Basics Of Plastic Injection Molding
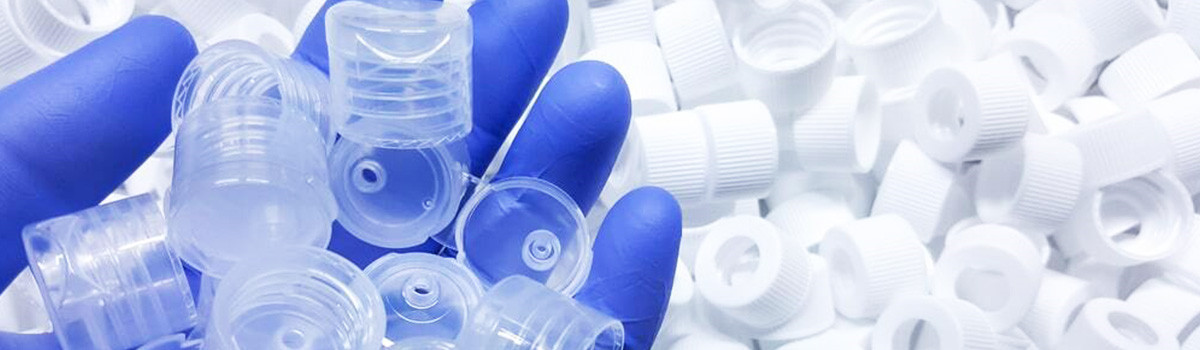
Explore the injection molding process and how it works.
Plastic injection molding is a popular manufacturing technique in which thermoplastic pellets are converted into high volumes of complex parts. The injection molding process is suitable for a variety of plastic materials and is a vital aspect of modern life—phone cases, electronic housings, toys, and even automotive parts would not be possible without it. This article will break down the basics of injection molding, describe how injection molding works, and illustrate how it is different from 3D printing.
What Are the Basics of Plastic Injection Molding?
The basics of plastic injection molding process includes creating the product design, making a tooling a mold to fit the product design, melting the plastic resin pellets, and using pressure to inject the melted pellets into the mold.
See a breakdown of each step below:
1. Creating the Product Design
Designers (engineers, mold maker businesses, etc.) create a part (in the form of a CAD file or other transferrable format), following fundamental design guidelines specific to the injection molding process. Designers should try to include the following features in their designs to help increase the success of a plastic injection mold:
*Bosses for threaded inserts/fasteners
*Constant or near-constant wall thicknesses
*Smooth transitions between variable wall thicknesses
*Hollow cavities in thick sections
*Rounded edges
*Draft angles on vertical walls
*Ribs for supports
*Friction fits, snap-fit joints, and other non-fastener joining features
*Living hinges
Additionally, designers should minimize the following features to reduce defects in their designs:
*Non-uniform wall thicknesses or especially thin/thick walls
*Vertical walls with no draft angles
*Sudden geometrical changes (corners, holes, etc.)
*Poorly designed ribbing
*Undercuts/overhangs
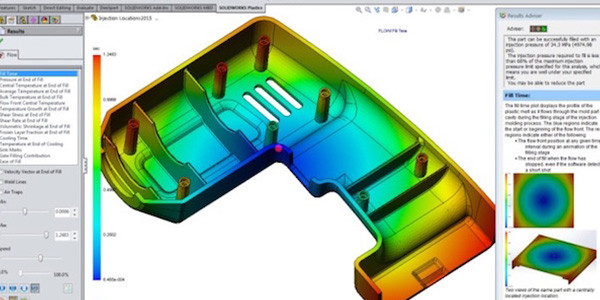
2. Making a Tooling Mold to Fit the Product Design
Highly skilled machinists and toolmakers, using the product design, fabricate a tooling mold for the injection molding machine. A tooling mold (also known as simply a tool) is the heart and soul of the injection molding machine. They are carefully designed to contain the negative cavity for the product design and additional features such as sprues, runners, gates, vents, ejector systems, cooling channels, and moving components. Tooling molds are made out of specific grades of steel and aluminum that can withstand tens of thousands (and sometimes hundreds of thousands) of heating and cooling cycles, such as 6063 aluminum, P20 steel, H13 steel, and 420 stainless steel. The mold fabrication process takes upwards of 20 weeks to complete, including both fabrication and approval, making this step the most extended aspect of injection molding. It is also the most expensive part of injection molding, and once a tooling mold is fabricated, it cannot be drastically changed without incurring additional costs.
3. Melting the Plastic Resin Pellets
After operators obtain the finished mold, it is inserted into the injection molding machine, and the mold closes, starting the injection molding cycle.
Plastic granules are fed into the hopper and into the barrel. The reciprocating screw is drawn back, allowing materials to slip into the space between the screw and the barrel. The screw then plunges forward, forcing the material into the barrel and closer to the heater bands where it melts into molten plastic. The melting temperature is kept constant as per the material specifications so that no degradation occurs in the barrel or in the mold itself.
4. Using Pressure to Inject the Melted Pellets Into the Mould
The reciprocating screw forces this melted plastic through the nozzle, which is seated within a depression in the mold known as a mold sprue bushing. The moving platen pressure fits the mold and the nozzle together tightly, ensuring no plastic can escape. The melted plastic is pressurized by this process, causing it to enter all parts of the mold cavity and displacing cavity air out through the mold vents.
Injection Molding Machine Components
The components of an injection molding machine include hopper, a barrel, a reciprocating screw, heater(s), movable platen, a nozzle, a mold, and a mold cavity.
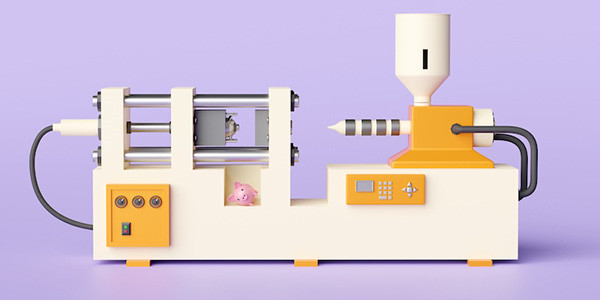
More information on each of the injection molding components in the list below:
*Hopper: the opening where plastic granules are fed into the machine.
*Barrel: the outer housing of the injection molding machine, which contains the reciprocating screw and the plastic granules. The barrel is wrapped in several heater bands and is tipped with a heated nozzle.
*Reciprocating screw: the corkscrew component that conveys and pressurizes the plastic material as it melts through the barrel.
*Heaters: also known as heating bands, these components provide thermal energy to the plastic granules, turning them from a solid form to a liquid. form.
*Movable Platen: The moving component connected to the mold core that applies pressure to keep both mold halves airtight and also releases the mold core when revealing the finished part.
*Nozzle: the heated component that provides a standard outlet for molten plastic into the mold cavity, keeping both temperature and pressure as stable as possible.
*Mold: the component or components that contain the mold cavity and additional supporting features like ejector pins, runner channels, cooling channels, vents, etc. At a minimum, molds are separated into two halves: the stationary side (closer to the barrel) and the mold core (on the moving platen).
*Mold Cavity: the negative space that, when filled with molten plastic, will shape it into the desired final part plus supports, gates, runners, sprues, etc.
How Does Injection Molding Work?
Once the plastic has filled the mold including its sprues, runners, gates, etc., the mold is kept at a set temperature to allow uniform solidification of the material into the part shape. A holding pressure is maintained while cooling to both stop backflow into the barrel and reduce shrinking effects. At this point, more plastic granules are added to the hopper in expectation of the next cycle (or shot). When cooled, the platen opens and allows the finished part to be ejected, and the screw is drawn back once more, allowing material to enter the barrel and start the process over again.
The injection molding cycle works by this continuous process—closing the mold, feeding/heating the plastic granules, pressurizing them into the mold, cooling them into a solid part, ejecting the part, and closing the mold again. This system allows for the rapid production of plastic parts, and upwards of 10,000 plastic parts can be made in a workday depending upon the design, size, and material.
Djmolding is low volume injection molding companies in china.Our plastic injection molding process produces custom prototypes and end-use production parts with lead times as fast as 1 day,low volume plastic injection molding part supplier for up to 10000 parts per year