Case in the UK
DJmolding’s Solutions for Warpage Defect in Injection Molding
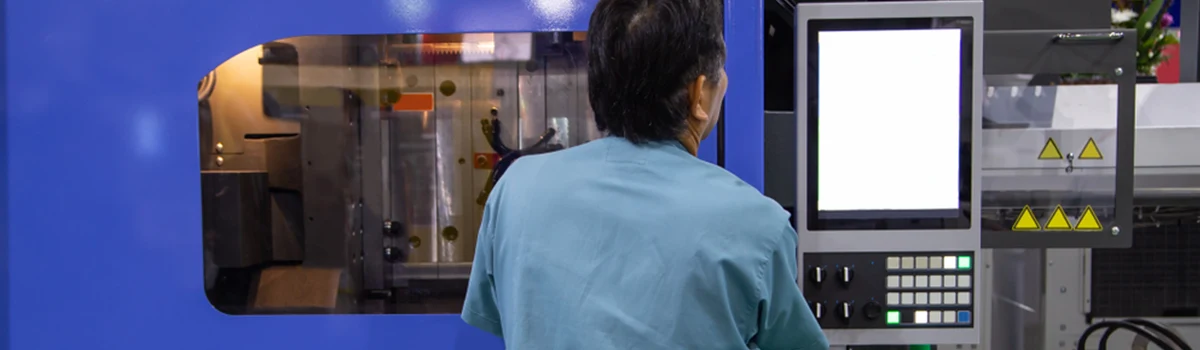
DJmolding’s Customer from the UK, they used to purchase the plastic injection parts from English domestic manufacturing, but there were always Warpage Control problems existing.
DJmolding deal Warpage Control very well, for this reason this company form the UK corperates with DJmolding now.
Mold Warping: Common Problems and DJmolind’s Solutions for Warpage Control
Warpage in plastic injection molding is when the intended shape of the molded part is distorted during the cooling process. Mold warping can cause the part to fold, bend, twist or bow.
In order to determine what is causing molding warpage you’ll need to know:
*How much your parts warp
*What direction the warpage tends to occur
*What that means in relation to the mating requirements of your parts
When it comes to warpage in plastic injection molding, there are 3 main problems: Cooling Rate, Cavity Pressure & Fill Rate. However, there are multiple contributing factors that can cause such molding problems.
Below we discuss common mold warping problems and their solutions:
Problem: Inadequate Injection Pressure or Time
If there is not enough injection pressure the plastic material will cool and solidify before the mold is properly packed.
If there is inadequate mold injection hold time, the packing process is minimized.
If there is inadequate mold injection pressure or hold time the molecules will not be constrained, which allows them to move around uncontrolled during the cooling process. This causes the part to cool at different rates and results in mold warpage.
DJmolding’s Solution: Increase mold injection pressure or hold time.
Problem: Inadequate Residence Time
Residence time is the amount of time the resin is exposed to heat in the barrel. If there is inadequate residence time the molecules will not absorb heat uniformly throughout the material. The under-heated material will become stiff and will cool before the mold is properly packed. This causes the molecules to shrink at different rates during the cooling process which results in mold warpage.
DJmolding’s Solution: Increase residence time by adding time to the cooling process of the cycle. This will ensure the material receives the proper amount of residence time and eliminate mold warping.
Problem: Barrel Temperature too Low
If the barrel temperature is too low, the resin is not able to heat up to the proper flow temperature. If the resin is not at proper flow temperature and is pushed into the mold it will solidify before the molecules are properly packed. This causes the molecules to shrink at varying rates which produces mold warpage.
DJmolding’s Solution: Increase barrel temperature. Make sure material melt temperature is homogenous for the entire shot size.
Problem: Mold Temperature Too Low
If there is insufficient mold temperature the molecules will solidify prior to packing and at different rates, causing mold warpage.
DJmolding’s Solution: Increase mold temperature based on the resin supplier’s recommendations and adjust accordingly. In order to allow the process to re-stabilize, operators should allow 10 cycles for every 10 degree change.
Problem: Uneven Mold Temperatures
Uneven mold temperatures cause molecules to cool and shrink at an uneven rate, resulting in mold warpage.
DJmolding’s Solution: Check mold surfaces that are in contact with the molten resin. Determine if there is more than a 10 degree F temperature difference using a pyrometer. If the temperature difference is greater than 10 degrees between any 2 points, including between the mold halves, a difference in shrink rates will occur and mold warping will happen.
Problem: Nozzle Temperature too Low
Since the nozzle is the final transfer point from the barrel to the mold, it’s essential to analyze. If the nozzle is too cold, the resin’s travel time can slow which prevents the molecules from getting properly packed. If the molecules don’t pack evenly, they will shrink at different rates which causes mold warping.
DJmolding’s Solution: First, the operator should ensure that the nozzle design is not interfering with the flow rate as some nozzles are not designed for the resin being used. If the proper nozzle is being used for the flow and resin, the operator should adjust the nozzle temperature by 10 degrees Fahrenheit until mold warpage resolves.

Problem: Improper Flow Rate
Resin manufacturers provide specific formulations for a range of standard flow rates. Using those standard flow rates as a guide, the operator should select an easy flow material for thinly walled products and a stiffer material for thicker walled products. The operator should use the stiffest material possible for thin or thick walled products since a stiffer flow improves the mold’s physical properties. However, the stiffer the material is the harder it is to push. Difficulty in pushing the material may result in the material solidifying before full packing can take place. This results in varying molecule shrink rates, which creates mold warping.
DJmolding’s Solution: Operators should work with the resin supplier to determine which material will have the stiffest flow rate without causing warpage.
Problem: Inconsistent Process Cycle
If the operator opens the gate too soon and the product is ejected before the material incurred proper and even cooling time, the operator has shortened the process cycle. An inconsistent process cycle can lead to uncontrolled shrinkage rates, which then causes mold warping.
DJmolding’s Solution: Operators should use an automatic process cycle and only interfere if an emergency occurs. Most importantly, all employees should be instructed on the criticality of maintaining consistent process cycles.
Problem: Inadequate Gate Size
Inadequate gate size restricts the flow rate of the molten resin as it tries to pass through. If the gate size is too small it can cause the plastic filling rate to slow down enough to cause a huge pressure loss from point-of-gate to last-point-to-fill. This restriction can cause physical stress to the molecules. This stress is released after injection, which results in mold warp.
DJmolding’s Solution: Mold gate size and shape should be optimized based on the resin supplier’s data. Usually, the best solution for mold warpage is to increase the gate size as much as possible.
Problem: Gate Location
Aside from gate size, gate location can also be a contributing factor to mold warping. If the gate location is in a thin area of the part geometry and the last-point-to-fill is a much thicker area, it can cause the filling rate to pass from thin to thick, which causes a very large pressure drop. This huge pressure loss can result in a short/inadequate fill.
DJmolding’s Solution: The mold may need to be redesigned in order to move the gate location so that the mechanical part properties required by the finished product can be achieved.
Sometimes, additional gates must be added in order to reduce pressure loss & reduce molded-in stress.
Problem: Lack of Ejection Uniformity
If the mold’s ejection system and press are not inspected and adjusted regularly, they can operate improperly and produce uneven ejection force or part perpendicular inaccuracies. These malfunctions can cause stresses in the mold as it tries to resist ejection. The stresses cause mold warping after ejection and cooling have taken place.
DJmolding’s Solution: Operators should ensure regular inspection and adjustments of the ejection system and press. All adjusting devices should be locked down to ensure components are properly lubricated and to eliminate slipping.
Problem: Product Geometry
Product geometry can also be an issue that causes mold warpage. Part geometry can result in many combinations of filling patterns that can cause plastic shrink to be different throughout the cavity. If the geometry is producing an inconsistent shrink rate warpage can occur, especially if there are high levels of pressure loss in areas of thin vs thick wall stock.
DJmolding’s Solution: Consult a custom plastic injection molder who specializes in engineering-grade resins to identify an optimal solution. At DJmolding, we have Master Molders who are trained and certified by highly regarded industry resources.
DJmolding is plastic Injection molding manufacturer, and we can solve the injection molding preblems, not only for the Enland but over the world.
If you’re having warpage defects in your injection molding that you haven’t been able to resolve, turn to the specialists at DJmolding.