Choosing The Best Low Volume Plastic Injection Molding Service Near Me: A Comprehensive Guide
Choosing The Best Low Volume Plastic Injection Molding Service Near Me: A Comprehensive Guide
The industrial sector is being revolutionized by low-volume injection molding, which provides an affordable option for small-scale production. Due to its capacity to offer lower costs, faster lead times, and more adaptability, low-volume plastic injection molding has become very important across a range of industries. In this article, we will discuss small-scale injection molding and its pros and cons over traditional production techniques, appropriate use instances, content and design issues, the procedure involved, financial considerations, and things to think about when selecting a small-scale injection molding supplier.
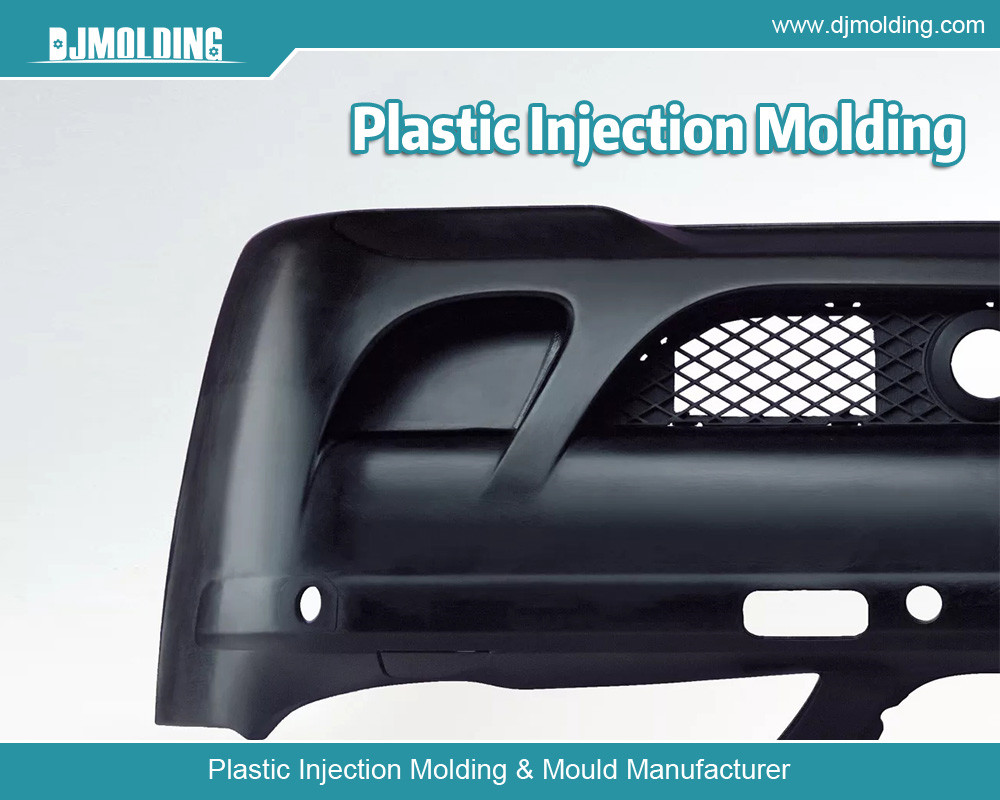
Recognizing the Definition of Low Volume Injection Molding and Its Principal Features
Low-volume injection casting is a manufacturing process that uses injection molding techniques to produce small parts. It offers the advantages of both classic injection molding and fast prototyping, enabling effective manufacturing with lower lead times and tooling costs.
Traditional Manufacturing’s Benefits
Compared to conventional manufacturing techniques, minimal-volume injection molding has a number of benefits. By reducing material waste and doing away with the need for expensive tooling, it lowers expenses. Faster market entry and product iterations are made possible by the reduced lead times. Numerous sectors, such as limited production runs, specialized markets, and prototyping, are supported by low-volume injection molding.
Suitable Use Cases
Application areas for low-volume injection molding are numerous. It facilitates iterative design modifications prior to large-scale production, which is advantageous for prototyping. Low-volume production’s flexibility helps niche markets by offering tailored items for particular client segments. Additionally, restricted production runs are accommodated by low-volume injection molding, which also lowers inventory costs and addresses variations in demand.
Materials and Thoughts into Design
Many materials can be injected into low-volume injection molding, such as engineering-grade resins, thermoplastics, and elastomers. Achieving the best outcomes requires careful consideration of design issues. Careful consideration must be given to elements including wall thickness, draft angles, undercuts, and part complexity. Manufacturers are able to adapt molds to meet particular design specifications.
Procedure for Creating a Low-Capacity Injection Mold
Making a mold is the first step in the low-volume molding by injection process. Mold design is the process of converting an innovative part into a three-dimensional mold while taking cooling, gating, and part ejection into account. Depending on the demands of the project, a variety of mold fabrication techniques, including additive manufacturing and CNC machining, can be used.
Procedure for Injection Molding
The injection molding procedure starts as soon as the mold is prepared. It consists of multiple processes, the first of which is material selection, in which the right resin is selected according to the final part’s desired qualities. After being warmed and pumped into the cavity of the mold, the material goes through a cooling process. At last, the completed part is ejected by someone opening the mold.
Examination and quality assurance
To guarantee the manufacture of high-quality parts in low volume through injection molding, quality control is essential. Examination methods that confirm the part complies with specifications include dimension analysis, visual examination, and functional testing. Mechanical, thermal energy, and chemical testing are among the testing methods used to confirm the part’s functionality.
Cost Factors and Advantages
Low-volume molding by injection has several advantages over conventional manufacturing techniques in terms of cost. Now let’s discuss a few important points:
Decreased Tooling Costs:
A major financial advantage of low-volume molding by injection is the significant decrease in tooling costs. Small-scale production is hampered by the need for costly molds and tooling in traditional manufacturing. Low-volume molding by injection makes tooling more accessible and inexpensive for organizations with tight budgets by allowing for significant tooling cost reductions.
Minimal material waste:
When using traditional production techniques, there is frequently a large amount of material waste, particularly in the setup and testing stages. This can raise expenses and cause environmental issues. By carefully regulating the quantity of material pumped into the mold, low-volume injection molding eliminates material waste, which lowers costs and supports sustainable manufacturing practices.
Faster Time-to-Market:
In today’s cutthroat business environment, time truly is money. Because low-volume molding by injection has shorter lead times than typical production, it allows for a quicker time to market. From mold development to production, the simplified procedure allows for faster iterations and modifications. Businesses that are responsive to shifting customer expectations or operate in quickly changing industries may particularly benefit from this quick turnaround time.
Customization and flexibility:
High levels of customization and flexibility are possible with low-volume injection molding. Businesses can quickly adapt designs and make changes to satisfy unique client needs. This degree of personalization reduces the need for pricey post-production edits or rework, which saves money and boosts client satisfaction.
Savings on Limited Manufacturing Runs:
Low-volume molding by injection is especially economical for goods for specialized markets or small manufacturing runs. Businesses have the option to create modest quantities on demand rather than acquire large-scale manufacturing equipment. By using this strategy, you can cut storage costs, minimize keeping excess inventory, and lessen the likelihood of producing too much.
Flexibility and risk reduction:
Before committing to large-scale manufacturing, businesses may evaluate the market and validate consumer demand using low-volume injection molding, which enables them to increase production gradually. Because of its scalability, organizations can lower the financial risks involved with mass production by adjusting production volumes in response to market demand.
Increased Profit Margins:
By lowering tooling costs, cutting down on material waste, and enabling quicker time-to-market, low-volume injection-molded products can increase profit margins. Businesses can improve financial results by streamlining production processes, cutting expenses, and raising efficiency.
Selecting the Best Provider of Low Batch Injection Molding
Selecting a low-volume injection-molded product supplier can be challenging for organizations because there are a lot of things to take into account. The following crucial aspects will assist you in choosing wisely:
Experience:
Seek out a supplier who has successfully completed small-scale injection molding projects in the past. A seasoned supplier is probably equipped with the skills and know-how necessary to produce top-notch goods.
Quality Control:
In injection molding, quality control is essential since even small flaws can cause major production delays and expenses. To guarantee that the finished product satisfies your requirements, make sure the supplier has an effective quality control system.
Customization:
Injection molding can produce a wide range of products, from tiny components to enormous parts. Seek a supplier who can alter their offerings to suit your requirements in terms of manufacturing volume, mold design, and material choice.
Cost:
While cost is always a component to be taken into account, it shouldn’t be the sole one. Seek out a supplier who can provide good customer service and high-quality products at a competitive price.
Environmental Responsibilities:
Selecting a supplier dedicated to sustainable production methods is crucial as environmental issues gain importance. Seek out a supplier who recycles garbage and uses environmentally friendly products and procedures.
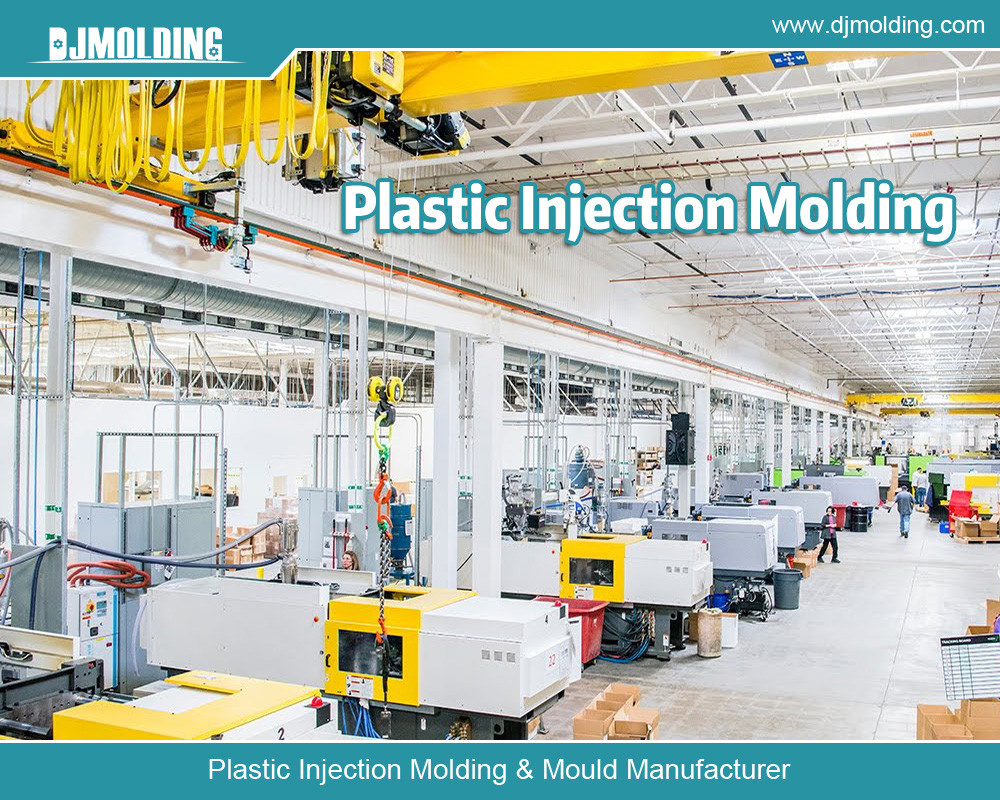
In summary
For small-scale production, low-volume resin injection molding offers an economical and practical alternative. Due to its benefits over conventional manufacturing techniques, which include lower prices, faster lead times, and more flexibility, it is now a popular choice across a range of industries. Through comprehension of the procedure, evaluation of materials and design elements, and selection of an appropriate supplier, enterprises can effectively utilize low-volume injection molds to enhance their manufacturing tactics and attain prosperity in the marketplace.
For more about choosing the best low volume plastic injection molding service near me: a comprehensive guide,you can pay a visit to Djmolding at https://www.djmolding.com/molding-service/ for more info.