depend on the machine’s brand, model, and availability. It is recommended to maintain an inventory of commonly used spare parts to minimize downtime and reduce shipping costs.
- On-site service visits may incur additional costs, such as travel expenses, accommodation, and technician fees. These costs can vary depending on the location of the machine and the service provider’s policies. Remote diagnostics and troubleshooting options may be available, which can help reduce the need for on-site visits and associated costs.
- It is advisable to obtain quotes from multiple service providers to compare costs and services offered. Consider the reputation, experience, and expertise of the service provider, as well as their response time and availability for urgent situations.
- Investing in regular maintenance and timely repairs can help minimize long-term costs. Neglecting maintenance can lead to more frequent breakdowns, reduced machine lifespan, and increased repair expenses.
Conclusion
CNC machine service is essential to ensure that these machines operate efficiently and effectively. CNC machine service providers offer a range of services to maintain, repair, and upgrade these machines to ensure that they meet the needs of manufacturing businesses. Regular maintenance, inspections, and repairs are critical to prevent downtime and reduce the risk of expensive repairs. By investing in CNC machine service, businesses can ensure that they maximize the potential of their CNC machines and improve their overall productivity.